5901 Botham Jean Blvd, Dallas, TX 75215
How Are Magnets Made? An Introduction to Magnet Manufacturing
May 20, 2025From the speakers in your smartphone to the motors in electric vehicles, magnets are essential components in countless technologies we rely on daily. These powerful objects, which attract or repel, don’t simply exist in nature in their final form. They’re the result of precise engineering and manufacturing processes developed over decades of scientific advancement.
At its core, magnet manufacturing transforms ordinary materials into objects with extraordinary properties. The process begins with selecting specific raw materials that can be magnetized. These include ferromagnetic metals like iron, nickel, and cobalt, which have unique atomic structures allowing them to maintain magnetic alignment.
Different types of magnets require different manufacturing approaches. Permanent magnets maintain their magnetic field indefinitely without an external source. In contrast, soft magnets can be magnetized temporarily but lose their magnetism when the external field is removed. Rare-earth magnets, including neodymium and samarium cobalt varieties, represent the strongest permanent magnets available today, though they require more complex production methods.
What Materials Are Used to Make Magnets?
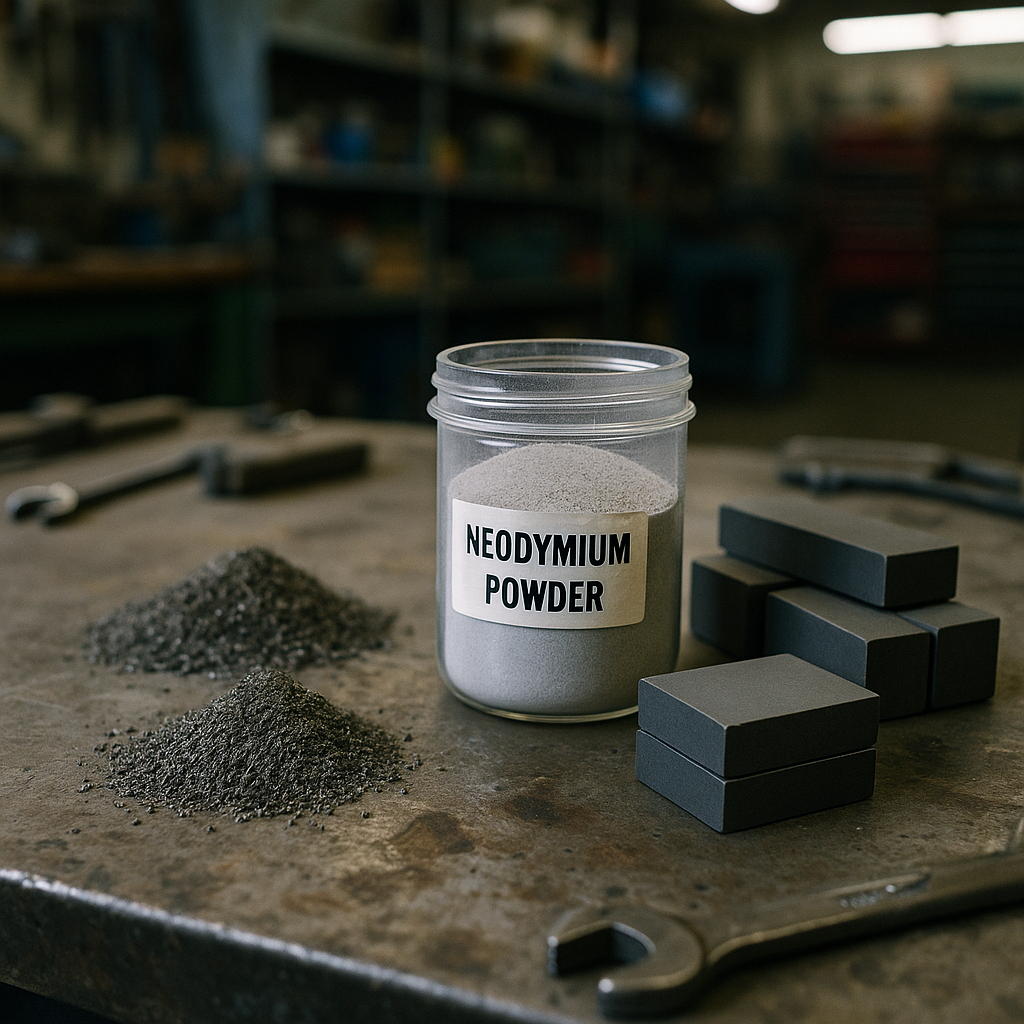
The raw materials for magnets vary significantly based on the type and intended use. Ferromagnetic materials, such as iron, cobalt, and nickel, are foundational as they are naturally attracted to magnetic fields and can be magnetized.
Permanent magnets are categorized into five main families, each with distinct compositions. Ceramic or ferrite magnets, the most economical option, consist of iron oxide combined with barium or strontium carbonate, making them brittle yet resistant to corrosion and suitable for many commercial uses.
Alnico magnets, composed of aluminum, nickel, and cobalt, have been in use since the 1930s. They are particularly valued for maintaining magnetic properties at high temperatures, making them ideal for specialized industrial applications.
For applications requiring extremely powerful magnetic fields, rare earth magnets are preferred. The two main types are samarium cobalt (SmCo) and neodymium iron boron (NdFeB). Samarium cobalt magnets, developed in the early 1970s, perform well at elevated temperatures while maintaining strong magnetic properties.
Neodymium magnets are the strongest commercially available, composed of neodymium, iron, and boron. They can create magnetic fields significantly stronger than other types, projecting about three times the magnetic flux of a ceramic magnet of the same size.
Flexible magnets, created by binding ferrite or rare-earth magnetic powders in carriers like vinyl, sacrifice some strength for flexibility, making them suitable for applications needing bendable magnetic materials.
The choice of material impacts a magnet’s performance characteristics, such as maximum operating temperature. Alnico magnets can function over 540°C (1,000°F), while ferrite and samarium cobalt magnets operate effectively up to about 300°C (570°F). Neodymium magnets have a lower temperature tolerance, around 140°C (280°F).
Manufacturing processes also influence magnetic strength. Hard ferromagnetic materials undergo special processing in strong magnetic fields during manufacture to align their internal structure, making them difficult to demagnetize and effective as permanent magnets.
Material Type | Composition | Br (Gauss) | Hc (Oersted) | BHmax (MGOe) | Density (g/cm3) | Max Operating Temp (°C) | Temperature Coefficient |
---|---|---|---|---|---|---|---|
Neodymium | Neodymium, iron, boron | 13,000 | 11,500 | 42 | 7.4 | 80 | 0.11% |
Alnico | Aluminum, nickel, cobalt, iron | 12,500 | 640 | 5.5 | 7.3 | 500 | -0.02% |
Ferrite | Iron oxide, ceramic materials | 3,850 | 2,950 | 3.5 | 5 | 180 | -0.2% |
Samarium Cobalt | Samarium, cobalt | 11,000 | 9,700 | 28 | 8.4 | 350 | 0.11% |
Magnetic Rubber | Barium/Strontium powder, PVC or synthetic rubber | 2,000 | 1,600 | 0.8 | 3.5 | 50 | 0.2% |
Material selection depends on the specific requirements, including magnetic strength, operating temperature, corrosion resistance, and cost. For instance, while neodymium magnets offer superior strength, their higher cost and lower temperature resistance may make ferrite magnets more suitable for certain applications.
What Are the Key Steps in Magnet Manufacturing?
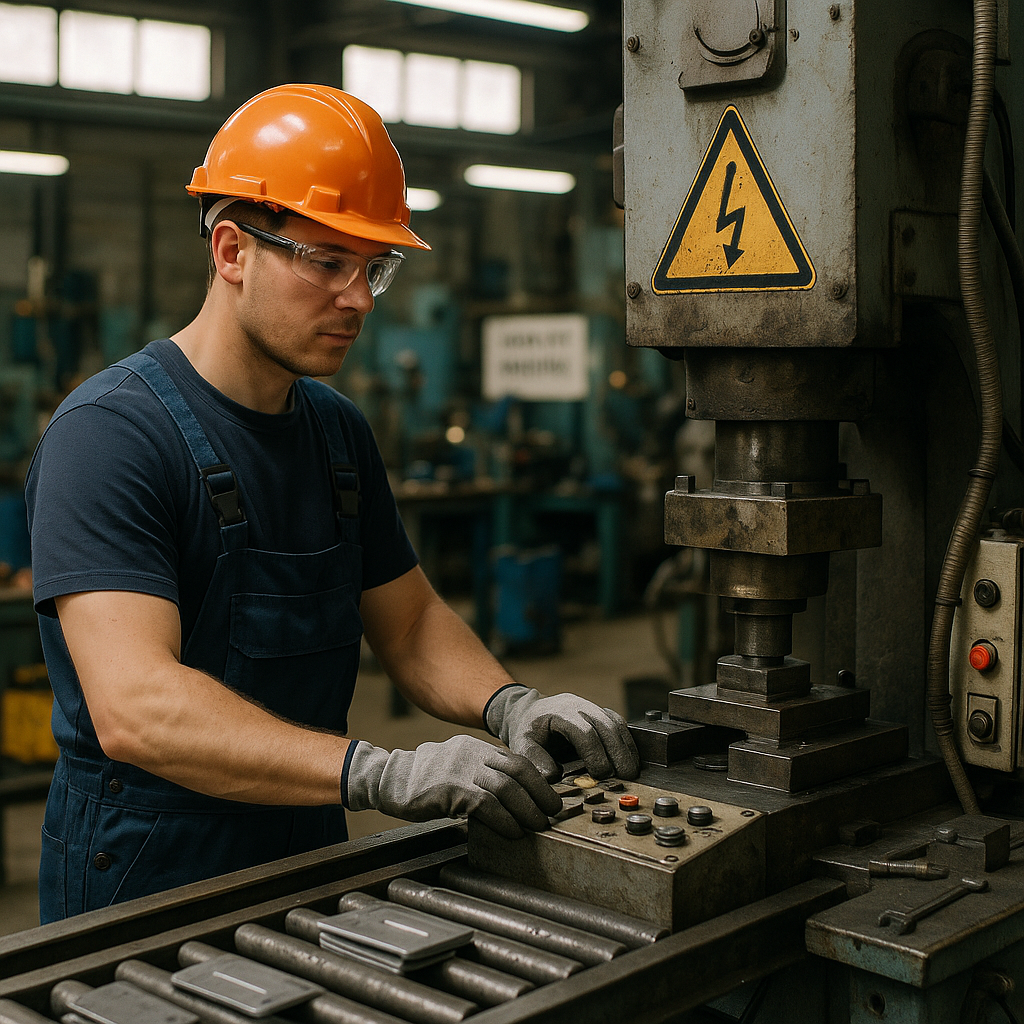
Magnet manufacturing is a precise, multi-stage process that transforms raw materials into powerful magnetic components. Each phase in production directly impacts the final magnet’s strength, durability, and performance characteristics. Explore the critical steps that bring these essential devices to life.
Material Selection
The foundation of any magnet begins with choosing the right materials. Manufacturers select specific elements based on the intended application and desired magnetic properties. For rare earth magnets like neodymium, crucial materials include neodymium, iron, and boron. Samarium cobalt magnets require samarium and cobalt, while ferrite magnets use iron oxide with barium or strontium.
The exact composition significantly affects magnetic strength, temperature tolerance, and resistance to demagnetization. For instance, adding dysprosium to neodymium magnets increases their resistance to demagnetization at high temperatures, making them suitable for automotive applications operating in hot environments.
Smelting and Alloy Formation
Once materials are selected, they undergo smelting in vacuum induction furnaces at temperatures exceeding 1600°C. This process melts the raw elements and combines them into alloys with specific compositions. For neodymium magnets, manufacturers often use strip casting, where molten alloy pours through a nozzle onto a water-cooled drum, forming thin metal sheets that cool rapidly.
This rapid cooling is crucial for controlling the microstructure and preventing unwanted crystal formations. The cooling rate directly influences the magnetic properties, with rates of 500-1000°C per second being common for high-performance magnets.
Powder Metallurgy
The solidified alloy is then processed through powder metallurgy techniques. For neodymium magnets, hydrogen decrepitation is often used to embrittle the material. The alloy absorbs hydrogen, creating microscopic cracks that make it easier to pulverize.
The material is then ground into extremely fine powder using jet mills or ball mills. The particle size is critical, typically around 5 micrometers for neodymium magnets. This fine powder consists of single-crystal particles that will retain their magnetic orientation once aligned.
Alignment and Pressing
The powder is placed in a mold and exposed to a strong magnetic field to align the particles in a uniform direction. While still under this magnetic field, the powder is compressed using either die pressing or isostatic pressing techniques. This alignment is fundamental to creating anisotropic magnets with directional magnetic properties.
The applied pressure must be sufficient to hold the particles together but not so high that it disrupts their careful alignment. The degree of alignment directly influences the magnet’s remanence and maximum energy product.
Sintering or Bonding
Most high-performance magnets undergo sintering, where the pressed powder is heated in vacuum or inert gas atmospheres to temperatures below the melting point. For neodymium magnets, sintering occurs at approximately 1050-1080°C, causing the particles to fuse together into a dense solid without completely melting.
Alternatively, bonded magnets are made by mixing magnetic powder with polymers and then curing the mixture. While bonded magnets offer less magnetic strength than sintered ones, they provide greater design flexibility and are easier to manufacture into complex shapes.
Magnetization
After cooling, the material has the proper microstructure but isn’t yet fully magnetized. The magnet receives its final magnetic properties through exposure to an intense magnetic field generated by specialized magnetizing equipment. These machines create field strengths 2-3 times stronger than the magnet’s coercivity.
For high-coercivity magnets, peak magnetization fields may reach 30,000-40,000 Oersteds. The magnetizing process aligns the magnetic domains permanently in the desired direction, activating the magnet’s full potential.
Surface Treatment and Coating
To protect against corrosion and physical damage, magnets typically undergo surface treatment. Neodymium magnets are particularly vulnerable to corrosion and usually receive protective coatings such as nickel, zinc, epoxy, or gold. These coatings extend the magnet’s useful life while preserving its magnetic properties.
The coating thickness must be carefully controlled. Too thin, and it won’t provide adequate protection. Too thick, and it creates an unwanted air gap that reduces the magnet’s effective strength in applications.
Quality Control and Testing
Throughout and after manufacturing, magnets undergo rigorous testing to verify their magnetic properties. Key measurements include flux density, coercivity, and energy product. Manufacturers also perform physical inspections to check dimensions, surface quality, and coating integrity.
Quality control ensures that each batch of magnets meets application-specific requirements. Testing may include salt spray exposure for corrosion resistance or thermal cycling to verify performance across temperature ranges.
Each step in the manufacturing process builds upon the previous one, with careful control of parameters throughout. The result is a finished magnet with precisely tailored properties for applications ranging from tiny medical devices to massive wind turbine generators.
[[artifact_table]] Key manufacturing parameters and their effects on magnet properties [[/artifact_table]]How Are Different Types of Magnets Manufactured?
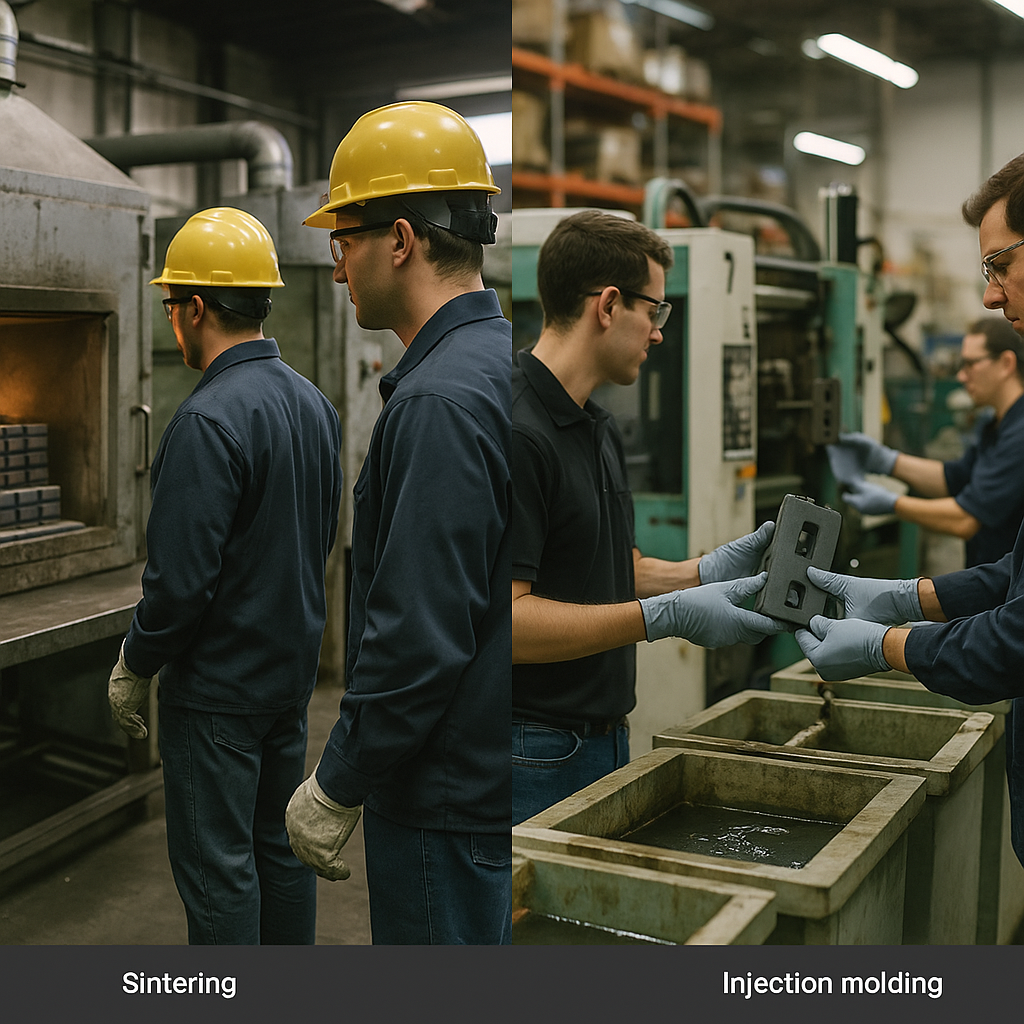
Manufacturing magnets involves specialized techniques tailored to each type’s unique properties and applications. Three primary categories—permanent, flexible, and electromagnets—require distinct production methods to achieve their characteristic properties.
Permanent Magnet Manufacturing
Permanent magnets like ferrite and rare-earth varieties are produced through powder metallurgy. This begins with preparing raw materials, typically metal alloys containing iron, cobalt, nickel, and other elements depending on the specific magnet type.
For rare-earth magnets such as neodymium-iron-boron (NdFeB) and samarium-cobalt (SmCo), the process starts with vacuum induction melting of raw materials to create the base alloy. The resulting material is crushed and milled to create a fine powder with particles approximately 3-5 microns in diameter.
This powder is aligned in a magnetic field during compaction to ensure optimal magnetic orientation. The aligned powder is sintered at temperatures between 1150-1300°C, causing the particles to fuse together while maintaining their alignment. The sintering process creates a dense, solid magnet that shrinks 15-25% from its original pressed size.
Ferrite magnets follow a similar process but use ceramic materials containing iron oxide combined with barium or strontium carbonate. After calcination at temperatures around 1250-1300°C, the material is wet-milled to achieve particle sizes of 0.7-0.9 microns.
Flexible Magnet Production
Flexible magnets represent a significant departure from traditional rigid magnetic materials. These magnets are manufactured by combining magnetic powders—typically ferrite—with polymeric binders like vinyl, rubber, or other plastics.
The production begins by mixing ferrite powder with the polymer material in precise ratios. This mixture is then processed through either calendering or extrusion. In calendering, the mixture is passed between rollers to form thin sheets, while extrusion forces the material through shaped openings under pressure to create various profiles.
The resulting composite material maintains magnetic properties while gaining flexibility. The polymer content determines the degree of flexibility—higher polymer ratios create more flexible magnets but with reduced magnetic strength. After forming, the material is magnetized in a strong magnetic field to align the magnetic domains.
Electromagnet Construction
Electromagnets follow a different manufacturing approach. Unlike permanent and flexible magnets, electromagnets generate magnetic fields only when an electric current flows through them.
The basic construction involves winding conductive wire (usually copper) around a core material. The core is typically made from soft magnetic materials like iron, silicon steel, or various ferromagnetic alloys that easily magnetize and demagnetize.
The wire is wound in multiple turns around the core, creating a solenoid. When electricity passes through this wire coil, it generates a magnetic field proportional to both the current strength and the number of wire turns. Once the current stops, the magnetic field disappears in most electromagnet designs.
Manufacturing variations include different core materials, wire gauges, insulation types, and winding patterns. These factors determine the electromagnet’s strength, efficiency, heat dissipation, and response characteristics.
Specialized Manufacturing Methods
Advanced magnet manufacturing techniques have emerged to enhance performance characteristics. For high-performance rare-earth magnets, methods like hot pressing, die-upset processing, and grain boundary diffusion can significantly improve magnetic properties.
Alnico magnets use casting techniques where the molten alloy is poured into molds and then subjected to a controlled cooling process in a magnetic field. This directional cooling creates the elongated microstructure responsible for alnico’s magnetic properties.
For specialized applications requiring precise magnetic field patterns, multipole magnetization techniques allow manufacturers to create complex field configurations within a single magnet piece.
Each manufacturing method produces magnets with distinct advantages for specific applications. Powder metallurgy creates strong permanent magnets ideal for motors and generators. Flexible magnet production yields versatile materials for refrigerator magnets and signage. Electromagnet winding allows for controllable, switchable magnetic fields essential for solenoids, relays, and MRI machines.
The continued development of magnet manufacturing techniques remains crucial for advancing technologies in renewable energy, transportation, electronics, and medical fields.
Magnet Type | Manufacturing Method | Key Characteristics |
---|---|---|
Nd-Fe-B | Sintering | High magnetic strength, complex production |
Sm-Co | Sintering | High temperature stability |
Alnico | Casting | Temperature resistance, brittle |
Ferrite | Ceramic process | Economical, non-corroding |
Flexible | Calendering/Extrusion | Flexible, less magnetic strength |
Conclusion: The Importance of Precision in Magnet Manufacturing
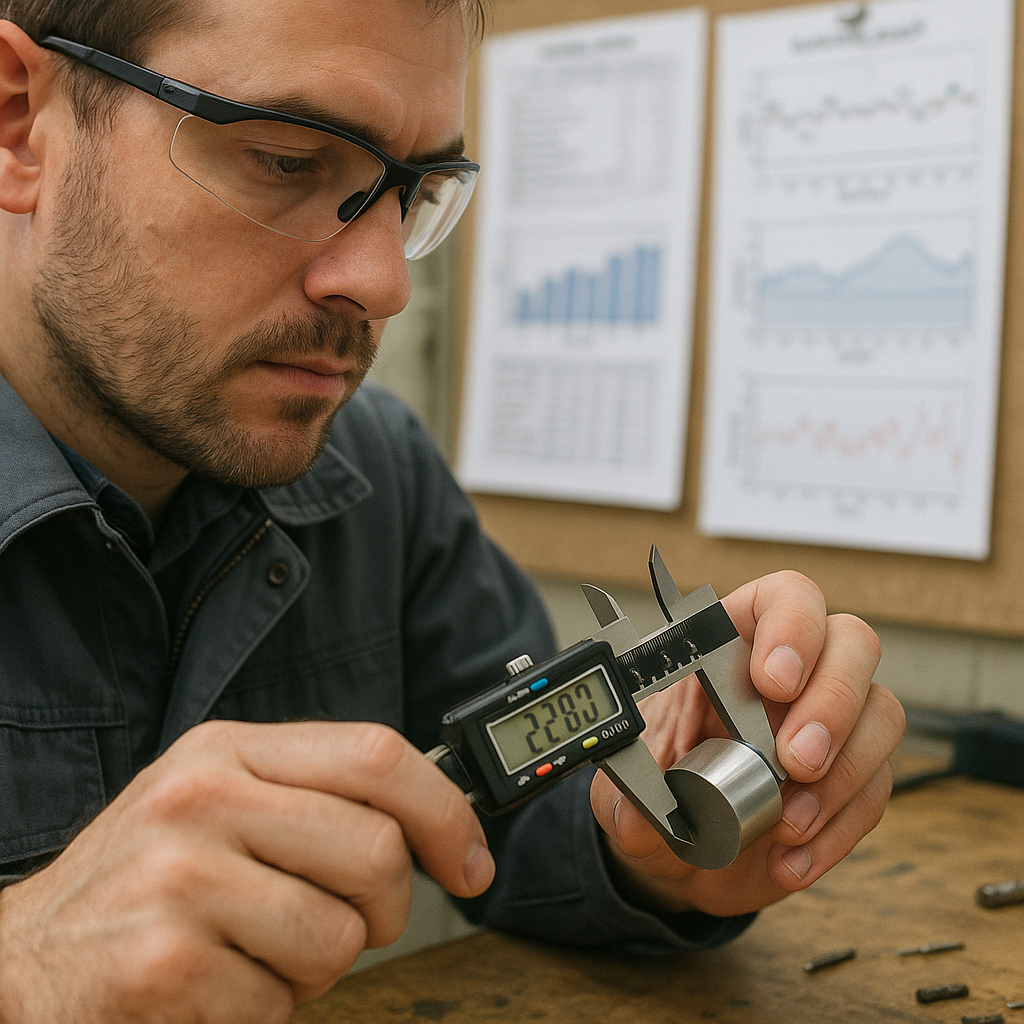
The production of magnets involves a sophisticated process requiring meticulous attention to detail. Material science, engineering expertise, and precision manufacturing techniques must work together seamlessly to create magnetic components with specific properties. From raw material selection to quality control, each step in magnet manufacturing demands precision to ensure optimal performance in various applications.
As technology advances, the demand for high-performance magnets is growing rapidly. These magnetic components are essential in driving innovations in renewable energy, healthcare, automation, and transportation. The precision in their manufacturing directly impacts their effectiveness and the advancement of the technologies they support. For expert guidance on recycling and proper disposal of magnetic materials from industrial applications, contact Okon Recycling at 214-717-4083.