5901 Botham Jean Blvd, Dallas, TX 75215
The Growing Importance of Copper Recycling for Electronics Waste
May 7, 2025Only 33% of post-consumer copper was recycled in the USA in 2023. This statistic highlights an urgent challenge as global demand for copper in technology continues to surge. Electronics contain significantly higher percentages of copper than what is currently being mined, yet much of this valuable resource ends up in landfills.
Copper serves as the backbone of modern electronic infrastructure. Its exceptional electrical conductivity makes it indispensable in everything from circuit boards and wiring to connectors and components. As our reliance on technology grows, so does our need for this versatile metal.
The recovery of copper from electronic waste represents both an environmental imperative and an economic opportunity. E-waste is one of the fastest-growing waste streams worldwide, and efficient copper recycling can significantly reduce mining impacts while meeting market demands. By transforming what was once considered waste into a valuable resource, we can move toward a more sustainable and circular approach to managing electronic materials.
Why is Copper Recycling from E-Waste Crucial?
As global copper ore grades decline, recycling this valuable metal from electronic waste has become an economic necessity. Modern mining operations must process significantly more earth to extract the same amount of copper compared to decades ago. Electronic devices, meanwhile, often contain higher copper concentrations than current mining sites.
The energy implications are substantial. Mining and processing raw copper ore requires enormous amounts of energy. Recycling copper from e-waste uses about 85% less energy than extracting it from virgin sources, resulting in lower production costs and reduced carbon emissions—a key consideration as industries worldwide work toward sustainability goals.
The growing technology sector continues to drive copper demand to new heights. Copper plays an essential role in renewable energy systems, electric vehicles, and smart infrastructure. A single wind turbine can contain up to a ton of copper, and electric vehicles require up to four times more copper than conventional vehicles. This increasing demand cannot be sustainably met through mining alone.
Environmental Protection Through E-Waste Recycling
Copper mining operations cause significant environmental harm. The process creates tailings and waste rock that can leach harmful chemicals into soil and water. Mining activities often lead to deforestation, habitat destruction, and landscape alterations that permanently damage ecosystems.
Recycling copper from electronic waste eliminates these impacts while addressing the growing e-waste crisis. According to the Global E-waste Statistics Partnership, the world generated 53.6 million metric tons of electronic waste in 2019, but only 17.4% was properly collected and recycled. This represents an enormous untapped resource of copper and other valuable materials.
The environmental benefits extend beyond avoiding mining impacts. Processing recycled copper produces significantly fewer emissions than primary production, helping combat climate change while preventing soil and water pollution associated with improper e-waste disposal.
Resource Conservation for Future Generations
Copper reserves are finite. By implementing robust recycling systems, we extend the availability of this essential resource for future generations. This approach is particularly important given copper’s role in green technologies that will help address climate challenges.
Copper is uniquely suited for recycling because it can be processed repeatedly without degradation in quality. Recycled copper maintains the same electrical conductivity and physical properties as newly mined copper. This “infinite recyclability” makes copper a cornerstone material in the circular economy.
Process | Energy Requirement | CO₂ Emissions |
---|---|---|
Mining Copper | 100% | 3.2 tons per ton of copper |
Recycling Copper | 15% | Significantly lower |
Economic Advantages
The economic case for recycling copper from e-waste is compelling. Beyond energy savings, recycling operations typically require less capital investment than mining operations. They can also be located closer to urban centers where most e-waste is generated, reducing transportation costs and associated emissions.
For businesses, recycling copper from electronic waste can transform a waste management challenge into a revenue opportunity. As ore grades decline and mining costs increase, the value of recovered copper will likely continue to rise. Investing in copper recovery technologies positions companies to benefit from this trend while contributing to sustainability goals.
The recycling process also drives innovation in material recovery technologies. These advances have applications beyond copper recycling, benefiting the broader waste management and resource recovery sectors. The economic ripple effects extend to job creation in collection, processing, and technology development.
What are the Challenges in Copper Recycling from Electronics?
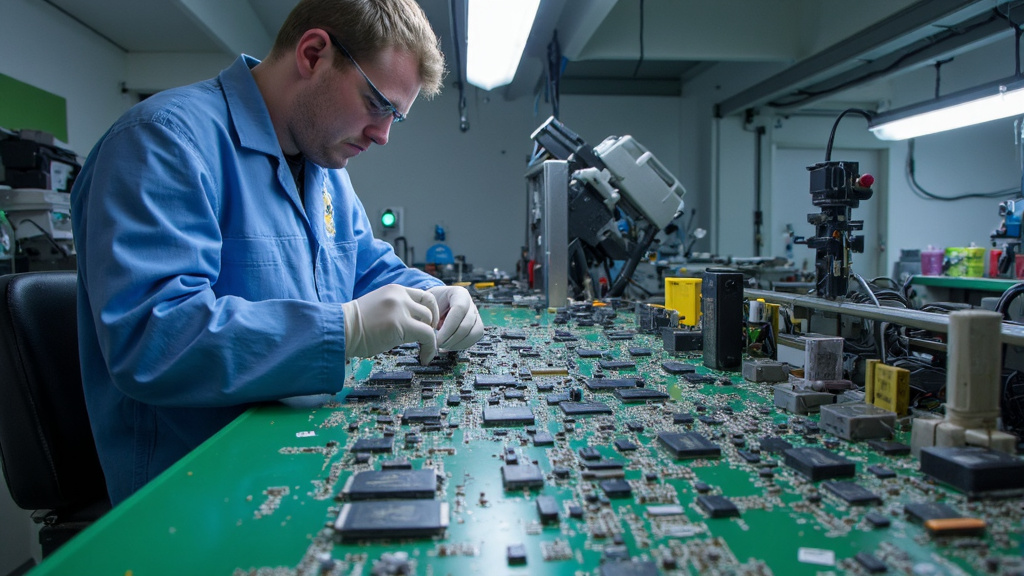
Recycling copper from electronic waste presents significant hurdles for the waste management industry. The complexity of modern devices makes copper recovery technically demanding. Multiple components are tightly integrated, requiring specialized processes to separate copper from other materials.
Modern electronics contain copper in various forms – from wiring and circuit boards to connectors and micro-components. Each form requires different extraction approaches. For instance, copper in circuit boards is intertwined with fiberglass, resins, and other metals, making separation energy-intensive.
Inadequate Collection Infrastructure
One of the most pressing challenges is the lack of comprehensive collection systems. Unlike regular waste streams, e-waste requires specialized handling networks. Many regions lack convenient drop-off locations, making it easier for consumers to discard electronics with regular trash.
Current infrastructure gaps are particularly evident in rural areas where transportation costs make collection economically prohibitive. Urban centers often have better systems, but even these frequently suffer from inadequate capacity to handle increasing volumes of discarded devices.
Economic and Process Challenges
The economics of copper recycling from electronics can be challenging. Virgin copper mining operations benefit from economies of scale that many recycling operations cannot match. Extraction of copper from e-waste requires significant energy input, with some processes using up to 85% less energy than mining – yet still representing a substantial cost.
Processing costs are further complicated by market fluctuations. When copper prices drop, the economic incentive for recycling diminishes. This price volatility makes long-term investment in recycling infrastructure risky for businesses.
Consumer Behavior and Incentives
Consumer participation remains a critical bottleneck. Many people store unused electronics indefinitely rather than recycling them. Studies show the average household has several unused electronic devices, creating a substantial “hibernating” stock of potentially recoverable copper.
The lack of financial incentives for consumers contributes to this problem. While some programs offer small payments for returned devices, these rarely reflect the true value of recoverable materials. Education about the environmental benefits of recycling has increased awareness, but behavioral change requires stronger incentives.
Device Type | Copper Content (%) | Recovery Challenges |
---|---|---|
Smartphones | 27.83 ± 13.87 | Complexity of materials, collection challenges |
Cellphones | 36.25 ± 6.52 | Complexity of separation |
Printed Circuit Boards (PCB) | 15.86 ± 9.86 | Separation from fiberglass, resins, and other metals |
Waste Printed Circuit Boards (WPCB) | 20 | High impurity levels, energy-intensive extraction |
Scrap | 75 | Easier to recover due to higher concentration |
Technical Complexities with Mixed Materials
The presence of other materials in electronic devices complicates copper recycling. Hazardous substances like lead, mercury, and flame retardants require careful handling during processing. Their removal adds steps and costs to the recycling process.
Ironically, the presence of precious metals like gold, silver, and palladium actually improves the economics of e-waste recycling. These metals are often recovered first, with copper as a secondary product. In WPCB (waste printed circuit boards), copper represents only about 20% of the value, while precious metals account for up to 95%.
Plastics in electronics pose another challenge. When burned during smelting processes, they generate harmful emissions requiring expensive treatment systems. Some advanced facilities have invested millions in gas treatment technology to address this issue.
Technological Solutions Emerging
Despite these challenges, technological innovations are improving copper recovery rates. Advanced pyrometallurgical processes can now achieve copper recovery rates of 94-97%, substantially higher than earlier methods that managed only 79-83% recovery.
Hydrogen-based reduction methods show promise for reducing the carbon footprint of copper recycling. These approaches can achieve a 71-97% lower carbon footprint compared to primary extraction, particularly when powered by renewable energy sources.
How Can Copper Recycling from E-Waste be Improved?
Enhancing copper recycling from electronic waste requires innovative strategies across multiple areas. The rapid growth of e-waste—now the world’s fastest-growing waste stream at 62 million tons annually—presents both challenges and opportunities for recovering valuable metals like copper.
Advanced Sorting and Extraction Technologies
Current copper extraction methods from e-waste include mechanical processing, pyrometallurgical, and hydrometallurgical techniques, each with varying efficiency levels. Emerging technologies show promise in improving recovery rates.
Innovations in automated sorting systems using artificial intelligence can identify and separate copper-rich components more accurately than traditional methods. These systems reduce contamination and improve the quality of recovered materials.
New leaching processes using environmentally friendly reagents represent another advancement. Research shows glycine-based leaching can effectively extract copper from printed circuit boards while reducing environmental impact compared to conventional acid-based methods.
Robust Collection Systems and Consumer Incentives
Collection remains a primary bottleneck in e-waste recycling. Implementing convenient collection points in urban centers, retail locations, and community spaces significantly increases participation rates.
Consumer incentive programs have proven effective in boosting collection volumes. Refund or deposit systems for electronic devices create economic motivation for returning end-of-life products. These programs work particularly well when paired with awareness campaigns about the value of recycling.
The European Union has demonstrated success through its End-of-Life Vehicles Directive, which mandates 95% recovery and 85% recycling of materials, including copper. Similar frameworks could be adapted specifically for electronic waste.
Policy Implementation and Regulatory Frameworks
Effective policies create the foundation for successful recycling systems. Regulatory approaches should include extended producer responsibility (EPR) programs that require manufacturers to manage their products throughout their lifecycle.
Standardized labeling requirements for metal content in electronics would facilitate identification and proper recycling. Such standards could help recyclers quickly identify copper-rich components.
Cross-border regulations also need attention. Current policy changes have disrupted the global copper scrap trade, with China’s solid waste import ban in 2017 significantly impacting how low-grade scrap sources are processed. Regional and domestic recycling capacity must increase to compensate.
Design for Recycling
The most effective improvements begin at the product design stage. Electronics designed with disassembly in mind facilitate easier separation of valuable materials. This approach requires collaboration between manufacturers, designers, and recycling specialists.
Using standardized components and connection methods across products simplifies the recycling process. When fasteners, connectors, and assemblies follow consistent patterns, automated disassembly becomes more efficient.
Reducing the use of composite materials that are difficult to separate also improves recyclability. Clear material identification and minimizing the variety of materials used can significantly enhance copper recovery rates.
Multi-Stakeholder Collaboration
Successful improvements in copper recycling require cooperation across the entire value chain. The China Resource Recycling Group exemplifies this approach, bringing together government agencies and industry partners to enhance nationwide recycling efforts for metals from various sources, including e-waste.
Academic-industry partnerships drive innovation through research into more efficient extraction methods. These collaborations lead to practical applications of new technologies at commercial scales.
International knowledge sharing is equally important. MIT researchers have demonstrated that with advanced processing technologies and improved recycling rates, approximately two-thirds of end-of-life copper scrap could be recovered by 2040—potentially recovering over 6 million tons annually.
Method | Advantages | Disadvantages |
---|---|---|
Precipitation | Eliminates need for organic solvents, reduced carbon emissions, high copper recovery | Requires engineered solutions for scalability |
Solvent Extraction | High selectivity for copper, facilitates ligand reuse | Uses large quantities of organic solvents, higher emissions |
The economic benefits of improved copper recycling are substantial. Recycled copper requires up to 85% less energy than mining and extraction of virgin materials. This energy saving translates to reduced greenhouse gas emissions and lower production costs, making recycling increasingly competitive as energy prices rise.
To achieve the projected doubling of global end-of-life copper recycling rates from the current 32% to 66%, these improvement strategies must be implemented systematically. The potential rewards—both environmental and economic—make this transition not just desirable but essential for meeting the growing demand for copper in our increasingly electrified world.
Conclusion: The Future of Copper Recycling from Electronics Waste
Copper recycling from electronics waste offers significant opportunities in our resource-constrained world. With copper reserves potentially depleting within 50-60 years at current consumption rates, e-waste recycling provides a sustainable path to meet growing demand. The environmental benefits are substantial—recycling copper requires just 15% of the energy needed for mining and reduces carbon emissions by up to 85%.
The economic case is compelling as well. The recycling industry creates jobs in the circular economy, stabilizes prices for manufacturers, and ensures the availability of this critical metal for future technologies. As e-waste volumes increase and primary copper ore grades decline, developing more efficient collection systems and recycling technologies is essential for creating a truly circular copper economy that supports both environmental sustainability and economic growth.
For comprehensive recycling solutions that maximize resource recovery and minimize environmental impact, contact Okon Recycling at 214-717-4083.