5901 Botham Jean Blvd, Dallas, TX 75215
Everything You Should Know About Industrial Magnet Handling Procedures?
July 23, 2025Industrial magnet handling procedures are comprehensive safety protocols designed to protect workers who operate with powerful magnets in manufacturing environments. These specialized guidelines address the unique hazards presented by high-strength industrial magnets in recycling, manufacturing, and processing sectors.
The magnetic forces exerted by industrial-grade magnets can be deceptively powerful. A medium-sized neodymium magnet can easily exert enough force to cause severe pinching injuries if fingers are caught between two attracting surfaces. This risk makes proper handling techniques essential for workplace safety.
Beyond personnel safety, these procedures protect sensitive equipment and maintain the integrity of the magnets. Proper handling prevents demagnetization and physical damage, ensuring magnets remain effective throughout their operational life. As magnetic separators and lifting systems become more common in industrial recycling operations, these procedures have become a fundamental aspect of workplace safety training.
What Are the Key Safety Risks When Handling Industrial Magnets?
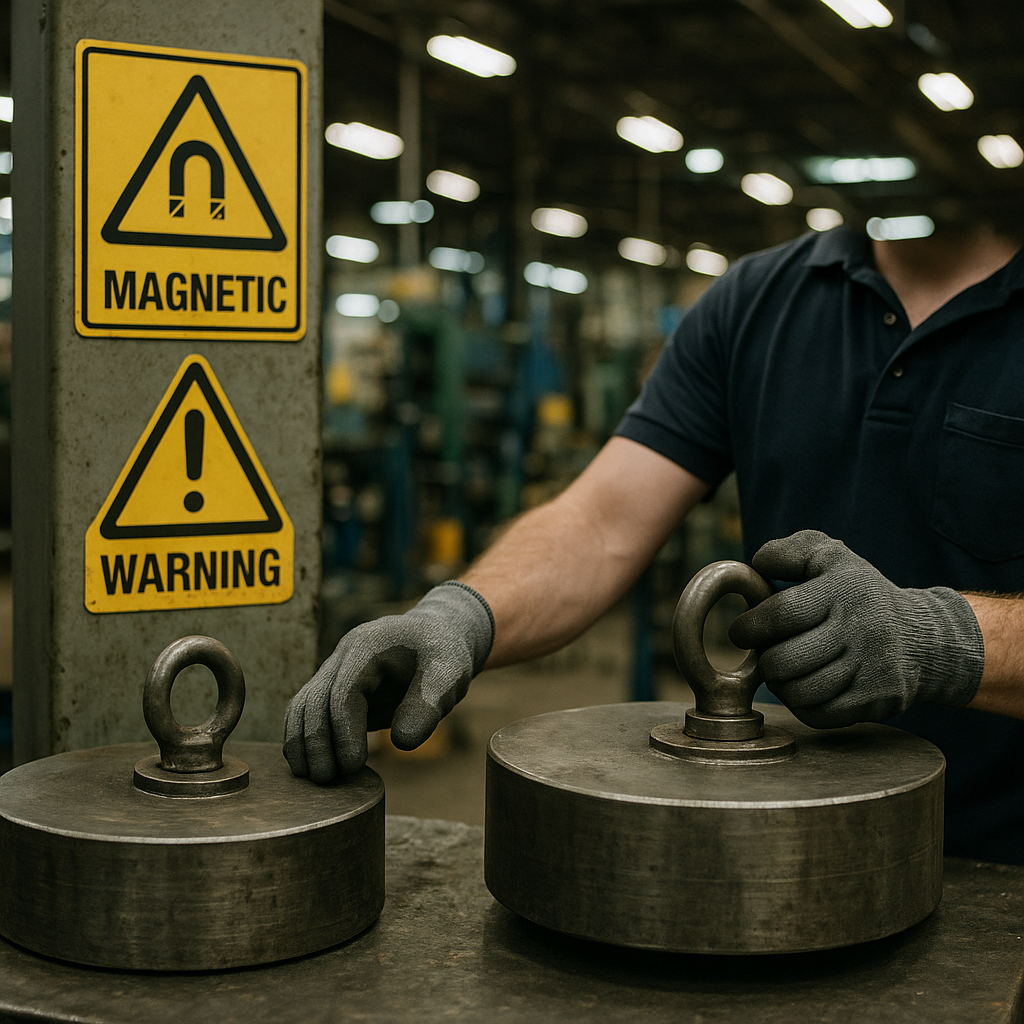
Industrial magnets pose several significant safety hazards that require careful attention in recycling operations. Understanding these risks is essential for implementing proper handling procedures and maintaining a safe work environment.
Pinching Hazards
The most common injury associated with industrial magnets is pinching. When two magnets or a magnet and ferrous object rapidly attract, they can trap fingers, skin, or other body parts between them. These forces can be surprisingly powerful, creating pressure similar to being caught between pliers.
Workers in recycling facilities are particularly vulnerable to pinching injuries when separating materials or cleaning magnetic separators. Even moderately sized industrial magnets can generate enough attractive force to cause severe tissue damage or bone fractures.
In one documented case at a materials recovery facility, a worker suffered a crushed finger when two neodymium magnets unexpectedly attracted while he was adjusting equipment without wearing proper protective gloves.
Equipment Damage
Uncontrolled magnetic forces can cause significant damage to equipment and infrastructure. When magnets suddenly attract to machinery or metal structures, the resulting collisions can damage both the magnet and the equipment.
This risk is particularly relevant in recycling plants where magnetic separators operate near other processing equipment. Sudden magnetic attraction can pull tools from workers’ hands, creating projectiles that damage control panels, sensors, or other sensitive components.
The cost of equipment repair and downtime from such incidents can be substantial, affecting the operational efficiency and profitability of recycling operations.
Medical Device Interference
Industrial magnets create magnetic fields that can interfere with electronic medical devices. Pacemakers, implantable cardioverter defibrillators (ICDs), and insulin pumps are particularly susceptible to magnetic interference.
Workers with these devices need to maintain a safe distance from strong magnetic fields. The specific safe distance varies depending on the strength of the magnet and the type of medical device.
Many recycling facilities now implement special protocols and clear signage to warn employees and visitors about magnetic field hazards in specific work areas.
Magnet Damage and Degradation
Improper handling can damage the magnets themselves, reducing their effectiveness and creating additional hazards. Dropping, striking, or exposing magnets to extreme temperatures can cause them to crack, chip, or lose magnetic strength.
Damaged magnets present several problems. First, they may not perform their intended function in recycling operations. Second, sharp edges from broken magnets create additional injury risks. Finally, some magnet materials can release harmful dust or particles when damaged.
Proper storage is also critical. Industrial magnets stored improperly can demagnetize each other or attract unwanted ferrous debris that compromises their performance.
Safety Risk | Prevention Measure |
---|---|
Pinching Hazards | Train workers on proper handling techniques and use protective gloves. |
Equipment Damage | Use controlled movements and keep magnets away from sensitive equipment. |
Medical Device Interference | Maintain safe distances from workers with medical implants. |
Magnet Damage and Degradation | Ensure proper storage and handle magnets carefully to avoid physical damage. |
Electronic Equipment Damage | Designate magnet-free zones in areas with sensitive electronics. |
Electronic Equipment Damage
Strong magnetic fields can damage or erase data from electronic devices, including smartphones, computers, hard drives, and other storage media commonly found in modern recycling facilities.
Beyond data loss, magnets can permanently damage sensitive electronic components in control systems that manage automated recycling processes. This presents both a safety and operational risk, as malfunctioning control systems can lead to equipment failures.
Creating designated “magnet-free” areas for electronic equipment and implementing strict protocols for keeping magnets away from control rooms helps minimize these risks.
What Are Best Practices for Storing and Transporting Industrial Magnets?
Optimal Storage Environment
Industrial magnets require specific conditions to maintain their magnetic properties and structural integrity. Store magnets at room temperature, between 15–30°C (59-86°F), to prevent thermal stress-induced demagnetization. Keep humidity levels below 50% to avoid corrosion, especially for neodymium magnets, which are highly susceptible to moisture damage.
Temperature fluctuations can severely impact magnetic performance. Extreme heat above a magnet’s Curie point causes irreversible demagnetization, while cold temperatures may lead to brittleness and potential cracking in types like ceramic magnets.
Apply anti-corrosive coatings or platings as additional protection against environmental degradation. These treatments significantly extend magnet life by creating a barrier against moisture and chemical exposure.
Proper Storage Techniques
When storing multiple magnets together, use non-ferromagnetic separators between them. Wood, plastic, or cardboard dividers prevent magnets from attracting each other, which can cause chipping or breaking upon collision. This separation is particularly important for brittle materials like neodymium and samarium cobalt magnets.
Store magnets in vibration-free, shock-proof containers to prevent mechanical damage. Mishandling can lead to chips or cracks that compromise magnetic performance. Closed containers also prevent magnets from attracting ferrous particles from their surroundings.
Organize storage areas with clear labeling and adequate shelf clearance. Insufficient space between stored magnets can cause them to shift or jump during access and removal, creating safety hazards.
Safe Transportation Practices
Transportation of industrial magnets requires careful planning and execution. Use shielded packaging with non-magnetic materials such as wood, plastic, or cardboard. Add shock-absorbing materials like foam, bubble wrap, or sponge inside packages to minimize movement and protect magnets from physical impact.
Apply clear warning labels on packages indicating “Strong Magnets” and “Handle with Care” to alert handling personnel. For magnets with specific pole orientations, mark the direction on the packaging for correct identification upon arrival.
Plan transportation routes that avoid proximity to ferrous objects, as magnets can exert force over surprising distances. Employ wooden or plastic casings to lessen magnetic force during transit. This shielding helps prevent unwanted attraction to metal objects in the transport environment.
Professional Handling Considerations
Only trained personnel should handle industrial magnets, particularly during transportation. Experienced staff know how to move magnets safely and can anticipate potential hazards. Provide proper protective equipment like gloves and eye protection to prevent injuries from pinching or flying debris.
For especially powerful magnets, implement regular inspection protocols during transportation. Check for package integrity and magnet condition, taking immediate corrective action if problems arise.
Keep magnets away from sensitive electronics, magnetic storage media, and individuals with medical implants like pacemakers. The magnetic field can interfere with these devices, causing data loss or medical emergencies.
Industrial magnets stored in proper environmental conditions with appropriate protection maintain their magnetic properties longer. Implementing these storage and transportation best practices not only preserves magnet performance but also enhances workplace safety by reducing accident risks.
How Should Employees Be Trained in Magnet Handling?
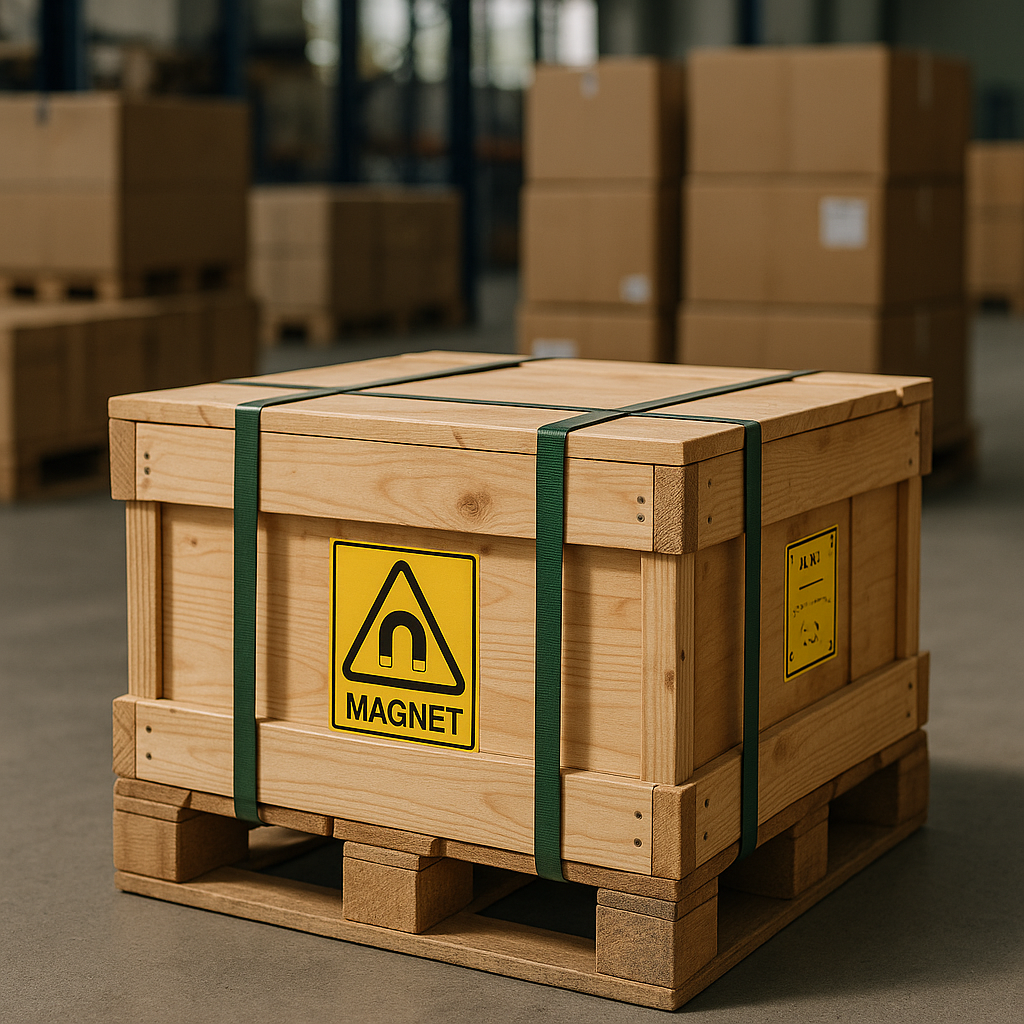
Comprehensive training is essential for anyone working with or around magnetic materials. Strong magnets can pose serious hazards, including pinching injuries, equipment damage, and interference with medical devices. A structured training program ensures that employees understand these risks and can handle magnets safely.
Training should begin with teaching employees about the fundamental properties of magnetic materials. This includes explaining different types of magnets, their strength ratings, and how magnetic fields operate. Understanding that magnetic attraction can occur suddenly and with surprising force helps employees respect the potential dangers these materials present.
Risk Identification and Assessment
Employees need to recognize potential hazards before they become dangers. Training should cover how to identify risks such as pinching hazards, potential for flying metal objects, and equipment damage. Workers should learn to scan their environment for ferrous materials that could be attracted to magnets unexpectedly.
Risk awareness also includes understanding who should avoid working with magnets. Employees with pacemakers or other implanted medical devices should be instructed to maintain a safe distance from strong magnetic fields, typically at least 12–18 inches for high-power magnets.
Safe Handling Procedures
Proper handling techniques form the core of magnet safety training. Employees should be taught to move magnets slowly and deliberately, never allowing them to snap together uncontrolled. Using non-magnetic spacers when separating or storing magnets prevents unexpected attraction.
Training should emphasize maintaining a clean, organized workspace free of metal objects that could be pulled into the magnetic field. Employees should learn to use appropriate tools, such as magnetic lifters or hoists, for heavy or bulky magnetic items rather than attempting manual lifting.
Personal Protective Equipment
Appropriate PPE is critical when handling magnets. Training must cover:
- Proper gloves that can resist pinching
- Safety goggles to protect against possible flying debris
- Steel-toed boots for foot protection
- High-visibility vests in busy work environments
Employees should understand not only what PPE to wear but also how to inspect it for damage and when replacement is necessary. Even with PPE, workers should be trained to maintain appropriate distances from strong magnets.
Emergency Procedures
Despite precautions, accidents can happen. Training should include clear emergency procedures covering what to do in case of injury or equipment damage. This includes knowing who to contact, how to safely remove a person from a dangerous magnetic situation, and basic first aid for common magnet-related injuries.
Employees should practice these emergency procedures regularly through drills, so responses become automatic when needed. The training should emphasize the importance of reporting all incidents, even minor ones, to improve safety protocols.
Implementation Strategies
When implementing magnet safety training, several approaches prove effective:
New employees should always be supervised when working with magnets until they demonstrate consistent safe handling practices. Refresher training should be conducted at regular intervals, not just as a one-time orientation event. Safety audits should be performed regularly to ensure protocols are being followed.
Clear warning signage should be posted in areas where magnets are used or stored. These signs should indicate magnetic hazards and remind workers of safety protocols. For consistent education across an organization, consider implementing an online training program that can be accessed by all relevant personnel.
Evaluating Training Effectiveness
Regular assessment of training effectiveness helps identify gaps in knowledge or practice. Post-training tests can verify understanding, while observation of work practices confirms proper implementation. Safety coordinators should monitor incident reports related to magnet handling to identify areas needing additional training focus.
A manufacturing plant reported a serious incident in 2019 when an employee suffered a severe hand injury due to improper magnet handling. After implementing a comprehensive training program, including regular refreshers and strict safety guidelines, the company went three years without a single magnet-related injury. This demonstrates how proper training directly impacts workplace safety.
Injury Type | Prevention Measures |
---|---|
Pinching Injuries | Wear heavy-duty gloves to reduce risk and improve grip. |
Crushing Injuries | Use non-metallic tools and separate magnets carefully. |
Projectile Hazards | Maintain clear, metal-free workspace and be cautious when magnets are near metal objects. |
Interference with Medical Implants | Stay at least 12-18 inches away from sensitive devices (e.g., pacemakers). |
Magnet Damage/Chipping | Store and transport magnets in shock-proof, shielded containers. |
Data Loss and Equipment Malfunction | Keep magnets away from electronic equipment and storage media. |
Ultimately, effective training creates a culture of safety awareness. When employees understand both the risks and proper procedures for magnet handling, they become active participants in maintaining a safe work environment rather than passive rule-followers. This culture of safety leads to fewer accidents, less downtime, and greater operational efficiency.
Conclusion: Ensuring Safe Industrial Magnet Handling
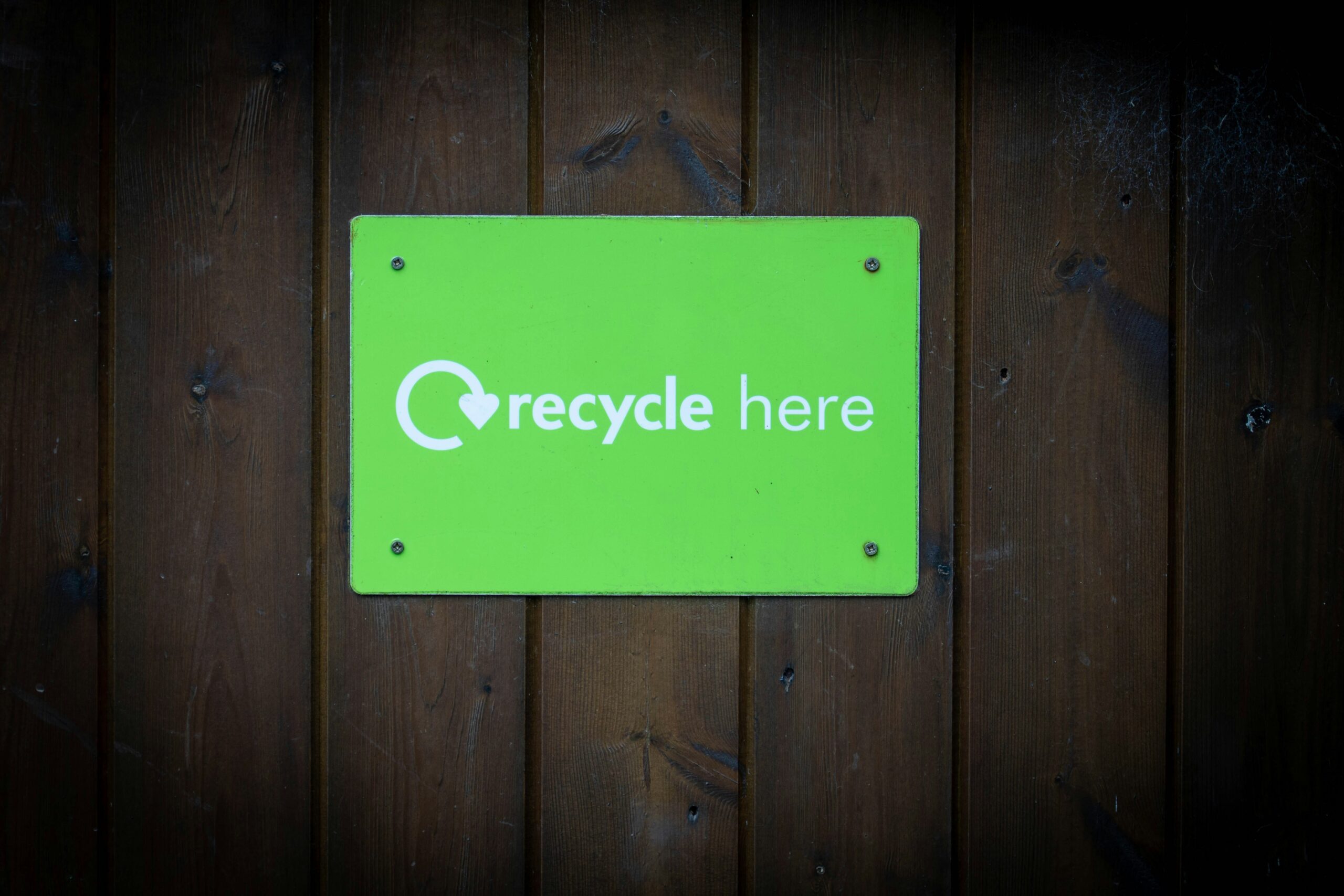
Industrial magnets are vital in manufacturing, recycling, and material handling operations, but their power requires careful handling. Proper procedures protect workers and equipment while ensuring efficiency. Effective safety protocols integrate comprehensive training, suitable protective equipment, and organized workspaces.
When organizations prioritize magnet safety with thorough training, clear protocols, and appropriate PPE, they not only protect employees but also enhance operational efficiency by reducing accidents, preventing equipment damage, and minimizing downtime. A culture of safety awareness around industrial magnets is essential for sustainable operations in any facility using these powerful tools. For assistance with your industrial magnet recycling or handling needs, contact Okon Recycling at 214-717-4083.