5901 Botham Jean Blvd, Dallas, TX 75215
Exploring the Importance of Metal in Construction
July 1, 2025The skylines of today are built on metal. The construction industry consumes nearly 50% of all metal produced globally, establishing it as the backbone of our modern built environment. Metal provides critical structural integrity that few other materials can match.
From the framework of towering skyscrapers to the intricate details of residential buildings, metals offer an unparalleled combination of strength, durability, and adaptability. Their capacity to withstand extreme loads while maintaining relatively lightweight profiles has transformed what is possible in construction.
Beyond their functional benefits, metals bring remarkable versatility to building projects. Architects and engineers rely on various metal types to address specific challenges, whether creating load-bearing structures, weather-resistant exteriors, or efficient internal systems.
This article explores the most common construction metals, examining their distinctive properties and essential applications in the current building landscape.
What are the Main Types of Construction Metals?
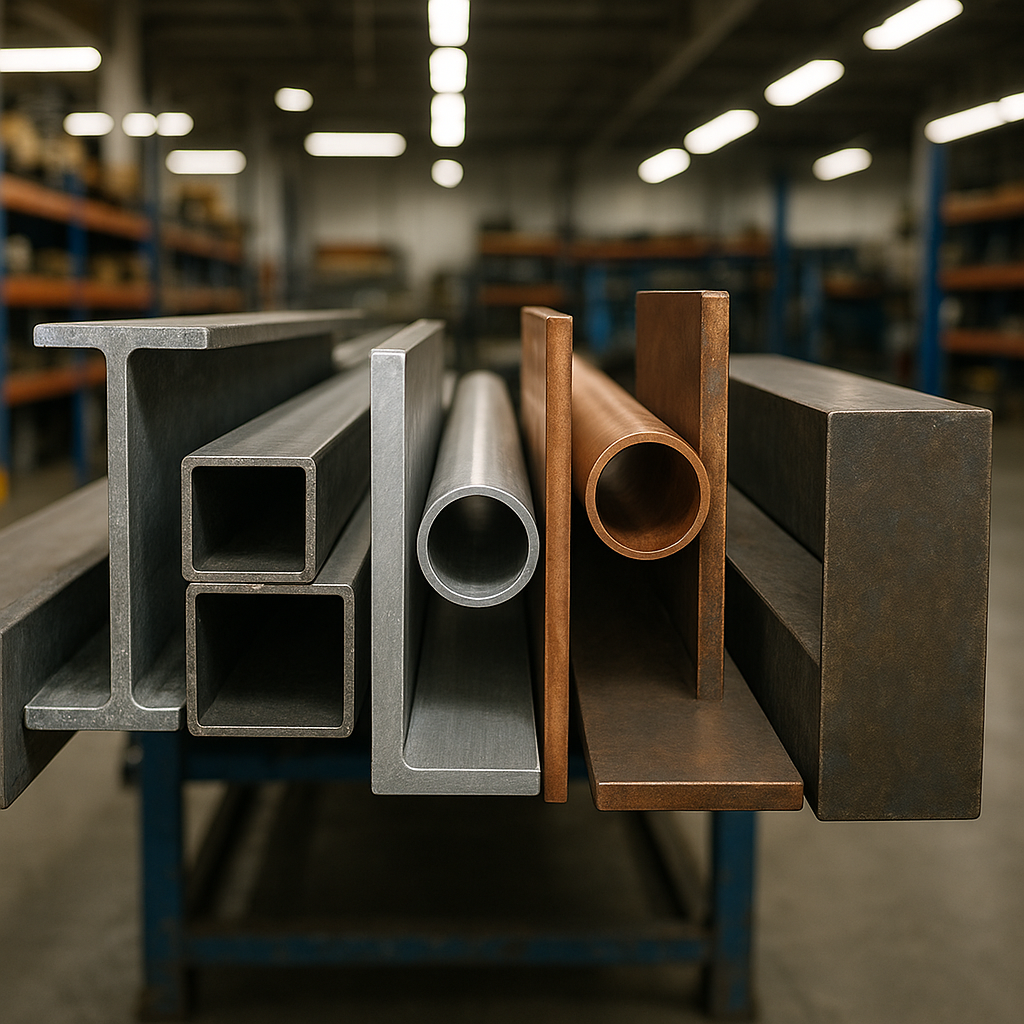
Carbon steel is fundamental to modern construction. This versatile metal’s varying carbon content affects its strength and workability. Low-carbon steel offers excellent formability for general structural components, medium-carbon steel enhances strength for load-bearing applications, and high-carbon steel provides superior hardness for specialized, wear-resistant uses.
Stainless steel is the premium choice for projects where corrosion resistance is crucial. This alloy contains chromium, forming a protective layer when exposed to oxygen, maintaining structural integrity in harsh environments, and offering an appealing appearance without additional finishing. It is available in various grades, including ferritic, martensitic, austenitic, duplex, and precipitation-hardening.
Aluminum has revolutionized modern construction with its excellent strength-to-weight ratio. This lightweight metal is about one-third as heavy as steel while offering significant structural integrity. Its natural corrosion resistance often removes the need for protective coatings. Aluminum’s high malleability enables the formation of complex shapes and prefabricated components, reducing construction time and costs.
Copper is valued in construction for its reliability. Its reddish-brown color and exceptional electrical conductivity make it ideal for wiring and electrical systems. Copper’s natural antimicrobial properties also bring benefits to healthcare settings. Over time, it develops a characteristic green patina serving as a protective layer against further corrosion.
Brass, a copper-based alloy with zinc, is notable for its construction applications. It combines copper’s corrosion resistance with improved machinability and strength. Available in various forms, such as flat strips, sheets, bars, and specialized shapes, brass is used in decorative elements, hardware, and plumbing fixtures.
Choosing construction metals depends on specific project requirements, such as structural loads, environmental exposure, aesthetic considerations, and budget constraints. Steel remains the most widely used due to its combination of strength, versatility, and cost-effectiveness. However, each metal offers unique advantages for specialized applications in modern building projects.
How is Steel Used in Construction?
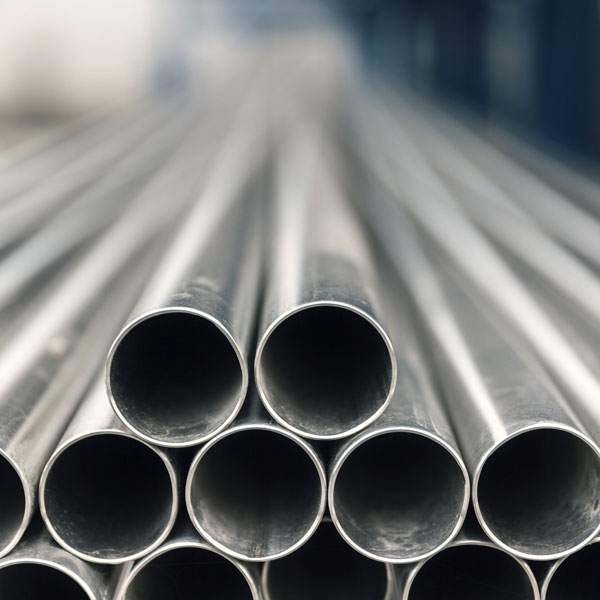
Steel is the backbone of modern construction, known for its excellent strength-to-weight ratio that makes it the preferred choice for builders worldwide. Its adaptability allows it to be molded into various forms while maintaining structural integrity across different applications.
Structural Framework Applications
Steel’s primary role in construction is forming the skeleton of buildings. I-beams, H-beams, and T-beams are crucial support structures bearing weight and providing stability to the entire building.
In high-rise buildings and skyscrapers, structural steel frames allow for greater height without excessive weight. The strength of steel enables wider spans between support columns, resulting in more usable interior space than other materials permit.
Commercial and industrial buildings heavily rely on steel frameworks due to their quick assembly time and ability to support heavy machinery. Warehouses, factories, and retail centers often feature exposed steel beams and columns as part of their architectural design.
Reinforcement in Concrete Structures
Reinforcing bars, colloquially known as rebar, represent another crucial application of steel in construction. These steel rods are embedded within concrete, providing tensile strength and reinforcing an otherwise brittle material.
In foundations, floors, and load-bearing walls, steel reinforcement prevents cracking and structural failure under stress. Combining concrete’s compression resistance with steel’s tensile strength creates a composite material ideal for structural applications.
Bridge construction particularly benefits from reinforced concrete, allowing structures to withstand heavy traffic loads, environmental stresses, and natural movement without compromising safety.
[[artifact_table]] Common Steel Components in Building Construction and Their Applications [[/artifact_table]]External and Finishing Applications
Beyond structural uses, steel is vital in building exteriors and finishing elements. Corrugated steel sheets and panels are durable, weather-resistant materials for roofing and siding in both residential and commercial buildings.
Steel framing systems for interior walls offer advantages over traditional wood framing, including fire resistance, dimensional stability, and resistance to pests and decay. These lightweight frames allow for easier installation of electrical and plumbing systems.
In decorative applications, stainless steel elements add both aesthetic appeal and functional value to buildings. Railings, facades, and architectural features made from steel blend strength with visual impact.
Infrastructure and Utilities
Steel pipes and tubes are essential components of building utility systems. From plumbing and gas lines to HVAC ducts, steel provides the strength and durability needed for these critical systems.
Temporary construction structures such as scaffolding and formwork depend on steel for their strength and reusability. These supporting elements ensure worker safety and facilitate access to all areas of a construction project.
Infrastructure projects like bridges, stadiums, and transportation hubs rely on structural steel to support massive loads while spanning great distances. The Golden Gate Bridge and modern sports arenas showcase steel’s capabilities on a grand scale.
What are the Benefits of Aluminum in Construction?
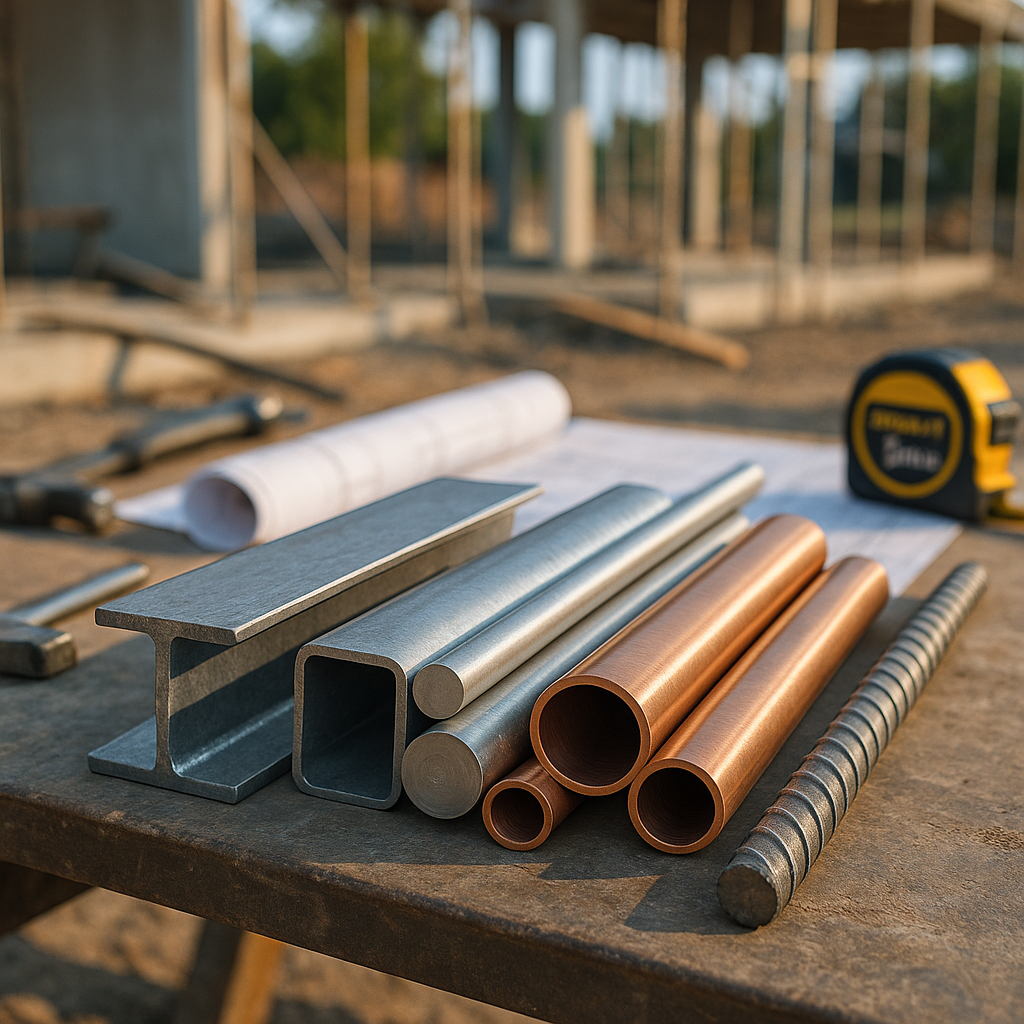
Aluminum offers exceptional value in construction due to its unique properties. Its impressive strength-to-weight ratio makes it ideal for structural applications without adding unnecessary weight. Construction teams can handle and install aluminum components more easily, reducing labor costs and installation time.
Aluminum’s natural corrosion resistance ensures extraordinary durability in harsh environments. Unlike other metals that deteriorate quickly when exposed to moisture and air, aluminum forms a protective oxide layer that shields it from environmental damage. This is especially beneficial in coastal areas where salt air would quickly degrade other materials.
Durability and Structural Advantages
One of aluminum’s most compelling benefits is its impressive lifespan. Aluminum building components can last 50-60 years with minimal maintenance, nearly doubling the lifespan of alternatives like PVC, which typically need replacement after 25-30 years.
The material’s inherent strength allows for slim, minimalist profiles in windows and doors without compromising structural integrity. Architects can design large openings with thinner frames, maximizing natural light and creating sleek aesthetic lines that bulkier materials can’t achieve.
Aluminum is also resilient in terms of fire safety. Classified as fire class A1, aluminum is non-combustible and doesn’t contribute to flame spread, releasing no toxic emissions when exposed to high temperatures. This enhances building safety standards.
Energy Efficiency and Thermal Performance
Modern aluminum window and door systems incorporate thermal break technology to significantly improve insulation. This technology uses polyamide barriers between interior and exterior aluminum sections to prevent temperature transfer, resulting in excellent thermal efficiency and consistent indoor temperatures.
Buildings with quality aluminum fenestration can substantially reduce heating and cooling costs. The thermal break technology prevents condensation on interior surfaces, eliminating conditions favorable to mold growth and improving indoor air quality.
Additionally, aluminum roofing’s reflective properties can reduce internal temperatures by up to 15 degrees, decreasing air conditioning demands during warm months and contributing to overall energy efficiency.
Design Flexibility and Aesthetics
Aluminum’s ductility makes it extremely versatile for architectural applications. It can be extruded into complex shapes and profiles to meet specific design requirements, allowing architects to create distinctive building elements without compromising structural performance.
The material accepts a broad range of finishes and colors through painting and anodizing processes. Building owners can select virtually any color or finish effect, with options for different treatments on interior and exterior surfaces of the same component, meeting diverse architectural styles.
For modern design aesthetics, aluminum enables minimalist frames and profiles that maximize glass area. Its strength supports curtain wall systems that create dramatic all-glass facades with minimal visible structure, bringing abundant natural light into buildings while maintaining structural integrity.
Sustainability Credentials
Aluminum is an environmentally responsible building material. It is 100% recyclable and can be reprocessed indefinitely without quality degradation, unlike plastic-based materials. Aluminum maintains its performance characteristics through unlimited recycling.
The recycling process for aluminum requires only 5% of the energy needed for primary production, significantly reducing the carbon footprint of aluminum products. The industry has established extensive recycling infrastructure that recovers approximately 75% of all aluminum ever produced.
Using aluminum in construction contributes to green building certifications like LEED, aligning with sustainability objectives due to its recyclability, durability, and energy-efficient performance.
Aluminum components require minimal maintenance compared to alternatives like wood or steel. Simple cleaning with water and mild detergent usually suffices to maintain appearance and performance, resulting in reduced lifetime costs for building owners and facilities managers.
How Do Builders Choose the Right Metal for Projects?
Selecting the right metal for a construction project involves more than just aesthetics. It requires careful analysis of several factors to ensure the material will perform reliably throughout the structure’s lifetime while staying within budget constraints.
Builders assess each metal’s unique properties against the specific demands of their project. A thorough approach to metal selection can make the difference between a lasting structure and one that needs frequent repairs or early replacement.
Assessing Structural Requirements
The primary consideration for any construction project is whether the chosen metal can support the required loads. Steel, with its tensile strength of up to 250 MPa, is preferred for heavy-duty applications like support beams in commercial buildings.
Aluminum, though less strong than steel, offers an excellent strength-to-weight ratio, making it ideal for projects where weight reduction is crucial, such as in high-rise buildings where the overall mass impacts foundation requirements.
For specific applications, builders also evaluate specialized properties. Copper’s conductivity is essential for electrical systems, while titanium’s remarkable strength-to-weight ratio is suited for aerospace components and specialized architectural features.
Evaluating Environmental Conditions
Environmental factors significantly influence metal selection. Exposure to moisture, chemicals, and temperature fluctuations can strongly affect a metal’s performance and longevity.
In coastal areas, metals face continuous exposure to salt spray, accelerating corrosion. Stainless steel and aluminum form protective oxide layers that resist this corrosion, making them preferred choices for oceanfront structures.
For industrial environments where chemical exposure is common, metals with appropriate resistance properties are crucial. Stainless steel containing molybdenum offers enhanced protection against chemical damage, while titanium provides exceptional resistance to most industrial chemicals.
Temperature variations also impact metal performance. In regions with extreme heat or cold, builders select metals that maintain structural integrity across temperature ranges. Steel performs well in high heat, while aluminum retains its properties in freezing conditions.
Balancing Cost and Availability
Budget considerations often influence the final decision in metal selection. Steel costs around $700-$800 per ton, making it economical for most structural applications. Aluminum, at approximately $1,900 per ton, represents a higher investment but may offer long-term savings through reduced maintenance.
Specialty metals like titanium ($8,000+ per ton) or copper ($4+ per pound) require careful cost-benefit analysis. Their premium prices are justified when their specific properties are essential to project success.
Availability also factors into decision-making. Steel’s wide availability makes it accessible for most projects with reasonable lead times. Less common metals may require longer procurement periods, potentially affecting construction schedules.
Considering Aesthetic Requirements
The visual appeal of exposed metals influences architectural choices. Stainless steel offers a modern, clean aesthetic popular in contemporary designs. Its ability to take a high polish makes it suitable for decorative elements and visible structural components.
Copper develops a distinctive green patina over time, creating a living finish that evolves with age. This property makes it popular for roofing, flashing, and architectural accents in both traditional and modern designs.
Aluminum can be anodized in various colors or given different surface treatments, offering versatility for designers seeking specific visual effects. Its lightweight nature also allows for more complex forms that might be impractical with heavier metals.
Maintenance Requirements
Long-term maintenance costs impact metal selection. Stainless steel requires minimal maintenance beyond occasional cleaning, making it cost-effective over the structure’s lifetime despite higher initial costs.
Carbon steel needs regular painting or coating to prevent rust, adding to its lifetime expense. However, its lower initial price may still make it economical for certain applications, especially when protected from moisture.
Aluminum’s natural corrosion resistance means minimal maintenance in most environments, contributing to its popularity where access for maintenance is difficult or costly.
In manufacturing facilities where frequent equipment cleaning is necessary, stainless steel’s resistance to cleaning chemicals and its non-porous surface make it ideal despite higher upfront costs.
Real-World Selection Examples
Commercial skyscrapers typically use structural steel for their primary frameworks due to its strength, availability, and cost-effectiveness. The steel frame provides the necessary support for vertical loads and wind resistance, while aluminum is often selected for the curtain wall systems that form the building envelope.
In bridge construction, weathering steel (such as COR-TEN) has gained popularity since it forms a stable rust-like appearance that protects against further corrosion, eliminating the need for painting while providing necessary structural strength.
For coastal residential projects, builders often choose aluminum for window frames and exterior components due to its corrosion resistance. Stainless steel fasteners are used throughout to prevent galvanic corrosion that occurs when dissimilar metals contact moisture.
Healthcare facilities frequently use copper for touch surfaces like door handles and railings due to its natural antimicrobial properties. This selection represents a case where a specific metal property justifies higher material costs through improved functionality.
Conclusion: The Future of Metals in Construction
The metal construction industry is at a pivotal moment. Smart technology now allows buildings to manage lighting, HVAC, security, and energy usage from central interfaces. Sustainability has become a key driver of innovation, with green construction practices gaining momentum. The move toward eco-friendly structures, energy efficiency, and material reuse shows how metal construction is adapting to environmental demands.
For businesses aiming to embrace these trends and create efficient, technologically advanced, environmentally responsible structures, expert guidance is essential. Contact Okon Recycling at 214-717-4083 for sustainable metal recycling solutions that support your construction projects while contributing to a circular economy.