5901 Botham Jean Blvd, Dallas, TX 75215
Learn the Environmental Impact of Rare Earth Magnets
July 25, 2025Rare earth magnets are powerful permanent magnets made from alloys containing rare earth elements. Neodymium-iron-boron (NdFeB) is the most common type, offering exceptional magnetic strength despite its small size. These magnets are essential components in many modern technologies, from smartphones and hard drives to wind turbines and electric vehicles.
The environmental impact of these magnets starts at extraction and continues through their lifecycle. Mining operations for rare earth elements like neodymium and dysprosium create massive open-pit mines that destroy habitats and alter landscapes. These operations generate significant quantities of toxic tailings containing radioactive materials such as thorium and uranium, which naturally occur alongside rare earth deposits.
Processing these elements requires harsh chemicals, including sulfuric acid and ammonia, which can contaminate local water systems if improperly managed. The separation and refining processes consume enormous amounts of energy, often from coal-powered plants, releasing greenhouse gases and air pollutants. Producing a single ton of rare earth oxide can require 200-400 cubic meters of water, further straining environmental resources in mining regions.
How Does Rare Earth Mining Affect the Environment?
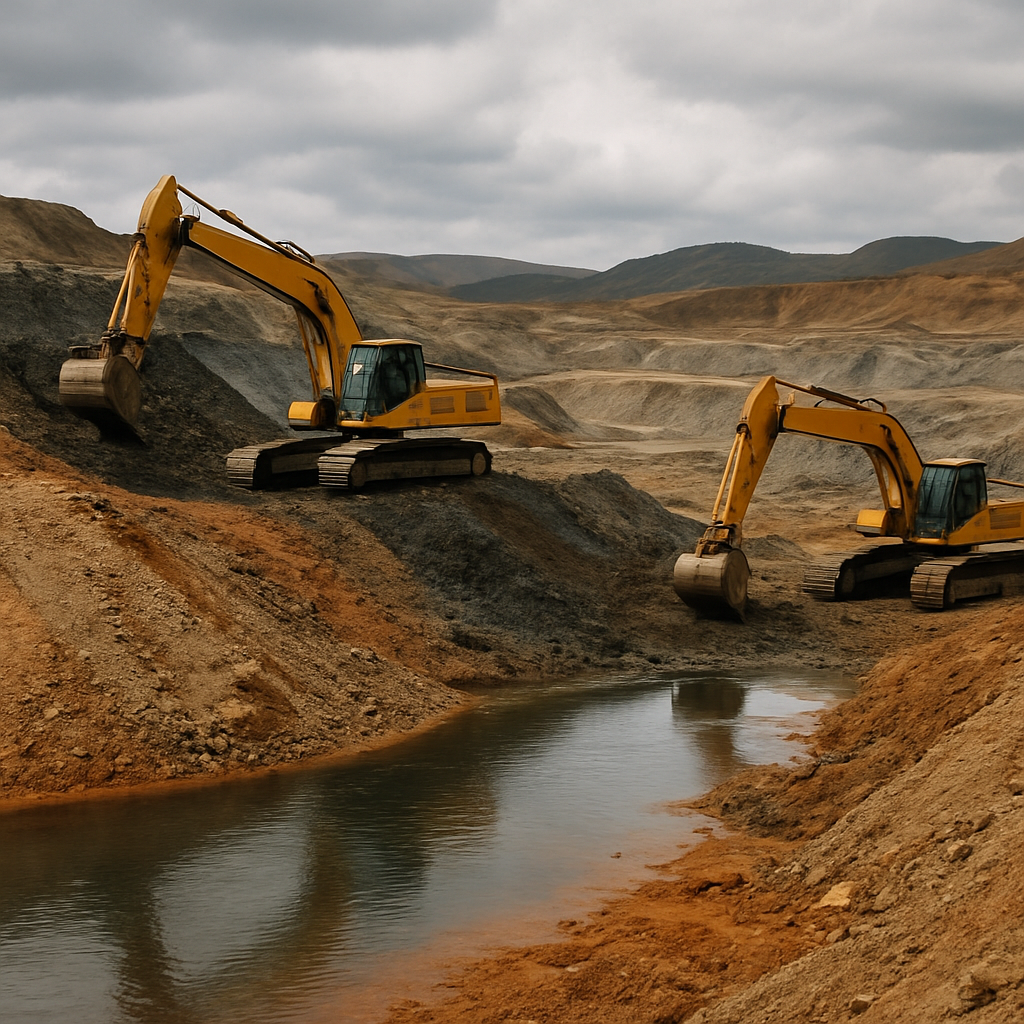
Rare earth elements mining causes extensive environmental damage through multiple pathways. Open-pit mining, the most common method for extracting these minerals, transforms vibrant ecosystems into barren industrial zones, leaving lasting scars on the landscape.
The mining process begins with clearing large tracts of land. Heavy machinery strips away topsoil and vegetation, destroying habitats for local wildlife and plant species. At China’s Bayan Obo mine, one of the world’s largest rare earth mining operations, this land clearance has accelerated desertification, allowing the Gobi Desert to encroach into once-fertile areas.
Water systems suffer severe impacts from rare earth mining. The extraction process requires vast amounts of water, altering natural groundwater patterns. Acid mine drainage occurs when rainwater flows through exposed mining materials, creating acidic runoff that harms aquatic ecosystems. This runoff can contain heavy metals like cadmium and lead, along with radioactive elements like thorium and uranium that naturally occur alongside rare earths.
Chemical contamination is another serious threat. Processors use strong acids and solvents, including sulfuric acid and ammonia, to separate rare earth elements from raw ore. These chemicals can leak into soil and water, poisoning agricultural land and drinking water sources. In Malaysia, concerns about radioactive waste from rare earth processing led to public protests when approximately 1.5 million metric tons of waste were stored in hills near Kuantan without permanent containment solutions.
Air quality deteriorates significantly near mining operations. The extensive crushing and grinding of ore releases fine dust particles containing toxic materials that can travel for miles. Workers and nearby communities face increased risks of respiratory issues, with some studies showing higher rates of pulmonary fibrosis and lung inflammation among those exposed to rare earth processing fumes.
Soil degradation extends beyond the immediate mining area. Aside from chemical contamination, mining activities compact soil, increase erosion, and deplete nutrients. The resulting landscape becomes nearly impossible to reclaim for agriculture or to restore to its natural state. In areas with mountainous terrain, this soil disruption raises the risk of dangerous landslides.
The environmental footprint of rare earth mining extends far beyond the extraction site. Studies from the Chinese State Council acknowledged that rare earth mining has caused “severe damage to the ecological environment,” with evidence of vegetation destruction, water pollution, and landslides in mining regions. The environmental cost of obtaining these valuable minerals continues to raise serious questions about sustainability in the industry.
How Do Rare Earth Magnets Impact Green Energy Technologies?
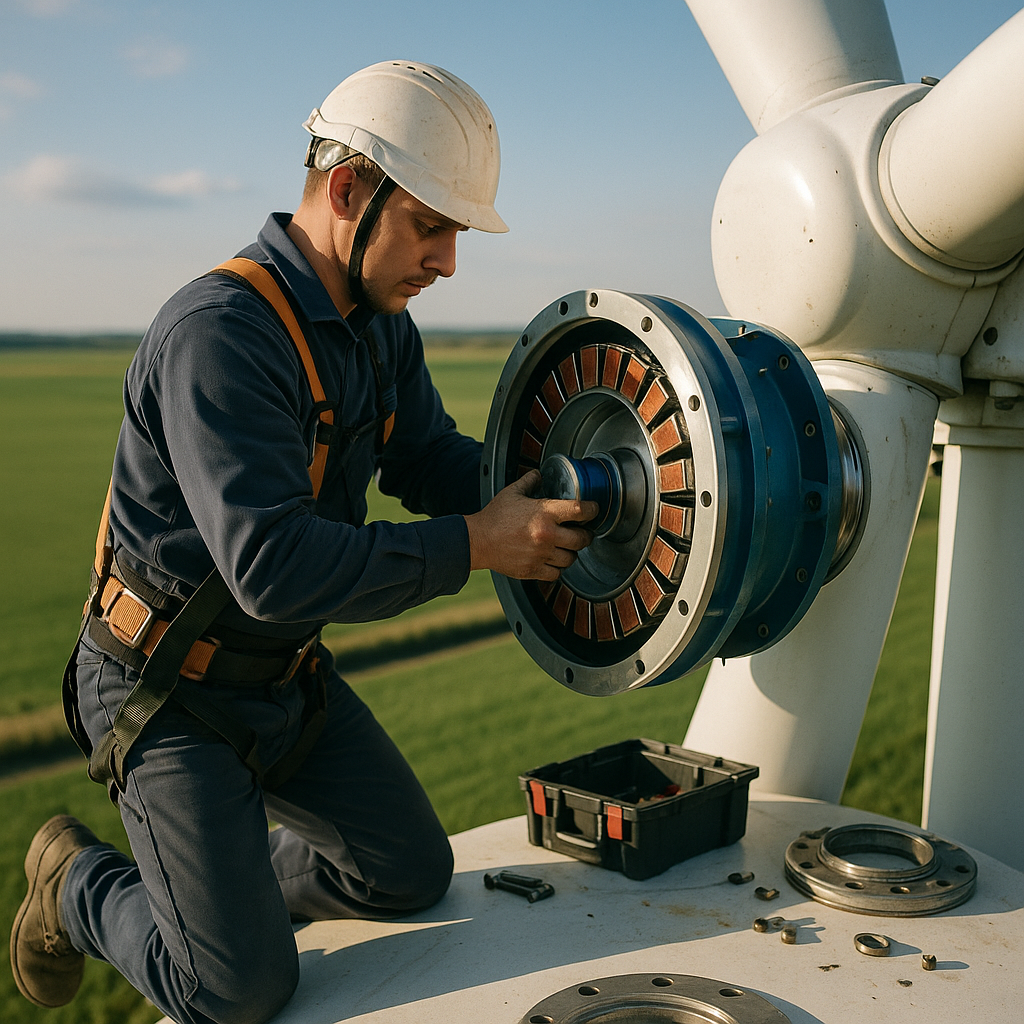
Rare earth magnets are essential to the advancement of renewable energy, powering wind turbines and electric vehicles with exceptional efficiency. Without these powerful magnets, progress in clean energy would falter. However, their production presents a paradox that questions the sustainability of green technologies.
The environmental impact of producing these magnets creates a sustainability challenge. Recent studies show that each 1% increase in green energy production depletes approximately 0.18% of rare earth element reserves. More concerning is the associated 0.90% rise in greenhouse gas emissions during mining and processing phases.
The Carbon Footprint Paradox
The carbon emissions from rare earth magnet production are significant. Between 2010 and 2020, permanent magnets used in green technologies produced 32 billion tonnes of CO2-equivalent emissions globally, nearly equaling a year’s total global greenhouse gas emissions.
Wind turbines—often lauded for carbon-free energy—require significant amounts of neodymium and dysprosium. A typical offshore wind turbine contains up to 232 kg of neodymium-praseodymium (NdPr) per megawatt, accruing environmental costs before generating electricity.
Mining operations in countries like China and Myanmar result in open pits that devastate natural habitats. The separation process employs harsh chemicals, such as sulfuric acid and ammonia, which produce toxic waste. Additionally, radioactive waste containing thorium and uranium persists for generations.
Electric Vehicles: Clean Operation, Dirty Production
Electric vehicles face similar contradictions. While they emit no tailpipe emissions, their motors contain 0.5-1.5 kg of neodymium. Extracting and processing these materials inflicts substantial environmental damage long before the vehicles are on the road.
Magnet production facilities consume large amounts of energy, often sourced from coal-dependent grids. This highlights the irony that materials crucial for clean energy technologies have significant environmental costs.
Supply Chain Challenges
The geographic concentration of rare earth processing adds another layer to the sustainability challenge. China dominates approximately 60% of global rare earth oxide mining and over 85% of processing capacity, creating supply vulnerabilities and potential market instability.
Demand for rare earth magnets continues to escalate. Industry forecasts indicate the global rare earth magnet market will reach USD 17.44 billion by 2028, up from USD 10.97 billion in 2022, reflecting a 8.03% compound annual growth rate.
The European Union alone is expected to require around 13,000 tonnes of neodymium and praseodymium for wind turbines by 2030, with projections increasing to 69,600 tonnes by 2050.
Finding Balance: Technological Solutions
Researchers are developing solutions to mitigate these impacts. Recycling rare earth elements from discarded magnets and electronic waste is promising, requiring 75-85% less energy than primary production. Advanced techniques like spark plasma sintering create high-performance magnets with improved thermal stability while using less energy.
Developing alternative magnet materials that reduce or eliminate reliance on rare earth elements is another approach. Magnetocaloric materials and iron-nitride magnets offer potential for specific applications. Companies like Toyota are planning to eliminate rare earth elements from their electric motors.
Green manufacturing processes that incorporate renewable energy sources have shown potential to reduce carbon footprints by up to 60%. Some facilities have implemented closed-loop water systems that recycle up to 90% of water used in production.
The path toward truly sustainable green energy technology requires addressing these contradictions. Without careful attention to rare earth magnets’ full lifecycle impacts, clean energy systems risk having dirty supply chains—undermining the environmental benefits they intend to deliver.
What Solutions Exist for Reducing the Environmental Impact?
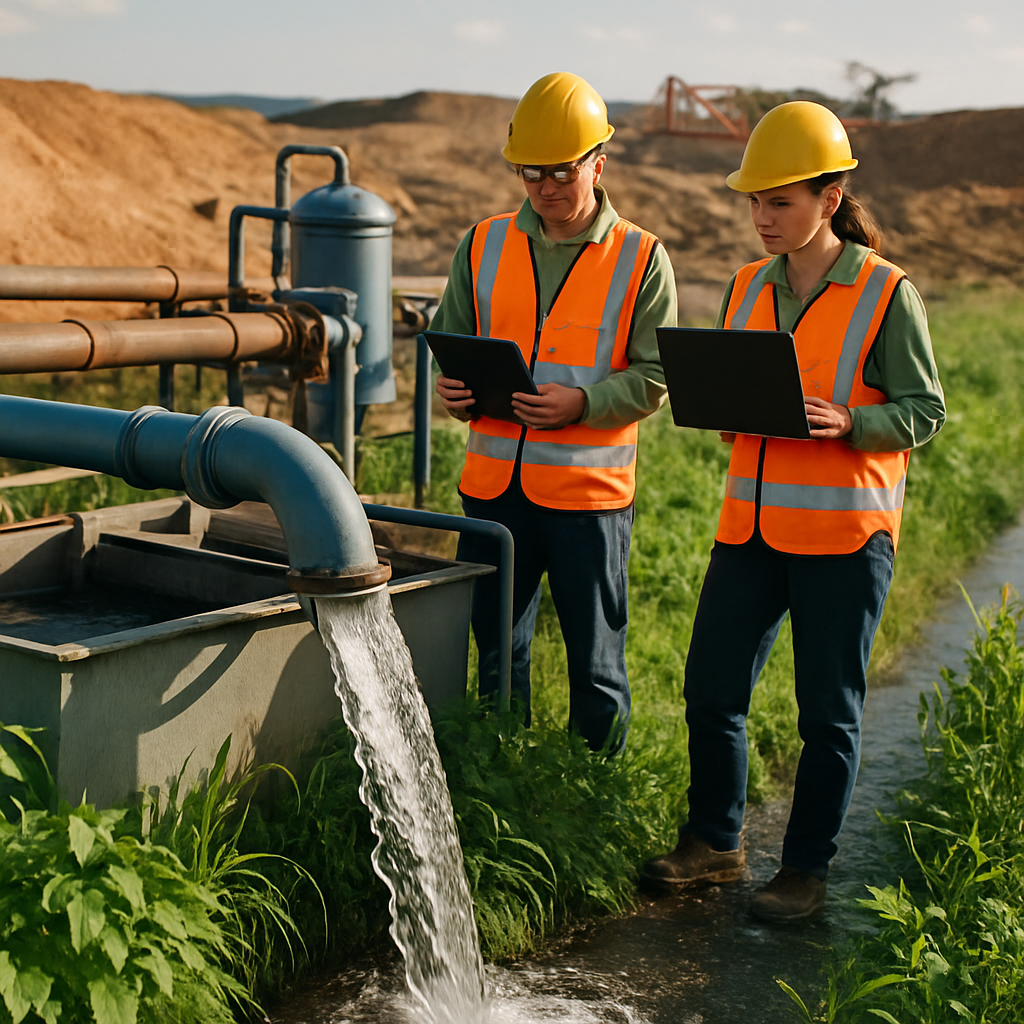
Addressing the environmental challenges posed by rare earth magnets requires a comprehensive approach. The mining and processing of rare earth elements generate significant pollution, including toxic waste and greenhouse gas emissions. Fortunately, several promising solutions have emerged to mitigate these impacts while maintaining access to these critical materials for green technologies.
Recycling rare earth elements from discarded magnets and electronic waste is one of the most effective strategies. This process requires 75-85% less energy than primary production methods, substantially reducing the carbon footprint associated with these materials. Companies like Noveon Magnetics have established supply chains that secure scrap material at reasonable prices, demonstrating the economic viability of recycling operations.
The hydrogen-based recycling process (HPMS) shows particular promise for efficiently processing post-consumer goods. However, this method requires high-purity feedstock to operate effectively, highlighting the need for improved collection and sorting systems. Currently, less than 1% of rare earth elements are recycled globally, indicating enormous untapped potential in this area.
Alternative Materials Development
Developing alternative magnetic materials offers another path toward sustainability. Iron nitride magnets represent a promising option as they can be produced from abundant, low-cost materials. These alternatives aim to maintain necessary performance characteristics while reducing or eliminating dependence on scarce rare earth elements.
Several automotive manufacturers have announced plans to reduce or eliminate rare earth magnets in their motors. Toyota has developed technology that cuts dysprosium use by up to 50% in their magnets, while Tesla has explored motors that function without rare earth elements entirely. These innovations reflect industry commitment to finding sustainable alternatives.
Magnetocaloric materials, which achieve low energy consumption through temperature changes rather than traditional magnetic properties, represent another promising research direction. High-entropy alloys (HEAs) are also being explored, as these multi-element compositions may achieve magnetic properties comparable to rare earth-based magnets.
Green Manufacturing Processes
Improving manufacturing processes is another critical avenue for environmental impact reduction. Implementing renewable energy sources in production facilities can significantly lower the carbon footprint of magnet manufacturing. Advanced sintering techniques enhance magnetic properties while minimizing material waste.
Closed-loop water systems in production facilities reduce water consumption and prevent contamination of local water sources. This approach is especially important given the water-intensive nature of rare earth processing. Some companies have also developed acid-free processes for recovering rare earth elements, eliminating the need for harsh chemicals that pose environmental risks.
TdVib offers an example of green innovation with their water-soluble method to dissolve magnets. Unlike conventional approaches that require corrosive acids and high-energy processes, this technique significantly reduces environmental impact while maintaining extraction efficiency.
Policy and Collaborative Frameworks
Supportive policy frameworks play an essential role in driving sustainable practices. Extended producer responsibility policies can encourage manufacturers to design products with recycling in mind. Research subsidies and tax incentives for companies developing alternative materials or recycling technologies help overcome economic barriers to innovation.
International collaboration presents another crucial element for addressing environmental challenges. Organizations like the Rare Earth Industry Association (REIA) unite stakeholders worldwide to develop standards and best practices for sustainable production and recycling. These collaborative efforts help distribute research burdens and leverage global talent to tackle complex sustainability challenges.
Transparency initiatives that track rare earth elements through their lifecycle create accountability and help identify opportunities for improvement. By implementing traceability systems and certification schemes, companies can verify sustainable sourcing and build consumer trust.
The combined effect of these approaches—recycling, alternative materials, improved manufacturing, and supportive policies—creates a pathway toward significantly reduced environmental impact from rare earth magnets. As these solutions scale up, they promise to make these essential components of green technology truly sustainable throughout their lifecycle.
Conclusion: Balancing Green Technology and Environmental Protection
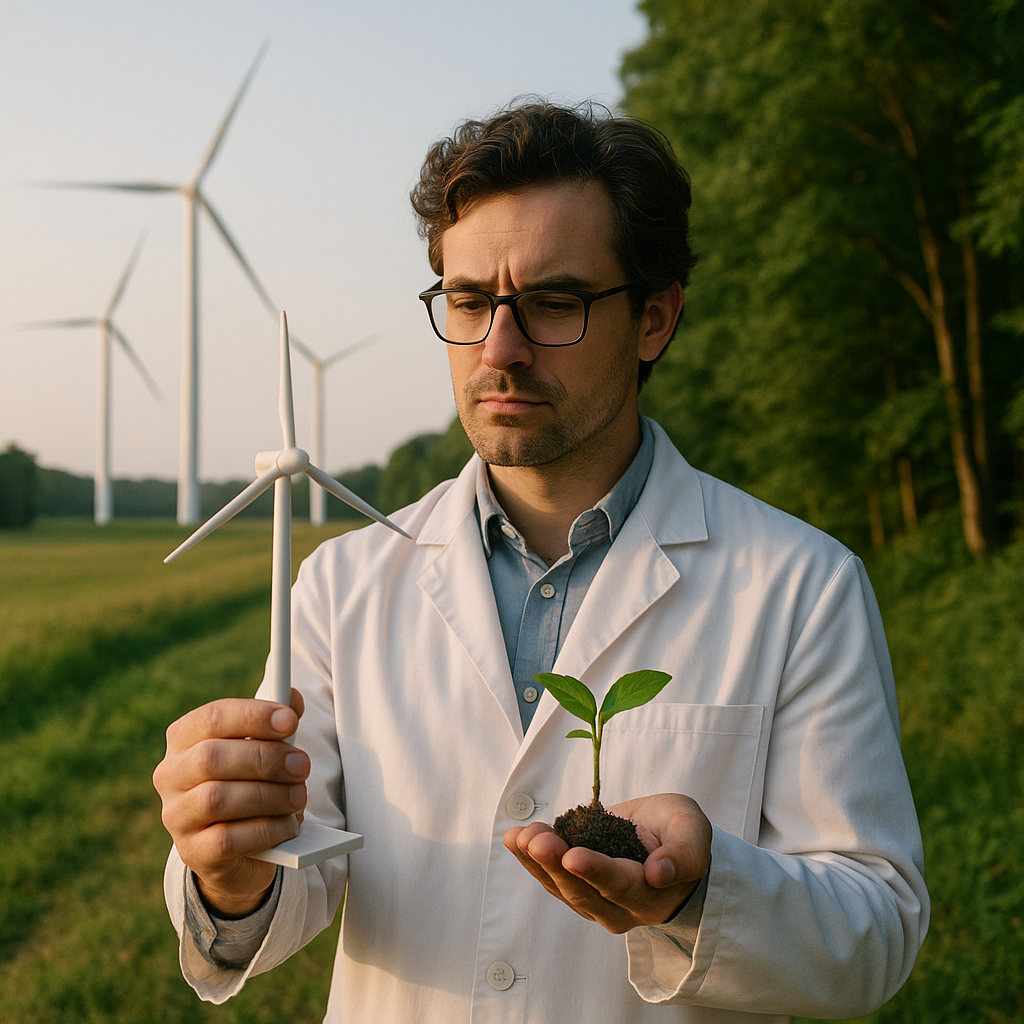
The environmental impact of rare earth magnets is a challenging paradox in our shift to green energy. These crucial magnets are key components in wind turbines and electric vehicle motors—technologies that help lower carbon emissions. Yet, their production often involves destructive mining practices, toxic processing chemicals, and significant energy use.
Achieving balance requires a multifaceted approach. Recycling rare earth elements shows promise, with both short-loop and long-loop strategies providing ways to reduce dependence on environmentally harmful primary extraction. Additionally, developing alternative materials like manganese-aluminum-carbon alloys and enhancing manufacturing techniques can reduce reliance on critical rare earth elements. For businesses and policymakers, understanding the complete lifecycle impact of these materials is vital for making truly sustainable choices.
For assistance with recycling solutions that can help reduce your organization’s environmental footprint while maintaining access to these critical materials, contact Okon Recycling at 214-717-4083.