5901 Botham Jean Blvd, Dallas, TX 75215
Specialty Recycling for Magnetic Materials: The Challenges and Opportunities
July 22, 2025Each year, billions of electronic devices containing powerful magnets reach the end of their lifecycle. These magnets contain critical rare earth elements essential for modern technology. The rising demand for these materials has created an urgent need for sustainable recovery solutions.
Specialty recycling for magnetic materials is a focused process designed to recover valuable rare earth elements like neodymium, dysprosium, and praseodymium from discarded products. These elements are vital components in everything from smartphones and computers to industrial equipment and renewable energy technologies.
This specialized recycling approach is distinct from conventional methods, employing precise extraction techniques to isolate and purify these elements from complex assemblies. The aim is twofold: to reduce the environmental impact of mining new materials and conserve these limited resources for future generations.
What Are the Key Challenges in Magnetic Waste Recycling?
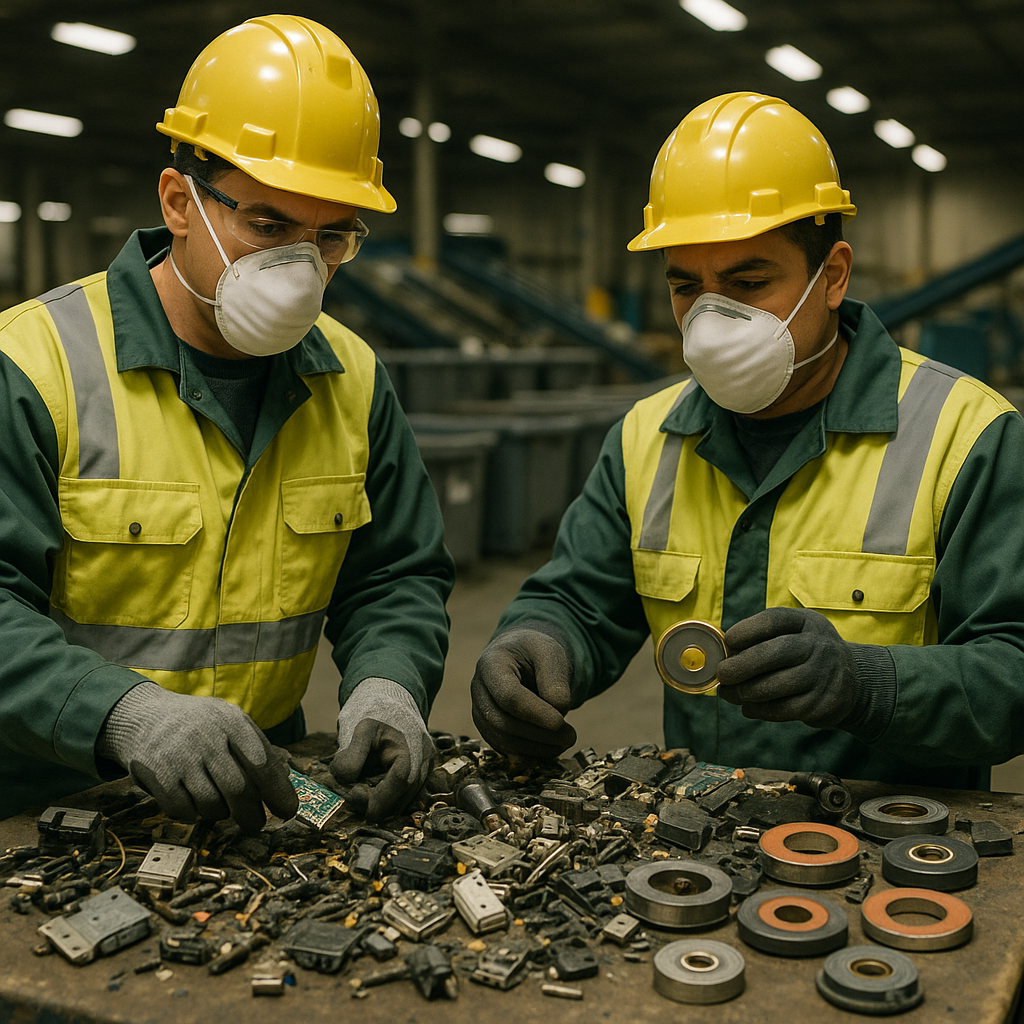
Magnetic waste recycling presents several significant hurdles that impact the efficiency and viability of recovery operations. These challenges cover technical, economic, and logistical areas, creating a complex landscape for recyclers. Despite the environmental benefits, organizations face multiple barriers when processing magnetic materials.
Technical Complexity in Material Separation
A major challenge in magnetic waste recycling is the technical difficulty of material separation. Rare earth magnets are often deeply embedded within electronic devices and machinery, making extraction labor-intensive and often requiring manual disassembly.
The physical properties of these materials further complicate recycling efforts. Many manufacturers use industrial-grade adhesives to secure magnets within devices, creating strong bonds that make separation nearly impossible without damaging valuable components.
Contamination presents another significant technical hurdle. Even small amounts of nickel or copper from drive components can reduce the magnetic properties of recycled materials by up to 25%, which diminishes their market value and usability in high-performance applications.
Economic Viability Concerns
The economics of magnetic waste recycling remain challenging. Recycled magnets must compete with newly manufactured ones from primary sources, which often benefit from economies of scale and established supply chains.
Market fluctuations in rare earth element prices create additional uncertainty, making it difficult for recyclers to forecast revenues and plan long-term operations with confidence.
The initial investment required for specialized equipment and facilities is a significant barrier to entry. Without supportive policies or financial incentives, many potential recycling operations struggle to secure adequate funding.
- Recycling costs often exceed expenses for mining and refining new materials
- Lack of price premiums for recycled content limits profit potential
- High capital expenses for processing equipment reduce return on investment
- Processing costs increase with smaller or more complex input materials
Collection and Supply Chain Difficulties
The lack of mature collection systems is a major obstacle for magnetic waste recycling. Unlike established recycling streams for materials like aluminum or paper, few dedicated collection points exist for products containing rare earth magnets.
The unpredictability of waste streams further complicates recycling efforts. The composition, volume, and availability of end-of-life products containing magnets vary significantly, making it challenging for recyclers to maintain consistent operations.
Product labeling presents another logistics challenge. Without clear identification of magnetic components within devices, recyclers must manually inspect each item, significantly increasing processing time and operational costs.
Energy-Intensive Processes
Current magnetic recycling technologies require substantial energy inputs. Pyrometallurgical recycling methods, in particular, use high temperatures exceeding 1000°C to separate magnet components based on melting points.
While hydrometallurgical processes offer more energy-efficient alternatives, they still consume significant resources. These chemical-intensive methods use acids and other solvents that require careful handling and disposal.
Energy requirements contribute to both environmental impact and operational costs. Finding a balance between efficiency and sustainability remains an ongoing challenge for the industry.
Secondary Waste Generation
Recycling processes can generate their own waste streams. Chemical treatments in hydrometallurgical processes produce effluents requiring proper treatment and disposal to prevent environmental contamination.
The materials removed during processing, such as coatings and adhesives, create additional waste management challenges. These secondary materials often have limited recycling potential.
Even with advanced recycling techniques, some material loss is inevitable. Achieving 100% recovery rates remains technically impossible with current technologies, resulting in some valuable elements being lost.
Challenge | Description |
---|---|
Technical Complexity in Material Separation | Rare earth magnets are embedded in complex assemblies; extraction requires manual disassembly and careful separation to avoid contamination and loss of magnetic properties. |
Economic Viability Concerns | Recycled magnets struggle to compete with those from virgin materials; price volatility and high capital costs create barriers to entry. |
Collection and Supply Chain Difficulties | Lack of dedicated collection systems for magnetic waste results in unpredictable waste streams; labeling confusion increases costs. |
Energy-Intensive Processes | Recycling technologies such as pyrometallurgy require high energy input, affecting sustainability and operational costs. |
Secondary Waste Generation | Chemical processes generate hazardous byproducts; separation processes may not recover 100% of valuable components. |
Despite these challenges, recycling magnetic materials is crucial for environmental sustainability and resource security. As technologies improve and stakeholders collaborate more effectively, the prospects for greater recycling rates continue to improve. Innovative approaches like hydrogen-based recycling methods and improved collection infrastructure offer promising paths forward for this essential industry.
What Innovative Technologies are Emerging for Magnetic Waste Management?
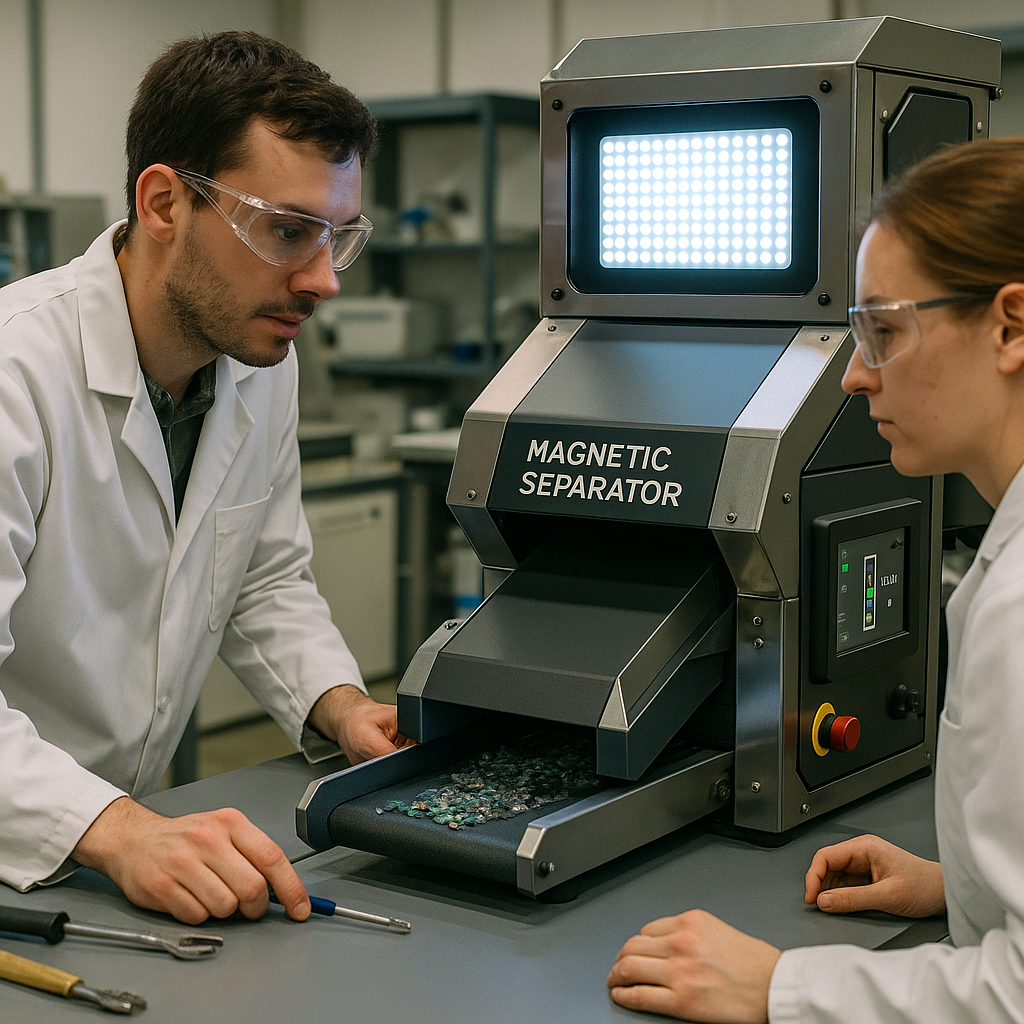
The field of magnetic waste management is rapidly advancing with several groundbreaking technologies paving the way for more sustainable recycling practices. These innovations address longstanding industry challenges while creating new opportunities for resource recovery.
Hydrogen-assisted recycling stands out as one of the most promising advancements in magnetic waste recycling. This technology, known as Hydrogen Processing of Magnetic Scrap (HPMS), uses hydrogen to break down magnetic materials into a reusable powder form. When exposed to hydrogen, sintered NdFeB magnets are reduced to a friable, demagnetized powder that can be easily separated from materials like coatings and adhesives. UK-based company HyProMag is making significant strides with this technology, planning to commission a chemical processing plant in Birmingham with a recycling capacity of at least 100 tonnes of magnets annually.
Another key development is the creation of custom magnet solutions designed with end-of-life recyclability in mind. Manufacturers are engineering magnets using materials and processes that facilitate easier recovery and reprocessing. Custom AlNiCo magnets (aluminum-nickel-cobalt) and SmCo magnets (samarium-cobalt) can be melted down to recover constituent metals for reuse in new magnet production. These solutions support a circular economy approach where materials are continuously cycled back into production.
Green solvent technologies are changing how we extract valuable materials from magnetic waste. Traditional solvent-based recycling often relies on harsh chemicals that pose environmental hazards. Researchers are exploring biodegradable organic acids and ionic liquids as alternative solvents for extracting rare earth elements. These green chemistry approaches minimize environmental impact while maintaining extraction efficiency. UK startup IonicTech exemplifies this approach with their liquid-liquid extraction technology, which uses liquid salts to chemically separate rare earth elements from crushed magnets.
Hybrid recycling systems that combine different processing techniques are gaining traction. These integrated systems merge direct recycling, hydrometallurgical, and pyrometallurgical methods to optimize rare earth element recovery. French rare earth refiner Carester is implementing such a hybrid approach in its Caremag project. After mechanical processing, the permanent magnets undergo a combination of processes followed by solvent extraction to separate rare earth elements. The Caremag plant aims to recycle 2,000 tonnes of rare earth magnets annually.
Automation and robotics are enhancing the precision and efficiency of magnetic waste processing. Automated systems can sort, disassemble, and process waste magnets with greater accuracy than manual methods. These technologies improve the quality of recycled materials while reducing labor costs. Automated dismantling is particularly valuable for extracting magnets from complex electronic devices where manual disassembly would be prohibitively time-consuming.
As these innovative technologies mature and scale, they promise to transform magnetic waste management from a challenging environmental problem into a sustainable resource recovery opportunity. The continuous advancement of these technologies will be crucial for building a truly circular economy for magnetic materials.
Technology | Description | Key Advantages | Challenges |
---|---|---|---|
Hydrogen-Assisted Recycling | Uses hydrogen to break down magnetic materials into reusable powder form. | Reduces environmental impact; allows for easy separation of magnets. | Requires advanced technology and infrastructure. |
Custom Magnet Solutions | Development of magnets designed for end-of-life recyclability. | Facilitates easier recovery and reprocessing; supports circular economy. | Initial design and production costs. |
Green Solvent Technologies | Utilizes biodegradable solvents for extracting rare earth elements. | Minimizes environmental impact; reduces energy consumption. | Development and scalability of green solvents. |
Hybrid Recycling Systems | Combines different processing techniques for optimal recovery. | Higher recovery rates; lower energy consumption. | Complex integration of multiple processes. |
Automation and Robotics | Automated systems for sorting and processing waste magnets. | Improves precision and efficiency; reduces labor costs. | High initial investment in technology. |
How Can Businesses and Consumers Contribute to Eco-Friendly Magnetic Waste Management?
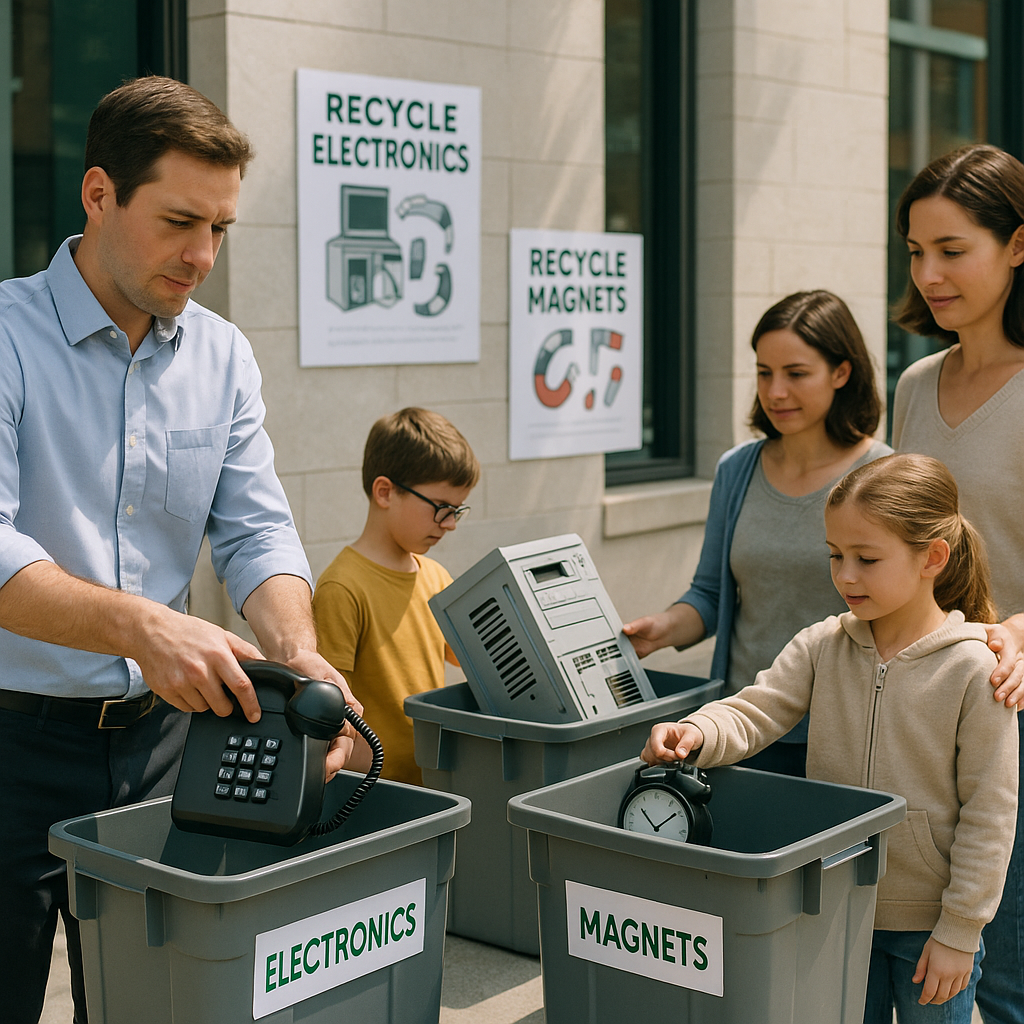
Businesses significantly impact magnetic waste management through their product design choices. Companies that create products for easy disassembly enable recyclers to extract valuable magnetic components at the end of a product’s life. This approach conserves rare earth elements while reducing environmentally harmful mining operations.
Design modifications that enhance recycling include using standardized magnet sizes, avoiding permanent adhesives that complicate separation, and clearly labeling components containing magnetic materials. These simple changes dramatically improve recycling efficiency and material recovery rates.
Take-back programs are another effective business strategy. By accepting used products from customers, companies create closed-loop systems where valuable magnetic materials return to the manufacturer instead of reaching landfills. Some forward-thinking businesses offer incentives like discounts on new purchases or rebates to boost participation in these programs.
Using recycled magnetic materials in manufacturing completes the circular economy approach. Businesses that source recycled neodymium, samarium-cobalt, or aluminum-nickel-cobalt magnets reduce extraction demands while often achieving cost savings. The quality and availability of these recycled materials continue to improve as processing technologies advance.
For consumers, properly disposing of electronics containing magnets is crucial to preventing magnetic waste pollution. Instead of discarding old devices in the trash, consumers should research local e-waste collection points or specialized recycling facilities. Many communities host regular collection events for electronic waste, making proper disposal more convenient.
Consumers can also influence the market by supporting products made with recycled magnetic materials. Purchasing decisions that prioritize brands using recycled components send a clear message to manufacturers that sustainability matters. This market pressure drives innovation toward more environmentally friendly practices.
Community awareness campaigns amplify individual actions. Consumers can educate others about magnetic waste recycling through social media, community forums, or local environmental groups. These efforts expand the impact of personal choices and build momentum for broader change.
Participating in public policy discussions provides another avenue for consumer impact. Supporting regulations that promote responsible magnetic waste management, such as extended producer responsibility programs, helps create systemic change. Letters to representatives, signing petitions, or speaking at community meetings strengthen the collective voice for environmental protection.
Business-consumer partnerships offer promising solutions. Educational workshops where businesses explain their recycling initiatives and consumers learn proper disposal methods foster mutual understanding and shared commitment to addressing magnetic waste challenges.
Recycling cooperatives represent an innovative collaborative approach, with businesses and community members working together to collect, sort, and process magnetic waste. These organizations create local jobs while ensuring proper handling of materials that might otherwise pollute the environment.
Government incentives can accelerate eco-friendly practices. Tax benefits for businesses implementing recycling programs or rebates for consumers who properly dispose of electronic waste create financial motivation aligned with environmental goals. Supporting these policies benefits both businesses and consumers.
Investing in research and development of new recycling technologies benefits the entire magnetic waste ecosystem. Businesses that fund innovation and consumers who support these forward-thinking companies advance solutions to technical challenges in magnetic material recovery.
Through these complementary approaches, businesses and consumers can transform magnetic waste from an environmental liability into a valuable resource stream. The resulting reduction in pollution, conservation of rare earth elements, and progress toward a circular economy benefit everyone’s long-term interests.
Conclusion: The Future of Eco-Friendly Magnetic Waste Management
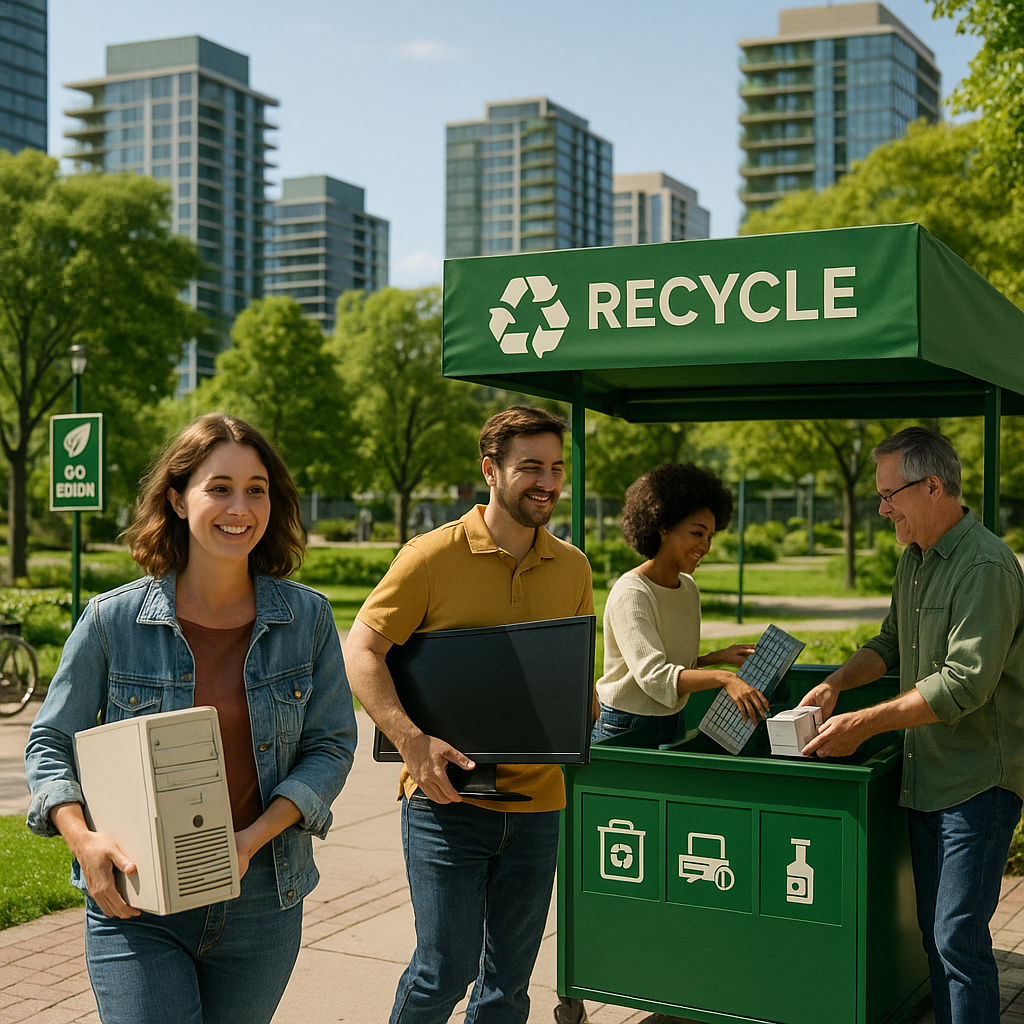
As industries including clean energy, electric vehicles, and consumer electronics continue to demand more rare earth magnets, managing these valuable resources sustainably becomes ever more essential. The future of magnetic waste management relies on advancing recycling technologies such as hydrogen decrepitation and magnet-to-magnet processes, which significantly reduce environmental impacts compared to traditional production methods.
Recycling magnetic materials provides numerous benefits beyond environmental conservation. Recovered magnets can produce up to 80% lower environmental impacts across most categories compared to primary magnets. These sustainable strategies help mitigate supply chain risks, reduce reliance on mining operations that create toxic waste, and preserve finite resources for future generations. For your magnetic recycling needs, contact Okon Recycling at 214-717-4083.