5901 Botham Jean Blvd, Dallas, TX 75215
Neodymium Iron Boron (NdFeB) Magnets: A Quick Beginner’s Overview
June 30, 2025Neodymium Iron Boron magnets, commonly known as NdFeB or simply neodymium magnets, represent the pinnacle of permanent magnet technology. These materials are an alloy of neodymium (a rare earth element), iron, and boron, forming a precise Nd2Fe14B tetragonal crystalline structure.
What distinguishes these magnets is their remarkable strength. They produce magnetic fields significantly stronger than any other commercially available permanent magnets. This exceptional force is due to their unique composition and structure, offering superior magnetic properties, including high coercivity (resistance to demagnetization) and impressive remanence (ability to retain magnetization).
The development of NdFeB magnets in the 1980s revolutionized many industries by enabling smaller, lighter, and more efficient magnetic components. These rare earth magnets are essential in numerous modern applications where space constraints and powerful magnetic performance are crucial.
What is the Composition and Structure of NdFeB Magnets?
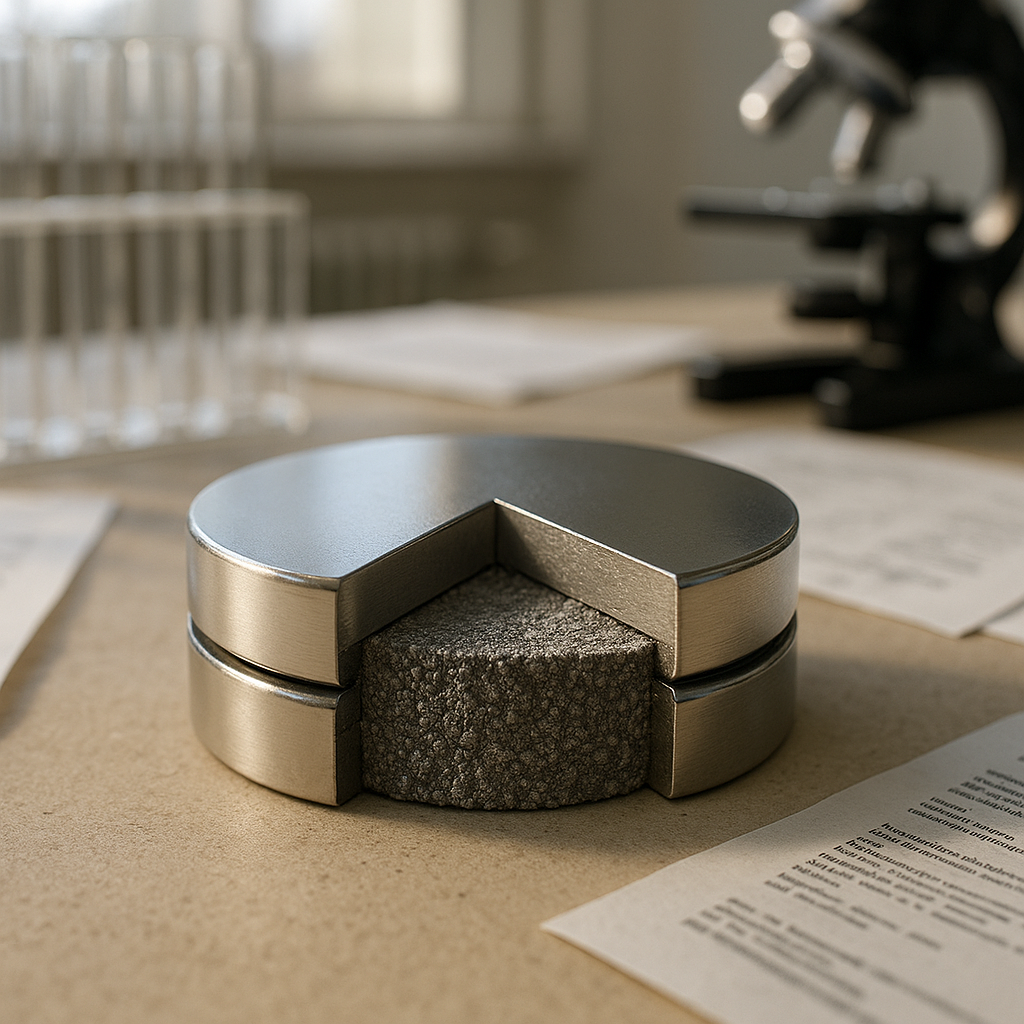
NdFeB magnets consist of a specific alloy of neodymium, iron, and boron, forming the intermetallic compound Nd₂Fe₁₄B. Typically, the composition includes 29-32.5% neodymium, 64-69% iron, and 1.1-1.2% boron. This precise ratio creates the tetragonal crystalline structure responsible for these magnets’ remarkable strength.
The atomic configuration features alternating layers of iron atoms and neodymium-boron compounds. Although boron is a minor component, it plays a crucial role. As diamagnetic atoms, boron does not directly contribute to the magnetic field but enhances cohesion through strong covalent bonding, effectively acting as the glue holding the structure together.
Manufacturers often add small amounts of other elements to enhance specific properties. Dysprosium (0.6-8%) is used to improve temperature stability, ensuring the magnets retain their magnetic properties at higher temperatures. Elements like niobium (0.3-0.5%), aluminum (0.3-0.5%), and copper (0.05-0.15%) may also be included to refine performance characteristics.
Within this structure, neodymium atoms exhibit a large magnetic dipole moment due to their four unpaired electrons, compared to iron’s average of three. In magnets, these unpaired electrons align with their spin in the same direction, generating the magnetic field. This alignment results in a high saturation magnetization of approximately 1.6 tesla and a remanent magnetization typically of 1.3 tesla.
The tetragonal Nd₂Fe₁₄B crystal structure also has exceptionally high uniaxial magnetocrystalline anisotropy. Once magnetized along a specific crystal axis, the material strongly resists demagnetization or changes in magnetic orientation. This property, combined with the alignment of microscopic grains during manufacturing, gives NdFeB magnets their extraordinary coercivity and strength.
The relatively low rare earth content by volume (about 12%) and the greater abundance of neodymium and iron compared to other rare earth elements make NdFeB magnets more economical than other high-performance options like samarium-cobalt magnets, despite their superior magnetic properties.
How are NdFeB Magnets Manufactured?
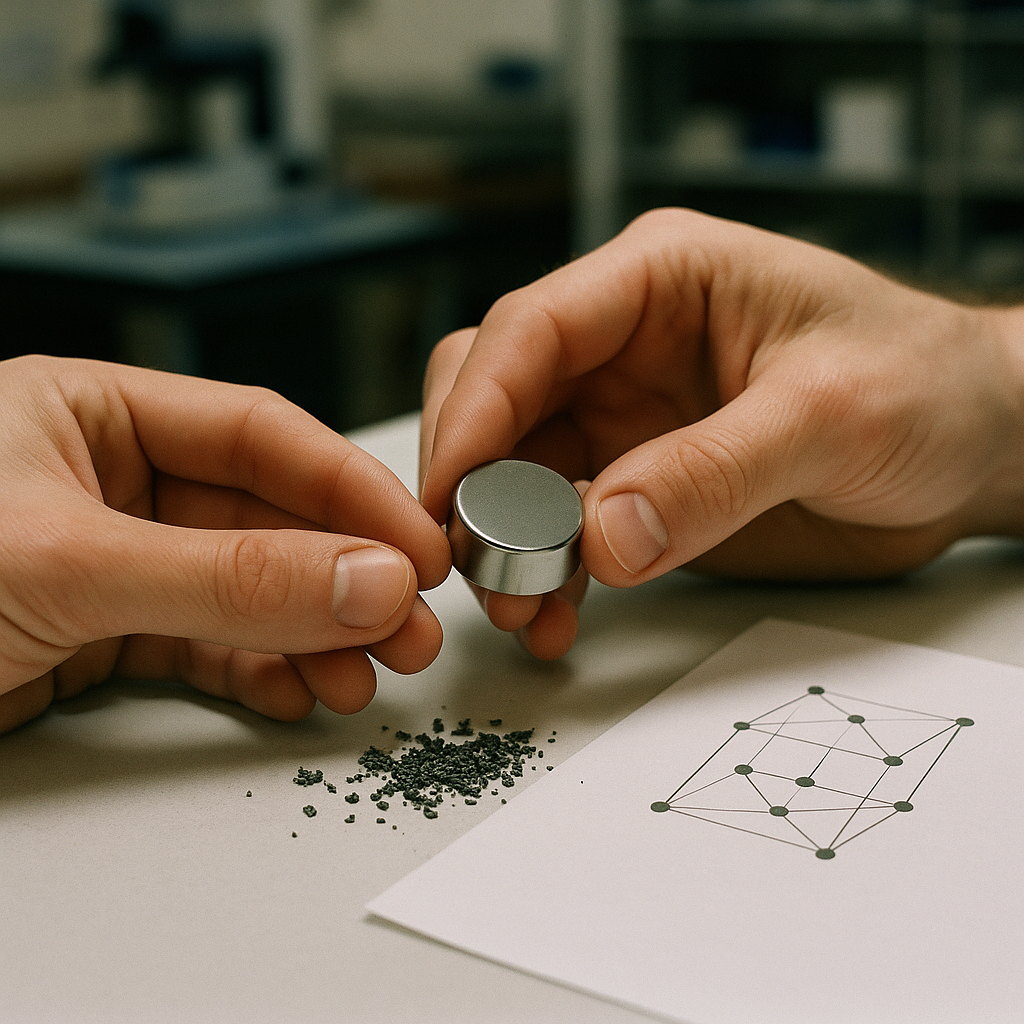
The manufacturing of NdFeB (Neodymium Iron Boron) magnets involves two main methods: sintered and bonded. Each process produces magnets with unique properties, suitable for various industrial applications.
Sintered NdFeB Manufacturing Process
Sintered magnets are created through a powder metallurgy process that results in high-density magnets with strong magnetic capabilities. The process includes several key steps:
- Preparing raw materials: combining neodymium, iron, and boron in precise proportions
- Melting and casting into ingots under controlled conditions
- Pulverizing the alloy into fine powder particles
- Compacting the powder under high pressure in a magnetic field to align particles
- Sintering at about 1100°C to fuse particles into dense blocks
- Cooling and heat treatment to optimize magnetic properties
- Grinding and cutting into final shapes
- Surface treatment or coating to prevent corrosion
This method yields magnets with exceptional strength but limited shape complexity. They are especially valuable in applications requiring high performance, such as electric motors, wind turbines, and MRI machines.
Bonded NdFeB Manufacturing Process
Bonded magnets are produced by combining magnetic powder with binders, which allows for more complex shapes and designs:
- Creating NdFeB alloy through rapid solidification using melt spinning
- Cooling the molten alloy on a spinning wheel to form thin ribbons
- Crushing the ribbons into fine magnetic powder
- Mixing the powder with a polymer binder, like epoxy, nylon, or PPS
- Molding through injection, compression, extrusion, or calendaring techniques
- Curing to solidify the binder and secure magnetic particles
- Final magnetization in the desired direction
This approach produces versatile magnets with moderate magnetic properties, excelling in applications requiring complex shapes, such as sensors, small motors, and office equipment components.
Key Differences in Manufacturing Impact
The manufacturing method significantly impacts the final magnet properties. Sintering produces denser magnets with greater magnetic strength but fewer shape options. The bonded process trades some strength for design and shape flexibility.
The choice of method depends on the intended application. High-performance applications generally use sintered magnets, while those requiring intricate designs or flexibility prefer bonded magnets.
Recent advancements in manufacturing technologies have narrowed the performance gap. Improvements in powder processing and binding materials enhance the capabilities of both types of NdFeB magnets.
What are the Key Applications of NdFeB Magnets?
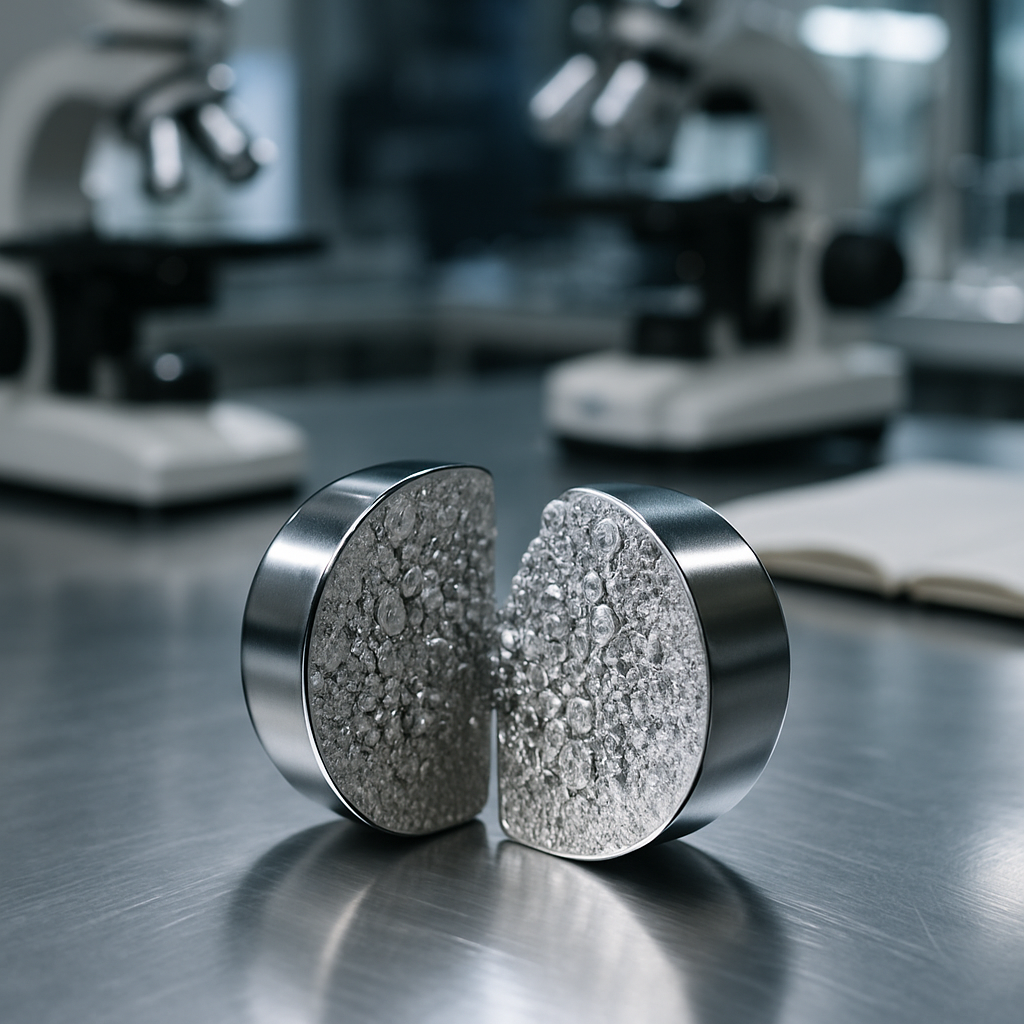
NdFeB magnets have transformed multiple industries with their exceptional magnetic strength-to-size ratio. These powerful rare earth magnets offer remarkable performance in compact dimensions, making them invaluable across various sectors. Their versatility has led to widespread adoption in both everyday consumer products and sophisticated industrial equipment.
Consumer Electronics
In the electronics sector, NdFeB magnets are essential components in many devices we use daily. Computer hard drives rely on these magnets to control read/write heads precisely, enabling increasingly smaller storage devices without sacrificing performance.
Audio equipment benefits tremendously from NdFeB technology. Headphones and loudspeakers use these magnets to convert electrical signals into sound waves with exceptional clarity. The strong magnetic field generated by even small NdFeB magnets allows for compact, lightweight audio devices that deliver superior sound quality.
Transportation and Renewable Energy
The automotive industry has embraced NdFeB magnets as crucial to electric vehicle technology. Electric motors in hybrid and fully electric vehicles use these magnets for higher efficiency, reduced weight, and compact design. This application is especially important as the global market moves toward sustainable transportation solutions.
In renewable energy, NdFeB magnets have advanced wind power generation. Wind turbine generators equipped with these magnets operate with greater efficiency and reliability, eliminating the need for gearboxes, reducing maintenance requirements, and improving overall energy output.
Medical Equipment
The medical field has seen significant advances through NdFeB magnet applications. Magnetic Resonance Imaging (MRI) machines depend on these magnets to create powerful, stable magnetic fields necessary for producing detailed internal body images. The high magnetic field strength allows for clearer diagnostic results, aiding medical professionals in making more accurate assessments.
Beyond MRI technology, NdFeB magnets appear in various medical devices, including pacemakers and neurostimulators. Their reliability and compact size make them ideal for applications where space constraints exist but performance cannot be compromised.
Industrial Applications
In industrial settings, NdFeB magnets serve crucial roles in sensors, motors, and separation systems. Manufacturing facilities use magnetic separators with NdFeB magnets to remove metal contaminants from production lines. Industrial automation systems rely on these magnets in sensors and actuators that detect changes in motion, position, or speed.
The versatility of NdFeB magnets extends to magnetic bearings that eliminate friction and wear in high-speed applications. These frictionless systems improve energy efficiency and reduce maintenance needs across industries from aerospace to energy production.
Conclusion: The Impact and Future of NdFeB Magnets
Neodymium iron boron (NdFeB) magnets have transformed numerous industries with their exceptional magnetic strength and efficiency. From wind turbines and electric vehicles to medical equipment and consumer electronics, these powerful magnets are foundational in modern technology. Their ability to deliver high performance while remaining compact has enabled technological advancements that would otherwise be unattainable.
Looking ahead, key challenges will shape the future of NdFeB magnet technology. Supply chain vulnerabilities and raw material sustainability are significant concerns. The industry must address the environmental impacts of rare earth mining and processing through enhanced recycling systems and more environmentally friendly production methods. Ongoing innovation will continue to improve magnetic performance, temperature stability, and cost-effectiveness.
For businesses and municipalities managing end-of-life products containing these valuable materials, proper recycling is essential. Contact Okon Recycling at 214-717-4083 for sustainable solutions for your NdFeB magnet and rare earth material recycling needs.