5901 Botham Jean Blvd, Dallas, TX 75215
What Are Samarium Cobalt Magnets?
June 30, 2025Samarium cobalt magnets are powerful permanent magnets from the rare-earth magnet family. These specialized magnets combine samarium, a rare-earth element, with cobalt, a transition metal, resulting in a remarkably strong magnetic material with exceptional properties for specialized applications.
Developed in the early 1960s by Karl Strnat and Alden Ray, SmCo magnets marked a milestone as the first commercially viable rare-earth magnets. This breakthrough opened new possibilities for industries requiring compact yet powerful magnetic solutions. Unlike conventional magnets, these rare-earth types deliver significantly stronger magnetic fields relative to their size.
Samarium cobalt magnets are distinguished by their impressive features. They maintain magnetic strength at high temperatures (up to 300°C), resist corrosion without protective coatings, and offer excellent resistance to demagnetization. These characteristics make them indispensable in aerospace, defense, medical, and other high-performance applications where reliability under extreme conditions is essential.
What are the Key Properties of Samarium Cobalt Magnets?
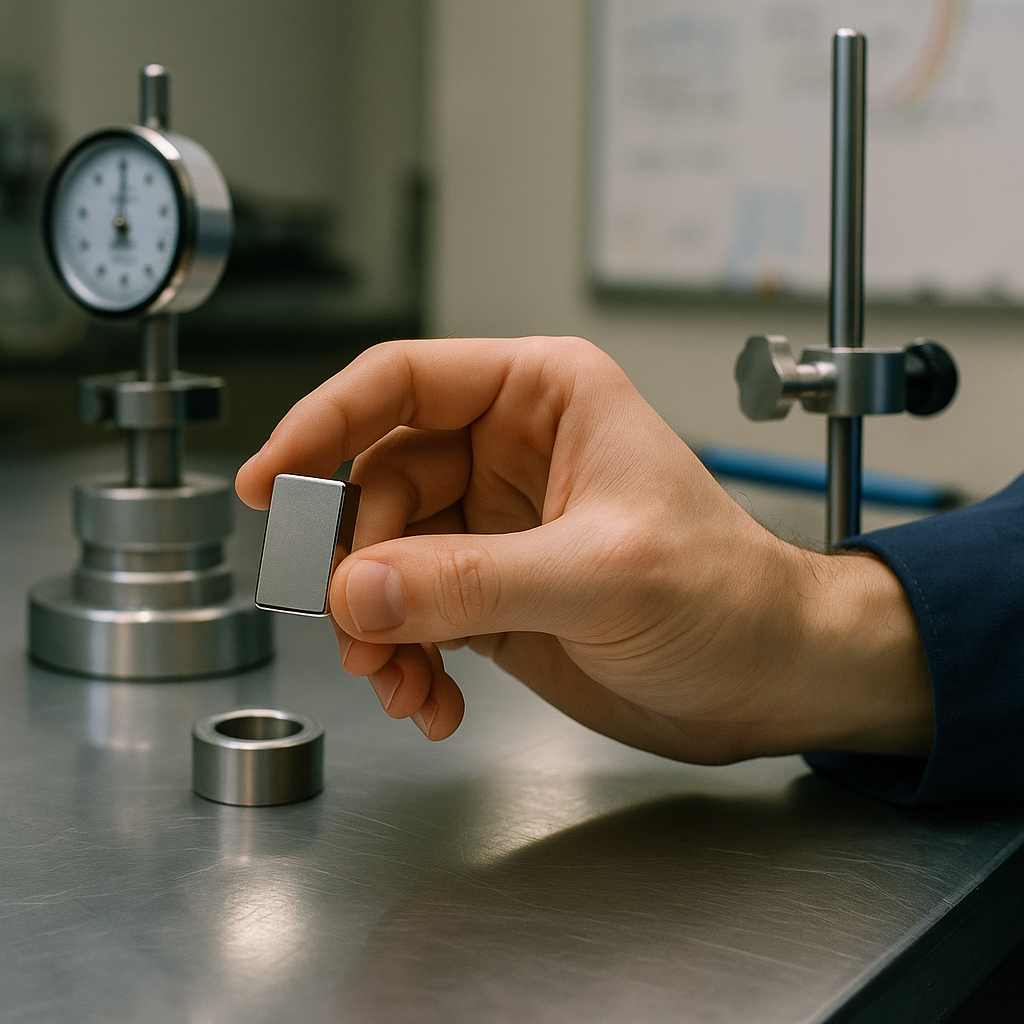
Samarium cobalt magnets are among the strongest permanent magnets available. These powerful rare earth magnets offer significant magnetic strength, with energy products ranging from 16 to 33 MGOe, making them second only to neodymium magnets.
These magnets are renowned for their exceptional temperature stability. They perform reliably at temperatures up to 350°C (662°F), with minimal changes in magnetic output across a wide temperature range, making them ideal for high-temperature industrial applications where other magnets might fail.
Additionally, they exhibit superior corrosion resistance. Unlike neodymium magnets, which contain 60-70% iron and require protective coatings, samarium cobalt magnets have minimal iron content. Their natural resistance to oxidation and corrosion allows them to function effectively in harsh environments without extra protective measures.
Types of Samarium Cobalt Magnets
Samarium cobalt magnets are available in two main types: SmCo5 and Sm2Co17, each offering specific advantages for different applications.
- SmCo5 (1:5 Series): The first generation of samarium cobalt magnets includes one samarium atom with five cobalt atoms, typically containing 15-25% samarium and 5-7% cobalt.
- Sm2Co17 (2:17 Series): The second generation includes two samarium atoms with seventeen cobalt atoms, containing 33-37% samarium and 12-14% cobalt, often with additional elements.
SmCo5 magnets provide better corrosion resistance and machinability since they contain no iron. Their energy products range from 16-24 MGOe, and they can operate at temperatures up to 250°C. Despite their lower magnetic strength compared to Sm2Co17, they often cost more due to higher cobalt content.
Sm2Co17 magnets offer greater magnetic strength with energy products reaching 26-33 MGOe. They can operate at higher temperatures up to 350°C. While they contain a small amount of iron, which may make them slightly susceptible to corrosion in extreme environments, they still provide excellent corrosion resistance compared to other magnetic materials.
Demagnetization Resistance
Both types of samarium cobalt magnets show remarkable resistance to demagnetization. Their high coercivity makes them suitable for applications where magnetic stability is critical, such as sensors and magnetic bearings. They maintain their properties even in strong opposing magnetic fields, ensuring reliable performance in complex systems.
The Sm2Co17 type exhibits higher coercivity than SmCo5, making it even more resistant to demagnetization. This feature is particularly valuable in applications with strong demagnetizing fields or where any loss of magnetic strength could compromise system performance.
Samarium cobalt magnets also perform well at extremely low temperatures. They retain their magnetic properties at temperatures as low as -273°C, making them suitable for cryogenic applications. This temperature versatility, along with their other properties, makes samarium cobalt magnets an excellent choice for demanding environments across various industries.
How are Samarium Cobalt Magnets Manufactured?
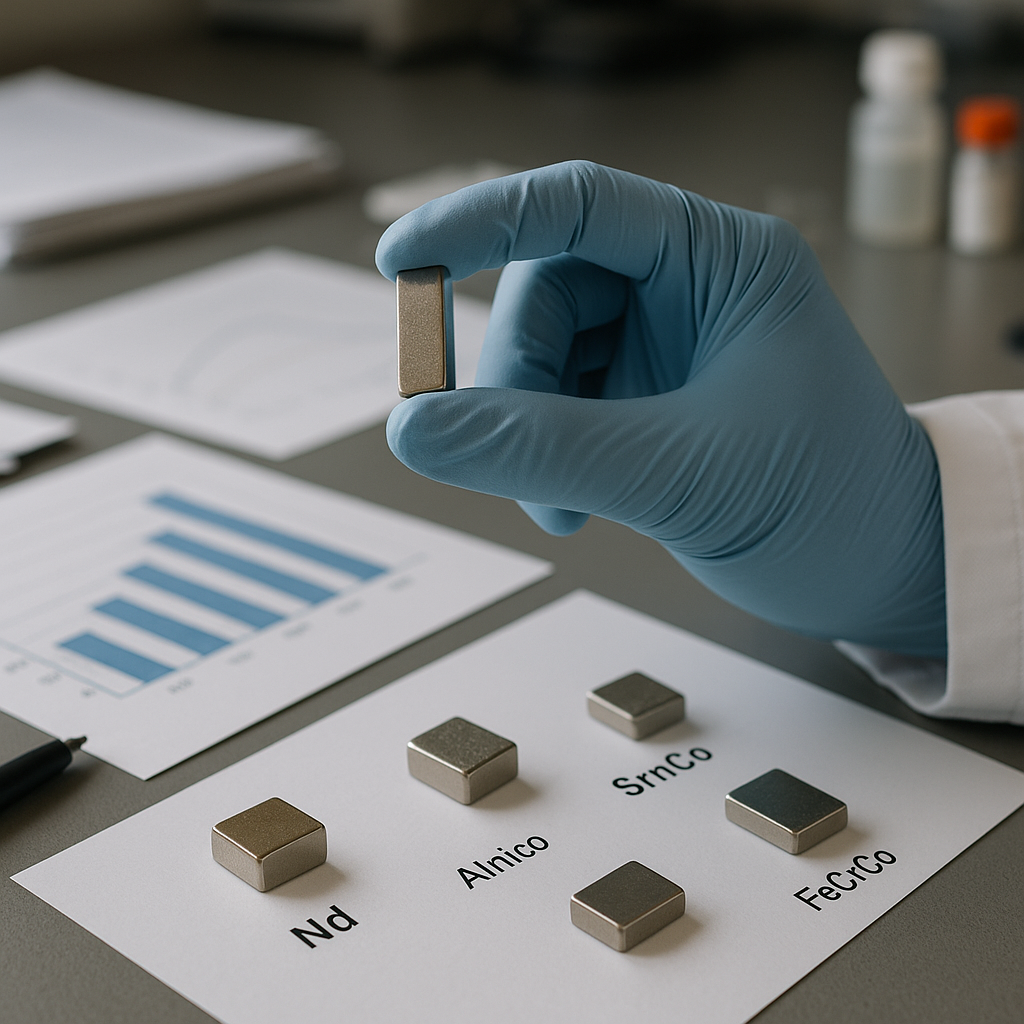
The manufacturing of samarium cobalt magnets involves a precise, multi-step process that combines metallurgical expertise with careful quality control. It begins with raw materials and transforms them into powerful permanent magnets through specialized techniques.
Raw Material Preparation
The process starts with the careful selection of raw materials. Samarium, a rare earth element, and cobalt are the primary components. Some grades also include small amounts of iron, copper, hafnium, zirconium, or praseodymium to enhance specific properties.
These raw materials undergo rigorous purification to remove impurities that could compromise magnetic properties. The purity of these materials directly impacts the performance of the final product.
Melting and Alloying
The purified raw materials are heated in an induction or arc furnace filled with argon gas. This inert atmosphere prevents oxidation during the melting process. The materials melt and combine to form the alloy with the desired composition.
Once melted, the liquid alloy is poured into molds and cooled with water to form solid ingots. This cooling step is carefully controlled to achieve the proper crystalline structure in the metal.
Pulverization and Milling
After cooling, the ingots are broken down, ground, and milled into a fine powder. This pulverization reduces the particle size to microscopic dimensions, typically 3-10 micrometers. The particle size is crucial for subsequent steps and affects the magnetic properties.
The milling process is usually performed in an inert atmosphere or liquid medium to prevent oxidation of the reactive powder particles.
Powder Pressing Under Magnetic Field
The fine powder is then pressed into the desired shape using dies while under a strong external magnetic field. This process, known as magnetic alignment, orients the particles to create anisotropic magnets with directional magnetic properties.
The applied pressure forms the powder into a solid compact suitable for handling. At this stage, the compact is referred to as a “green body” and remains relatively fragile.
Sintering Process
The green compacts are sintered at high temperatures, typically between 1100°C and 1250°C. During sintering, the powder particles fuse, creating a dense, solid magnet in a vacuum or inert gas atmosphere to prevent oxidation.
Sintering is critical for developing the magnet’s microstructure. The material becomes denser as particles bond together, reducing porosity and strengthening the magnet.
Heat Treatment
After sintering, the magnets undergo specific heat treatments to optimize their magnetic properties. This usually involves a solution treatment at high temperatures, followed by tempering between 700°C and 900°C.
The heat-treated magnets are then slowly cooled in the presence of an external magnetic field. This cooling helps establish the magnetic domain structure that gives samarium cobalt magnets their exceptional properties.
Machining and Finishing
Unlike bonded magnets, sintered samarium cobalt magnets require precision machining to achieve final dimensions. Due to the material’s hardness and brittleness, water-cooled diamond-coated grinding tools are used.
The machining process must be carefully controlled as the material is brittle and the dust generated highly flammable. Safety measures are crucial during this stage.
Surface Treatment and Magnetization
The finished magnets often receive protective coatings like nickel, gold, or epoxy to prevent corrosion. These coatings are selected based on the intended application environment.
Finally, the magnets are fully magnetized using powerful electromagnetic fields that can exceed several tesla in strength. This step permanently aligns the magnetic domains, creating the finished samarium cobalt magnet.
Throughout the manufacturing process, precise control of impurities and grain size is maintained. Even small variations can significantly affect magnetic properties, including coercivity, remanence, and temperature stability.
Quality Control and Testing
Each batch of magnets undergoes rigorous testing to ensure they meet specifications. Tests measure magnetic properties, dimensional accuracy, and surface quality. Only magnets that pass all quality checks are approved for distribution.
The extensive manufacturing process explains why samarium cobalt magnets are more expensive than other magnetic materials, but their exceptional performance in high-temperature applications justifies the investment for many specialized uses.
What are the Common Applications of Samarium Cobalt Magnets?
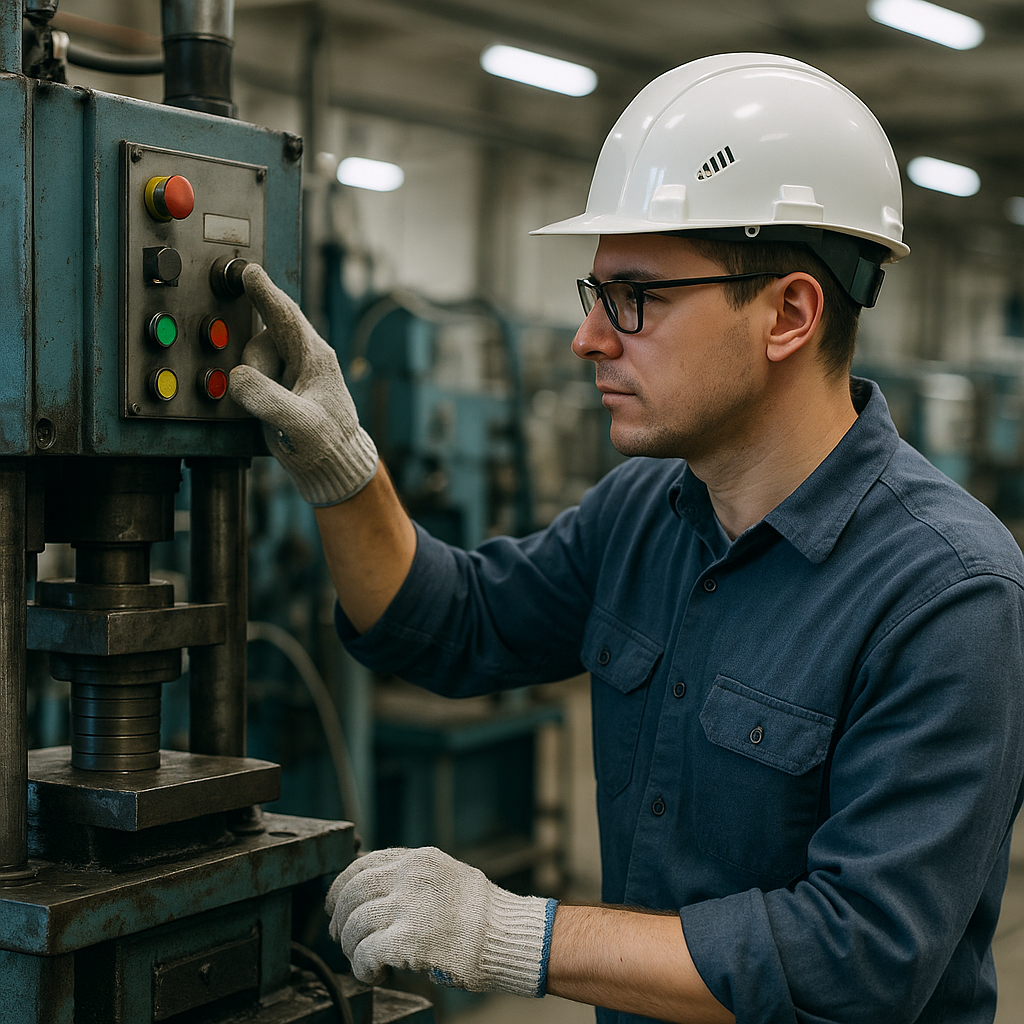
Samarium cobalt (SmCo) magnets excel in demanding environments where conventional magnets fail. Their remarkable thermal stability, corrosion resistance, and strong magnetic properties make them indispensable across multiple industries where reliability under extreme conditions is crucial.
Aerospace and Defense Applications
The aerospace industry relies on SmCo magnets for mission-critical components. Aircraft manufacturers integrate these magnets into control systems for aircraft and satellites, where they must perform consistently despite dramatic temperature fluctuations.
Military applications include precision guidance systems in supersonic jet engine inlets, where temperatures can reach extremes that would demagnetize other magnetic materials. SmCo magnets operate reliably in such environments, ensuring the accuracy of navigation and targeting systems.
Satellites and space equipment benefit from the radiation tolerance and stability of SmCo magnets in the vacuum of space. These magnets power attitude control systems and positioning mechanisms that must function flawlessly for years without maintenance.
Medical Equipment and Devices
In healthcare settings, SmCo magnets play vital roles in diagnostic and treatment technologies. Magnetic Resonance Imaging (MRI) machines use these magnets because they maintain their properties even when exposed to intense magnetic fields from primary superconducting magnets.
Implantable medical devices such as pacemakers use SmCo magnets for their small size and reliability. Their exceptional corrosion resistance makes them suitable for long-term implantation in the human body, where they operate effectively for many years.
Surgical instruments and equipment requiring sterilization at high temperatures also incorporate SmCo magnets, as they retain their magnetic properties through repeated autoclave cycles that degrade other magnetic materials.
Industrial and Energy Applications
The energy sector employs SmCo magnets in turbomachinery, generators, and high-efficiency electric motors. Wind turbine generators benefit from these magnets’ reliability in variable weather conditions and their ability to produce consistent power output.
Oil and gas exploration utilizes SmCo magnets in downhole drilling equipment, where temperatures can exceed 300°C. Their stability in these harsh environments enables precise measurements and tool operations at extreme depths.
High-performance industrial motors benefit from SmCo magnets’ strong magnetic fields and heat resistance. These motors operate efficiently and reliably in manufacturing environments where temperatures fluctuate significantly.
Sensors and Precision Instruments
Sensors across various industries incorporate SmCo magnets for consistent performance. Automotive manufacturers use them in anti-lock braking sensors and engine monitoring systems that must operate reliably from winter cold to summer heat.
Scientific instruments such as electron microscopes and spectrometers rely on SmCo magnets for precise electron beam control. Their stability ensures accurate measurements and consistent performance throughout extended research operations.
Flow meters and other fluid monitoring devices in chemical processing plants use SmCo magnets for their resistance to corrosive environments. These instruments maintain accuracy even when exposed to harsh chemicals that would damage other magnetic materials.
Electronics and Communications
Traveling wave tubes for satellite communications systems use SmCo magnets to focus electron beams. Their reliable performance ensures consistent signal strength in communications equipment that must operate continuously for years.
High-end audio equipment, including premium headphones and speakers, incorporates SmCo magnets for their powerful magnetic fields. These magnets help produce clearer sound with less distortion, even in compact audio devices.
Computer hard drives designed for extreme environments, such as those in industrial settings or military applications, often use SmCo magnets rather than the more common neodymium magnets found in consumer electronics.
Conclusion: The Future of Samarium Cobalt Magnets
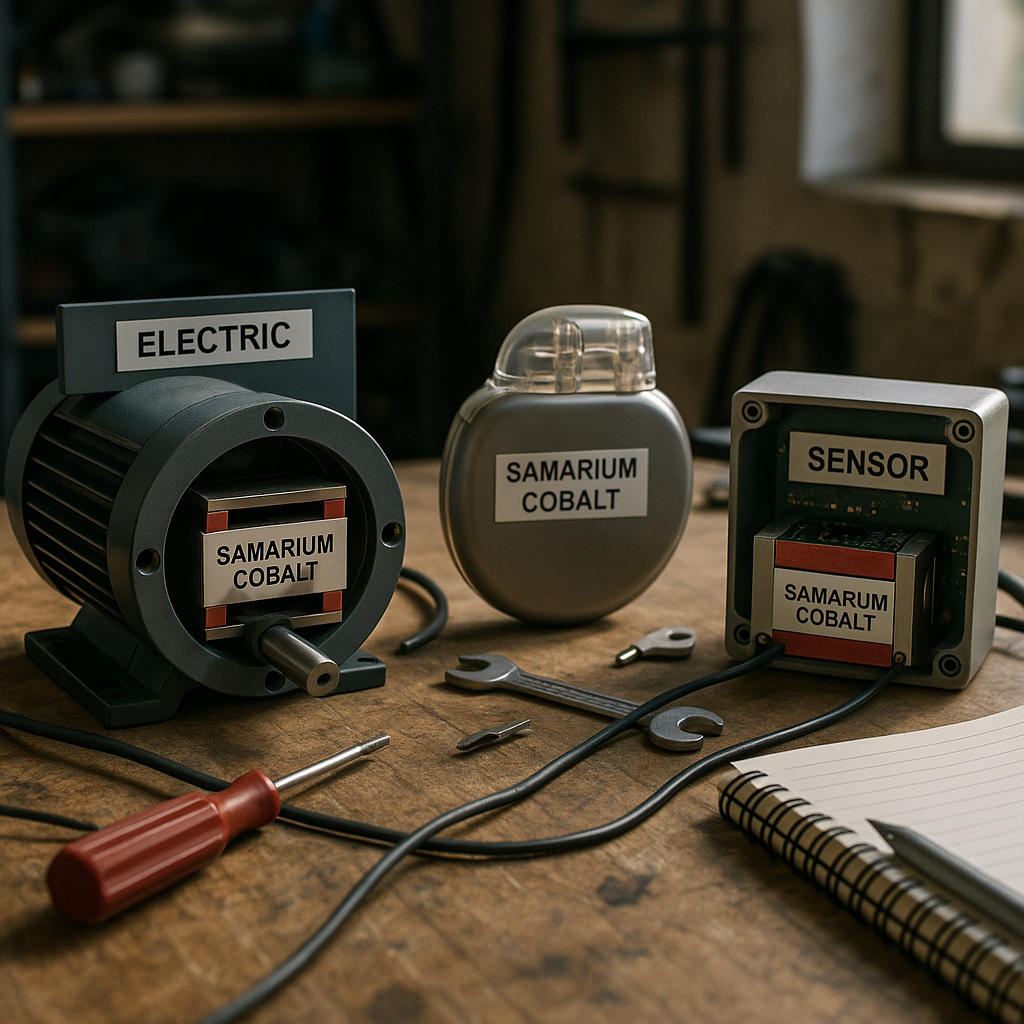
Samarium cobalt magnets remain crucial in advanced technological applications due to their exceptional magnetic strength and temperature stability. Their ability to perform reliably in environments with temperatures reaching up to 350°C gives them a significant advantage over other magnetic materials. Although neodymium magnets dominate some market segments, SmCo magnets are indispensable in aerospace, medical equipment, and industrial systems where consistent performance under harsh conditions is essential.
Looking to the future, samarium cobalt magnets have promising applications across several emerging fields. Advanced robotics, quantum computing, and space exploration technologies are likely to increase demand for these high-performance magnets. Additionally, their role in clean energy technologies, such as high-efficiency wind turbines and electric vehicle components, is expanding as these sectors grow. With ongoing research focused on enhancing their properties and developing more sustainable manufacturing processes, SmCo magnets will remain critical components in the technological landscape for years to come. For companies handling these valuable materials at the end of their life, contact Okon Recycling at 214-717-4083 for responsible recycling solutions to recover these rare earth elements.