5901 Botham Jean Blvd, Dallas, TX 75215
What is Metal Reclamation? Understanding its Benefits
July 2, 2025Metal reclamation is the process of recovering valuable metals from waste streams and scrap materials. The metals salvaged through this process are virtually identical to those produced through traditional mining and ore processing methods. When done properly, reclaimed metals retain all the same properties and qualities as their virgin counterparts.
With natural resources dwindling, metal reclamation has become a cornerstone of sustainable materials management. The process involves collecting, sorting, processing, and refining discarded metal products to extract materials that can be reused in manufacturing new goods, creating a circular flow of resources rather than the traditional extract-use-dispose model.
The importance of metal reclamation extends beyond environmental benefits. With raw material deposits becoming increasingly scarce and mining operations requiring significant energy inputs, reclaiming metals from waste streams offers a practical solution to resource scarcity while simultaneously reducing pollution and energy consumption. Industries worldwide now recognize metal reclamation as essential to their long-term economic viability and environmental responsibility.
What Are the Main Processes in Metal Reclamation?
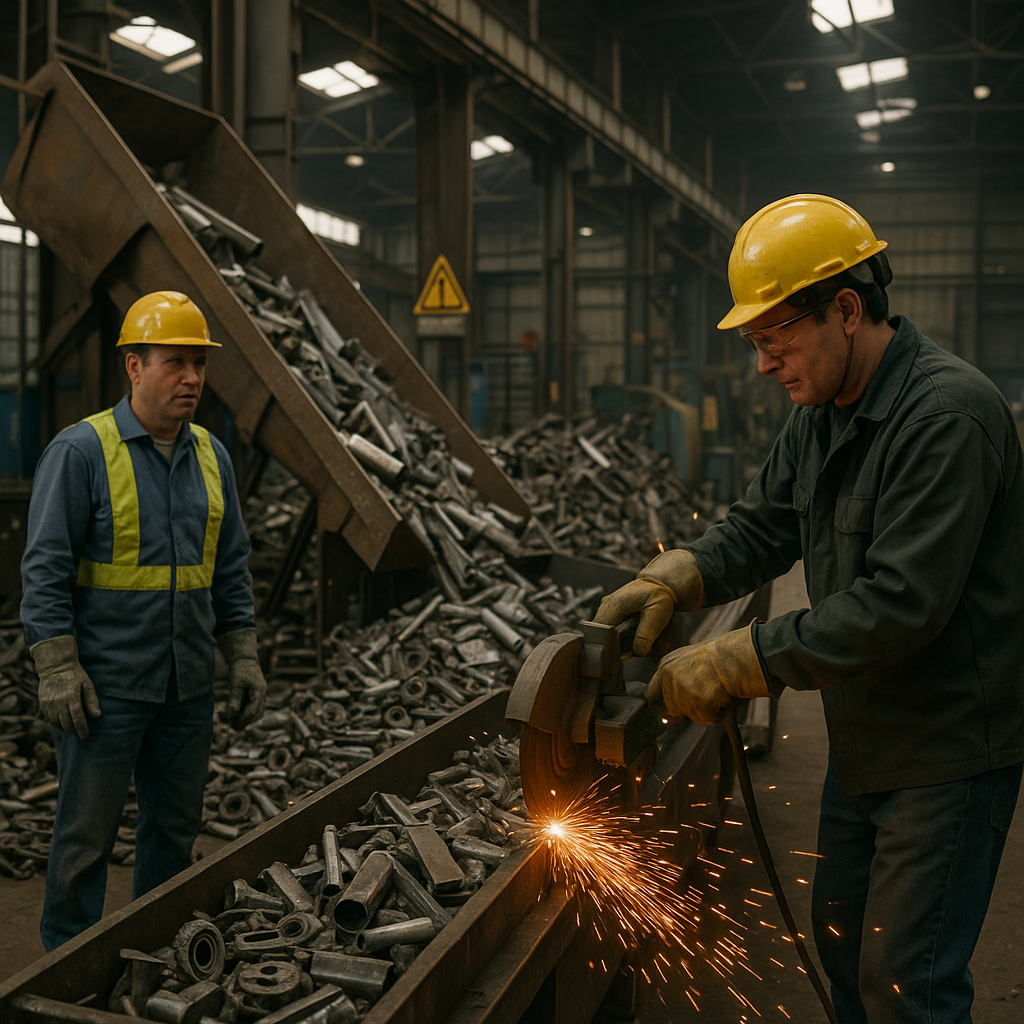
Metal reclamation transforms discarded metal materials into reusable resources through several specialized processes. Each step is crucial for ensuring maximum recovery and maintaining the quality of the final product.
Collection and Sorting
The initial step in metal reclamation involves collecting scrap metal from various sources, such as industrial waste, construction debris, and end-of-life products.
Once collected, sorting separates different types of metals. This often involves the combination of manual inspection and advanced technologies like magnetic separators for ferrous metals and eddy current separators for non-ferrous metals like aluminum and copper.
Proper sorting is essential as mixing incompatible metals can compromise the quality of the reclaimed material. For instance, even a small amount of copper in steel can significantly alter its properties.
Processing and Size Reduction
After sorting, the metals undergo crushing and grinding to reduce their size, increasing surface area and making subsequent processes more efficient.
Industrial shredders break down larger pieces into manageable fragments, while specialized crushing equipment handles various metals based on their hardness and composition.
Screening then separates the crushed materials by size, ensuring consistency for the next stages of reclamation.
Smelting
Smelting is a high-temperature process that melts the metal to separate it from impurities. The temperature and technique vary depending on the metal being reclaimed.
For example, aluminum reclamation typically uses reverberatory furnaces that reflect heat from the roof onto the metal. This allows aluminum to melt at around 660°C without direct flame contact that might introduce contaminants.
Copper and lead often undergo smelting in blast furnaces where heated air is forced into the bottom of the furnace. This creates temperatures high enough to separate the metals from their compounds.
During smelting, chemical reactions convert metal oxides into pure metals through a reduction process. Additives like limestone help draw out impurities, forming a layer of slag that can be removed.
Metal | Smelting Temperature (°C) | Smelting Temperature (°F) |
---|---|---|
Aluminum | 660 | 1220 |
Brass | 930 | 1710 |
Copper | 1084 | 1983 |
Iron | 1538 | 2800 |
Lead | 327.5 | 621 |
Silver | 961 | 1761 |
Refining
The final step involves refining the melted metal to achieve the desired purity levels. Different metals require specific refining techniques.
Electrolytic refining is common for copper reclamation, using electricity to transfer copper ions from an impure copper anode to a pure copper cathode in an electrolyte solution.
Zinc refining often involves distillation processes that take advantage of zinc’s relatively low boiling point compared to other metals and impurities.
For precious metals found in electronic waste, specialized refining processes extract minute quantities of gold, silver, and platinum group metals. These processes must be precise as these metals exist in very small concentrations.
Solidification and Transportation
After refining, the purified metal is cast into ingots, billets, or other forms suitable for manufacturing. These standardized shapes facilitate handling, transportation, and further processing.
Quality control measures verify the composition and properties of the reclaimed metal, ensuring it meets industry specifications for its intended use.
The reclaimed metals are then transported to manufacturers for use as raw materials in new products. This completes the recycling loop, demonstrating the circular economy in action.
What Are the Hazards and Control Measures in Metal Reclamation?
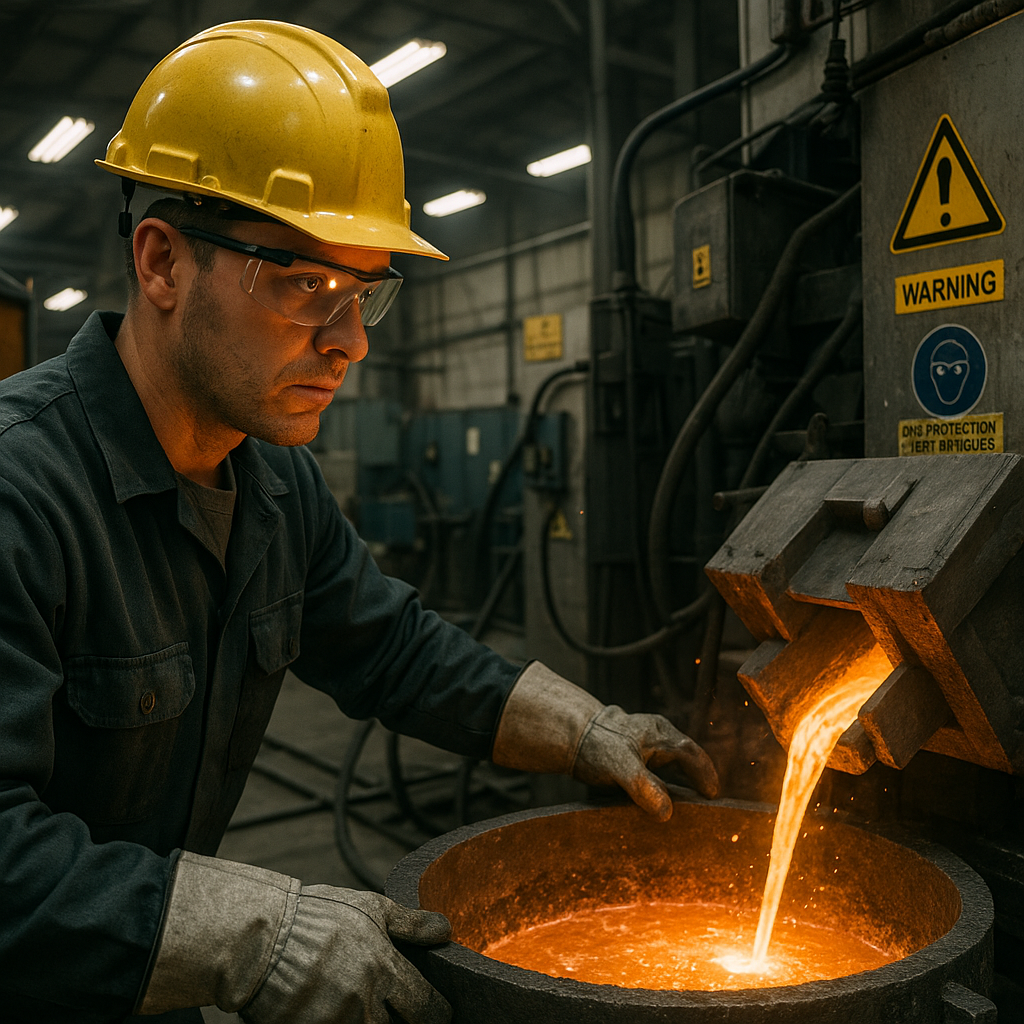
Metal reclamation facilities face numerous workplace hazards that require systematic management. Workers encounter daily risks from machinery, hazardous materials, and environmental conditions. These dangers threaten both employee health and operational efficiency.
Common Hazards in Metal Reclamation
Metal scrap recycling environments contain multiple safety concerns that demand attention. The recycling process generates various airborne contaminants, potentially causing acute and chronic health issues.
- Dust and Particulates: Cutting, grinding, and processing metals release fine particles that can penetrate deep into the lungs.
- Toxic Fumes: Welding, cutting, and melting operations produce metal fumes containing zinc, lead, and other harmful compounds.
- Chemical Exposure: Solvents, acids, and other chemicals used in metal processing can cause skin irritation, respiratory problems, and long-term organ damage.
- Excessive Noise: Heavy machinery and processing equipment generate noise levels that can permanently damage hearing without proper protection.
- Heat Stress: Furnaces and melting operations create extreme temperatures that pose risks of burns and heat-related illnesses.
- Machinery Hazards: Shredders, balers, cranes, and forklifts present dangers from moving parts, entanglement risks, and potential falls.
The combination of these hazards makes metal reclamation particularly challenging from a safety perspective. Without proper controls, workers face the risk of both immediate injuries and long-term health complications.
Essential Control Measures
Effective hazard management requires implementing multiple control strategies. The hierarchy of controls provides a framework for systematically addressing risks.
Engineering controls form the first line of defense in metal reclamation facilities. These physical modifications to equipment and workspaces reduce hazard exposure without relying on worker behavior.
- Local Exhaust Ventilation: Capture systems placed near dust and fume sources to remove contaminants before they reach workers’ breathing zones.
- General Area Ventilation: Facility-wide air exchange systems that dilute and remove airborne hazards.
- Noise Isolation: Enclosures, barriers, and dampening materials that reduce noise transmission from equipment.
- Machine Guarding: Physical barriers that prevent contact with moving parts of machinery.
Administrative controls supplement engineering measures by establishing safer work practices. These procedures minimize exposure duration and intensity.
Hazard | Control Measure |
---|---|
Dust and Particulates | Local exhaust ventilation |
Toxic Fumes | Masks and respirators |
Chemical Exposure | Chemical-resistant gloves and coveralls |
Excessive Noise | Earplugs or earmuffs |
Heat Stress | Proper hydration and rest breaks |
Machinery Hazards | Machine guarding and safety training |
Personal protective equipment serves as the final defense layer when other controls cannot fully eliminate hazards. Proper PPE selection depends on specific exposure risks.
- Respiratory Protection: Masks and respirators rated for specific contaminants present in the work area.
- Hearing Protection: Earplugs or earmuffs appropriate for the noise levels and duration of exposure.
- Eye and Face Protection: Safety glasses, goggles, or face shields that guard against flying particles and chemical splashes.
- Hand and Skin Protection: Chemical-resistant gloves, coveralls, and other clothing that prevent contact with hazardous substances.
Regular training ensures workers understand risks and properly implement safety measures. Comprehensive programs should cover hazard recognition, control measure usage, and emergency procedures.
What Are the Environmental and Economic Benefits of Metal Reclamation?
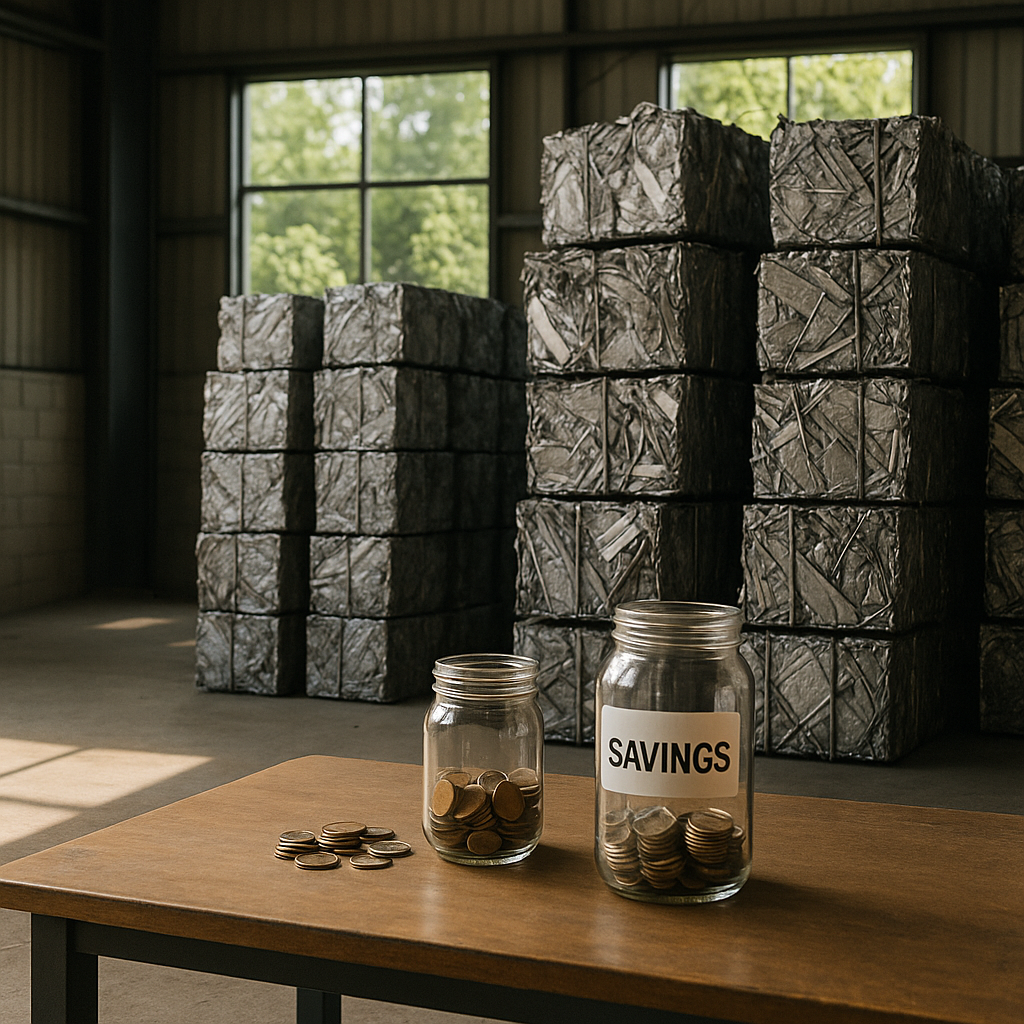
Metal reclamation offers a powerful mix of environmental and economic advantages, establishing it as a key component of sustainable resource management. The process transforms potential waste into valuable resources, delivering benefits from local communities to global ecosystems.
Environmental Benefits
A major environmental impact of metal reclamation is the reduction in mining activity. Traditional mining leads to significant habitat destruction, soil erosion, and water contamination. Recycling metals significantly decreases the need for these damaging practices.
Resource conservation is another critical benefit. Metal ores are finite and took millions of years to form. Recycling one ton of steel conserves about 2,500 pounds of iron ore, 1,400 pounds of coal, and 120 pounds of limestone, preserving natural resources for future generations.
Energy conservation is a major environmental advantage of metal reclamation. Processing recycled metals requires much less energy than mining and refining new ores. For example, recycling aluminum saves up to 95% of the energy needed to produce new aluminum from bauxite ore.
The reduction in greenhouse gas emissions further underscores the environmental benefits of metal reclamation. Lower energy consumption directly reduces carbon emissions, with studies showing that recycling one ton of aluminum can prevent up to nine tons of CO2 emissions.
Reducing landfill waste completes the picture. Metals do not biodegrade and can remain in landfills indefinitely, taking up valuable space and potentially leaching harmful substances. Metal reclamation diverts these materials from landfills, extending their lifespans and reducing pollution risks.
Economic Benefits
The economic benefits of metal reclamation are equally compelling. Job creation is a major advantage, with the recycling industry generating employment across a range of skill levels in collection, processing, manufacturing, and administrative roles. These jobs support local economies and provide sustainable livelihoods.
Cost-effectiveness makes metal reclamation attractive to businesses. Recycled metals usually cost less than new materials, lowering production expenses for manufacturers. These savings can be passed on to consumers or reinvested in business growth and innovation.
Revenue generation extends to those who collect and sell scrap metal. The value of reclaimed metals creates financial incentives that encourage recycling participation, driving environmental improvement.
Reducing import dependency is another economic benefit. Countries with robust metal reclamation systems can decrease reliance on imported raw materials, improving resource security and stabilizing supply chains.
Supporting the circular economy rounds out the economic picture. Metal reclamation keeps valuable resources in use, maximizing their economic value. Unlike many materials, metals can be recycled repeatedly without significant quality loss, allowing continuous reuse in manufacturing processes.
Environmental Benefit | Description |
Energy Conservation | Recycling metals like aluminum can save up to 95% of the energy required compared to producing metals from raw materials. |
Greenhouse Gas Reduction | Recycling processes significantly lower greenhouse gas emissions compared to mining and refining raw metals. |
Resource Conservation | Preserves natural resources like iron ore and coal by reducing the need for mining. |
Pollution Reduction | Decreases air and water pollution compared to traditional metal production methods. |
Landfill Waste Reduction | Reduces waste by preventing metals from ending up in landfills, thereby minimizing potential environmental hazards. |
The metal recycling industry generates billions annually while reducing environmental impact. This dual benefit makes metal reclamation a model for sustainable economic development, balancing profit with planetary health. As resource scarcity and environmental concerns increase, the advantages of metal reclamation are expected to grow even more significant.
Conclusion: The Future of Metal Reclamation
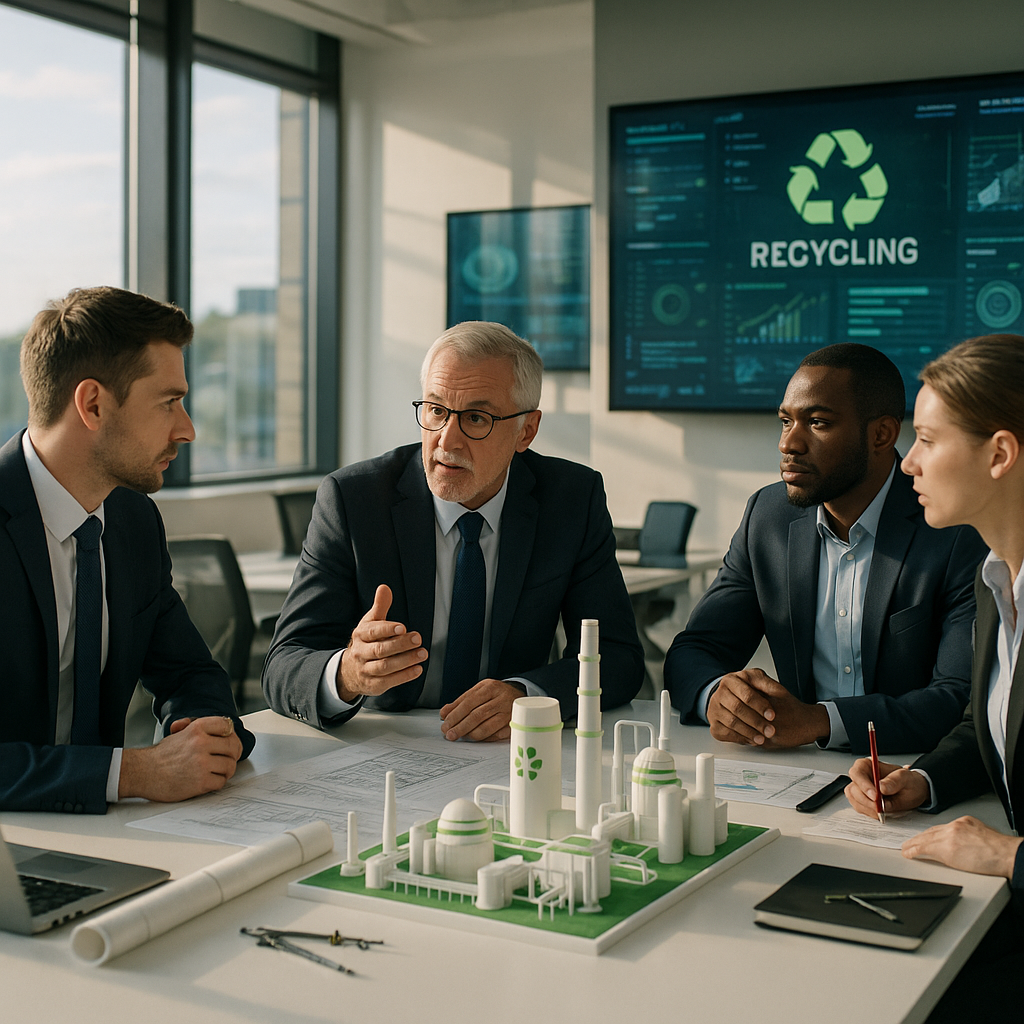
As natural resources become more scarce and environmental concerns grow globally, metal reclamation is set to become a cornerstone of the circular economy. Technologies transforming this sector—from AI-powered sorting systems to energy-efficient melting processes—are set to redefine how we recover and reuse valuable metals. These innovations will improve efficiency and reduce the environmental impact of reclamation operations.
The future of metal reclamation is promising. As international collaboration strengthens and consumer awareness increases, the industry will expand beyond traditional metals to recover more complex materials from electronics and composite products. This evolution is crucial for addressing resource scarcity while sustainably meeting the rising global demand for metals. For businesses and municipalities seeking expert guidance on implementing effective recycling solutions, contact Okon Recycling at 214-717-4083.