5901 Botham Jean Blvd, Dallas, TX 75215
Manufacturing Scrap Solutions: How to Reduce Waste and Boost Efficiency
July 11, 2025Manufacturing scrap presents a significant challenge for industrial operations. These unusable materials, generated during production processes, can include metal shavings, rejected parts, excess raw materials, and defective products that fail quality control. Without proper management, this waste directly affects a company’s bottom line through lost material costs, disposal expenses, and reduced production efficiency.
Solutions for managing manufacturing scrap have evolved considerably in recent years. Modern scrap management systems now offer comprehensive approaches to efficiently handle, track, and ultimately reduce waste materials. These integrated solutions combine technology, process improvements, and sustainable practices to transform what was once considered pure waste into potential resources.
For manufacturers facing tightening profit margins and increasing environmental regulations, implementing effective scrap management solutions is essential. These systems not only cut operational costs but also improve production efficiency and minimize environmental impact. As manufacturing increasingly adopts lean principles and sustainability goals, the ability to control and reduce scrap has become a competitive advantage in today’s industrial landscape.
How Can Real-Time Monitoring Reduce Manufacturing Scrap?
Real-time monitoring systems provide manufacturers with immediate visibility into scrap generation throughout the production process. These systems capture data directly from machines and production lines as operations occur. This instant feedback eliminates the delays associated with traditional end-of-shift or daily reporting methods.
Manufacturing facilities equipped with real-time monitoring technology can track scrap rates at each production stage. Sensors on equipment detect deviations in temperatures, pressures, and cycle times that often lead to defects. The system instantly alerts operators when parameters drift outside acceptable ranges, preventing continued production of defective parts.
The financial impact of scrap becomes immediately visible through real-time cost tracking. Rather than discovering excessive waste costs at month-end, managers can see the financial impact as it happens, creating urgency around addressing problems that might otherwise persist.
Immediate Intervention and Root Cause Analysis
The greatest benefit of real-time monitoring is enabling immediate intervention. When a machine begins producing defective parts, operators receive instant alerts. Supervisors can quickly investigate and implement corrective actions before significant waste accumulates, transforming a potential major scrap event into a minor issue.
Real-time systems also facilitate faster root cause analysis. The data collected shows exactly when problems began and the conditions at that moment, eliminating guesswork in troubleshooting. Manufacturers can identify whether issues stem from material variations, equipment settings, or operator actions.
Continuous monitoring allows for pattern recognition, detecting subtle trends before they result in defects. For example, gradually increasing temperatures might signal an impending equipment failure that could generate scrap. Maintenance teams can address these issues during planned downtime rather than after failures occur.
Cost Savings Through Data-Driven Decisions
Manufacturers implementing real-time scrap monitoring typically achieve 15-20% reductions in waste costs, stemming from reducing scrap volume and addressing issues faster. A plastic injection molding plant using real-time monitoring reduced material waste by 23% in the first six months after implementation.
Labor costs associated with rework decrease significantly as well. Real-time monitoring helps prevent defects rather than catching them during quality inspection, reducing resources needed for sorting, reworking, or scrapping products.
Energy efficiency improves as well. When machines produce scrap, they waste energy on unsellable parts. By reducing scrap rates, manufacturers improve energy utilization per good part produced. A metal stamping operation saved over $40,000 annually in energy costs after implementing real-time scrap monitoring.
Decision-making improves with accurate, current data. Production supervisors can focus on the most problematic areas, engineers can evaluate process improvements immediately, and executives gain clearer visibility into production costs and improvement opportunities.
Continuous improvement initiatives are more effective with real-time data. Teams can implement changes and immediately see the impact on scrap rates, accelerating the improvement cycle and building momentum for waste reduction efforts.
Benefit | Description |
---|---|
Reduced Downtime | Immediate alerts on equipment performance deviations prevent prolonged production of defective parts, minimizing downtime. |
Improved Quality Control | Real-time data enables swift reactions to maintain process parameters, enhancing product quality and reducing batch failures. |
Cost Reduction | Optimizing processes and reducing waste through RTM significantly lowers manufacturing costs. |
Faster Response Times | Continuous monitoring allows for prompt action to deviations, reducing waste and improving efficiency. |
Advanced Process Control (APC) | Utilizes RTM to detect and correct faults in process parameters swiftly, ensuring consistent quality. |
Integration with other systems enhances the value of real-time monitoring. When connected to maintenance management systems, scrap data can trigger preventive maintenance activities. Integration with quality systems creates a more comprehensive view of production performance, while supply chain systems can adjust material orders based on actual consumption, including scrap.
What Role Does Automation Play in Scrap Management?
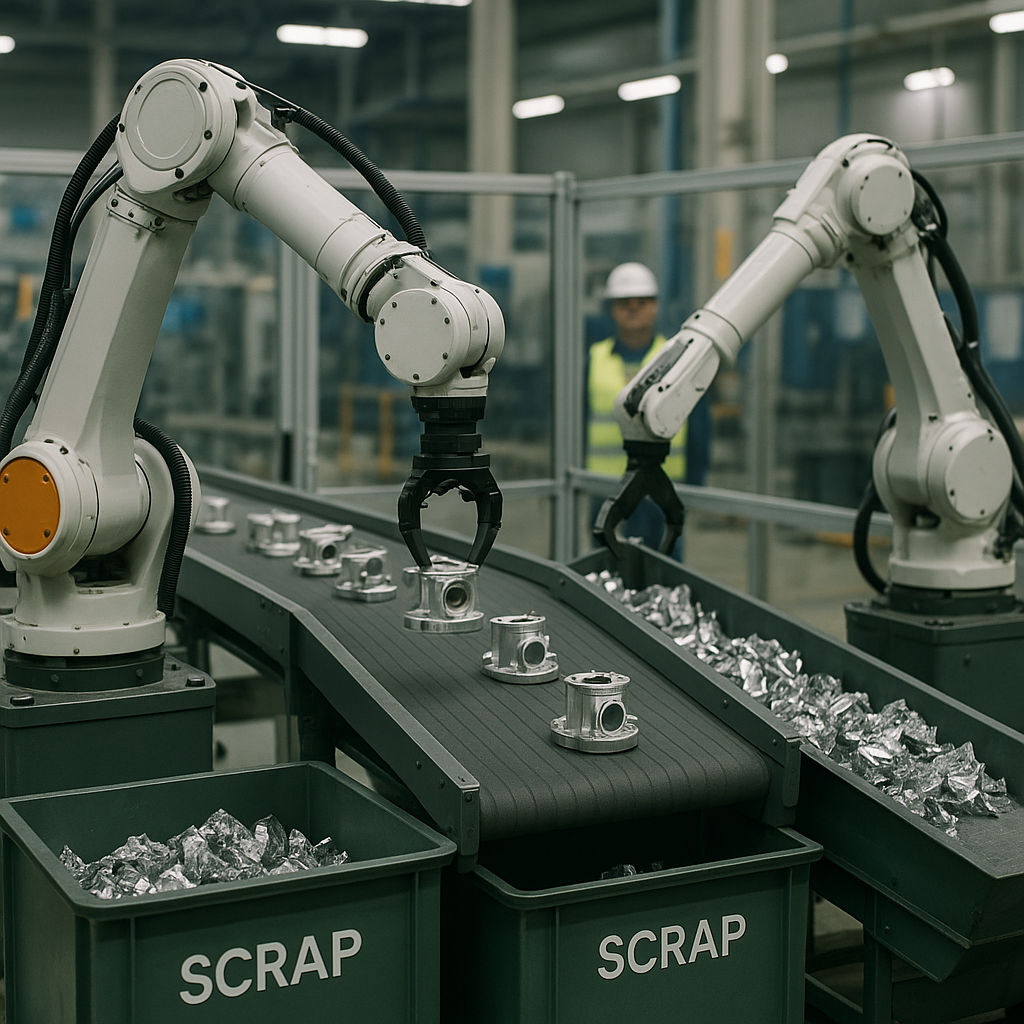
Automation has transformed modern scrap management by turning traditional manual processes into streamlined, efficient operations. Advanced automated systems now handle tasks that once required extensive labor and were prone to human error. Implementing these technologies allows manufacturers to process materials more quickly while maintaining higher accuracy rates.
Automated scrap management systems excel at collecting and monitoring real-time data. Sensors and IoT devices continuously gather information on material types, weights, and processing status. This constant flow of data enables manufacturing facilities to make informed decisions about resource allocation and identify opportunities for waste reduction.
A significant advantage of automation in scrap management is error reduction. Manual sorting and classification of scrap materials often lead to inconsistencies and mistakes. Automated systems using computer vision and AI can identify and categorize materials with remarkable precision, ensuring proper handling and processing of different scrap types.
- Automated planning processes that optimize collection schedules and routes
- Real-time tracking systems that monitor scrap throughout the facility
- Non-conforming material identification and separation
- Integration with production line applications for a seamless workflow
- Predictive analytics to forecast scrap generation and processing needs
Safety improvements are another crucial benefit of automation in scrap management. Handling scrap materials, particularly metals, can be significantly risky for workers. Automated systems reduce these risks by using robotics for sorting, handling, and processing potentially dangerous materials. This reduction in manual handling not only improves workplace safety but also allows businesses to reallocate human resources to higher-value tasks.
Cost efficiency is a compelling reason for implementing automated scrap management solutions. While the initial investment may be substantial, the long-term savings are significant. Automated systems reduce labor costs, minimize material waste through precise sorting, and improve the recovery of valuable materials. Additionally, by streamlining the entire scrap management process, companies can process larger volumes of material in less time, increasing overall operational efficiency.
Integrating automated scrap management with other production systems creates a more cohesive manufacturing environment. Modern automated solutions can communicate directly with manufacturing execution systems (MES), enterprise resource planning (ERP) platforms, and other production tools. This interconnectivity ensures that scrap management becomes an integral part of the manufacturing process rather than an isolated function.
Aspect | Manual Processes | Automated Processes |
---|---|---|
Speed and Consistency | Slower and subject to human inconsistencies | Faster and more consistent |
Error Prone | High potential for human errors | Reduced errors due to automated precision |
Labor Costs | Higher due to manual labor involvement | Lower due to reduced manpower |
Data Collection | Limited and often delayed | Real-time and continuous |
Safety | Higher risk for workers | Enhanced safety as personnel are removed from hazardous tasks |
Initial Investment | Lower upfront cost | Higher upfront cost |
Long-Term Savings | Fewer savings due to inefficiencies | Significant savings over time |
Environmental compliance and reporting have become increasingly important in manufacturing operations. Automated scrap management systems maintain detailed records of all processed materials, generating accurate reports for regulatory compliance with minimal effort. This capability helps manufacturers demonstrate their commitment to environmental responsibility while reducing the administrative burden associated with compliance documentation.
How Do Comprehensive Scrap Management Solutions Improve Overall Manufacturing Efficiency?
Comprehensive scrap management solutions that integrate seamlessly with Manufacturing Execution Systems (MES), Warehouse Management Systems (WMS), and Quality Management Systems (QMS) form a powerful ecosystem, enhancing manufacturing efficiency. These integrated approaches eliminate isolated data silos and provide real-time visibility across the entire production process.
When scrap management functions as part of a connected system rather than a standalone solution, manufacturers benefit from continuous data flows, enabling proactive decision-making. This integration offers a holistic approach to waste reduction, impacting multiple aspects of manufacturing operations.
Real-Time Production Monitoring and Control
Integrated scrap management solutions with MES platforms continuously monitor production processes, identifying potential failures or deviations before they generate waste. This proactive approach significantly reduces material loss and improves overall equipment effectiveness.
Real-time data capture allows production managers to track key performance indicators related to scrap generation. If patterns indicate increased waste in specific processes, teams can make immediate adjustments rather than discovering problems during end-of-shift reporting.
A connected system provides comprehensive visibility into each production stage, allowing manufacturers to target specific improvement areas. For example, if data reveals consistent material waste during a particular machining operation, engineers can analyze the process parameters and make precise adjustments.
Enhanced Inventory Management
The integration between scrap management solutions and WMS significantly improves material utilization. The system maintains accurate records of available materials, including recycled materials from previous production runs that can be reintroduced into manufacturing processes.
This integration reduces unnecessary material purchases by providing precise visibility into existing inventory. Manufacturers can better forecast material needs based on actual consumption rates rather than estimates that overlook reusable scrap.
Connected systems also optimize the storage of recyclable materials by category, quality, and intended reuse application, ensuring valuable materials don’t become waste due to improper cataloging or accessibility issues.
Quality Control Integration Benefits
Integrating scrap management with QMS gives manufacturers powerful tools for reducing defect-related waste. The system ensures products meet quality standards during production through automated inspection points and real-time validation.
This integration creates a feedback loop where quality issues are immediately identified, allowing for process adjustments before additional defective units are produced. The system can automatically halt production when quality parameters drift beyond acceptable ranges.
Digital records of quality incidents linked to specific production batches help engineers identify the root causes of recurring quality problems. This data-driven approach leads to targeted process improvements that reduce scrap generation permanently.
Traceability and Compliance Advantages
Comprehensive scrap management solutions provide end-to-end traceability that documents material flow throughout the manufacturing process, crucial for regulated industries where material accountability is mandatory.
The system maintains detailed records of all material movements, including when and where scrap was generated, how it was processed, and whether it was recycled or disposed of. This audit trail simplifies compliance reporting and verification.
Compliance with environmental regulations becomes more manageable with integrated systems that automatically generate the required documentation, reducing administrative burdens while ensuring accurate reporting on waste management practices.
Feature | Integrated Solutions | Standalone Solutions |
---|---|---|
Data Integration | Seamless integration with ERP and compliance systems, such as QuickBooks and NetSuite | Limited to no integration with external systems |
Process Efficiency | Real-time monitoring and automation streamline workflows | Manual processes increase the risk of errors and inefficiencies |
Visibility | Access data from anywhere in real-time | Limited visibility due to potential data silos |
Error Reduction | Automated systems reduce human error | High risk of errors with manual entry |
Maintenance and Predictive Insights | Integrated systems provide predictive maintenance alerts | Less proactive maintenance insights |
Environmental Compliance | Automatically generates compliance reports | Manual reporting with potential for human error |
Reduced Downtime Through Predictive Insights
Integrating scrap management with other manufacturing systems provides valuable data correlations that help predict potential equipment failures. The system identifies patterns where increased scrap generation precedes specific maintenance issues.
This predictive capability allows maintenance teams to schedule repairs proactively before equipment failures cause extended downtime and material waste. By addressing problems during planned maintenance windows, manufacturers avoid the substantial scrap generation that often accompanies catastrophic equipment failures.
The system also reduces setup-related waste by optimizing changeover procedures based on historical performance data. When operators follow standardized processes guided by the integrated system, material waste during transitions between production runs decreases significantly.
Cost Reduction Beyond Material Savings
While direct material savings are the most obvious benefit of integrated scrap management, the financial advantages extend much further. The system reduces labor costs associated with manual scrap handling, sorting, and reporting.
Energy consumption decreases when manufacturers eliminate the need to reprocess materials due to quality issues or production errors, translating to significant cost savings in energy-intensive manufacturing operations.
The comprehensive data available through integrated systems also supports more accurate financial forecasting. Manufacturers can precisely calculate the true cost of scrap, including hidden expenses related to storage, handling, and disposal.
By continuously monitoring scrap-related metrics across all connected systems, manufacturers gain insights that drive ongoing efficiency improvements. These data-driven optimizations create a cycle of continuous improvement, steadily reducing waste while enhancing overall manufacturing efficiency.
Conclusion: Implementing Effective Manufacturing Scrap Solutions
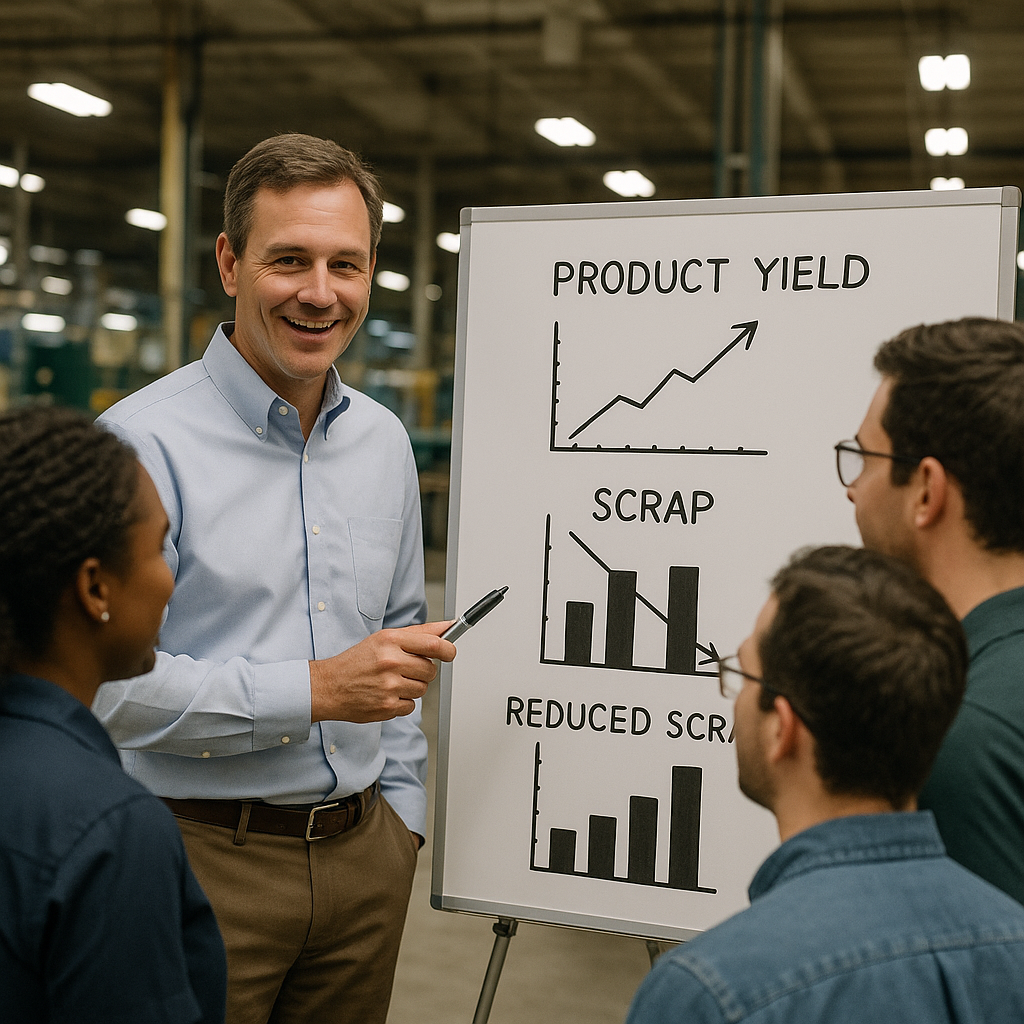
Implementing effective scrap management solutions is crucial for modern manufacturers. In a competitive environment, businesses that successfully minimize waste gain significant advantages in cost reduction, operational efficiency, and environmental sustainability. Research shows that companies implementing targeted scrap reduction initiatives can cut expenses by up to 40% while simultaneously improving product quality and production throughput.
The most successful manufacturers approach scrap reduction strategically, using real-time monitoring systems to identify waste sources instantly. By collecting accurate machine-level data, businesses can pinpoint inefficiencies, perform root cause analysis, and develop targeted solutions. Automation further enhances these efforts by standardizing processes and eliminating variables that lead to defects. When integrated with streamlined workflows and lean manufacturing principles, these technologies create a comprehensive system that continually improves quality and reduces material loss.
Don’t let manufacturing scrap erode your profit margins. Contact Okon Recycling at 214-717-4083 for expert recycling solutions tailored to your manufacturing operations.