5901 Botham Jean Blvd, Dallas, TX 75215
What is the Science of Recycling Scrap Metal?
May 20, 2025Scrap metal recycling involves recovering and processing metal materials from end-of-life products and structures. These materials are transformed into valuable resources for manufacturing new goods. This process is a crucial component of the circular economy.
In the United States alone, the industry processes approximately 56 million tons of scrap iron and steel annually. This significant recycling effort keeps valuable metals out of landfills, where they would otherwise remain for centuries. Metal is unique among recyclable materials because it can be processed repeatedly without degrading its properties.
The process of scrap metal recycling follows a systematic approach. It begins with collecting discarded metal items from businesses, demolition sites, and individuals, followed by precise sorting to separate ferrous (iron-containing) from non-ferrous metals like aluminum and copper. The materials then undergo preparation, melting, purification, and solidification before becoming raw material for new products.
What Are the Key Steps in the Scrap Metal Recycling Process?
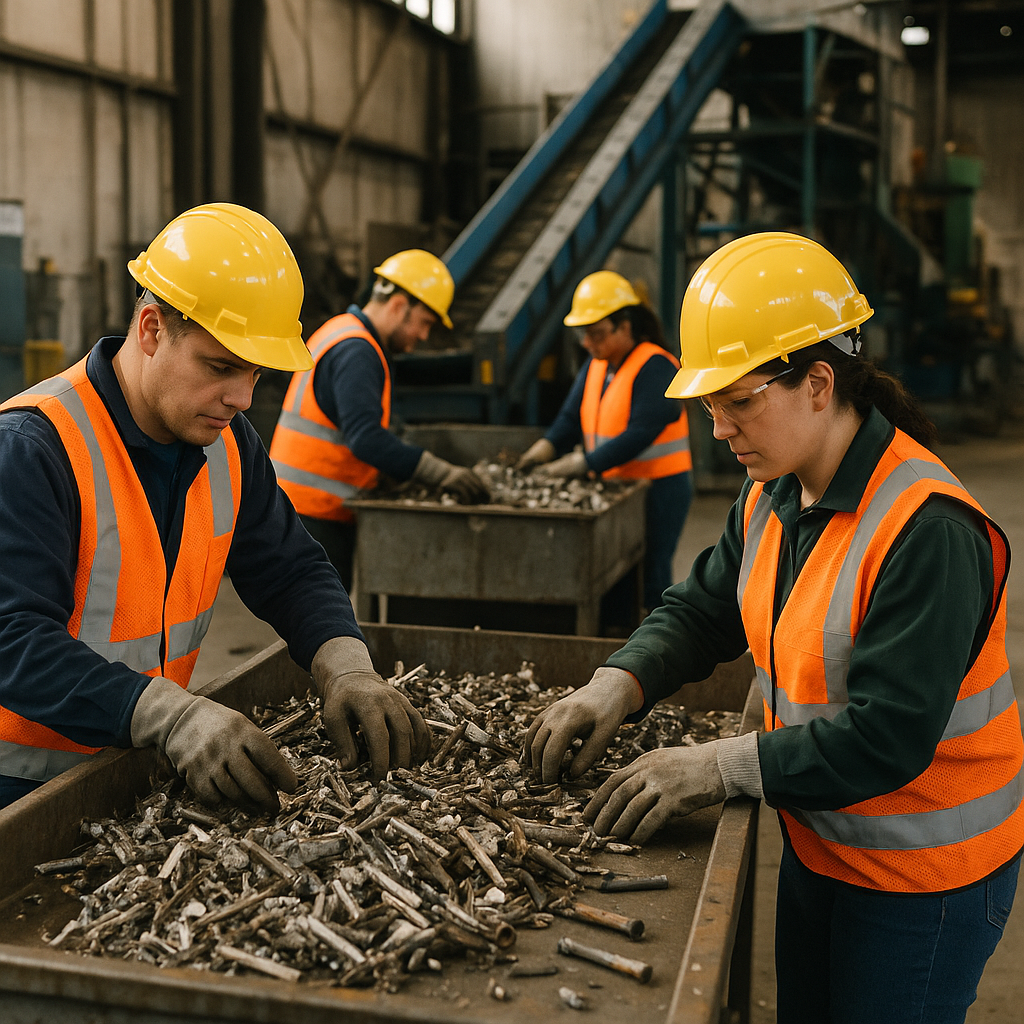
The scrap metal recycling process efficiently transforms discarded metal items into valuable new products. This not only conserves natural resources but also requires significantly less energy than producing metals from raw materials.
Collection
The process begins with collection, where metal-containing items are gathered from various sources such as construction sites, industrial facilities, warehouses, landfills, and homes.
Collection points include dedicated recycling centers, scrap yards, and municipal collection events. Many communities offer curbside pickup programs specifically for metal recycling.
Separation and Preparation
Once collected, scrap metal is thoroughly sorted at recycling facilities, separating metals by type as they require specific recycling methods.
Separation often starts with distinguishing ferrous metals (containing iron) from non-ferrous metals using magnets. Ferrous metals like steel stick to magnets, while non-ferrous metals like copper and aluminum do not.
After sorting, the materials are prepared for processing through shredding, shearing, and compacting, reducing large pieces into manageable sizes for the next stage.
Melting and Purification
The sorted metals move to steel mills or specialized facilities for melting. Large furnaces heat the scrap metal to specific temperatures, transforming it into liquid form.
During this stage, impurities and contaminants are removed, ensuring the recycled metal meets quality standards for new products.
Different metals require different purification techniques. For example, steel recycling often uses electric arc furnaces, while aluminum recycling employs methods to remove coatings and non-metal components.
Solidification
After melting and purification, the molten metal cools and solidifies into usable forms, typically cast into shapes like bars, blocks, or sheets called ingots.
The cooling and solidification process is carefully controlled to maintain the desired properties of the metal, impacting the final product’s strength and durability.
These newly formed metal pieces serve as raw material for manufacturing facilities across various industries.
Manufacturing
In the final step, recycled metal transforms into new products. Manufacturers use the processed metal to create items ranging from car parts and building materials to electronics and household goods.
The manufacturing process may involve additional treatments such as rolling, extruding, or machining to shape the metal into finished products, which then enter the market.
This closed-loop system exemplifies the circular economy, where materials maintain their value through repeated recycling rather than becoming waste.
Metal | Energy Savings from Recycling |
---|---|
Aluminum | 95% |
Copper | 85% |
Steel | 60% |
How Are Different Types of Metals Identified and Sorted?
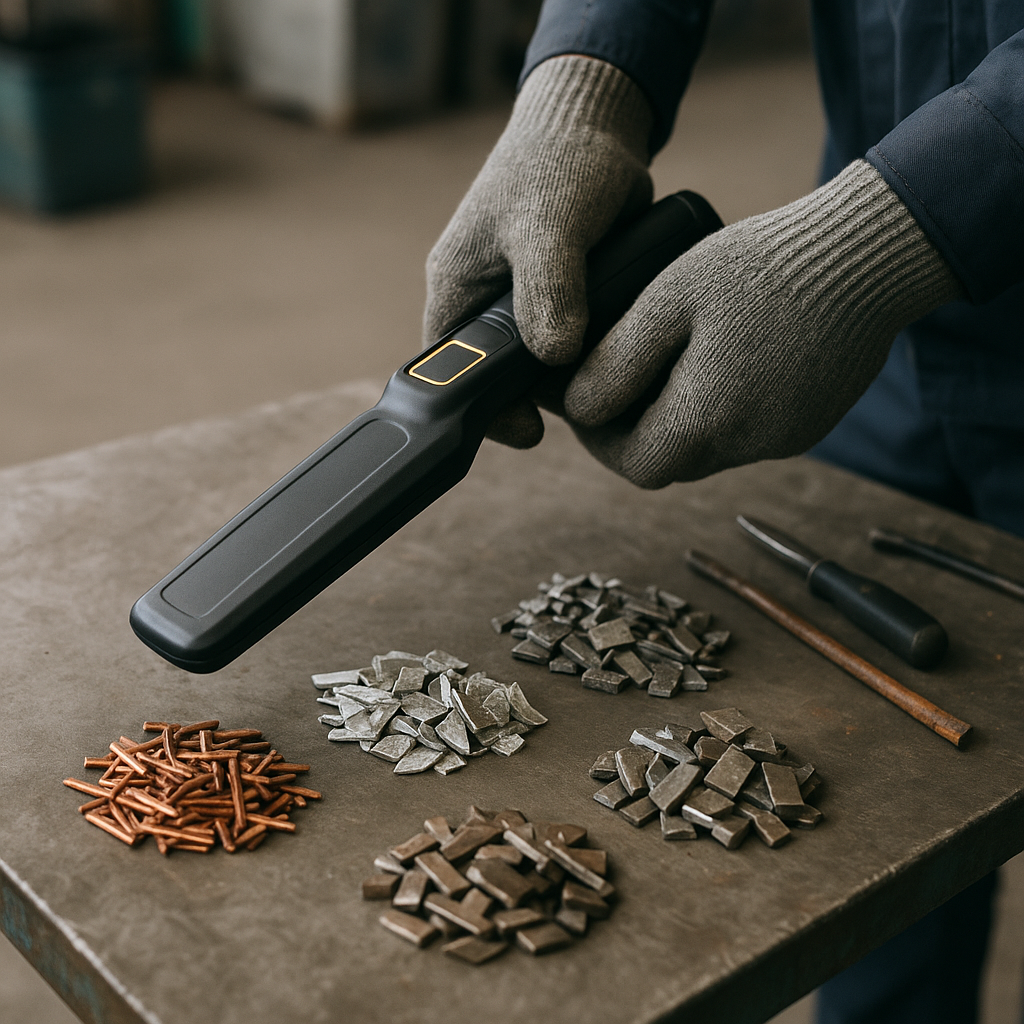
Identifying and sorting metals is crucial in the recycling process. Without proper identification, metals can end up in the wrong processing stream, compromising their recyclability and value. The recycling industry employs several methods to distinguish between different metal types, from basic manual techniques to sophisticated technological solutions.
Basic Identification Methods
The most straightforward method used in scrap yards is the magnet test. This simple yet effective technique separates ferrous metals (those containing iron) from non-ferrous metals. When a magnet is placed on a ferrous metal like steel or iron, it sticks firmly. Non-ferrous metals such as aluminum, copper, or brass show no magnetic attraction.
Visual inspection is another primary method used by experienced recyclers. The color, weight, and texture of metals can provide valuable clues to their composition. Copper has a distinctive reddish-brown appearance, while aluminum is lightweight and silvery. Brass displays a yellowish hue, and lead is notably heavy for its size.
Some recycling facilities also use basic tools like files to test hardness or chemical solutions to observe reaction patterns. While these methods require minimal equipment, they rely heavily on the operator’s experience and knowledge.
Advanced Sorting Technologies
For more precise identification, especially in large-scale operations, recyclers employ advanced analytical technologies. These methods provide detailed information about metal composition beyond what human inspection can determine.
X-Ray Fluorescence (XRF) analyzers have become increasingly popular in scrap yards. These devices direct X-rays at the metal surface, causing the atoms to emit secondary X-rays with energies unique to each element. XRF technology excels at identifying alloys and determining exact elemental composition without damaging the sample. It works particularly well for sorting aluminum alloys, precious metals, and specialized materials.
Laser-Induced Breakdown Spectroscopy (LIBS) represents another technological advancement in metal sorting. LIBS uses a focused laser pulse to vaporize a tiny portion of the metal sample, creating a plasma. As this plasma cools, it emits light at specific wavelengths that correspond to the elements present. LIBS has an advantage over XRF in detecting lighter elements like lithium, beryllium, and boron.
Optical Emission Spectrometry (OES) offers the highest precision for metal analysis. This technology works by exciting the atoms in a sample with an electrical spark or arc. The excited atoms emit light at characteristic wavelengths, which are then analyzed to determine the metal makeup. OES is particularly valuable for measuring trace elements and for quality control in metal production.
[[artifact_table]] Comparison of Metal Identification Technologies [[/artifact_table]]Industrial-Scale Sorting Systems
Large recycling operations implement automated systems that combine multiple identification technologies. Conveyor belt systems with magnets separate ferrous metals at the beginning of the process. Eddy Current Separators use rapidly rotating magnetic fields to repel non-ferrous metals like aluminum from non-metallic materials.
Some facilities incorporate sensor-based sorting systems that use cameras, X-rays, or near-infrared technology to identify and sort different metal types at high speeds. These automated systems can process tons of mixed scrap per hour with minimal human intervention.
The Impact of Proper Sorting on Recycling Value
The effort put into accurate metal identification directly affects the value and usefulness of recycled materials. Well-sorted metals command higher prices in the market. Contaminated or improperly sorted metals may require additional processing or result in lower-quality recycled products.
For example, when aluminum is contaminated with even small amounts of copper or iron, its melting point and physical properties change significantly. This contamination can render the recycled material unsuitable for certain applications. Similarly, different grades of steel must be properly sorted to maintain the specific properties required for various industrial uses.
The recycling industry continues to invest in better identification and sorting technologies. These investments improve efficiency and increase the percentage of metals that can be successfully recovered and repurposed.
What Are the Environmental Benefits of Scrap Metal Recycling?
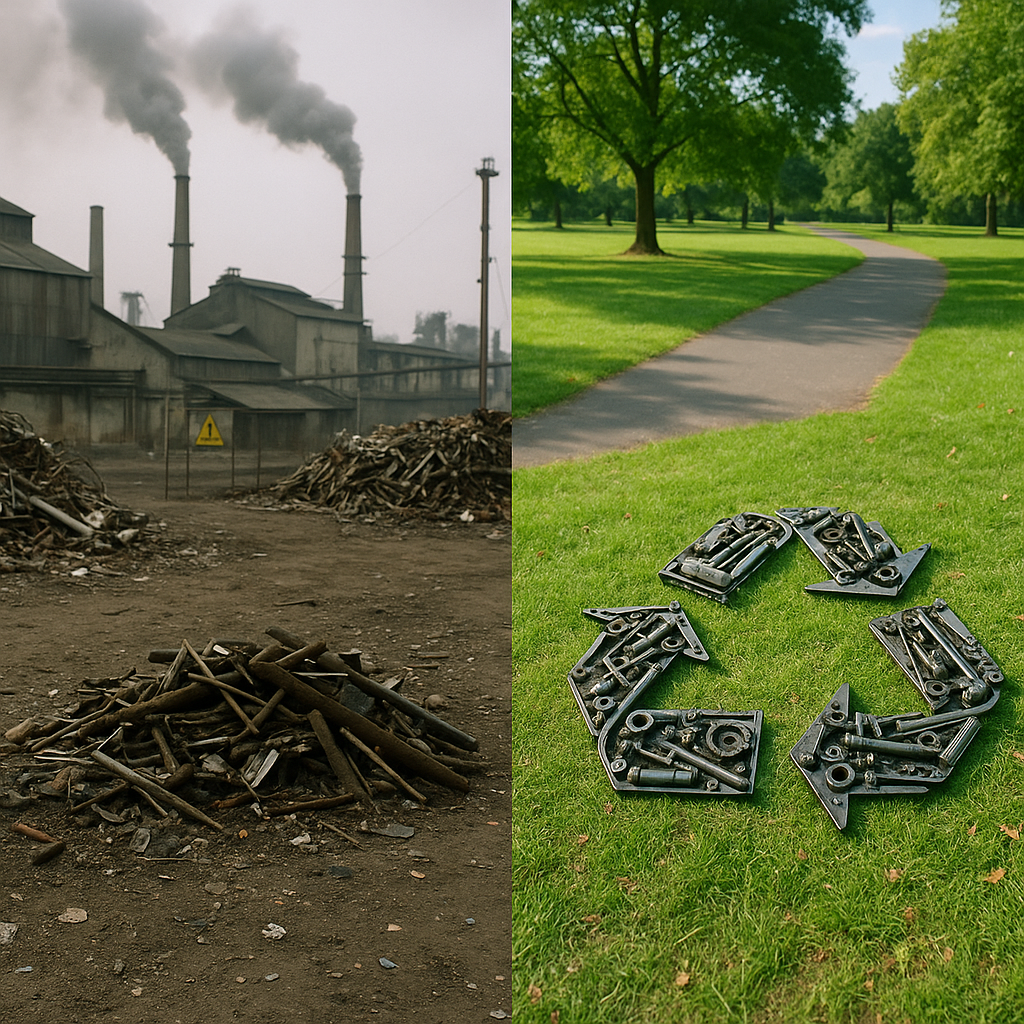
Scrap metal recycling is a highly impactful environmental practice in waste management. It transforms discarded metal items into valuable resources, preventing them from accumulating in landfills. This sustainable approach offers numerous environmental benefits beyond simple waste reduction.
Conservation of Natural Resources
Scrap metal recycling preserves finite natural resources. By reusing existing metals, we reduce the demand for raw ore extraction, which can lead to habitat destruction, soil erosion, and ecosystem disruption.
Recycling metal lessens the need for these harmful practices. For example, recycling one ton of steel saves nearly 2,500 pounds of iron ore, 1,400 pounds of coal, and 120 pounds of limestone. This conservation helps protect natural landscapes from mining activities.
The metal recycling process supports a circular economy where materials remain in use rather than discarded after a single application. This efficiency is crucial for building a sustainable future where valuable materials aren’t wasted.
Substantial Energy Savings
Processing recycled metal requires significantly less energy than producing new metal from raw ore. Aluminum recycling uses 95% less energy than extracting aluminum from bauxite, and steel recycling saves about 75% of the energy needed for primary production.
These energy savings reduce power plant emissions and overall environmental impact, decreasing pressure on electricity grids and fossil fuel consumption. Each ton of recycled metal represents significant energy conservation.
The manufacturing sector benefits from these efficiencies, lowering production costs and the environmental footprint of industries using recycled metals. This creates both economic and ecological advantages.
Reduction in Greenhouse Gas Emissions
Traditional metal production generates substantial greenhouse gas emissions through mining, refining, and manufacturing. Recycling produces a much smaller carbon footprint, with studies showing that recycling steel and aluminum reduces emissions by 86% and 95%, respectively.
By choosing recycled metal, manufacturers help combat climate change through reduced carbon dioxide output. The global impact of metal recycling programs represents millions of tons of prevented greenhouse gas emissions annually.
Recycling also reduces water vapor, methane, and other climate-altering gases, supporting global climate goals.
Decreased Landfill Waste
Metals occupy valuable landfill space and don’t break down over time. Some can leach harmful chemicals into soil and groundwater. Recycling programs divert these materials from waste streams.
Many municipalities have metal recycling programs to extend landfill lifespans, reduce contamination risks, and preserve disposal capacity for non-recyclable materials. This approach creates more sustainable communities.
Scrap metal represents a significant portion of recyclable material by weight, and its diversion from landfills greatly aids waste reduction efforts nationwide.
Minimized Pollution
Traditional metal production generates pollutants affecting air, water, and soil quality. Mining can contaminate waterways with heavy metals, while smelters release harmful compounds into the air.
Recycling metal significantly reduces these pollution sources. With fewer mining operations and cleaner processing, recycled metal production prevents many forms of environmental contamination, protecting ecosystems and public health.
By reducing the demand for newly mined ore, recycling helps minimize environmental hazards like acid mine drainage and habitat destruction.
Water Conservation
Metal production from raw ore requires vast amounts of water. Recycling metal can reduce water usage by up to 90% compared to primary production methods, crucial in water-scarce regions.
The reduced water demand also means less wastewater generation and fewer treatment challenges. Recycling dramatically reduces water quality concerns associated with industrial wastewater.
Fresh water sources remain protected when less water is diverted for industrial processes. This conservation benefits aquatic ecosystems that might otherwise be impacted by industrial water usage and potential contamination.
The environmental advantages of scrap metal recycling make a compelling case for expanding these programs. From resource conservation and energy savings to pollution reduction and climate protection, metal recycling delivers multiple ecological benefits. These advantages make recycling not just an environmentally responsible choice but an essential practice for sustainable resource management.
Conclusion: The Future of Scrap Metal Recycling
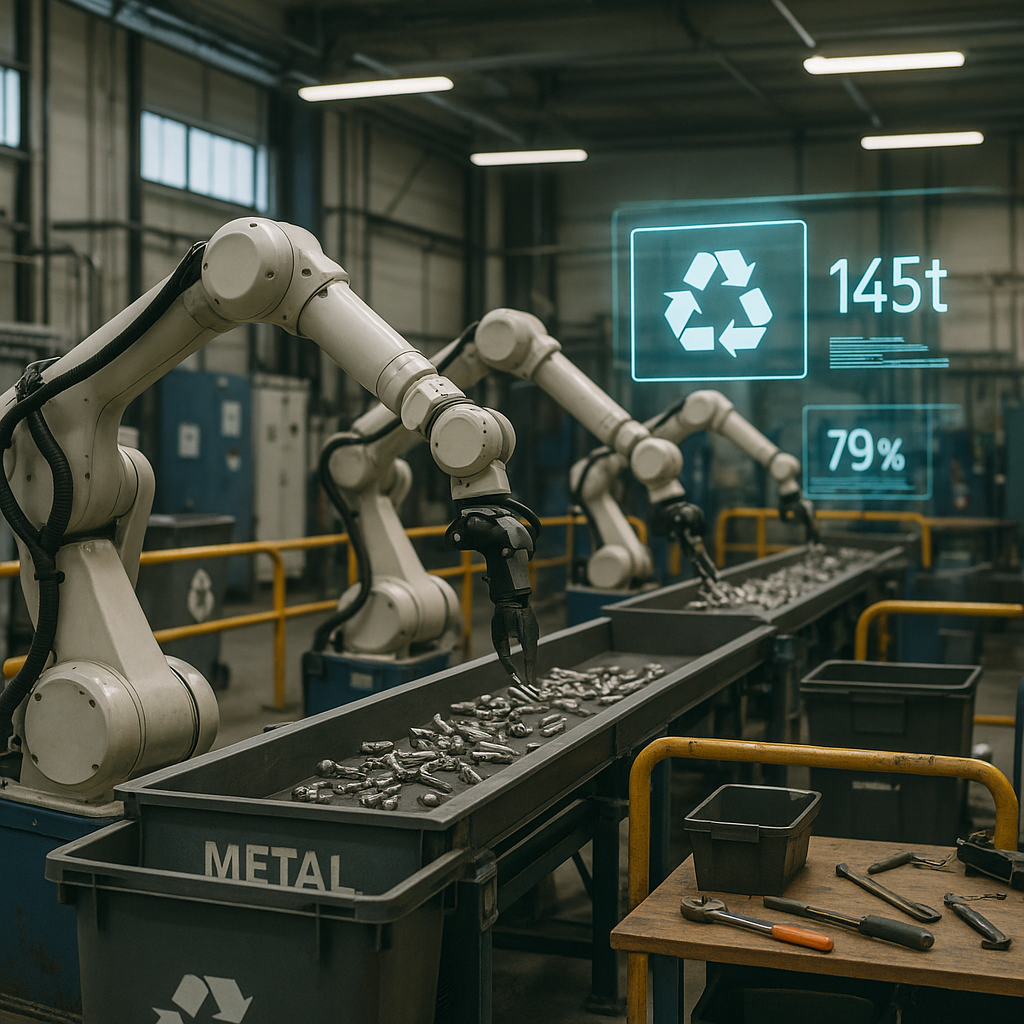
Scrap metal recycling is a cornerstone of sustainable waste management and resource conservation. The process transforms discarded metal into valuable resources, reducing the need for environmentally damaging mining operations. This recycling pathway saves up to 95% of the energy required to produce metals from raw materials and significantly decreases greenhouse gas emissions.
The future of scrap metal recycling is promising. Technological innovations in sorting techniques, artificial intelligence applications, and improved smelting processes will enhance efficiency and material recovery rates. As environmental awareness grows, individuals and businesses increasingly recognize that metal recycling creates jobs, stimulates local economies, and protects natural ecosystems. These combined benefits position scrap metal recycling as crucial in our transition toward a more sustainable circular economy.
For professional guidance on your recycling needs or to establish an effective metal recycling program, contact Okon Recycling at 214-717-4083.