5901 Botham Jean Blvd, Dallas, TX 75215
Key Aluminum Recycling Regulations: Everything You Need to Know
May 20, 2025Aluminum recycling is a crucial global industry, offering significant economic and environmental benefits. However, recycling rates vary widely across regions due to differences in infrastructure, policy frameworks, and market development.
Europe leads in aluminum recycling, with many countries achieving rates above 75%. Germany excels with recycling rates for aluminum packaging reaching 90-95%. The United Kingdom, France, and Italy follow with rates between 70-85%, driven by the European Union’s strict environmental regulations and efficient collection systems.
North America also performs well, with the United States achieving 70-75% recycling rates for aluminum beverage cans. Canada surpasses this with rates of 80-85% for cans and other aluminum packaging, thanks to established programs and strong market demand from industries like automotive manufacturing.
The situation is different in the Asia-Pacific region. Japan is notable for its exceptional aluminum can recycling rates of 90-95%, reflecting a strong commitment to resource efficiency. In contrast, other countries in the region have more modest results. China, despite being a major aluminum producer and consumer, has recycling rates of 60-65% for aluminum packaging, though these are improving.
Challenges in Aluminum Recycling
Developing regions face challenges in aluminum recycling. Parts of Africa have some of the lowest formal recycling rates globally, between 20-30%. This is not due to lack of interest but rather limited infrastructure, fewer formal collection systems, and developing regulatory frameworks. The economic value of aluminum does encourage informal collection, yet these activities often go unrecorded in official statistics.
The reasons for these regional differences are complex. High-performing regions typically have stringent environmental regulations, well-established infrastructure for collection and processing, public awareness and participation in recycling programs, and strong market demand for recycled aluminum from domestic industries.
Market demand is crucial for driving recycling rates. Industries like automotive, construction, and packaging require recycled aluminum consistently. The energy savings from recycling aluminum—up to 95% compared to primary production—offer a significant economic incentive. Recycling a ton of aluminum saves about 9 tons of CO2 emissions, appealing to companies aiming to reduce their carbon footprint.
The recycling landscape is evolving. Regions with historically lower recycling rates are investing in infrastructure and implementing new policies to boost collection and processing capacity. Technological advances in sorting and processing are enhancing the quality of recycled aluminum, making it suitable for high-value applications.
The global aluminum recycling market was valued at around $112 billion in 2024 and is projected to reach $168 billion by 2033, growing at a compound annual rate of 4.62%. This growth underscores the increasing importance of aluminum recycling as both an environmental necessity and an economic opportunity.
What Are the Latest Technological Innovations in Aluminum Recycling?
Aluminum recycling has recently experienced a technological transformation. New equipment and methodologies have turned a labor-intensive process into a sophisticated and efficient operation.
X-Ray Transmission (XRT) Technology
XRT technology is a significant breakthrough in aluminum recycling. It detects differences in material density by how they absorb X-rays, enabling instant classification and sorting.
Modern XRT systems like the STEINERT XSS T EVO 5.0 include Multilayer Data Evaluation (MDE) capabilities. This innovation helps address challenging sorting tasks, such as separating magnesium from aluminum scrap, which previously required manual labor.
The benefits extend beyond labor savings. By identifying and removing free magnesium, recyclers can produce aluminum that meets strict alloy specifications with minimal need for magnesium-reducing chemicals in furnaces.
Laser-Induced Breakdown Spectroscopy (LIBS)
LIBS technology marks another advancement in aluminum recycling. It works by directing laser pulses at scrap material, creating a small plasma of excited atoms. As the plasma cools, it emits light with distinct spectral patterns unique to different elements.
This process allows recyclers to analyze the precise content of aluminum alloys in real-time. Modern LIBS sorting lines can process up to five metric tons of scrap per hour, identifying exact compositions of alloying elements like copper, silicon, and magnesium.
The practical impact is significant. LIBS technology can distinguish between alloy families that appear identical to the human eye. For example, automotive manufacturers produce scrap containing both 5xxx alloys (aluminum-magnesium) and 6xxx alloys (aluminum-silicon-magnesium). Without proper sorting, this mixed scrap gets downcycled.
With LIBS sorting, recyclers achieve over 95% purity for both alloy families. This means the material can be directly incorporated into melting furnaces to produce high-quality aluminum products rather than being downgraded.
Advanced Robotics and Automation
Robotic systems have transformed the physical handling aspects of aluminum recycling. Facilities now use advanced robotics for tasks ranging from initial scrap handling to final product movement.
These systems integrate with AI-driven controls that continuously optimize the recycling process. Robots equipped with multiple sensors can identify, grab, and sort mixed materials more efficiently than human workers.
The automation extends to monitoring and calibration. For instance, STEINERT’s Automatic X-ray Monitoring (AXM) feature provides automated calibration of X-ray sensors, ensuring plants maintain consistently high detection and sorting quality throughout the equipment’s operational life.
These robotic systems increase throughput while reducing operational costs. They also improve workplace safety by removing humans from hazardous environments involving heavy machinery and potential contaminants.
Data Analytics and AI Integration
Modern recycling facilities increasingly leverage artificial intelligence to enhance operations. AI systems analyze vast amounts of data from the recycling process to identify optimization opportunities.
These systems monitor parameters like material flow, energy consumption, and output quality in real-time. When deviations occur, the AI can make immediate adjustments or alert operators.
The integration of data analytics also enables predictive maintenance. Systems can identify potential equipment failures before they happen, reducing downtime and maintenance costs.
By optimizing the entire recycling supply chain from collection to processing, these technological advances reduce operational costs while boosting productivity.
Real-World Impact
The real-world impact of these technologies is already substantial. Since March 2023, more than 6,000 metric tons of LIBS-sorted automotive scrap have been processed at Constellium’s automotive plant in France.
In Indiana, Trinity Metals employs XRT and other advanced sorting technologies to convert mixed shredded scrap into marketable aluminum, red metals, magnesium, and precious metals.
AMAG Austria Metall AG pioneered the industrial use of STEINERT LIBS systems in 2019, allowing them to produce high-grade primary, cast, and rolled products from purified aluminum scrap streams.
Technology | Conveying Speed | Throughput | Precision | Energy Consumption | Design | Sorting Suitability |
---|---|---|---|---|---|---|
XRT | High (3-4 m/s) | High | Narrow & precise grain grid necessary | High | Large | Well suited for Zorba sorting; less suitable for production waste |
XRF | Lower (2-3 m/s) | Lower per working meter | Exact material analysis | Lower | Compact | Versatile; suitable for mixed shredder fractions and production waste |
These technological innovations are essential for achieving true circularity in aluminum recycling. As more end-of-life vehicles containing aluminum components enter the waste stream, technologies like LIBS will be crucial for recovering different alloy families separately and maintaining a closed-loop recycling system.
How Do Carbon Pricing and Emissions Regulations Impact Aluminum Recycling?
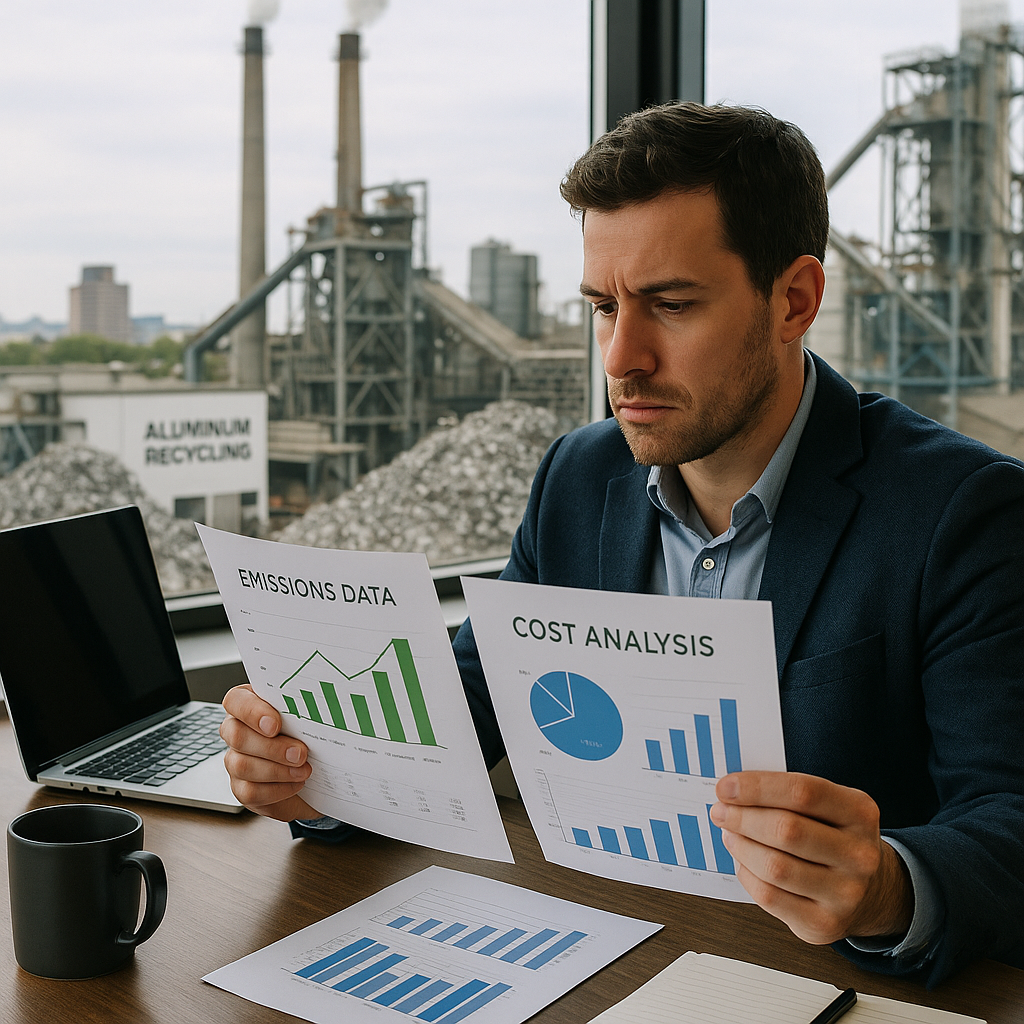
Carbon pricing mechanisms fundamentally change the economics of aluminum production. These policies assign a cost to carbon emissions, requiring producers to consider the environmental impact of their operations. When carbon taxes or cap-and-trade systems are implemented, energy-intensive primary aluminum production becomes much more expensive.
The financial impact is significant. Primary aluminum production emits about 8,515 kg of CO2 equivalent per 1,000 kg of aluminum. In contrast, recycled aluminum emits only 527 kg of CO2 equivalent for the same amount, representing a 94% reduction in carbon emissions through recycling.
As carbon prices rise, the cost gap between primary and recycled aluminum grows. This economic reality incentivizes manufacturers to use recycled materials. Companies facing carbon compliance costs find recycled aluminum increasingly attractive as a cost-saving measure.
Effects of Environmental Regulations on Industry Practices
Government regulations are transforming the aluminum industry. The European Union’s Green Deal targets and ban on CO2-emitting vehicles have increased demand for recycled aluminum. These policies aim to reduce greenhouse gas emissions while promoting circular economy principles.
Stricter emissions standards compel producers to innovate. Companies must adopt low-carbon technologies throughout their operations or face financial penalties and market disadvantages. This regulatory pressure has led to investments in more efficient recycling processes and renewable energy sources for recycling operations.
The global impact is becoming evident. According to the International Aluminium Institute, global emissions from aluminum production, including both primary metal and recycling, reached 10.04 tons in 2023. As regulations tighten, this figure is expected to decrease.
Balancing Supply and Demand Under Carbon Constraints
The World Bank highlights a critical challenge: balancing decarbonization with sufficient aluminum production capacity. Carbon pricing limits opportunities for new and existing aluminum smelters, potentially restricting production to existing facilities in countries like China and India.
One solution is to increase aluminum recycling rates. While aluminum is one of the most recycled materials with 42-70% recovery rates at end-of-life, the recycled content in new aluminum products averages only 34-36%. There is significant room for improvement.
Enhancing scrap collection systems and encouraging greater circularity can help meet growing demand while reducing emissions. The aluminum required for solar photovoltaic technologies demonstrates this urgency. Aluminum accounts for over 85% of solar PV components, making low-carbon aluminum essential for the clean energy transition.
Finding the right balance requires collaboration between governments and industry. Proactive policies must ensure aluminum remains available at competitive prices while minimizing environmental impact. Without such coordination, higher aluminum prices could increase the cost of critical low-carbon technologies.
What is the Future of Aluminum Recycling Regulations?
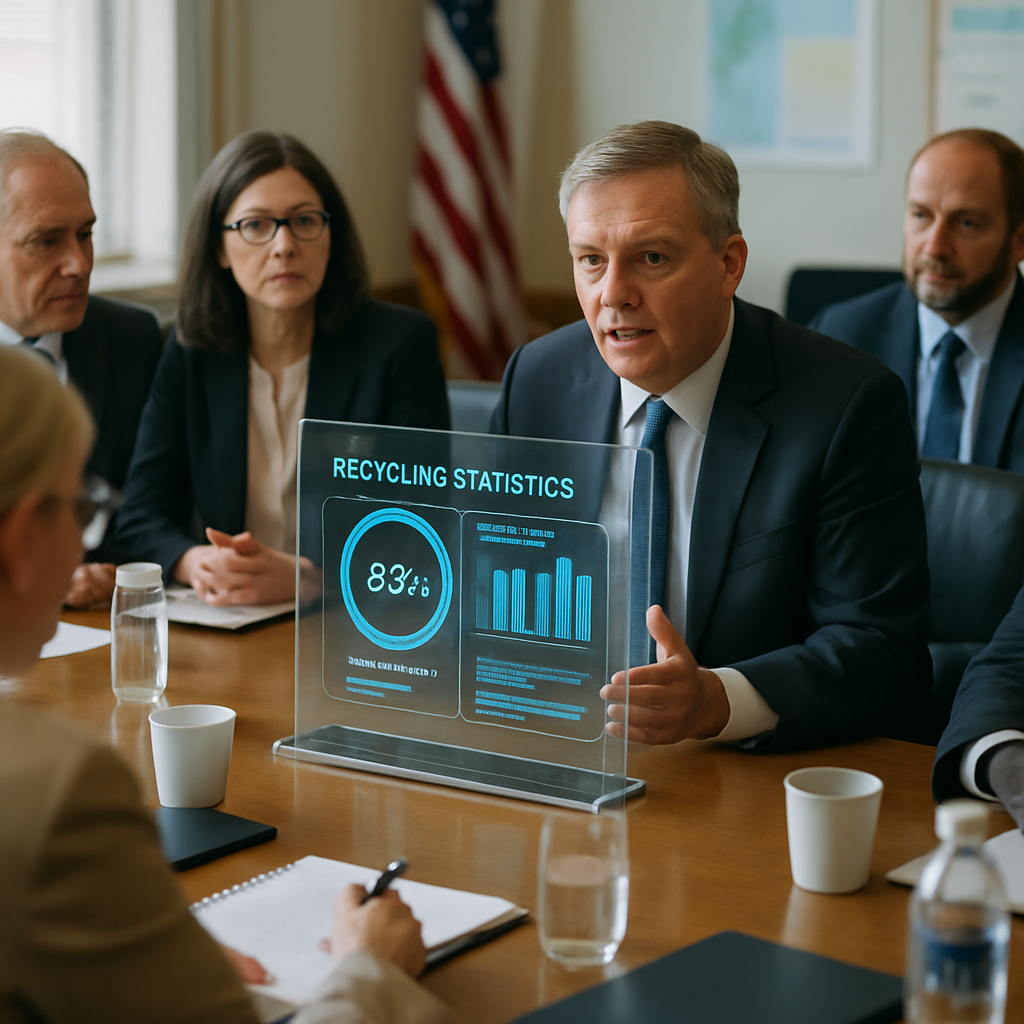
The aluminum recycling landscape is evolving rapidly, driven by international cooperation and harmonized standards. The global focus on circular economy principles is likely to accelerate the development of comprehensive regulatory frameworks. These frameworks aim to maximize resource efficiency and minimize the environmental impact of aluminum production and consumption.
Organizations like the International Aluminium Institute are leading efforts to develop global standards for responsible aluminum production and recycling. Their initiatives focus on creating transparent supply chains, standardizing measurement methodologies, and establishing industry-wide best practices. As these standards gain adoption, the aluminum industry will become more accountable, ensuring recycled aluminum consistently meets high environmental and quality requirements worldwide.
For businesses and municipalities involved in waste management, staying ahead of these regulatory developments is crucial. The aluminum industry will likely witness increased collaboration between governments, manufacturers, and recycling facilities to create more efficient collection systems and processing technologies. These partnerships will be essential in meeting ambitious recycling targets that future regulations may establish.
If you need guidance on navigating the evolving landscape of aluminum recycling regulations or want to optimize your recycling operations, contact Okon Recycling at 214-717-4083. Our expertise in sustainable recycling solutions can help you adapt to current regulations and prepare for future requirements.