5901 Botham Jean Blvd, Dallas, TX 75215
What Are the Options for Managing End-of-Life Industrial Magnets?
July 23, 2025Did you know that less than 1% of end-of-life rare earth magnets are currently recycled? As industries increasingly rely on powerful neodymium magnets in applications from wind turbines to electric vehicles, sustainable management of these materials at the end of their lifecycle has become a critical environmental challenge.
Industrial magnets, particularly those made from rare earth materials like neodymium-iron-boron (NdFeB), contain valuable elements that are both economically important and environmentally costly to extract through traditional mining. When these magnets reach the end of their useful life, two main management options exist: rebuilding or recycling.
Rebuilding involves restoring existing magnets to a functional condition, typically by demagnetizing, cleaning, and remagnetizing the original materials. The advantage of rebuilding is its simplicity and lower energy requirements compared to full recycling. This approach is most effective for larger, relatively intact magnets from applications like MRI machines or industrial equipment.
What Are the Benefits and Challenges of Rebuilding Industrial Magnets?
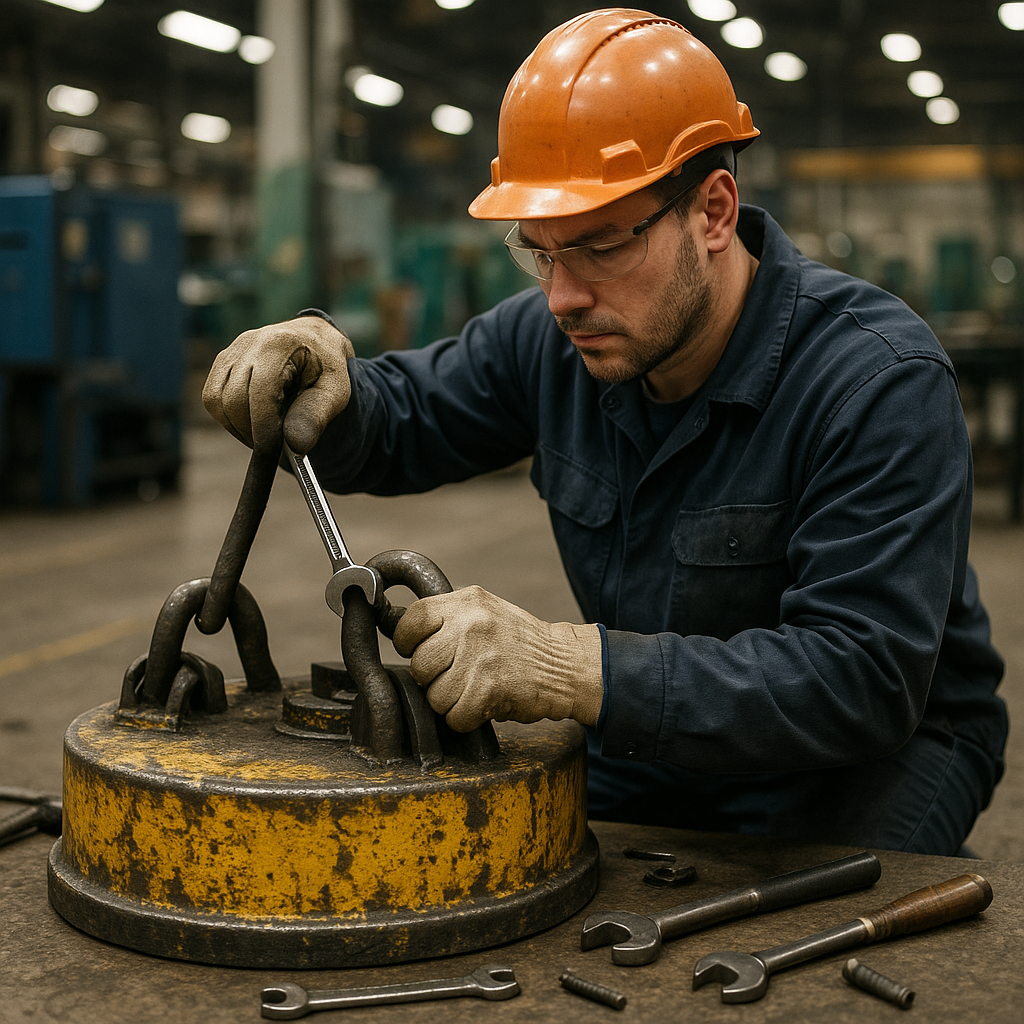
Rebuilding industrial magnets offers substantial cost benefits for organizations managing aging magnetic equipment. Rather than replacing costly magnets entirely, refurbishment extends their operational life while maintaining performance standards. The rebuilding process typically involves inspection, disassembly, remagnetization, and final quality testing to restore functionality.
Ohio Magnetics, a leader in magnet refurbishment, reports that rebuilt magnets typically cost between 15-25% of new replacement units. This significant cost difference makes rebuilding particularly attractive for high-value or custom-engineered magnetic systems where replacement costs can be prohibitive.
Key Benefits of Magnet Rebuilding
- Cost-effectiveness – Rebuilding averages 15-25% of the cost of purchasing new magnets, providing substantial savings for industrial operations.
- Performance restoration – Quality rebuilds can match or exceed original specifications when performed by experienced technicians.
- Reduced lead times – Rebuilding often offers faster turnaround than ordering custom replacements, minimizing operational downtime.
- Sustainability advantages – Extends the useful life of existing equipment and reduces the environmental impact of manufacturing new units.
- Potential for upgrades – During rebuilding, magnets can be modified or enhanced to improve performance beyond original specifications.
When evaluating industrial magnet rebuilding services, companies should seek providers that offer comprehensive inspection, testing, and quality assurance. Many reputable rebuilders include warranty coverage comparable to new equipment guarantees.
Limitations and Challenges
Despite its advantages, magnet rebuilding isn’t always feasible or appropriate. Several factors can limit rebuilding effectiveness or make replacement a better option:
- Severe corrosion or structural damage – When core components have deteriorated beyond repair, rebuilding may not restore full functionality.
- Technological obsolescence – Older magnetic designs may not meet current efficiency or performance standards even after rebuilding.
- Material limitations – Some specialized magnetic materials, especially certain rare earth compositions, present unique challenges during the remagnetization process.
- Economic thresholds – For smaller, less expensive magnets, the labor costs of rebuilding may exceed replacement expenses.
- Documentation gaps – Without original specifications, rebuilding to exact performance parameters is more difficult.
The rebuilding process typically begins with a thorough inspection to determine feasibility. For electromagnets, this often includes electrical testing and coil examination. Permanent magnets undergo field strength testing and surface evaluation. Based on these assessments, technicians can recommend the most cost-effective approach.
Some rebuilding services, like those offered by Ohio Magnetics, provide detailed reports outlining the cause of magnet failure and preventative measures to extend future service life. This diagnostic approach helps facilities improve their maintenance programs and avoid recurring issues.
For industrial operations managing multiple magnetic systems, establishing a relationship with a qualified rebuilding service offers immediate cost savings and long-term maintenance advantages. Many facilities implement regular inspection programs to identify candidates for rebuilding before catastrophic failure occurs.
Service Method | Description | Cost |
Rebuilding Industrial Magnets | Restores existing magnets to a functional condition through cleaning, remagnetizing, etc. | 15-25% of the cost of new magnets |
Replacing Industrial Magnets | Purchasing brand new magnets as replacements. | 100% of the standard cost (base cost of purchase) |
How Does the Recycling Process Work for Industrial Magnets?
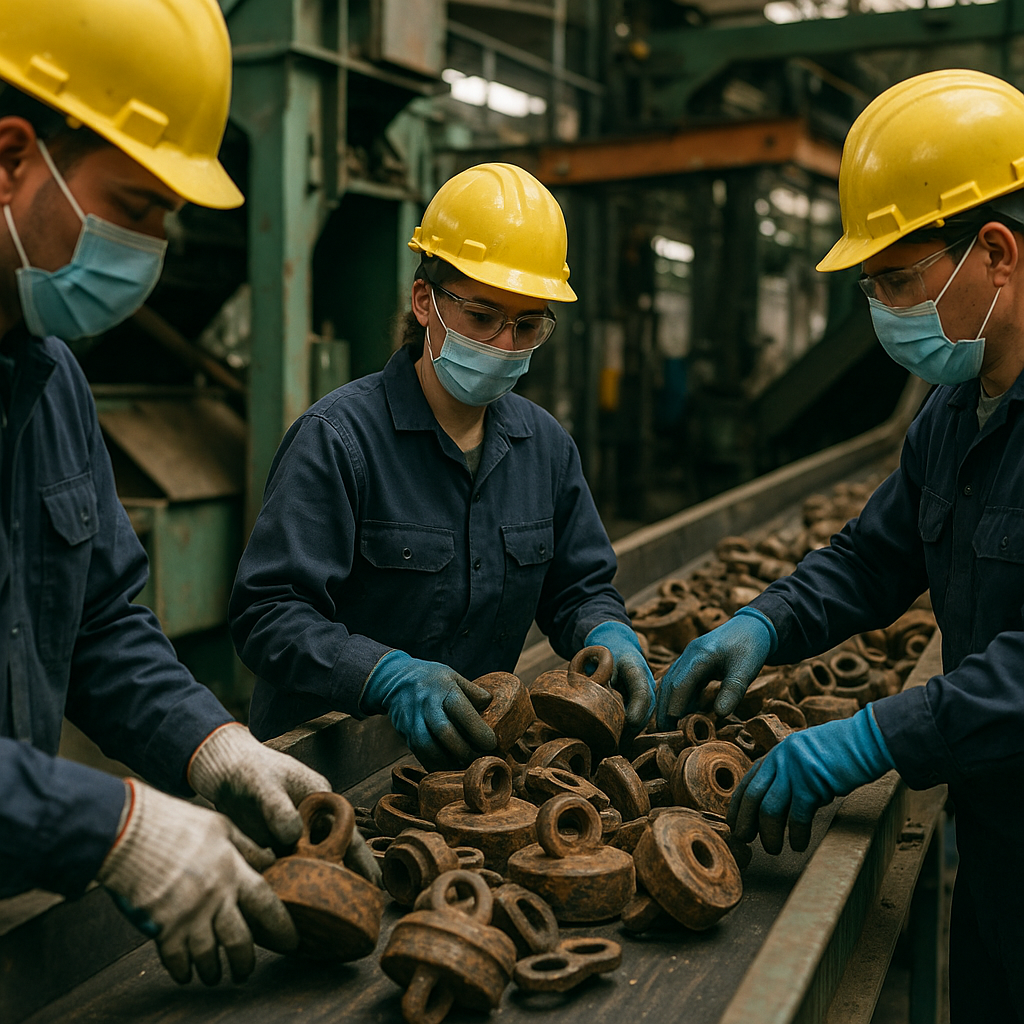
Recycling industrial magnets, particularly rare earth magnets, involves specialized processes designed to efficiently recover valuable materials. These processes vary based on the magnet’s type, condition, and the intended use of the recycled material. Most industrial magnet recycling focuses on neodymium-iron-boron (NdFeB) magnets due to their value and widespread use in modern technology.
Collection and Sorting
The first challenge in magnet recycling is obtaining suitable feedstock. Industrial magnets can be sourced from manufacturing scrap and end-of-life products such as electric motors, hard disk drives, and wind turbines. Collection systems must identify and separate magnetic components from mixed waste streams, a task made challenging by the limited information on magnet composition in most products and often requiring manual disassembly.
Once collected, magnets are sorted by type and composition. This step is critical because different compositions require specific recycling approaches. Modern recycling facilities increasingly use automated systems with sensors to identify and sort magnets based on their magnetic properties and composition.
Pre-processing and Demagnetization
Before recycling can begin, magnets undergo pre-processing to remove coatings, adhesives, and other contaminants that could interfere with recycling efficiency. This typically involves mechanical cleaning methods or thermal treatments. Coatings present a significant challenge, as they can decompose and remain as impurities through the recycling process.
Demagnetization is another crucial step. Industrial magnets, especially rare earth varieties, have powerful magnetic fields, complicating handling. Demagnetization is achieved by heating the magnets above their Curie temperature or using specialized equipment. This not only improves safety but also prepares the material for subsequent processing stages.
Material Recovery Methods
Multiple approaches exist for recovering rare earth elements from industrial magnets, each with distinct advantages and limitations. The two primary categories are:
1. Hydrogen Processing of Magnetic Scrap (HPMS)
HPMS has emerged as one of the most promising recycling technologies for rare earth magnets. This process uses hydrogen to break down the magnetic material into a powder form, simplifying processing. When hydrogen is introduced to NdFeB magnets, it triggers a reaction that expands and crumbles the material into a fine powder. This powder can then be:
- Directly reused to manufacture new sintered magnets
- Further processed to extract individual rare earth elements
- Used as feedstock for other magnet manufacturing methods
The key advantage of HPMS is its efficiency and lower environmental impact compared to traditional methods, requiring less energy and fewer chemicals. However, HPMS works best with relatively pure and uncontaminated magnets, as impurities can affect the quality of the final product.
2. Hydrometallurgical and Pyrometallurgical Processing
For more contaminated magnets or when specific rare earth elements need separation, chemical processing methods are employed:
- Hydrometallurgical processing dissolves magnets with acids and solvents to selectively extract rare earth elements. This approach allows for high-purity recovery but requires substantial chemical inputs and generates wastewater that must be treated.
- Pyrometallurgical processing involves high-temperature treatments to separate materials. While effective, this method is energy-intensive and may result in lower recovery rates for some elements.
Recent innovations in hydrometallurgical processing include liquid-liquid extraction technology with ionic liquids, achieving rare earth oxide purities exceeding 99.5%. Companies like IonicTech have demonstrated this approach commercially, separating light rare earths like neodymium from heavy rare earths like dysprosium.
Direct Recycling Approaches
An increasingly popular alternative to complete chemical breakdown is direct alloy recycling, or “magnet-to-magnet” recycling. This method maintains the alloy composition of the original magnet, reducing processing steps and energy requirements.
In direct recycling, magnets are demagnetized, cleaned, and then either:
- Reused in similar applications after remagnetization
- Crushed into powder and reformed into new magnets without separating the elements
- Re-melted and cast into new shapes
This method uses fewer resources than a complete chemical breakdown. However, it requires relatively pure starting materials and may result in magnets with properties slightly different from those made from virgin materials.
Challenges in Industrial Magnet Recycling
Despite advances in recycling technologies, several challenges remain:
- Material purity requirements: Many recycling processes require high-purity input to achieve high-quality output, but magnets from end-of-life products often contain contaminants.
- Complex disassembly: Extracting magnets from products like electric motors or hard drives is labor-intensive and often requires manual work.
- Variable composition: Different generations and types of magnets have varying compositions, complicating standardized recycling approaches.
- Coating removal: Protective coatings on magnets can be difficult to remove completely and may contaminate recycled materials.
Emerging Technologies
Several innovative approaches are being developed to address these challenges:
Continuous chromatography, adapted from the food industry, is being applied to rare earth separation by companies like ReElement. This process uses specialized resins to separate individual rare earth elements with high precision while potentially reducing chemical waste.
Another promising development is hybrid recycling systems combining physical and chemical processes. These approaches use mechanical and thermal pre-treatments followed by selective chemical extraction, optimizing recovery rates and minimizing environmental impact.
Automated disassembly systems using robotics and artificial intelligence are being developed to reduce labor costs in magnet recovery from complex products. These systems can identify, extract, and sort magnets more efficiently than manual processes.
As demand for rare earth magnets continues to grow in clean energy and high-tech applications, these recycling technologies will play an increasingly important role in securing sustainable supply chains and reducing the environmental impacts associated with primary mining operations.
How Do Environmental Impacts Compare Between Rebuilding and Recycling?
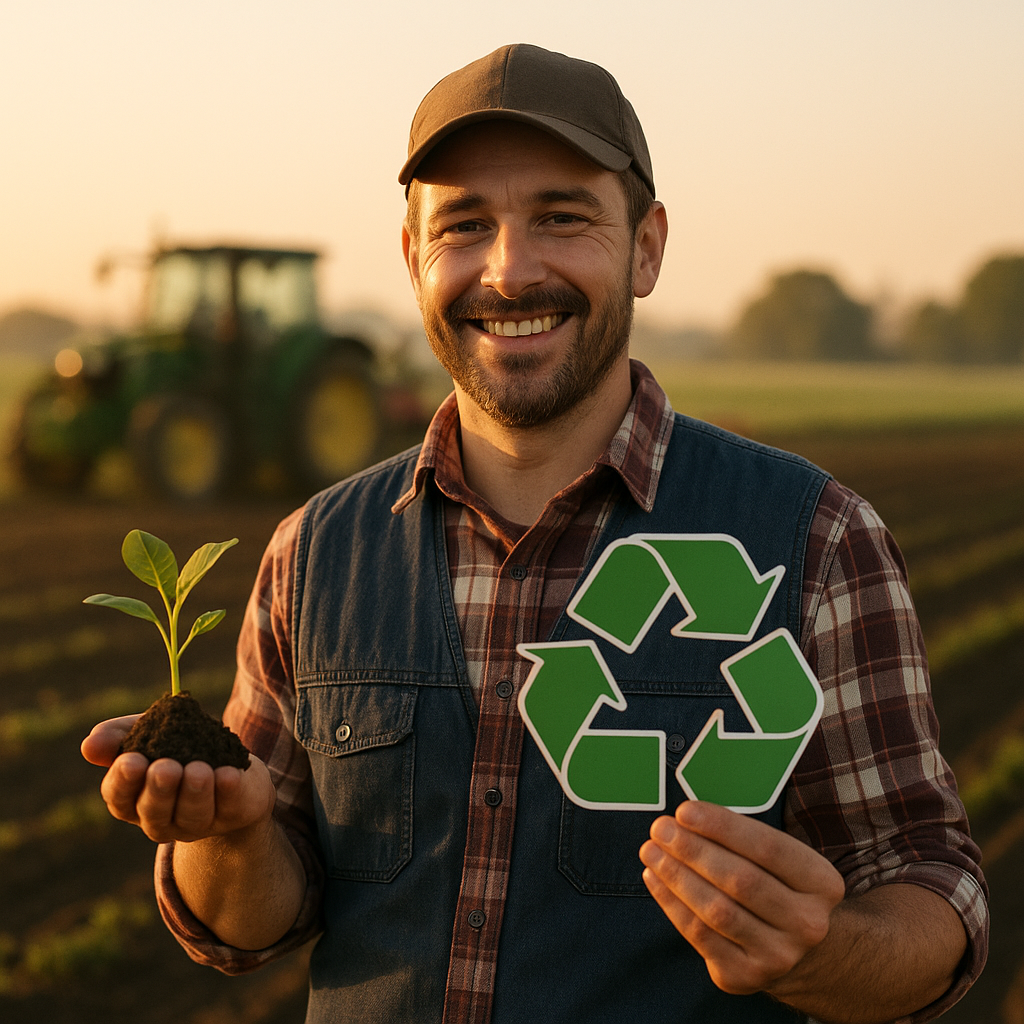
Life cycle assessments (LCAs) reveal that both rebuilding and recycling industrial magnets offer significant environmental benefits compared to primary production. Studies show that recycling rare earth magnets can lead to an over 80% reduction in environmental impact across most categories, making it a compelling alternative to mining and processing virgin materials.
The environmental advantages of recycling emerge primarily from avoiding the resource-intensive extraction processes associated with rare earth elements. Traditional mining generates toxic waste, consumes significant water resources, and often releases radioactive byproducts. In contrast, direct alloy recycling preserves the original composition of magnet materials while requiring much less energy and fewer chemical inputs.
Research indicates that recycled NdFeB magnets produced through large-scale operations can reduce greenhouse gas emissions by 75-85% compared to primary production. For some magnet types, rebuilding processes, where magnets are reprocessed without fully breaking down their components, may offer even greater environmental benefits. Rebuilding typically involves hydrogen processing of magnetic scrap (HPMS) or hydrogenation-disproportionation-desorption-recombination (HDDR) methods that maintain the alloy structure.
When comparing specific environmental impacts between rebuilding and recycling:
- Climate change impact: Rebuilding through remelting and HDDR shows approximately a 65% lower carbon footprint than primary production, while optimized recycling processes can achieve up to a 90% reduction.
- Freshwater ecotoxicity: Both rebuilding and recycling significantly outperform primary production, with recycling showing superior performance at an industrial scale.
- Land use: Recycling reduces land disturbance by over 80% compared to mining operations.
- Water usage: Improved rebuilding processes with closed-loop water systems can reduce water consumption by up to 88%.
Choosing between rebuilding and recycling should consider several key factors, including the condition of waste magnets, material composition, available technologies, and end-use requirements. Magnets with minimal oxidation or contamination are often better candidates for rebuilding, while those with significant degradation may be more suitable for complete recycling.
Technological advancements in both rebuilding and recycling continue to improve environmental performance. Scaling processes, internal recycling of materials, and optimization contribute to reduced impacts. For example, recovering inert gases used in jet milling can avoid energy-intensive gas production, saving approximately 15.9 kWh per processing cycle.
Evaluating which approach provides the greater environmental benefit involves considering the specific magnet type and manufacturing route. Bonded magnets typically show the lowest environmental impact across all recovery methods due to their less energy-intensive production process. For sintered magnets, direct recycling routes that preserve the alloy composition often offer the greatest environmental advantage.
Process | Energy Reduction (%) | Greenhouse Gas Emissions Reduction (%) | Environmental Impact Reduction (%) |
Recycling | 75-85% | ~90% | >80% across most categories |
Rebuilding | N/A | ~65% for carbon footprint | Significant, depending on methods used |
Primary Production | 0% | 0% | Baseline |
As industries aim to reduce their environmental footprint while securing critical material supplies, both rebuilding and recycling strategies offer valuable alternatives to primary production. The growing adoption of these approaches in magnet manufacturing not only benefits the environment but also enhances resource security and economic sustainability in the market for rare earth magnets.
What Are the Future Trends in Industrial Magnet Management?
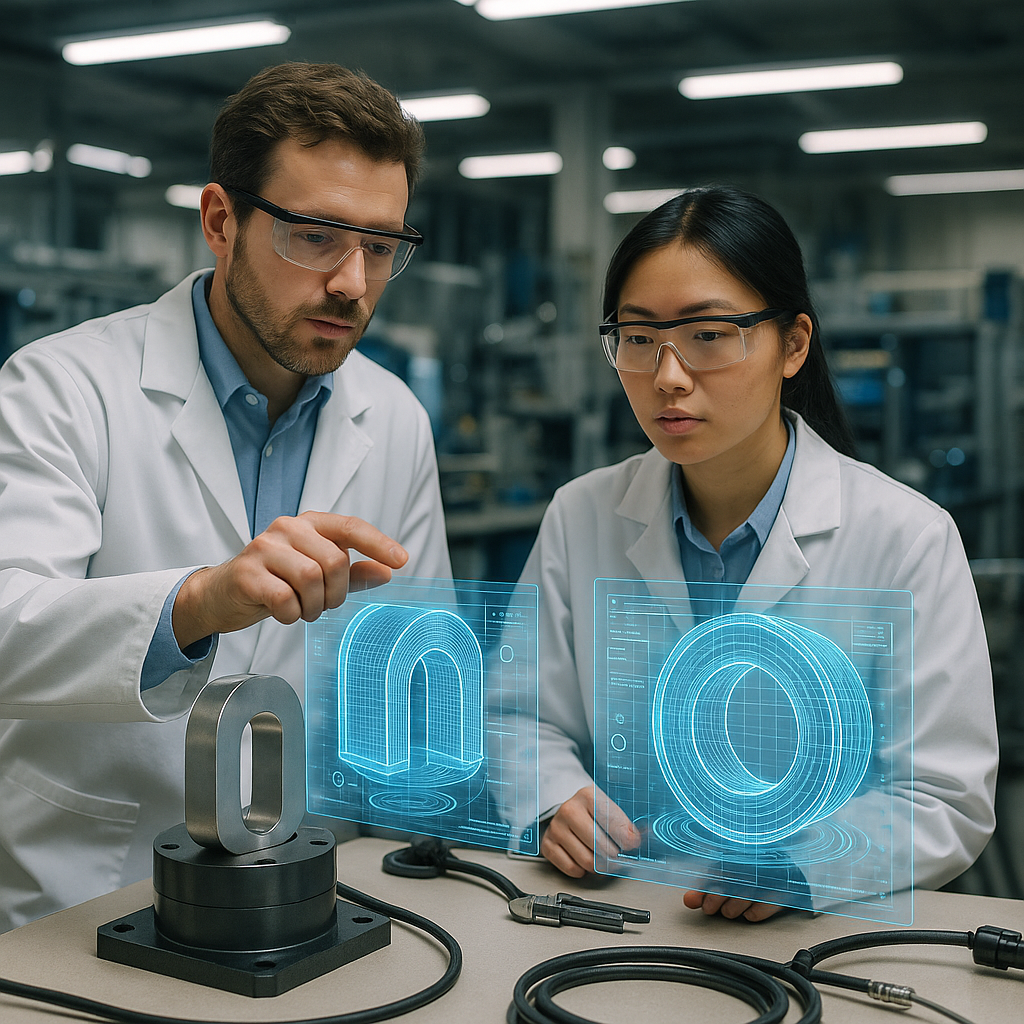
The industrial magnet management landscape is evolving rapidly. Advances in hydrogen-assisted recycling technologies now enable the recovery of high-quality materials from end-of-life magnets with significantly lower energy requirements than virgin production. Progressive manufacturers are embracing design for recyclability, creating magnets with compositions and configurations that support future material recovery. Notably, the emergence of closed-loop systems allows manufacturers to take responsibility for their products’ entire lifecycle, collecting and reprocessing their own magnets while reducing waste and resource extraction.
As the demand for magnets in renewable energy and electric vehicles continues to grow, sustainable magnet management is more important than ever. The industry is actively exploring alternative materials that reduce dependence on rare earth elements while maintaining performance. These innovations, combined with improving collection infrastructure and evolving regulations, suggest a more sustainable future for industrial magnets.
For expert guidance on implementing effective magnet recycling strategies for your operation, contact Okon Recycling at 214-717-4083.