5901 Botham Jean Blvd, Dallas, TX 75215
What is Metal Recovery from Chillers?
May 9, 2025Outdated industrial cooling systems are rich sources of valuable metals. When large chillers reach the end of their operational life, they still contain significant amounts of copper, steel, and aluminum that can be reclaimed and reused. This process is known as metal recovery from chillers.
Metal recovery from chillers involves systematically dismantling these industrial cooling units and using specialized techniques to extract valuable metals. The process employs methods such as pyrometallurgy (heat-based extraction), hydrometallurgy (water-based solutions), and electrometallurgy (electricity-driven separation) to recover metals with precision and efficiency.
As industrial waste continues to pose environmental challenges worldwide, metal recovery from chillers offers a practical solution with dual benefits. It diverts bulky equipment from landfills while conserving natural resources by reintroducing recovered metals into the manufacturing cycle. This recycling approach aligns with circular economy principles that increasingly guide modern industrial practices.
What Are the Key Techniques in Metal Recovery from Chillers?
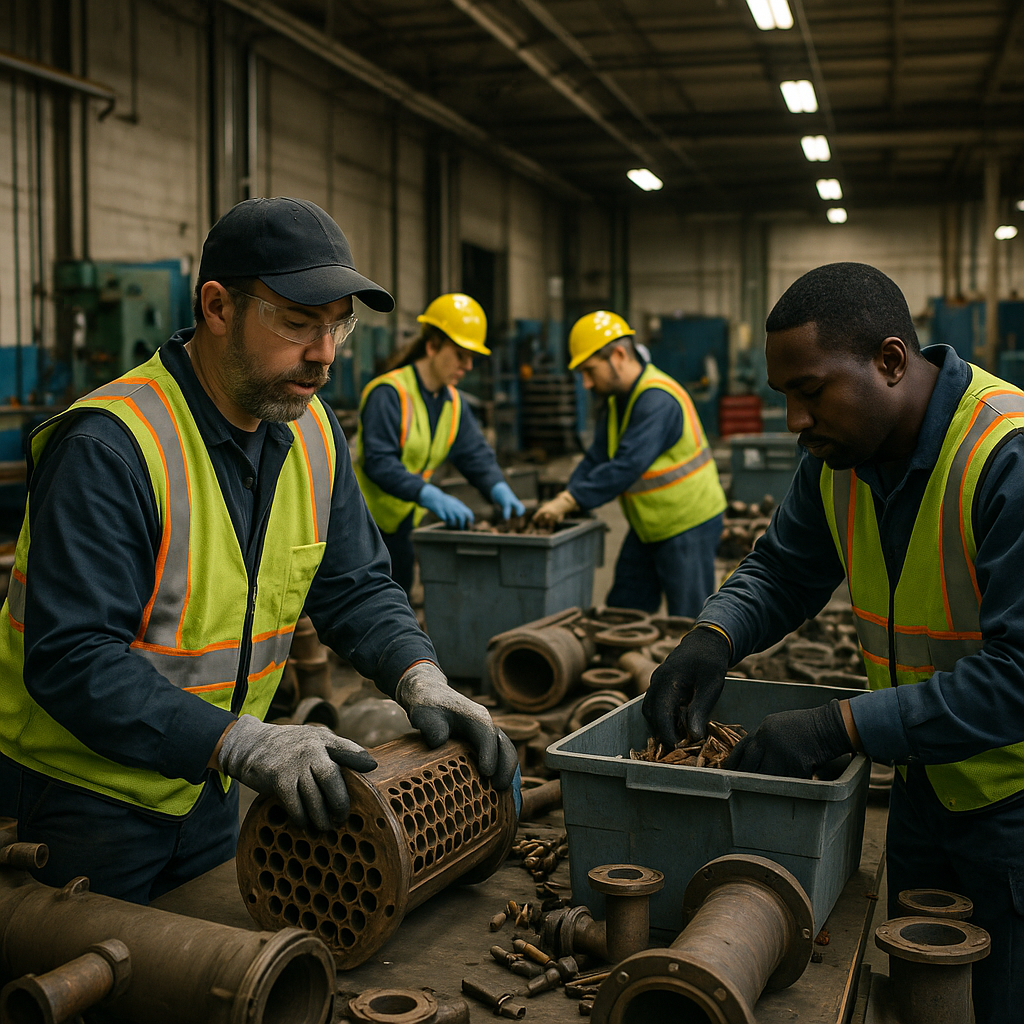
Extracting valuable metals from used chillers requires specialized techniques. Three primary methods have proven most effective in reclaiming these resources. Each approach offers distinct advantages in transforming what was once considered waste into valuable raw materials.
Pyrometallurgy: The Power of Heat
Pyrometallurgy harnesses extreme temperatures to separate metals from chillers. This method uses precise temperature control to drive chemical reactions. Different metals separate based on their unique properties when exposed to heat.
Modern pyrometallurgical systems employ sophisticated sensors for temperature management. This precision maximizes metal recovery while minimizing energy use. Specially formulated chemical additives enhance the separation process.
The results are impressive. Some facilities now achieve copper recovery rates of 98% using advanced pyrometallurgical techniques, a significant improvement over traditional methods that typically reached only 70% recovery rates.
Hydrometallurgy: The Chemical Solution
Hydrometallurgy offers an environmentally friendly approach using aqueous solutions. The process involves three key steps: leaching, solution concentration, and metal recovery. This method produces fewer emissions than high-temperature alternatives.
The leaching phase dissolves targeted metals using acidic or basic solutions. Different metals require specific leaching agents. Copper extraction often uses sulfuric acid solutions.
Solution concentration follows, using techniques like solvent extraction or ion exchange. These methods act as fine-tuned filters to isolate valuable metals. The final recovery step transforms metal ions back into solid, usable forms.
Electrometallurgy: Precision Through Electricity
Electrometallurgy applies electrical current to extract and refine metals to exceptional purity. This technique works through electrolytic cells and is particularly effective for metals like copper and nickel.
The process offers remarkable energy efficiency compared to traditional methods. Metallurgists can fine-tune electrical currents to optimize extraction, minimizing waste and energy consumption.
Recent innovations in electrolytic cell design have expanded capabilities. Improved electrode materials allow higher current densities and faster extraction. Automated monitoring systems adjust parameters in real-time to maintain quality.
Electrometallurgy can process lower-grade materials efficiently, extending the range of recyclable sources. The technique delivers high-purity metals with minimal environmental impact.
Technique | Energy Intensity | Temperature Requirement | Environmental Impact | Metal Recovery Process | Selective Metal Recovery |
---|---|---|---|---|---|
Hydrometallurgy | Lower | Lower | Less emissions | Aqueous solutions | More selective |
Pyrometallurgy | Higher | High | High emissions | High heat | Less selective |
Electrometallurgy | Lower | Lower | Fewer emissions | Electrolysis | Highly selective |
Each method brings unique strengths to metal recovery. Pyrometallurgy offers high-temperature efficiency for bulk processing. Hydrometallurgy provides environmentally friendly chemical extraction. Electrometallurgy delivers precision and exceptional purity.
The recycling industry continues to refine these techniques. Innovations in temperature control, chemical formulations, and electrode materials push recovery rates higher. What was once lost in discarded chillers now returns to the production cycle as valuable raw material.
How Does Pyrometallurgy Enhance Metal Recovery from Chillers?
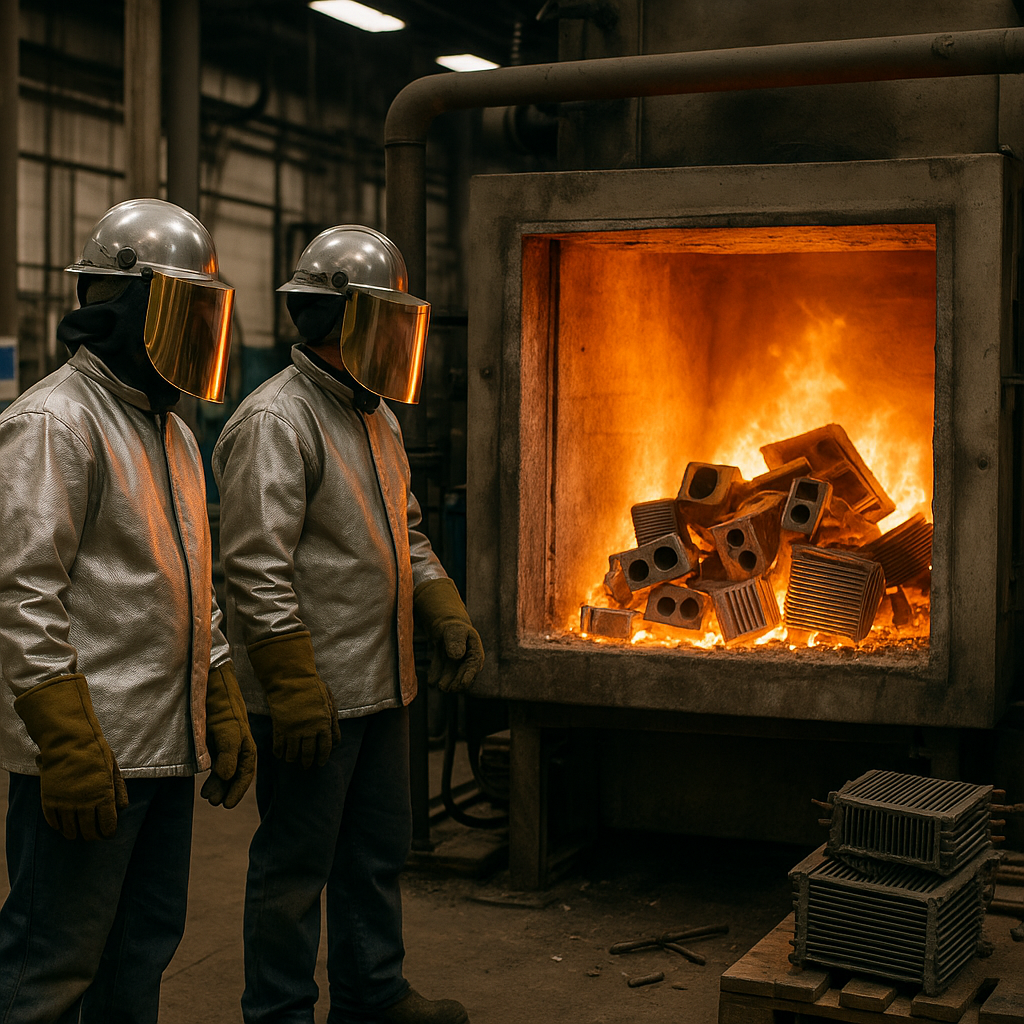
Pyrometallurgical techniques have transformed the chiller recycling industry by efficiently recovering valuable metals at high temperatures. These methods use reactions ranging from 800°C to 1200°C to separate and recover materials from end-of-life chiller units. The process involves chemical transformations that convert metallic impurities into high-quality materials.
Smelting, a core pyrometallurgical process, has evolved significantly with modern innovations. Today, smelting involves complex reactions where metals separate based on unique properties, allowing recyclers to isolate copper, aluminum, and other components precisely.
Temperature Management: The Key to Enhanced Recovery
Technological advancements have improved temperature control in pyrometallurgical systems. Modern furnaces use sensors and digital controls to fine-tune temperatures precisely, maximizing metal recovery rates.
Maintaining optimal reaction conditions ensures metals separate cleanly. When temperatures fluctuate, recovery efficiency drops. Latest equipment maintains temperature consistency, resulting in higher metal yields.
Improved temperature management has also reduced energy consumption. Newer systems require less fuel, cutting costs and environmental impact. Some facilities report energy savings of up to 30% compared to older methods.
Chemical Innovation Driving Higher Recovery Rates
Beyond temperature control, chemical innovations enhance pyrometallurgical efficiency. Researchers have developed flux materials that improve metal separation during smelting.
These innovations lower the melting point of metal compounds, allowing efficient separation at reduced temperatures. Custom flux formulations for specific chiller components boost recovery rates for metals like copper and aluminum.
The combination of precise temperature control and advanced chemical processes has expanded possibilities in metal recovery, making previously difficult extractions economical and efficient.
Real-World Impact: Dramatic Improvements in Recovery Rates
Recycling facilities using modern pyrometallurgical systems illustrate these advancements. A mid-sized operation in the Midwest improved copper recovery rates from 70% to 98% after upgrading.
The facility also reported a 30% decrease in energy consumption per ton, reducing costs and environmental impact. Higher recovery rates and lower energy use benefit both business and sustainability.
Environmental Benefits of Advanced Pyrometallurgy
Modern pyrometallurgical techniques offer environmental advantages beyond energy efficiency. Optimized reaction conditions reduce harmful emissions and waste byproducts, minimizing hazardous compound formation.
Higher recovery rates mean more metals are reclaimed from waste streams, reducing landfill volumes. Efficient recycling reduces the need for primary mining operations, lessening environmental footprints.
Method | Recovery Rate Before | Recovery Rate After |
---|---|---|
Pyrometallurgy | 70% | 98% |
Future Directions in Pyrometallurgical Innovation
Researchers are developing more advanced pyrometallurgical techniques. Emerging technologies like plasma-enhanced smelting promise higher recovery rates and reduced energy use.
These innovations could enable efficient extraction of critical materials. As demand for raw materials grows, advancements in pyrometallurgical recycling will become increasingly important.
Integrating artificial intelligence and machine learning into process control is another frontier. These technologies can optimize temperature profiles and chemical additions in real-time, further improving recovery rates and energy efficiency.
What Role Does Hydrometallurgy Play in Efficient Metal Extraction from Chillers?
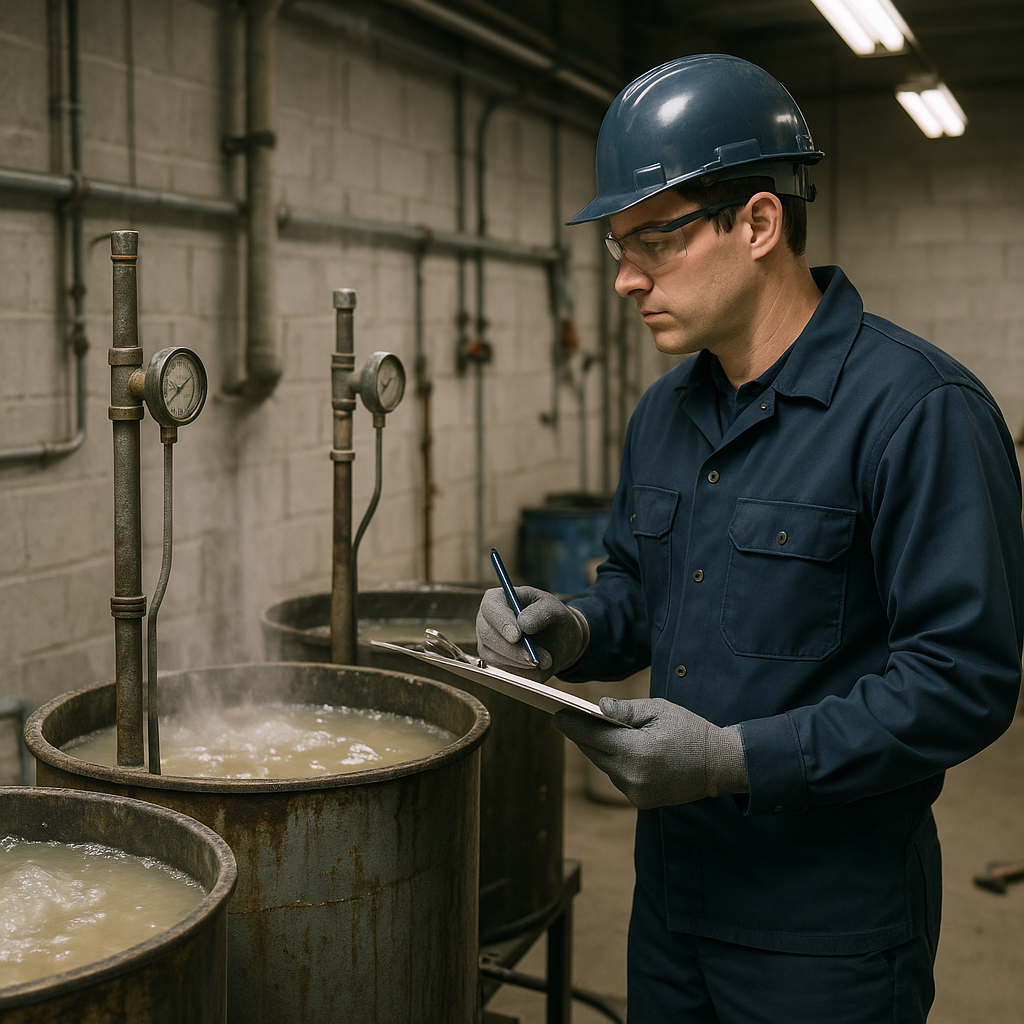
Hydrometallurgy represents a significant advancement in metal recovery techniques, utilizing aqueous solutions rather than extreme heat to extract valuable metals from chillers and other recycled materials. This water-based approach provides substantial environmental benefits while maintaining high efficiency.
Often called “wet metallurgy,” hydrometallurgy has gained popularity for its ability to produce exceptionally pure metals while consuming less energy than traditional methods. This technique is particularly valuable for processing complex materials found in end-of-life chillers.
Three Key Stages of the Hydrometallurgical Process
The hydrometallurgical metal extraction process consists of three essential phases that work together to recover valuable materials efficiently.
First is leaching, where aqueous solutions dissolve metals from the source material. Leaching agents can be acidic, basic, or specialized chemical compounds. These solutions selectively target specific metals while leaving unwanted materials behind. The choice of leaching agent depends on the target metals and material characteristics.
The second phase involves solution concentration and purification. This critical step separates valuable dissolved metals from impurities. Techniques like solvent extraction use organic solvents to selectively remove metal ions, while ion exchange methods employ resins that adsorb specific metals from the solution. These processes act as refined filters that ensure high metal recovery rates with minimal waste.
The final stage is metal recovery, where dissolved metals return to solid form. Electrowinning plays a key role here, using electricity to deposit metal ions onto cathodes. Other methods include chemical reduction or precipitation, depending on the specific metals involved. This versatility allows hydrometallurgy to produce metals with exceptional purity levels.
Environmental Advantages Over Traditional Methods
Hydrometallurgy offers several environmental benefits compared to pyrometallurgical approaches. The process operates at significantly lower temperatures and pressures, reducing energy consumption and carbon footprint.
Traditional pyrometallurgical methods require intense heat to extract metals, consuming large amounts of energy and producing greenhouse gas emissions. Hydrometallurgy avoids these drawbacks by using chemical reactions in controlled aqueous environments instead of high-temperature smelting.
The reduced environmental impact makes hydrometallurgy increasingly attractive as sustainability becomes a priority in industrial processes. The technique aligns with growing regulatory pressure to minimize emissions and waste in recycling operations.
Processing Complex Materials Efficiently
One of the most valuable aspects of hydrometallurgy is its ability to process materials that would be difficult or uneconomical to handle through conventional methods. Chillers often contain complex mixtures of metals and alloys that present challenges for recyclers.
Hydrometallurgy excels at selective metal extraction, allowing recyclers to recover individual metals from these complex mixtures with precision. This selectivity becomes particularly important when dealing with electronic components from modern chillers containing precious metals in small quantities.
The process enables the economic recovery of metals from low-grade sources that might otherwise be discarded, contributing to more comprehensive resource utilization and supporting circular economy principles.
Additionally, hydrometallurgy can process materials with complex compositions that might cause problems in traditional smelting operations. This adaptability makes it ideal for the diverse materials found in chillers and other cooling equipment.
Process | Advantages | Disadvantages |
---|---|---|
Hydrometallurgy | Environmentally friendly, efficient for low-grade ores, lower energy consumption | Slower process, can produce acidic wastewater |
Pyrometallurgy | High recovery rates, efficient for bulk processing | High energy consumption, produces toxic emissions |
Practical Applications in Chiller Recycling
When applied to chiller recycling, hydrometallurgy offers specific advantages for recovering metals like copper, aluminum, zinc, and other valuable materials. The process allows for targeted extraction of these metals, which can then be reused in manufacturing new products.
Modern chillers often contain specialized alloys and components designed for optimal heat transfer and energy efficiency. Hydrometallurgy can separate these materials effectively, preserving their value despite their complex composition.
The technique has proven especially useful for recovering copper from chiller components. Using selected leaching agents, recyclers can dissolve copper into solution and then use electrowinning to recover it at high purity levels. This approach preserves the value of this essential metal for reuse in new products.
As equipment designs evolve to include more diverse materials, hydrometallurgy provides recyclers with the flexibility to adapt their processes accordingly, helping maximize resource recovery as technology advances.
How Does Electrometallurgy Contribute to Advanced Metal Recovery from Chillers?

Electrometallurgy is at the forefront of modern metal extraction technology from chillers. This approach uses electrical energy to drive chemical reactions that extract and purify metals with precision. The process employs electrolytic cells where controlled electrical currents facilitate the separation and recovery of valuable metals.
A key advantage of electrometallurgy is its ability to produce high-purity metals. Unlike traditional methods, the electrolytic process achieves remarkable purity levels for critical metals such as copper and nickel. These purified metals meet the stringent requirements of industries from electronics to construction.
Energy Efficiency and Cost Benefits
Electrometallurgy offers significant energy conservation compared to conventional metal recovery methods. Traditional approaches often require substantial heat and chemical treatments. In contrast, electrolytic processes operate through precise electrical current control that optimizes energy use.
The efficiency comes from the ability to fine-tune electrical parameters. Metallurgists can adjust current density and other variables to maximize recovery while minimizing energy consumption. This precision ensures that only the necessary energy is used to separate metal ions from solutions.
Cost-effectiveness is another advantage. The use of electric current to extract metals means less reliance on extensive chemical treatments. This reduction in chemical usage translates to lower operational costs and fewer environmental concerns.
Technological Advancements in Cell Design
Recent years have seen remarkable innovations in electrolytic cell design. Engineers have developed improved electrode materials that withstand harsh conditions while maintaining excellent conductivity. These advances have led to higher current densities and significantly faster extraction rates.
Modern electrolytic cells incorporate sophisticated monitoring systems that adjust parameters in real time. This automation ensures consistent quality and maximum efficiency throughout the extraction process. The technology allows for precise control over metal deposition, resulting in superior product quality.
The integration of these technological improvements has expanded the capabilities of electrometallurgy. The process can now handle a wider range of metals and achieve faster recovery rates. This versatility makes it particularly valuable for processing complex materials like those found in chillers.
Environmental Advantages
The environmental benefits of electrometallurgy make it increasingly attractive for sustainable metal recovery. The process produces fewer emissions compared to high-temperature extraction methods. This reduction in pollution aligns with growing environmental regulations and corporate sustainability goals.
Electrometallurgy also requires less land disturbance than traditional mining and extraction operations. The compact nature of electrolytic facilities minimizes the physical footprint of metal recovery activities, preserving natural landscapes and reducing ecosystem disruption.
The ability to process recycled materials efficiently further enhances the environmental profile of electrometallurgy. The technology enables the recovery of metals from sources that might otherwise end up in landfills, supporting circular economy principles and resource conservation efforts.
Method | Principle | Advantages | Applications |
---|---|---|---|
Electrometallurgy | Uses electrical energy for extraction and refining | High-purity metal recovery, energy efficiency | Copper, nickel extraction from chillers |
Pyrometallurgy | Heat-based metal separation | High recovery rates, efficient for bulk processing | Reclaiming copper from chillers |
Hydrometallurgy | Chemical solutions for metal extraction | Environmentally friendly, low energy consumption | Processing complex materials in chillers |
Applications in Chiller Recycling
In chiller recycling, electrometallurgy excels at extracting valuable metals from end-of-life units. The process can selectively recover copper, aluminum, and other metals present in chiller components. This selectivity ensures maximum value recovery from discarded equipment.
The precision of electrometallurgical processes allows for the recovery of even trace amounts of precious metals. These metals, often present in electronic components of chillers, can be economically extracted using electrolytic methods. The recovery of these high-value materials significantly improves the economics of chiller recycling.
As demand for metals continues to rise, particularly for applications in renewable energy and electric vehicles, electrometallurgy will play an increasingly vital role. Its ability to deliver high-purity metals with minimal environmental impact positions it as a key technology for sustainable resource management.
Conclusion: The Future of Metal Recovery from Chillers
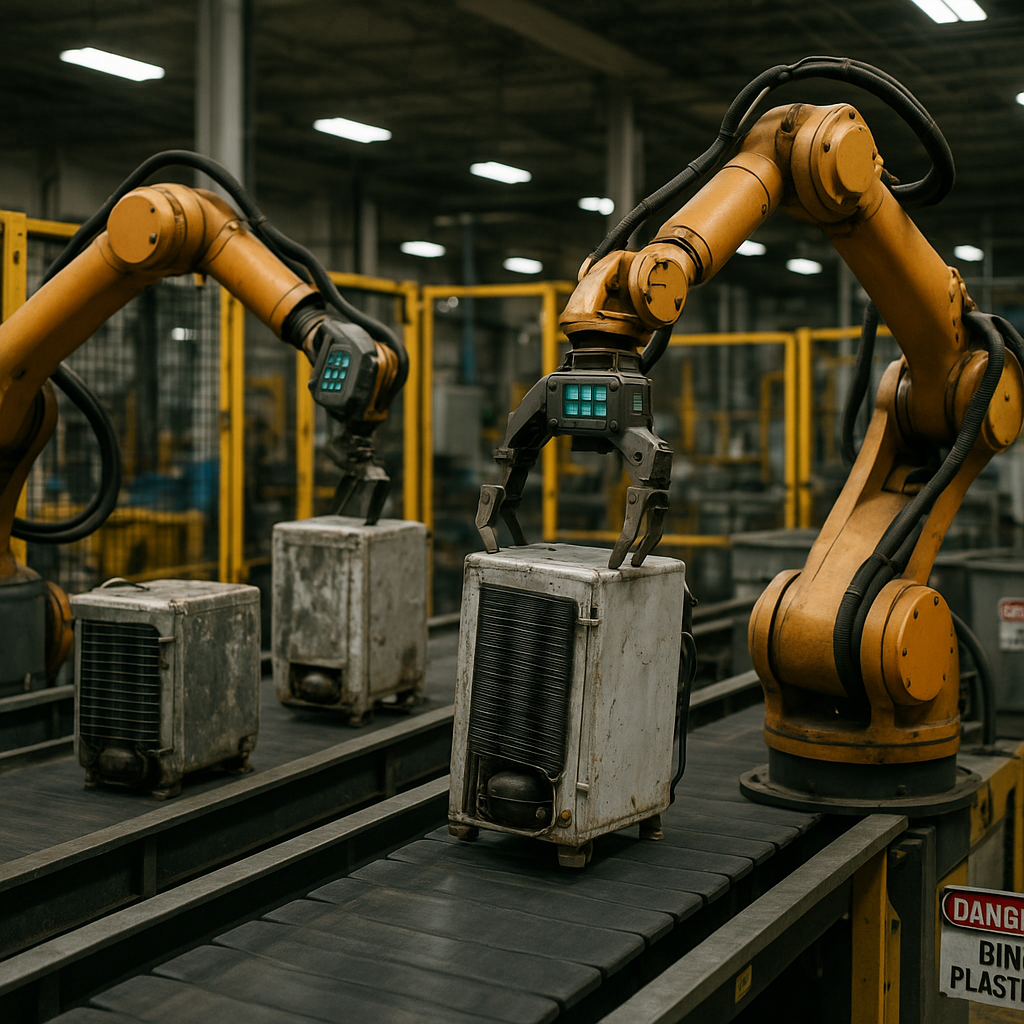
The metal recovery industry from chillers is undergoing significant transformation, driven by advancements in pyrometallurgy, hydrometallurgy, and electrometallurgy. These innovative extraction techniques are enhancing recycling processes and reshaping sustainability and resource management practices globally. Through precise temperature control, advanced chemical processes, and cutting-edge technology, we are achieving unprecedented efficiency in material recovery with tangible benefits: reduced environmental impact, conservation of finite resources, and progress toward a circular economy.
As these technologies evolve, recycling rates are expected to rise, creating employment opportunities, driving innovation, and strengthening supply chains. Achieving sustainable metal extraction from chillers requires collaboration from all stakeholders. For expert guidance on maximizing the value of recyclable materials while minimizing environmental impact, contact Okon Recycling at 214-717-4083.