5901 Botham Jean Blvd, Dallas, TX 75215
What Is Metal Shredding? Process, Machines, and Recycling Benefits Explained
July 10, 2025Metal shredding is a pivotal part of modern scrap metal recycling. This essential process turns bulky metal waste into uniform, manageable pieces that can be efficiently sorted and processed further. Instead of letting metal waste away in landfills for decades, shredding prepares it for a new life cycle.
At its core, metal shredding involves specialized industrial machinery designed to handle various types of metal. These robust shredders use powerful rotating hammers, blades, or cutting mechanisms to break down everything from discarded appliances to vehicle bodies. The technology can process both ferrous metals, like steel and iron, and non-ferrous materials such as aluminum, copper, and brass.
The environmental importance of metal shredding is significant. By reducing the volume of scrap metal and preparing it for efficient recycling, the process conserves natural resources, minimizes mining impacts, and greatly reduces energy consumption compared to producing new metal from raw materials.
What are the Key Steps in the Metal Shredding Process?
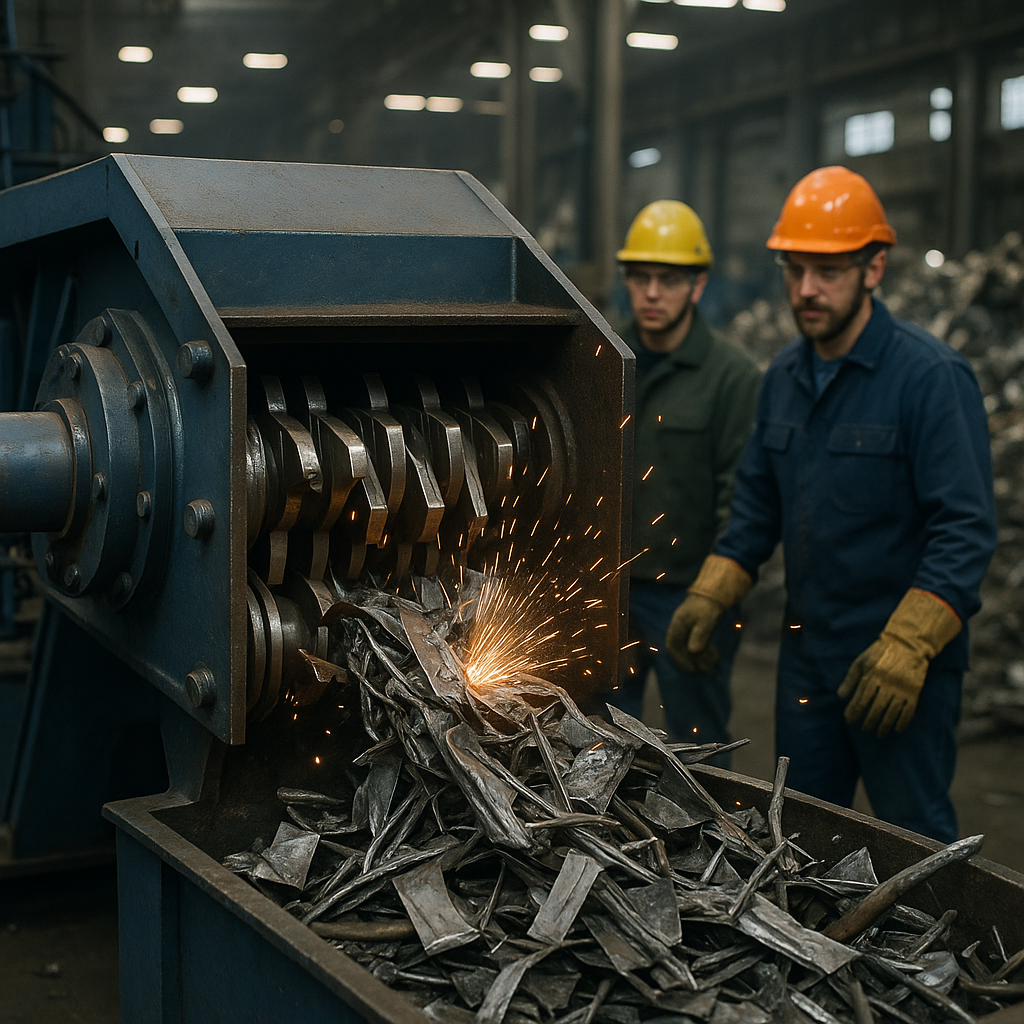
The metal shredding process includes four crucial stages that convert bulky scrap metal into valuable recycled materials. Each step is essential for maximizing resource recovery and processing efficiency.
Segregation
The first step in metal shredding is segregation. Collected scrap metal is carefully separated by type, size, and weight during this phase, ensuring the recycling process runs efficiently.
Metals are classified according to their density and composition. Modern facilities employ automated sorting equipment with magnetic sensors to differentiate ferrous metals (containing iron) from non-ferrous metals like aluminum and copper.
Foreign objects such as plastic, rubber, glass, and other non-metallic materials must be identified and removed. This ensures the final recycled product remains pure and free from contaminants.
Preparation
Once segregated, the metal enters the preparation phase, readying it for shredding. Similar materials are grouped together to optimize shredding efficiency.
Large pieces may be cut down to manageable sizes using specialized equipment. Some facilities employ pre-shredders to break down exceptionally bulky items before they enter the main shredding system.
The preparation stage is vital for preventing equipment damage and ensuring consistent processing. It also helps reduce wear on the main shredding machinery by removing problematic items that could cause jams or mechanical failures.
Shredding Process
The shredding process involves powerful machinery designed to cut, tear, and break down metal into smaller fragments. Industrial metal shredders use various mechanisms, including rotors with hammers, blades, or cutting discs.
Metal is fed into the shredder through a hopper or conveyor system. Inside the shredding chamber, the material encounters rapidly rotating components that reduce it to the desired size.
During shredding, the machinery’s high torque and cutting force transform bulky scrap into standardized pieces. This size reduction enhances subsequent processing efficiency and economics.
The shredded material passes through sizing screens, ensuring consistent fragment dimensions. Pieces that are too large are automatically recirculated for further size reduction.
Post-Processing
After shredding, the metal enters the post-processing stage. The shredded material is easier to transport and further process.
One major benefit of shredding is that it facilitates the separation of different materials. Shredding naturally helps detach non-metallic components like plastics, foam, glass, rubber, textiles, and electrical components from the metal.
Post-processing typically involves various separation technologies. Magnetic separators extract ferrous metals, while eddy current separators recover non-ferrous metals based on their conductivity. Air classification systems help remove lighter materials like plastic and paper.
The separated metal fragments are now ready for melting and refining into new products. Meanwhile, the non-metallic materials can be directed to appropriate recycling streams rather than ending up in landfills.
Component | Material Type |
Ferrous Materials | Steel, Iron |
Non-Ferrous Materials | Aluminum, Copper, Brass |
Plastics | Various Types |
Foam | Polyurethane, Styrene |
Glass | Silica Based |
Rubber | Synthetic, Natural |
Textiles | Cotton, Polyester |
Electrical Components | Various Metals and Plastics |
Through these four key steps, the metal shredding process transforms waste into valuable resources ready for reuse in manufacturing. This process significantly cuts down on the need for mining raw materials while conserving energy and minimizing environmental impact.
What Types of Metal Shredders are Used in the Process?
Metal recycling facilities use various shredder types to process different metal waste streams effectively. Each machine serves a unique role in metal recovery. The choice of equipment depends on the material being processed and the desired output.
Single-Shaft Shredders
Single-shaft shredders have one rotating shaft with cutting blades that work against fixed counter knives. They are ideal for processing lighter metal waste like cables and aluminum profiles. These machines operate at slower speeds but produce high torque.
The design of single-shaft shredders makes them lightweight and convenient for operations with limited space. They typically include a hydraulic ram that pushes material toward the cutting mechanism. This feature ensures consistent feeding and prevents jamming.
Double-Shaft Shredders
Double-shaft shredders consist of two parallel rotating shafts with interlocking blades. The counter-rotating action creates a powerful shearing force suitable for tougher metal scrap. These machines provide excellent stability and efficiency for medium-volume operations.
The robust construction of double-shaft models makes them suitable for continuous operation in demanding environments. They offer reliable performance when processing mixed metal waste, making them popular in scrap yards and recycling facilities.
Multi-Shaft Configurations
Four-shaft shredders are in the heavy-duty category of metal processing equipment. They include additional cutting surfaces for more intensive size reduction. The multiple shafts work together to process complex materials like automotive scrap and industrial waste.
These sophisticated machines can handle higher throughput volumes compared to simpler designs. The extra shafts create a more thorough shredding action, resulting in more uniform output sizes crucial for downstream sorting processes.
Hammer Mill Shredders
Hammer mill shredders use rapidly rotating hammers to pulverize metal materials against a solid anvil. Available in both horizontal and vertical configurations, these powerful machines excel at processing larger metal items like automobile bodies and appliances.
The impact-based design creates high-velocity force to break apart even tough metals. Hammer mills typically include screening systems to control output particle size. They are fundamental to large-scale metal recycling operations.
The versatility of hammer mills allows for the simultaneous processing of various metal types. However, they require significant power input and regular maintenance. Their throughput capacity makes them essential for high-volume recycling facilities.
Shredder Type | Application | Capacity (t/h) |
---|---|---|
Single-Shaft Shredder | Lighter metal waste like cables and aluminum profiles | 1.5 – 3.5 |
Double-Shaft Shredder | Medium-volume operations and mixed metal waste | Varies |
Four-Shaft Shredder | Complex materials like automotive scrap and industrial waste | Higher throughput volumes |
Hammer Mill Shredder | Larger metal items like automobile bodies and appliances | Up to 350 |
Each shredder type offers distinct advantages depending on the recycling operation’s specific requirements. The choice between these technologies affects processing efficiency, energy consumption, and final product quality. Modern facilities often use multiple shredder types in sequence to optimize metal recovery rates.
What Happens After Metal Shredding?
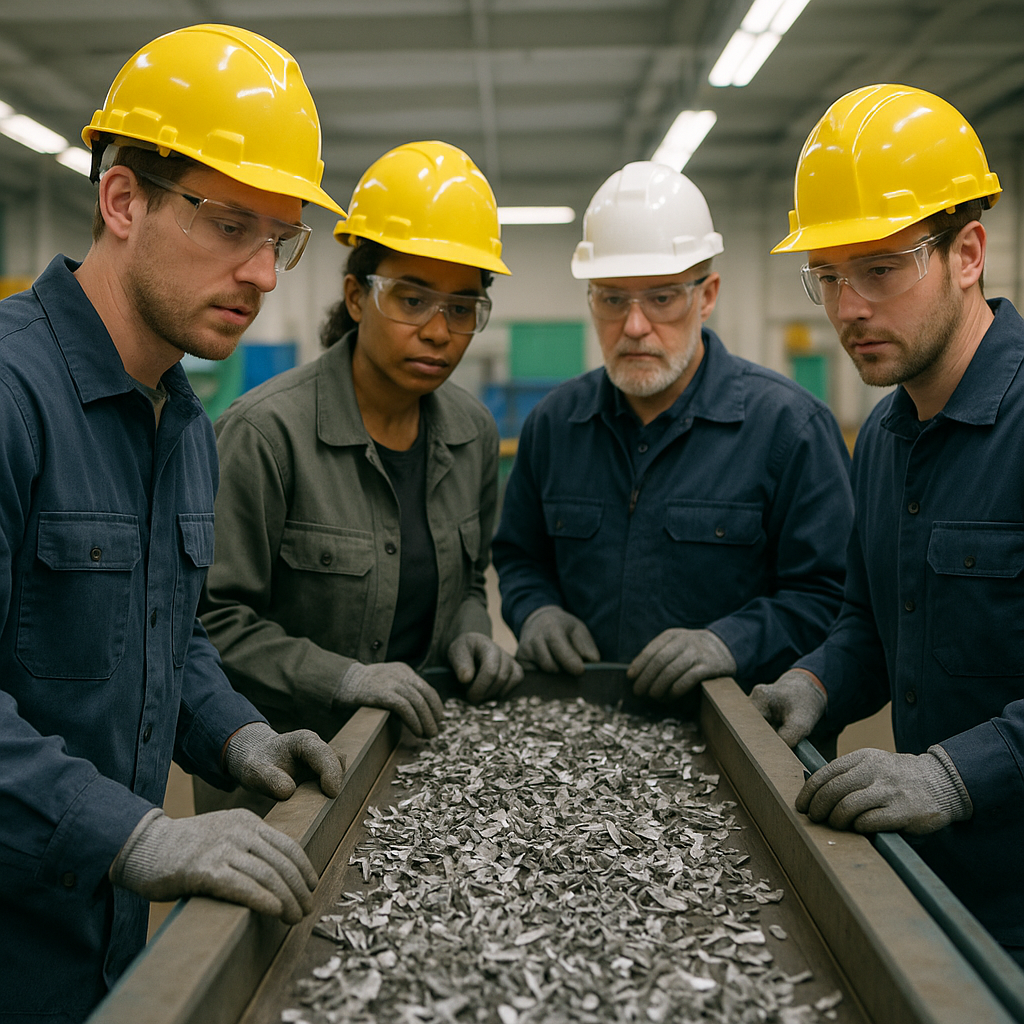
After metal shredding, it enters a series of crucial processing stages that transform it from fragmented scrap into valuable raw material. The journey from shredded metal to reusable resource involves several specialized techniques tailored to different metal types.
Material Separation
The first post-shredding step is the thorough separation of materials. Large magnetic separators efficiently extract ferrous metals like steel and iron from the mixture. These powerful magnets pull ferrous materials from conveyor belts, creating a clean stream of recyclable iron-based metals.
Non-ferrous metals such as aluminum, copper, and brass require different separation methods. Eddy current separators use rapidly alternating magnetic fields to repel non-ferrous metals from other materials. This technology works because the changing magnetic field induces electrical currents within the non-ferrous metals, creating a magnetic field that opposes the original field.
Advanced scrap yards also employ sensor-based sorting systems using optical, X-ray, or infrared technology to identify and separate different metal types with remarkable precision. This ensures maximum recovery of valuable materials from the shredded mixture.
Melting Process
Once properly sorted, the metals move to specialized furnaces for melting. Ferrous metals typically enter large electric arc furnaces where temperatures reach 3,000°F. Steel mills use this intense heat to transform solid scrap into molten metal in just a few hours.
Non-ferrous metals like aluminum melt at lower temperatures in furnaces designed specifically for these materials. The energy savings from recycling aluminum rather than producing it from raw bauxite ore are substantial – recycling saves about 95% of the energy required for primary production.
The melting process represents a crucial transformation point where irregularly shaped scrap becomes a uniform liquid state ready for purification and reforming. Different metals require specific furnace types and temperature controls to achieve optimal results.
Purification and Refining
The molten metal often contains impurities that must be removed. Electrolysis is one of the most effective purification methods, particularly for non-ferrous metals. During this process, an electric current passes through the liquid metal, causing impurities to separate from the pure metal.
For copper recycling, electrolytic refining achieves exceptional purity levels. The process involves placing the impure copper in an electrolytic cell where it dissolves and then redeposits on cathode plates as 99.99% pure copper.
Steel undergoes different refining methods, such as oxygen lancing to remove carbon impurities and the addition of alloying elements to achieve specific properties. This refining stage ensures the recycled metal meets quality standards for industrial applications.
Solidification and Preparation
After purification, the molten metal moves via conveyor systems to cooling stations where it solidifies into usable forms. Depending on market requirements, metals may be cast into ingots, bars, sheets, or specialized shapes.
Aluminum often becomes solid rectangular blocks called ingots, which foundries and manufacturers can melt again for various applications. Steel typically transforms into slabs, billets, or coils ready for rolling mills.
The cooling process requires precise temperature control to ensure proper crystallization and material properties. Once solidified, the metal undergoes quality testing to verify its composition and mechanical properties before shipment to manufacturers.
From Recycled Metal to New Products
The final stage in the metal recycling journey involves manufacturing new products from the processed material. Recycled steel finds its way into construction beams, automotive parts, and appliances. A recycled car can become a structural support in a new building in just weeks.
Aluminum recycling creates material for beverage cans, window frames, and electronics housing. The efficiency of aluminum recycling means a recycled can may return to store shelves as a new container in just 60 days.
Copper from old plumbing and wiring transforms into new electrical components, maintaining its excellent conductivity through multiple recycling cycles. This continuous loop of metal use and reuse forms the backbone of sustainable resource management in modern manufacturing.
The complete metal recycling process—from collection through shredding, melting, purification, and manufacturing—creates a circular economy that significantly reduces environmental impact compared to virgin metal production. This closed-loop system conserves natural resources while reducing energy consumption and greenhouse gas emissions.
Metal Type | Energy Saved Through Recycling | Benefits |
---|---|---|
Aluminum | 95% | Running an AC for 30 hours |
Copper | 85% | Powering a household for 2 weeks |
Steel | 60% | Driving 500 miles in an average car |
Conclusion: The Impact and Future of Metal Shredding
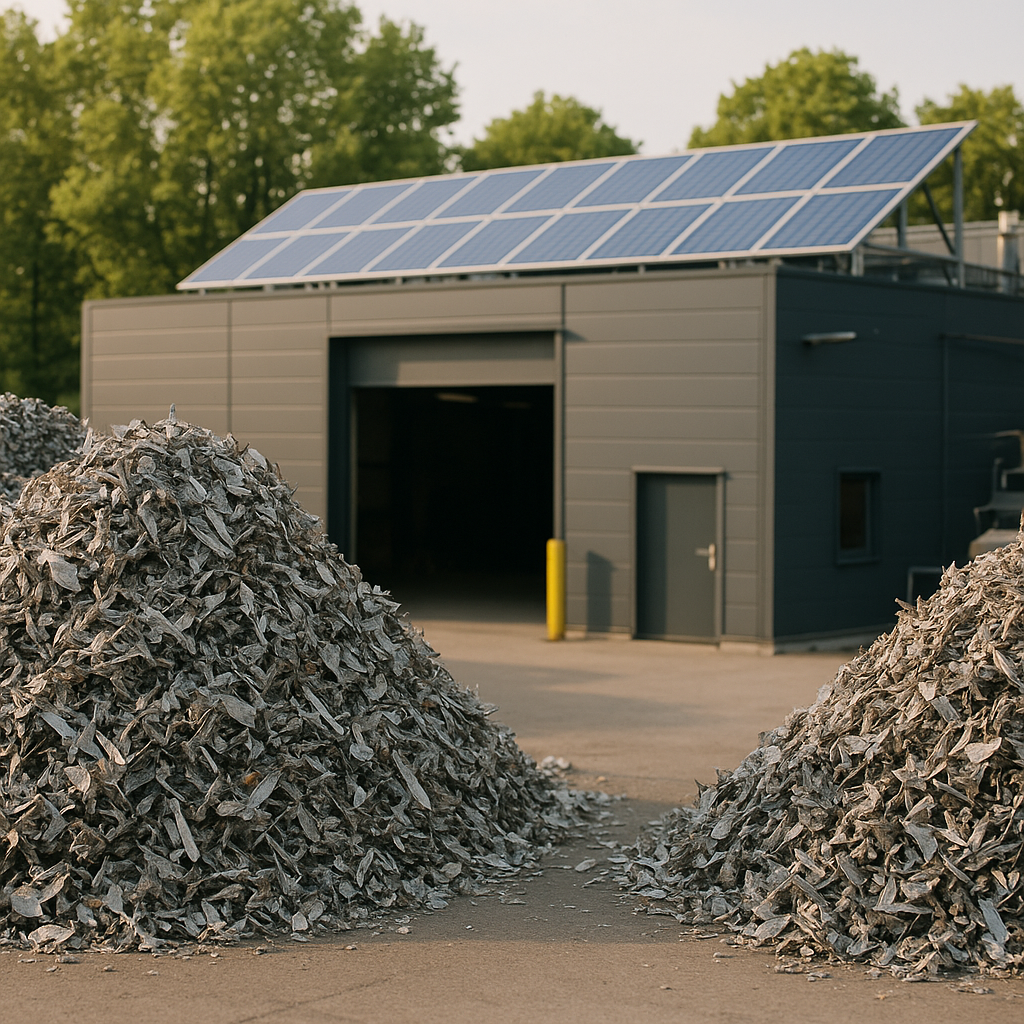
Metal shredding is a crucial component of contemporary recycling systems. By efficiently processing large volumes of scrap metal, shredding technology significantly reduces the need for extracting new metal. This conservation of natural resources leads to less mining, reduced energy consumption, and lower carbon emissions throughout the metal supply chain.
As shredding technology advances, more efficient and environmentally friendly processes are emerging. These innovations are reinforcing the circular economy model, where materials are retained in use for as long as possible. The recycling industry’s ability to process and recover metals is becoming increasingly vital as global demand for resources grows despite diminishing availability. For your metal recycling needs and to learn more about sustainable waste management solutions, contact Okon Recycling at 214-717-4083.