5901 Botham Jean Blvd, Dallas, TX 75215
What Is a Mobile Shear in Recycling?
July 24, 2025Mobile shears are among the most versatile tools in modern recycling operations. These powerful hydraulic attachments are specifically engineered to cut through metal with precision and force. Designed to handle the toughest materials, mobile shears efficiently process everything from scrap metal and steel beams to pipes and complex demolition debris.
The strength of mobile shears lies in their adaptability. They can be mounted on various types of heavy equipment, including excavators, material handlers, and specialized recycling machinery. This mounting flexibility allows operators to deliver cutting power directly where it’s needed most, whether at a bustling scrap yard, an active demolition site, or a metal recycling facility.
Mobile shears transform recycling operations by efficiently processing materials. Their robust cutting jaws and hydraulic power systems quickly reduce large metal objects into manageable sizes for further processing or transport. This capability is crucial in today’s resource-conscious recycling industry, where efficiency and material recovery rates directly impact profitability.
How Do Mobile Shears Work in Recycling Operations?
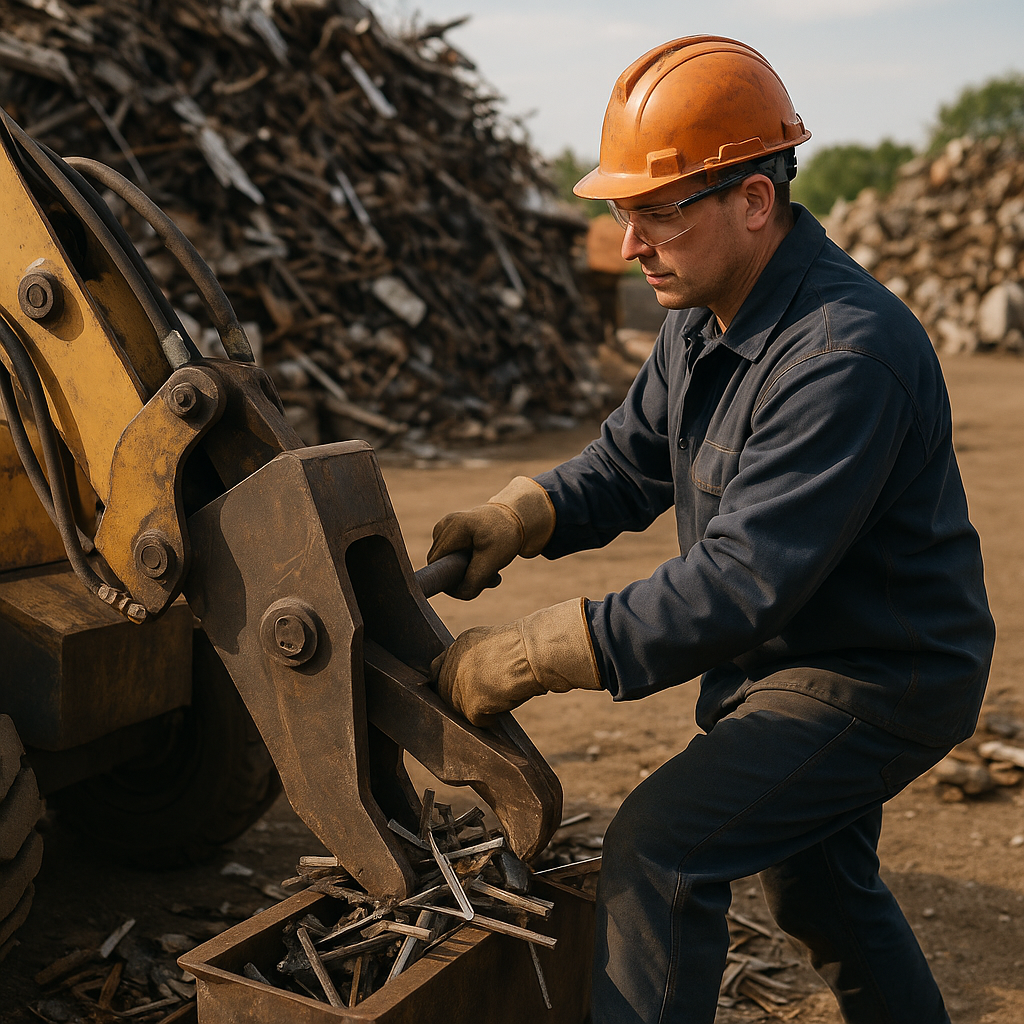
Mobile shears operate through a powerful hydraulic system that drives their upper and lower jaws. These jaws feature hardened steel cutting blades specifically designed to slice through various metals. The upper jaw moves against the stationary lower jaw, creating a scissor-like action that provides maximum cutting force precisely where needed.
When processing scrap metal, the operator positions the shear at the desired cutting point. The jaws open wide—typically between 22 to 32 inches, depending on the model—allowing them to grasp large pieces of steel, rebar, or other metals. Once the material is secured, the hydraulic system activates, driving the blades together with an impressive force ranging from 600 to over 1,000 tons of cutting pressure.
The design of mobile shears includes several key functional elements. Most models feature a bolt-on piercing tip at the front of the jaws that initially penetrates the material, aiding in efficiently beginning cuts, even on tough structural steel. The blades extend from this tip through to the throat of the device, ensuring complete cutting capability along the entire jaw length.
Modern mobile shears incorporate an internal guide system that maintains proper jaw alignment during operation. This alignment is crucial for clean, precise cuts and extends the life of the blades. The open throat design allows processed material to pass through, preventing jams that would otherwise slow down recycling operations.
An engineering advantage of mobile shears is their leverage system. The long lever arm on the pivoting jaw allows the shears to use lower hydraulic pressure while still delivering exceptional cutting force. This reduces structural stress on both the shear and the host excavator, extending equipment life and improving operational efficiency.
For continuous recycling operations, many mobile shears feature regenerative hydraulic systems. These systems recycle hydraulic fluid during operation, providing faster cycle times and increased productivity. This feature is especially valuable in high-volume recycling facilities where processing speed directly impacts profitability.
The effectiveness of mobile shears stems from their ability to deliver clean, accurate cuts with minimal distortion. Unlike torch cutting or other methods, shears create minimal heat and reduce the risk of fire when processing potentially flammable materials. The precision cutting action also produces more uniform scrap pieces, which can be efficiently processed in subsequent recycling steps.
Mounting options add to the versatility of mobile shears in recycling operations. Models can be attached directly to excavator booms or sticks, and many feature 360-degree rotation capabilities. This rotation allows operators to position the shears at optimal cutting angles without repositioning the entire machine, significantly improving efficiency in confined spaces or when working with complex materials.
Model | Weight (lbs) | Jaw Opening (in) | Reach 2nd Member (in) | Cutting Capacity (in) | Carrier Weight 2nd Member (tons) | Carrier Weight 3rd Member (tons) |
S3.5R | 772 | 10.5 | 61 | 1.5 | 1.6-3 | 3-7 |
S7R | 1653 | 13.5 | 69 | 1.75 | 4-8 | 8-15 |
S18R | 4409 | 19 | 98 | 2.5 | 10-20 | 16-27 |
S25XP | 6173 | 23 | 112 | 3.25 | 17-27 | 24-33 |
S38R | 8377 | 27.5 | 126 | 3.5 | 22-32 | 32-47 |
S54R | 12015 | 31 | 146 | 4.3 | 29-45 | 46-65 |
S71R | 15763 | 34 | 161 | 4.75 | 42-60 | 60-69 |
What Are the Key Features of Mobile Shears?
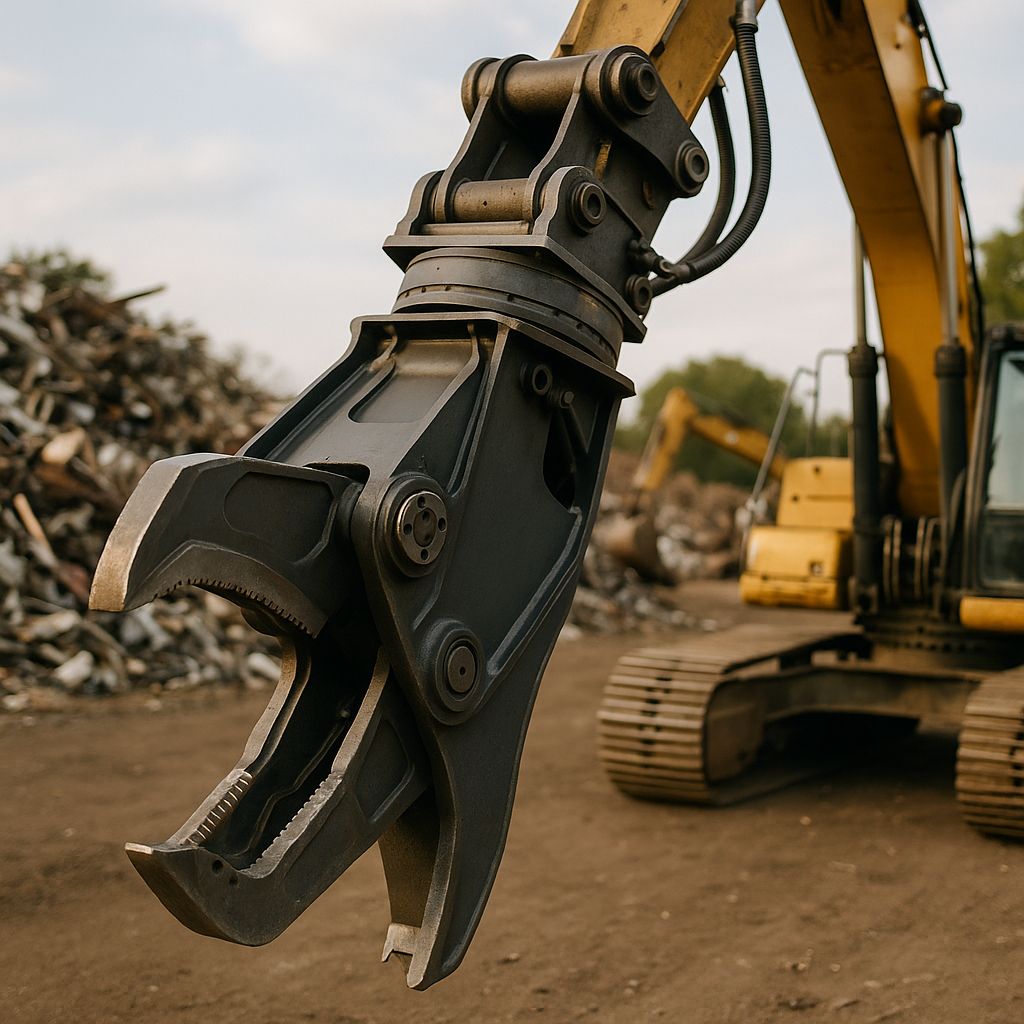
Mobile shears possess specific features necessary for effectively handling demanding recycling and demolition tasks. These powerful attachments turn excavators into efficient material processing tools. Understanding their key features assists operators in selecting the right equipment for their particular needs.
Excavator compatibility is the first crucial factor. Mobile shears are designed to mount on specific excavator models based on weight class and hydraulic capabilities. Manufacturers offer both second-member (boom-mounted) and third-member (stick-mounted) configurations to suit various applications.
Essential Performance Features
Jaw specifications affect cutting capability. Wider jaw openings allow processing of larger materials, while jaw depth determines how far materials can be inserted for cutting. For instance, the Genesis GXT 555 model has a 30-inch jaw opening with a matching 30-inch depth, ideal for processing substantial scrap.
Attachment reach and weight must be balanced for stability. The reach measurement — from mounting pivot to the front of the shear — affects how far the operator can extend the tool. Weight distribution impacts excavator stability, with advanced models like the GXT series having a center of gravity closer to the carrier for better handling.
Rotation capability enables precise positioning without moving the excavator. High-quality shears typically include 360-degree rotation systems with dedicated hydraulic circuits. This feature significantly boosts productivity by allowing operators to cut materials at optimum angles.
Maximum cutting force determines what materials the shear can process. This force varies across different points in the jaw — highest at the throat (rear) and decreasing toward the tip. Premium models generate excellent force-to-weight ratios for cutting various materials, including I-beams, pipes, and structural steel.
Advanced Design Features
Modern mobile shears feature redesigned cutting jaws that optimize material flow. Straight lower jaws with apex upper jaws distribute material along the blade’s length rather than compressing it at one point. This design utilizes cutting force more effectively and extends blade life.
Dual guide blades help maintain blade alignment during cutting operations. This feature prevents material from escaping between the blades and ensures clean cuts with minimal distortion. Single guide blades are typically found on smaller models like the GXT 115.
Enhanced piercing tips improve initial material penetration. Many models now feature bolt-on, reversible tips that can be quickly replaced when worn, reducing downtime and protecting the upper jaw from damage during piercing operations.
Speed valves in the hydraulic system reduce cycle times. These valves allow faster jaw opening while maintaining powerful closing force, resulting in more cuts per hour and increased productivity in demanding applications.
Maintenance Considerations
Blade design and mounting systems affect long-term operating costs. Premium shears offer reversible cutting edges — typically four per blade — that can be rotated to extend service life before replacement is needed. Some models use specialized retaining systems to prevent bolt loosening during operation.
Adjustable pivot assemblies allow operators to maintain proper blade alignment. This feature compensates for normal wear and ensures consistent cutting performance throughout the shear’s service life. Adjusting tolerances in the field minimizes downtime.
Build-up and hard-surfacing requirements vary between models. Areas subject to high wear often need periodic hard-surfacing to maintain structural integrity. Advanced designs minimize these requirements through improved geometry and replaceable wear components.
Hydraulic requirements must match excavator capabilities. Effective operation depends on maintaining proper operating pressure and flow rates to the attachment. Most models operate at pressures around 5,075 psi, with flow requirements varying by size.
Model | Weight (lbs) | Jaw Opening (in) | Reach 2nd Member (in) | Cutting Capacity (in) | Carrier Weight 2nd Member (tons) | Carrier Weight 3rd Member (tons) |
---|---|---|---|---|---|---|
S3.5R | 772 | 10.5 | 61 | 1.5 | 1.6-3 | 3-7 |
S7R | 1653 | 13.5 | 69 | 1.75 | 4-8 | 8-15 |
S18R | 4409 | 19 | 98 | 2.5 | 10-20 | 16-27 |
S38R | 8377 | 27.5 | 126 | 3.5 | 22-32 | 32-47 |
S54R | 12,015 | 31 | 146 | 4.3 | 29-45 | 46-65 |
Understanding these key features helps operators select the right mobile shear for their specific applications. When properly matched to the carrier and application, these versatile attachments can greatly improve productivity in scrap processing and demolition operations.
What Are the Applications of Mobile Shears in Recycling?
Mobile shears are versatile hydraulic attachments that have transformed scrap processing and recycling operations. These powerful tools are indispensable in many material recovery facilities due to their ability to efficiently cut through metal with precision and force.
Scrap Metal Processing
In scrap yards, mobile shears are essential for reducing large metal items into manageable pieces. They easily cut through I-beams, steel bars, pipes, and automobile bodies. This size reduction is crucial for further processing and transportation.
The cutting efficiency of these machines—some capable of 3-5 cuts per minute—enables recycling facilities to manage high volumes of mixed metal scrap quickly, leading to higher throughput and improved profitability.
Construction and Demolition Recycling
When buildings are demolished, mobile shears play a significant role. They excel in structural demolition, cleanly cutting steel beams and reinforced concrete while minimizing noise and dust compared to other methods.
Construction recycling projects benefit from mobile shears’ ability to separate valuable metals from other materials, facilitating the recovery of steel from concrete structures and other building components.
On-Site Preprocessing
A major advantage of mobile shears is their portability. Mounted on excavators or material handlers, they can preprocess scrap material directly on demolition sites or at temporary collection points.
This on-site preprocessing significantly reduces transportation costs by allowing contractors to cut materials down to efficient sizes where they are generated, instead of hauling bulky scrap to a recycling facility.
Specialized Recycling Applications
Mobile shears are also used in specialized recycling sectors. In automotive recycling, they efficiently dismantle end-of-life vehicles, separating valuable metals from other components.
Railway maintenance operations employ specialized rail-cutting mobile shears to process old tracks and railway components. These purpose-built attachments can handle the hardened steel used in rail infrastructure.
In industrial settings, mobile shears assist in decommissioning equipment and processing manufacturing scrap. Their precision cutting capabilities are ideal for dismantling complex industrial machinery.
Environmental Benefits
By enabling more efficient recycling processes, mobile shears offer significant environmental benefits. They maximize the recovery of valuable metals from scrap, reducing the need for new raw material extraction.
Using mobile shears in recycling lowers energy consumption compared to traditional processing methods. For instance, recycling aluminum with these tools can save up to 95% of the energy required to produce new aluminum from raw materials.
The versatility of mobile shears allows recycling facilities to adapt to changing material streams. As waste composition evolves, these adaptable tools continue to demonstrate their value in extracting recyclable materials efficiently and economically.
Conclusion
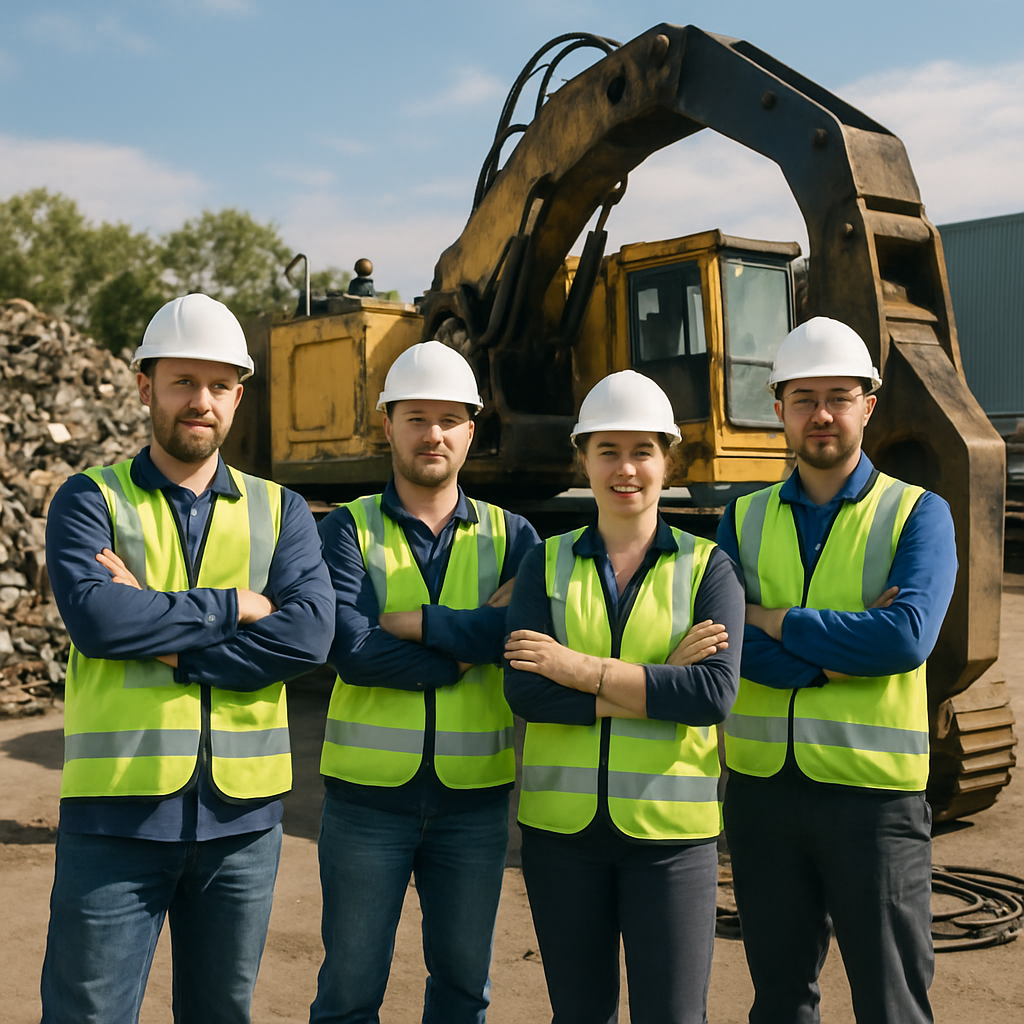
Mobile shears have become indispensable in modern recycling due to their unmatched versatility, cutting precision, and operational efficiency. Whether processing scrap metal at a facility or performing on-site demolition, these hydraulic tools significantly accelerate material handling and recovery. Their ability to produce clean, uniform scrap improves downstream processing, reduces transportation costs, and contributes to a more efficient and sustainable recycling workflow.
Contact Okon Recycling at 214-717-4083 to learn how mobile shears can enhance your recycling operation’s productivity and profitability.