5901 Botham Jean Blvd, Dallas, TX 75215
What Are Small Powerful Magnets and How Do They Work?
June 30, 2025A small rare earth magnet can lift objects more than 1,000 times its own weight. These tiny powerhouses represent significant achievements in materials science. Known as rare earth magnets, they derive their extraordinary strength from elements in the lanthanide series of the periodic table.
Rare earth magnets primarily consist of alloys containing neodymium or samarium combined with transition metals like iron or cobalt. Neodymium magnets (NdFeB) typically include neodymium, iron, and boron, while samarium cobalt magnets (SmCo) combine samarium with cobalt. These combinations create materials with unique crystalline structures that concentrate magnetic fields in a highly directional manner.
The process occurs at the atomic level. In these magnets, unpaired electrons align in the same direction, creating strong, persistent magnetic fields. Their crystal structures—hexagonal for samarium cobalt and tetragonal for neodymium—allow them to maintain this alignment even in compact forms. This explains why these small magnets can generate magnetic fields vastly stronger than traditional ferrite or alnico magnets of the same size.
What Are the Different Sizes and Applications of Small Powerful Magnets?
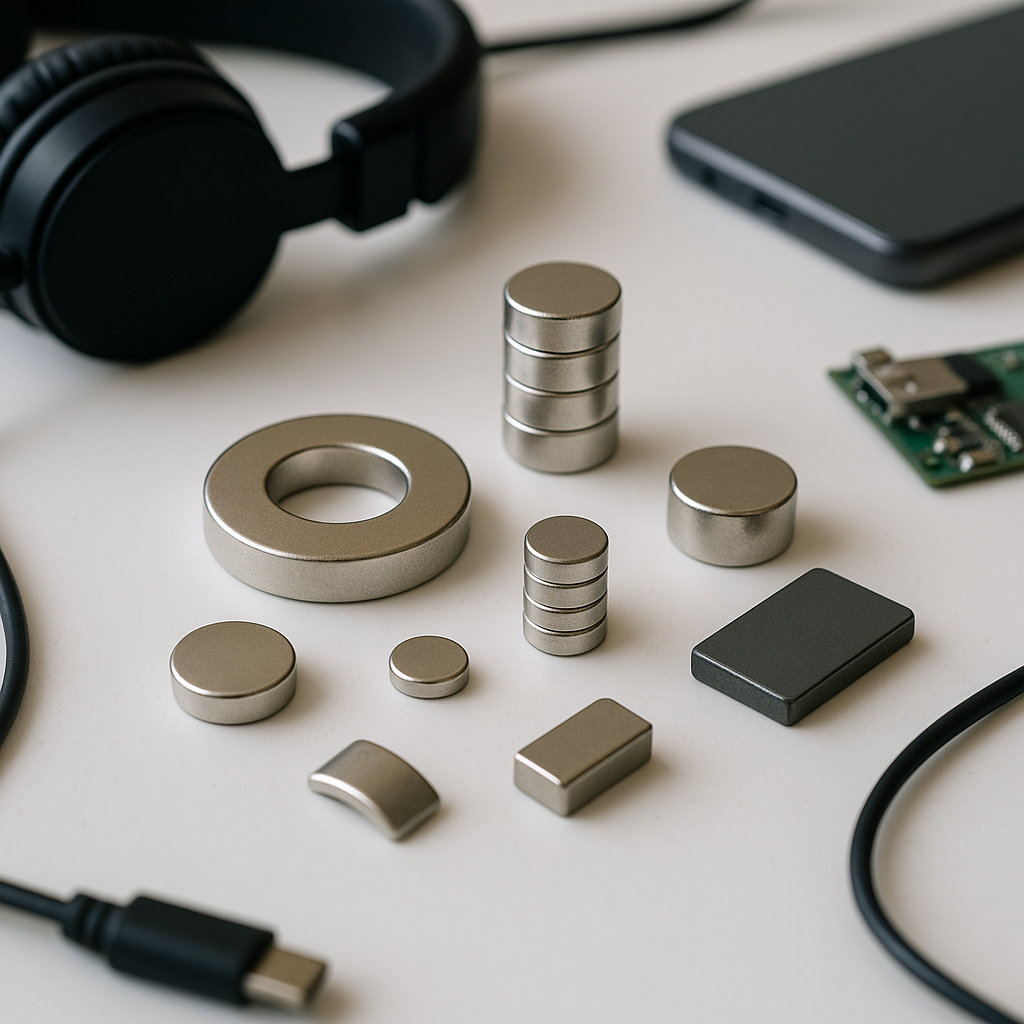
Small rare earth magnets come in various sizes, typically ranging from 1mm to 10mm. Despite their small size, these magnets are remarkably strong due to their neodymium composition. Each size category serves specific functions across different industries based on its unique dimensions.
Micro Magnets (1mm-3mm)
The smallest rare earth magnets, measuring between 1mm and 3mm, play critical roles in precision applications. At just 1mm, they are perfect for delicate jewelry making, providing subtle connections. Their minimal footprint makes them ideal for intricate crafts requiring nearly invisible closures.
In the medical field, micro magnets facilitate innovations in diagnostic equipment. Some medical devices use 2mm magnets in sensors for tracking patient movement or in medication delivery systems. Their small size allows non-invasive monitoring without adding bulk to sensitive instruments.
Consumer electronics manufacturers use these small magnets in earbuds, smartphone speakers, and vibration motors. A typical wireless earbud contains multiple 2-3mm magnets that secure the earpiece in its charging case while maintaining a sleek profile.
Mid-Range Magnets (4mm-7mm)
Magnets between 4mm and 7mm strike a balance between size and strength. These versatile magnets find applications in automotive systems, where space constraints exist but significant holding power is needed. Many sensor assemblies in modern vehicles use 5mm magnets to detect position and movement.
The technology sector heavily utilizes this size range in hard disk drives and various computer components. A standard HDD contains multiple 5mm magnets that control read/write head movement with precision. Their reliability makes them crucial for data storage systems worldwide.
Home applications also benefit from these mid-sized magnets. Cabinet latches, refrigerator door seals, and decorative holders typically use 6mm magnets that provide sufficient strength without requiring special handling procedures.
Power Magnets (8mm-10mm)
The largest small rare earth magnets, ranging from 8mm to 10mm, deliver impressive magnetic force for industrial applications. Manufacturing equipment relies on these magnets for automated sorting processes and component alignment. Their substantial pull force enables secure connections in vibration-prone environments.
Aerospace technology implements these powerful magnets in critical systems. Aircraft sensors and control mechanisms use 10mm magnets that maintain reliability under extreme conditions. Their resistance to demagnetization at high temperatures makes them suitable for demanding aerospace applications.
Renewable energy systems also benefit from these larger magnets. Wind turbine generators use numerous 8-10mm magnets to help convert mechanical rotation into electrical output. Their efficiency contributes to improved energy generation in sustainable power sources.
Industry-Specific Applications
Beyond size categories, small powerful magnets serve specialized roles across various industries. In electric motors, these magnets create the magnetic fields necessary for energy conversion. Their high magnetic flux density enables the development of compact, efficient motors for everything from power tools to electric vehicles.
Medical devices leverage these magnets for both diagnostic and therapeutic purposes. MRI machines use precisely arranged magnets to generate detailed body images. Surgical tools incorporate small magnets for guidance systems that improve precision during delicate procedures.
The growing field of robotics relies heavily on small rare earth magnets. Robotic joints, grippers, and sensors utilize these components for smooth movement and accurate positional feedback. Their high strength-to-weight ratio makes them ideal for applications where weight considerations are critical.
What Are the Advantages of Using Small Powerful Magnets?
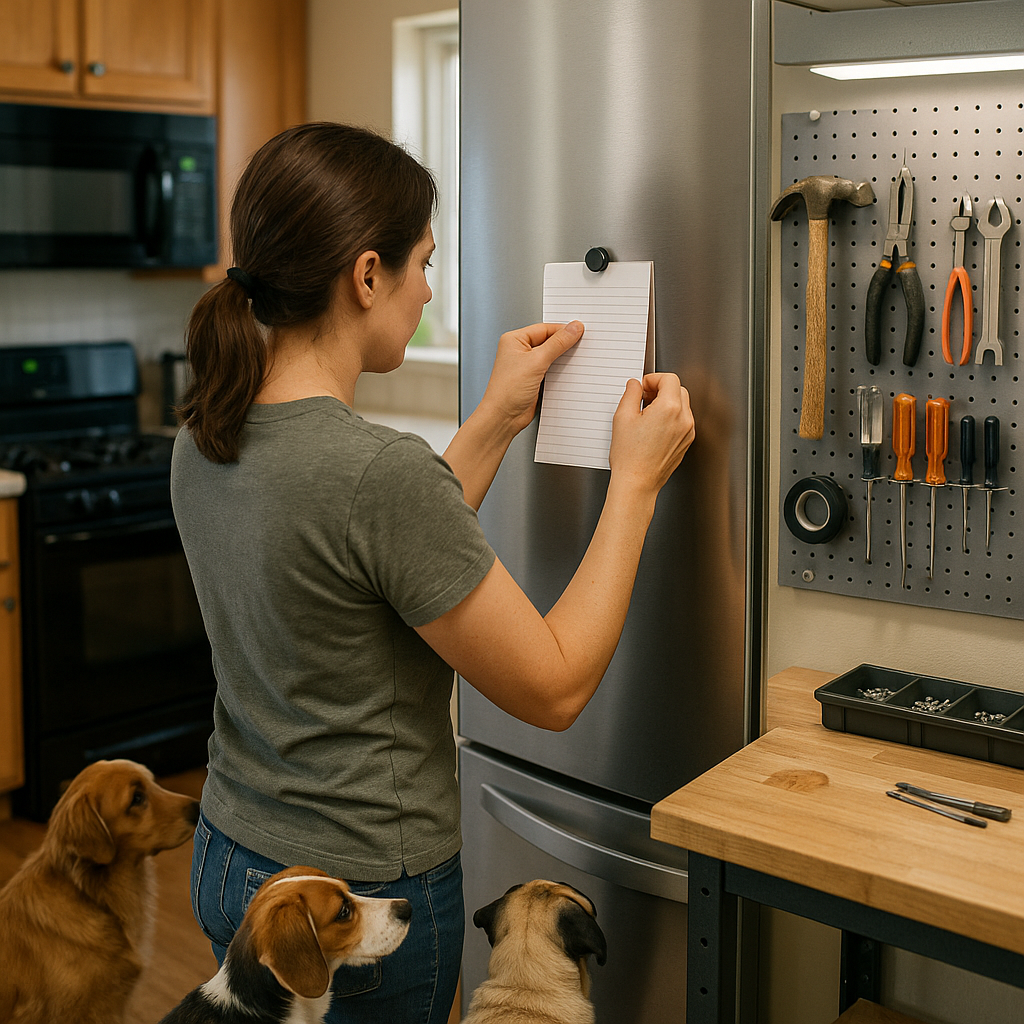
Small, powerful magnets offer great capabilities in compact forms. Their magnetic strength allows them to lift objects many times their own weight, making them essential in situations where space is limited but power is required.
One key advantage is their exceptional magnetic stability. Unlike larger, less powerful alternatives, small magnets like neodymium and samarium-cobalt provide superior resistance to demagnetization, ensuring consistent performance in challenging environments.
The size-to-strength ratio delivers significant practical benefits:
- Space efficiency – Their compact dimensions allow integration into tight spaces in electronic devices, medical equipment, and precision instruments.
- Weight reduction – Small, powerful magnets contribute to lighter products without sacrificing magnetic performance, crucial for aerospace and portable electronics.
- Design flexibility – Engineers can create more compact and versatile products by using powerful magnets that require minimal space.
Different types offer specialized advantages for specific applications. Samarium-cobalt magnets, although more costly than some alternatives, provide exceptional corrosion resistance and withstand temperatures up to 300°C (572°F). They are ideal for challenging environments like automotive sensors, industrial equipment, and high-temperature manufacturing processes.
The long-term reliability of small, powerful magnets is another benefit. Once magnetized, high-quality neodymium magnets retain their magnetic properties for decades with minimal degradation, reducing replacement costs and maintenance needs in industrial applications.
In material handling, small, powerful magnets enable precise separation and lifting capabilities. For example, recycling facilities use them to effectively separate ferrous materials from mixed waste streams, enhancing recovery rates and product purity.
What Are the Challenges and Considerations When Using Small Powerful Magnets?
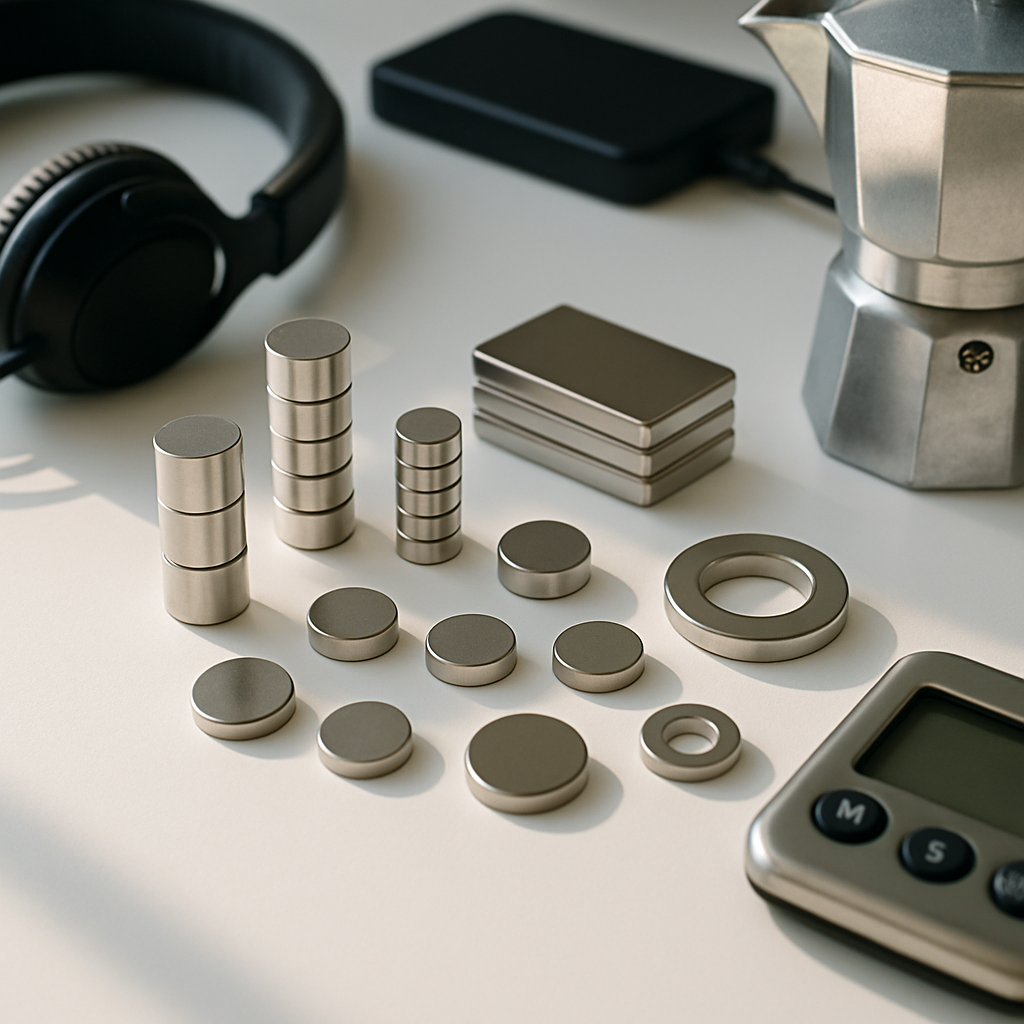
Small, powerful magnets like neodymium offer exceptional strength in compact sizes, but this remarkable power comes with significant challenges. The rarity of materials and sophisticated manufacturing processes make these magnets relatively expensive compared to conventional alternatives. Many industrial users find cost a key consideration when scaling up applications.
Brittleness is another major concern with these magnets. Unlike more malleable materials, small, powerful magnets can chip or crack when subjected to mechanical impacts. This fragility requires careful handling during installation and operation. Their brittle nature also limits their use in applications where physical stress is common.
Safety risks are considerable when working with small, powerful magnets. Their strong magnetic fields can cause serious pinching injuries when fingers get caught between attracting magnets. Professional recycling facilities often implement strict handling protocols for processing equipment containing these magnets to prevent workplace accidents.
Environmental Sensitivities
Temperature sensitivity presents a significant challenge for many small, powerful magnets. Neodymium magnets can lose their magnetic properties when exposed to temperatures above 175°F (80°C). In extreme cases, they may catch fire and produce toxic fumes, creating hazardous conditions. This limits their use in high-temperature environments without proper engineering controls.
Corrosion vulnerability also affects uncoated neodymium magnets, particularly in humid environments. When exposed to moisture, these magnets can rapidly deteriorate, reducing their strength and effectiveness. Protective coatings like nickel-copper-nickel, epoxy, or parylene are essential for maintaining magnet integrity in challenging environments.
Handling Precautions
Working with small, powerful magnets requires specific safety measures. Wearing protective gloves and eye protection is essential when handling larger magnets. The risk of breakage is high due to their brittle nature, and flying fragments can cause serious eye injuries. Non-metallic tools like plastic wedges should be used for separating magnets instead of manual force.
Storage considerations are equally important. These magnets should be kept in closed, clean containers away from electronic devices, magnetic media, and medical devices like pacemakers. Different types of magnets should not be stored together, as this can lead to demagnetization. Using spacers or keepers during storage prevents unintended attraction between magnets.
Despite these challenges, with proper handling procedures and application-specific engineering, small, powerful magnets continue to enable technological advances across numerous industries. Understanding these limitations allows for safer, more effective use of these remarkable materials.
Conclusion: Harnessing the Power of Small Magnets
Small, powerful magnets are key drivers of innovation and efficiency across many industries. These compact devices provide exceptional magnetic force despite their size, making them indispensable in modern technology and manufacturing. From healthcare equipment like MRI machines to sustainable energy solutions in wind turbines, these magnets consistently demonstrate versatility and effectiveness.
The applications of small, powerful magnets span nearly every economic sector. In consumer electronics, they enable the miniaturization of speakers and sensors while maintaining high performance. In automotive systems, they power critical components such as electric motors and sensors that enhance vehicle efficiency and safety. In industrial settings, they facilitate precision manufacturing, material separation, and automation that would otherwise be unattainable. For recycling needs and to explore sustainable solutions for magnet disposal and recovery, contact Okon Recycling at 214-717-4083.