5901 Botham Jean Blvd, Dallas, TX 75215
Scrap Metal Drop-off Rules: What to Know Before You Go
May 1, 2025In the United States, over 130 million tons of scrap metal are recycled annually, preventing 29 million tons of carbon dioxide from entering the atmosphere.
These impressive numbers highlight the importance of proper scrap metal recycling beyond just clearing out your garage or worksite. By following established drop-off protocols, you contribute to this significant environmental impact.
Scrap metal recycling is not as simple as tossing unwanted metal items in a bin. It is a structured process that requires proper sorting, preparation, and handling. Ferrous metals like steel need different treatment than valuable non-ferrous metals such as copper and aluminum. Adhering to these guidelines ensures materials move efficiently through the recycling stream while maximizing both environmental benefits and potential financial returns.
Understanding drop-off regulations protects more than just the environment. Improperly handled scrap metals can pose serious safety risks to workers and potentially release harmful substances into soil and water.
What Are the General Guidelines for Scrap Metal Drop-off?
The primary guideline for scrap metal recycling is the 50 percent rule. An item must contain at least 50 percent metal to qualify as recyclable scrap metal, even if combined with materials like plastic or rubber.
Materials meeting this threshold are worth recycling despite mixed composition. For instance, a car radiator with plastic parts can be recycled if its metal content exceeds half of its makeup.
Material Sorting Requirements
Proper sorting is essential before dropping off scrap metal. Separate ferrous metals (iron and steel) from non-ferrous metals (aluminum, copper, brass) to help recycling facilities process materials efficiently.
Remove any obvious non-metal attachments when possible. Detach plastic handles from metal pots or rubber grips from metal tools. This step increases the value of your scrap and improves recycling outcomes.
Many facilities require different metals to be placed in designated containers. Follow on-site signage carefully to ensure materials go to the correct processing streams.
Preparation Guidelines
Clean scrap metal before drop-off. Remove dirt, grease, or other contaminants that could interfere with recycling processes. A quick rinse is often sufficient for most household items.
Drain all fluids from appliances or automotive components. Items like refrigerators must have coolant professionally removed before recycling. Vehicles require proper drainage of oil, coolant, and gasoline.
Break down larger items when practical. Disassembling complex objects into their components makes processing easier and often results in higher payouts at scrap yards.
Documentation Requirements
Many states require identification when dropping off certain types of scrap metal. Bring a valid ID, such as a driver’s license, when visiting recycling facilities.
Some items, particularly those with high theft potential like copper wiring or catalytic converters, may trigger additional verification requirements. Be prepared to complete paperwork documenting the source of these materials.
Facilities must follow strict regulations under the Resource Conservation and Recovery Act (RCRA), which governs proper disposal of potentially hazardous materials often found in metal items.
Scrap Metal Type | Preparation Requirement |
---|---|
#1 Bare Bright Copper Wire | Bare, uncoated, unalloyed copper wire free of attachments. All insulation must be removed. |
#1 Copper Tubing | Bare, uncoated, unalloyed copper bus bar/pipe free of attachments. |
#1 Flashing Copper | Bare, uncoated, unalloyed copper free of tar, corrosion, and paint. |
#1 Heavy Melting Steel | Prepared pieces smaller than 60”x 24” over ¼“ thick. |
#2 Copper Tubing | Burnt copper, copper with light tin coating, solder, or brass fittings still attached. |
What Are the Legal Requirements for Scrap Metal Drop-off?
Legal requirements for scrap metal drop-off vary significantly across states and localities throughout the United States. This patchwork of regulations creates a complex legal landscape that recycling facilities and those dropping off materials must navigate carefully.
Most jurisdictions implement these regulations to combat metal theft, which rose notably following the 2008 recession when metal prices increased. States like California, Texas, and New York have particularly stringent requirements compared to less populated areas.
Common Legal Requirements
While specific regulations differ by location, several common legal requirements exist across many jurisdictions:
- Licensing and Permits: Scrap yards must obtain proper business licenses and specialized permits to operate legally. These often require annual renewals and compliance inspections.
- Transaction Documentation: Detailed records of all purchases must be maintained, including a description of materials, weight, date, time, and payment amount.
- Seller Verification: Most states require scrap facilities to verify and document seller identities using government-issued photo identification. Some states even photograph sellers alongside their materials.
- Stolen Property Prevention: Facilities must implement measures to identify potentially stolen materials and report suspicious transactions to authorities.
- Material Holding Periods: Many jurisdictions enforce mandatory holding periods (typically 3-7 days) before processing certain types of scrap to allow time for stolen items to be identified.
- Restricted Materials: Special handling procedures exist for items like catalytic converters, utility wires, manhole covers, and materials with identifying marks.
Payment restrictions represent another significant regulatory area. Some states prohibit cash payments above certain thresholds, requiring checks or electronic transfers instead. Florida, for instance, restricts cash payments for certain materials to reduce untraceable transactions potentially involving stolen goods.
Reporting Requirements
Reporting obligations pose substantial administrative responsibilities for scrap facilities. Many states now require electronic submission of transaction data to specialized databases that law enforcement can access. This digitization trend continues to expand as states modernize their regulatory frameworks.
In addition to state laws, local ordinances may impose additional requirements. Counties and municipalities sometimes enforce stricter rules than their state governments, particularly in urban areas experiencing high rates of metal theft.
The consequences for non-compliance can be severe. Penalties range from fines and license suspension to criminal charges in cases of willful violations or handling clearly stolen materials. First offenses typically result in warnings or moderate fines, while repeat violations trigger escalating penalties.
Staying current with changing regulations presents an ongoing challenge. State laws undergo frequent revisions as legislators respond to emerging trends in metal theft and recycling practices. What was compliant last year might not meet current standards.
To navigate this complex regulatory environment, individuals and businesses should consult resources like state-by-state guides to scrap metal laws. These compilations provide valuable starting points for understanding applicable regulations.
Beyond general state requirements, certain materials trigger specialized regulations. For example, vehicles and catalytic converters face particularly stringent documentation requirements due to their high theft rates and value.
Environmental compliance adds another layer of legal requirements. Proper handling and disposal of hazardous materials often found in scrap (such as mercury switches, refrigerants, or lead) must follow federal EPA guidelines regardless of state location.
Regular compliance audits help scrap facilities avoid violations. Many operations conduct quarterly internal reviews to identify potential issues before they become regulatory problems during official inspections.
What Safety Precautions Should Be Taken When Dropping Off Scrap Metal?
Safety is crucial when handling scrap metal. The recycling industry processes millions of tons of metal annually, and without the right precautions, workers and customers face significant risks. These essential safety measures protect everyone involved in the recycling process.
Personal Protective Equipment (PPE)
Always wear suitable PPE when handling scrap metal. This includes heavy-duty gloves to prevent cuts, safety goggles to shield your eyes from debris, and steel-toed boots to guard against falling objects.
Thick clothing or disposable coveralls offer additional protection against harmful substances and sharp edges. For certain materials, respiratory protection may be necessary to avoid inhaling toxic dust or fumes.
Inspect your PPE before each use and replace damaged items immediately to maintain proper protection levels during handling.
Safe Handling Techniques
Use proper lifting techniques to prevent musculoskeletal injuries. Bend at your knees rather than your waist when picking up heavy items. For larger or awkward pieces, use mechanical aids like dollies, carts, or forklifts.
Be cautious of sharp edges that can cause serious injuries. Approach jagged metal carefully and use tools instead of your hands whenever possible. Stay aware of your surroundings and communicate clearly with others when moving large materials.
Keep your work area clean and organized to prevent accidents. Remove debris and scrap pieces from walkways and work zones promptly. Poor visibility significantly increases accident risks when handling potentially dangerous materials.
Chemical and Hazardous Material Awareness
Be aware that scrap metal may contain hazardous substances such as lead, mercury, or cadmium. These materials can release toxic fumes during processing or cause health problems through contact.
Follow proper procedures for identifying and handling potentially contaminated materials. This might include segregation, specialized containment, or specific disposal methods as required by regulations.
Maintain good hygiene practices throughout the handling process. Wash your hands thoroughly after touching scrap metal and before eating or drinking to prevent accidental ingestion of harmful substances.
Hazardous Material | Source | Health Risks |
---|---|---|
Lead | Batteries, paint | Neurotoxicity, kidney damage |
Mercury | Thermostats, switches | Neurological damage, respiratory issues |
Cadmium | Plating, batteries | Kidney damage, bone fragility |
Polychlorinated Biphenyls (PCBs) | Capacitors, transformers | Cancer, immune system suppression |
Emergency Preparedness
Know basic first aid procedures for common metal-related injuries like cuts, puncture wounds, and eye injuries. Have well-stocked first aid kits readily available during transport and drop-off.
Establish clear emergency protocols for serious incidents. Everyone involved should know what to do in case of significant injuries, chemical exposure, or other emergencies.
When dropping off at recycling facilities, follow all posted safety guidelines and instructions from staff. These rules exist to protect both workers and customers from common hazards in the recycling environment.
What Are the Best Practices for a Successful Scrap Metal Drop-off?
Proper preparation is key to a successful scrap metal drop-off. The right approach not only streamlines the recycling process but also maximizes the value of your materials. Following best practices ensures your experience will be efficient and productive.
Sort Your Metals Properly
Sorting is essential for maximizing value from your scrap metal. Use a magnet to separate ferrous metals (containing iron) from non-ferrous metals like copper, aluminum, and brass.
Keep high-value non-ferrous metals in separate containers, as these materials typically command higher prices when properly identified and sorted at drop-off.
Use sturdy, clearly labeled bins for each metal type to prevent mixing during transport. Many recycling facilities offer premium prices for well-sorted metals since it reduces their processing costs.
Clean and Prepare Your Materials
Remove all non-metallic components before recycling. Strip plastic, rubber, or wood parts from metal items to increase their value. For example, removing insulation from copper wiring can significantly boost its value.
Clean visible dirt, grease, and debris from metal surfaces. Wiping off contaminants prevents issues during recycling and helps facilities assess quality accurately.
For appliances and larger items, dismantle them first. Remove electronic components and non-metal casings that could contaminate the recycling process.
Research Facility Requirements
Contact your chosen recycling center before visiting. Confirm their current operating hours and verify they accept the types of scrap metal you have.
Ask about specific preparation requirements. Some facilities have guidelines about how they accept certain metals or limitations on size and quantity.
Inquire about documentation needed for drop-off. Many scrap yards require identification and may have special procedures for larger quantities of material.
Transport Safety Measures
Secure your load properly during transport. Use straps or chains to prevent shifting that could cause metals to mix or create road hazards.
Distribute weight evenly in your vehicle or trailer. Proper weight distribution maintains stability and prevents dangerous situations while driving.
Consider covering your load with a tarp. This prevents lighter pieces from blowing away during transit and keeps your materials contained.
Personal Safety Precautions
Always wear appropriate protective equipment. Heavy-duty gloves, safety goggles, and steel-toed boots protect against cuts, debris, and crushing injuries.
Be cautious of sharp edges when handling scrap metal. Approach jagged pieces carefully and use tools rather than bare hands when possible.
Maintain awareness of your surroundings at the recycling facility. Follow all posted safety guidelines and staff instructions while on site.
Documentation and Record-Keeping
Bring proper identification to the recycling facility. Most legitimate operations require ID to process transactions and maintain records.
Keep receipts and documentation of your transactions. These records are valuable for tax purposes and provide proof of legal disposal.
Maintain a log of materials you recycle regularly. Tracking helps you monitor values over time and optimize your recycling efforts.
Metal Type | Preparation Steps |
---|---|
Steel | Separate ferrous metals, remove non-metal attachments |
Aluminum | Ensure non-magnetic separation, clean surface |
Copper | Strip insulation, clean, and remove any non-metal parts |
Brass | Remove non-metal attachments, clean thoroughly |
Lead | Ensure clean surface, remove contaminants |
Ethical Considerations
Ensure you have the legal right to recycle the materials you bring. Never collect scrap from unauthorized locations or someone else’s property.
Follow local regulations regarding scrap metal collection and recycling. Many areas have specific rules designed to prevent theft and illegal dumping.
Choose reputable recycling facilities that follow environmental best practices. Responsible recyclers process materials with minimal environmental impact.
Conclusion: Responsible Scrap Metal Recycling
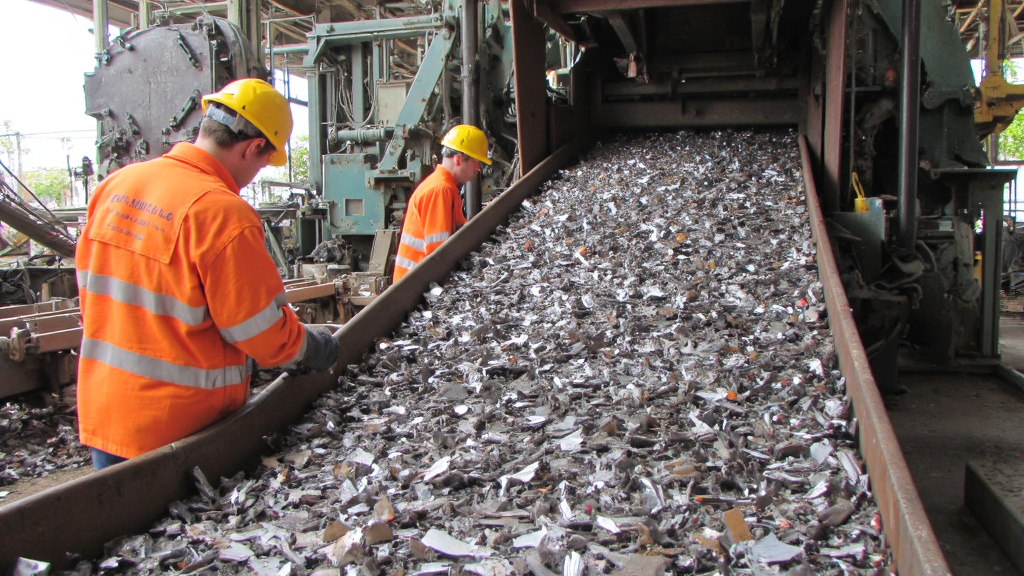
Adhering to scrap metal recycling regulations is crucial for environmental protection and legal compliance. When individuals and businesses follow proper drop-off procedures, they significantly contribute to resource conservation by keeping valuable metals out of landfills. These efforts reduce the need for environmentally harmful mining operations while creating jobs in the recycling industry.
Following local, state, and federal guidelines not only enhances environmental sustainability but can also offer financial benefits. By properly sorting, cleaning, and delivering scrap metal to authorized facilities, participants in the recycling chain help ensure materials maintain their value and utility.
For recycling questions or to responsibly recycle your scrap metal, contact Okon Recycling at 214-717-4083.