5901 Botham Jean Blvd, Dallas, TX 75215
What Is the HVAC Chiller Recycling Process?
May 9, 2025The HVAC chiller recycling process follows a structured workflow that recovers valuable materials while protecting the environment. Modern chillers contain many recyclable components and potentially harmful substances that require proper handling. Recycling prevents these industrial cooling units from contributing to landfill waste.
Chiller recycling begins with a comprehensive assessment of each unit. Technicians evaluate the condition, age, and components to determine the most effective recovery approach. This step is crucial for mapping out the recycling journey and identifying which parts can be repurposed or reclaimed.
The process is vital for environmental protection due to the refrigerants in these systems. These chemicals can significantly contribute to ozone depletion and global warming if released improperly. Through responsible recycling practices, we can minimize industrial waste while recovering valuable metals, copper, and other materials for reuse in manufacturing.
What Components Can Be Recycled in HVAC Chillers?
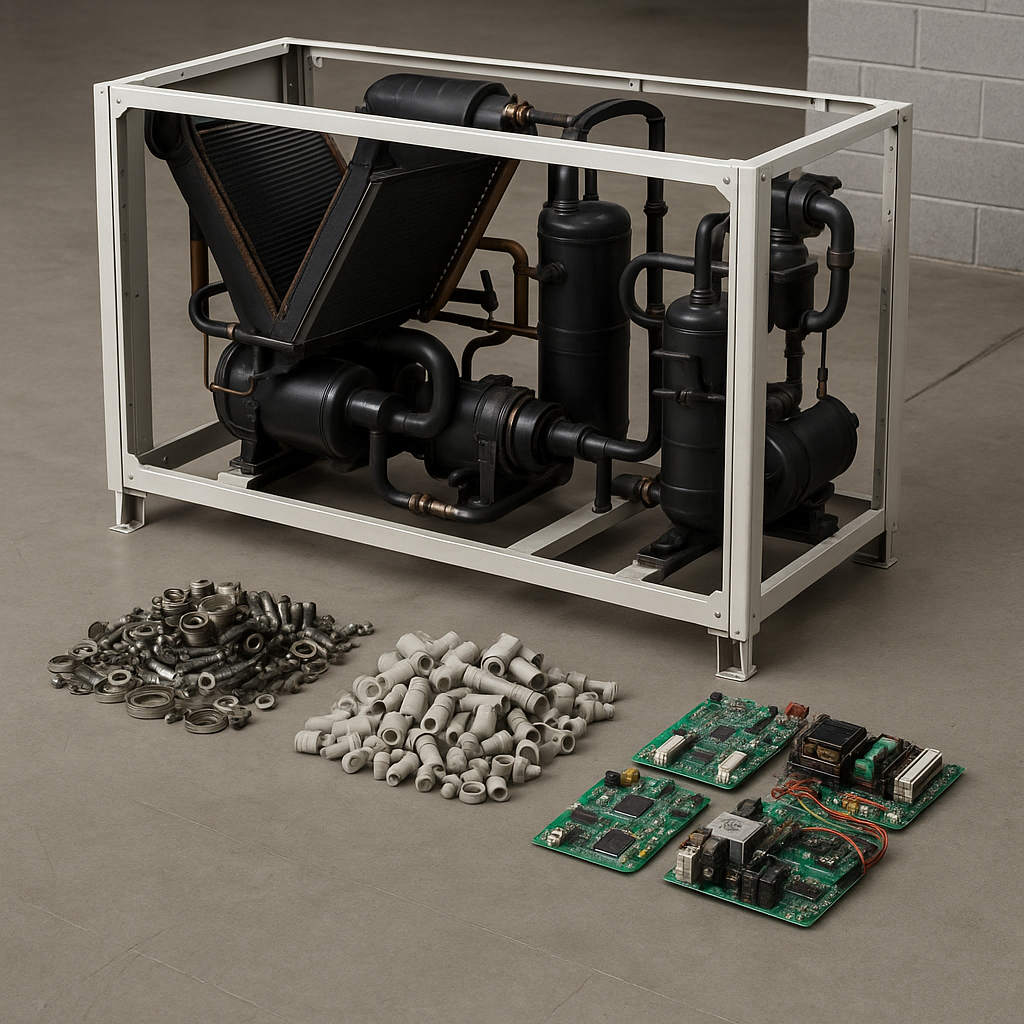
An overview of a disassembled HVAC chiller showcasing various sorted components on the industrial floor.
HVAC chiller systems contain valuable materials that can be effectively recycled. Key recyclable materials include steel, aluminum, copper, and brass. These metals are highly sought after in the recycling market due to their durability and reusability.
Professional HVAC contractors typically separate these materials by type during disassembly. This separation is crucial for maximizing the recycling value of each component. Proper sorting ensures efficient processing at recycling facilities.
Recyclable Components
When an HVAC chiller reaches the end of its service life, several components can be recycled. These parts hold significant value in the scrap metal market. Steel frames, although less valuable than other metals, provide structural support and can be fully recycled.
Copper components are among the most valuable recyclable materials in HVAC chillers. Found in refrigerant lines and coils, copper commands premium prices due to its high demand and excellent conductivity. Proper recovery of copper significantly increases the overall recycling value of an old unit.
Aluminum parts are also highly recyclable. This lightweight metal is commonly used in heat exchangers and fins due to its corrosion resistance and thermal conductivity. Recycling aluminum saves up to 90% of the energy required to produce new aluminum from raw materials.
- Motors
- Compressors
- Copper tubing and coils
- Sheet metal components
- Brass fittings and valves
- Metal ductwork
- Furnaces
- Aluminum heat exchangers
Brass components, primarily found in fittings and valves, are made of copper and zinc alloys. Their durability and resistance to corrosion make them ideal for HVAC applications. These components maintain good value in the recycling market due to their metal content.
Non-Recyclable Components
Not all parts of HVAC chillers can be recycled through standard metal recycling processes. Some components require special handling or disposal methods. Understanding which parts cannot be recycled is important for proper waste management.
- Fiberboard materials
- Capacitors
- Small plastic components
- Flex ducts
These non-recyclable components must be separated from recyclable materials and disposed of according to local regulations. In some cases, specialized facilities may be able to process these items, but they generally cannot be included with standard metal recycling.
Before recycling an HVAC chiller, all refrigerants must be properly recovered by certified technicians. The EPA requires that refrigerants be reclaimed to prevent harmful emissions that can contribute to ozone depletion. HVAC professionals must follow specific safety guidelines and maintain detailed logs about refrigerant handling.
Recyclable Components | Non-Recyclable Components |
---|---|
Steel frames | Fiberboard materials |
Copper tubing and coils | Capacitors |
Aluminum heat exchangers | Small plastic components |
Brass fittings and valves | Flex ducts |
Motors | |
Compressors | |
Sheet metal components | |
Metal ductwork | |
Furnaces |
Proper recycling of HVAC chillers not only recovers valuable materials but also reduces landfill waste and conserves natural resources. By sorting and cleaning components before recycling, the value of scrap materials can be maximized while minimizing environmental impact.
How is Refrigerant Handled in the Recycling Process?
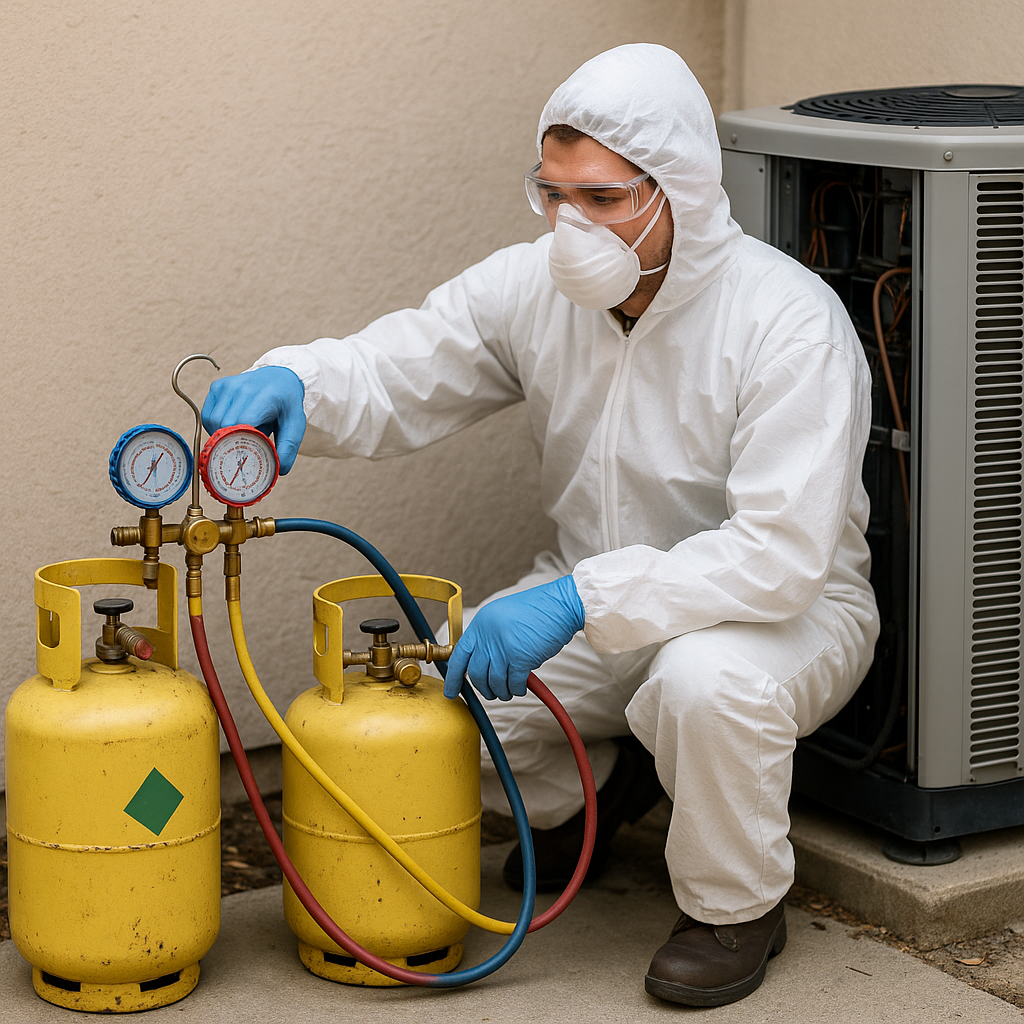
A technician ensures safe refrigerant extraction from an HVAC unit.
Refrigerant handling is a crucial aspect of HVAC chiller recycling. These compounds, when released into the atmosphere, contribute significantly to ozone depletion and climate change. The Environmental Protection Agency (EPA) regulates refrigerant management through Section 608 of the Clean Air Act, which prohibits the knowing release of refrigerants during maintenance, service, repair, or disposal of air-conditioning equipment.
Only EPA-certified technicians are authorized to handle refrigerants in HVAC systems. This certification ensures technicians understand the environmental implications and proper handling procedures. The certification varies based on the equipment being serviced, and technicians must keep their certification documentation at their place of business for at least three years after they stop working as technicians.
Refrigerant Recovery Process
The first step in proper refrigerant handling is recovery. Certified technicians must evacuate refrigerant before opening or disposing of appliances using specialized recovery equipment. The EPA mandates specific evacuation levels that technicians must achieve before opening systems. These requirements help minimize refrigerant emissions and prevent environmental harm.
Recovery techniques vary based on system size and refrigerant type. Technicians may use liquid recovery, vapor recovery, or push-pull methods depending on the specific situation. Each method requires specialized equipment designed to safely capture refrigerant without releasing it to the atmosphere.
After recovery, technicians transfer the refrigerant to appropriate storage cylinders for transport. These cylinders must meet Department of Transportation specifications and be properly labeled with the refrigerant type. Improper storage can lead to dangerous situations, including potential cylinder rupture.
Reclamation and Documentation Requirements
Recovered refrigerant cannot simply be reused in most cases. The EPA requires that refrigerant be reclaimed to meet purity standards before reuse. This reclamation process involves removing contaminants through specialized filtration and distillation techniques performed by EPA-certified reclaimers.
Detailed documentation is essential for refrigerant compliance. Technicians must maintain comprehensive records of all refrigerant handling activities. For systems containing 5 to 50 pounds of refrigerant, records must include the location and date of recovery, refrigerant type, monthly recovery quantities, and transfer details for reclamation or destruction.
These logs serve multiple purposes. They help businesses track their environmental impact, provide necessary documentation for regulatory compliance, and create accountability throughout the refrigerant lifecycle. The EPA may request these records during compliance inspections.
Leak Inspection and Verification
EPA regulations include specific leak inspection requirements for systems containing ozone-depleting refrigerants. Large commercial systems with over 500 pounds of refrigerant require quarterly inspections if they exceed allowable leak rates. Systems between 50-500 pounds need annual inspections. These inspections help identify and address leaks promptly, reducing environmental impact.
When repairing leaks, technicians must perform verification tests to confirm repairs were successful. These tests include an initial verification before adding refrigerant and a follow-up test after the system returns to normal operation. The goal is to ensure that refrigerant remains contained within the system rather than escaping into the atmosphere.
For refrigerant that cannot be reused or reclaimed, proper disposal is essential. The refrigerant must be transferred to EPA-certified destruction facilities using specific protocols. This final stage of the refrigerant lifecycle requires the same careful documentation as earlier stages.
What Are the Steps in the HVAC Chiller Recycling Process?
The HVAC chiller recycling process is a systematic approach that combines environmental responsibility with resource recovery. It begins when specialized contractors remove old equipment during system upgrades or replacements. These professionals are trained to handle large commercial units safely.
After removal, technicians thoroughly assess each unit to identify valuable components and materials for reclamation, focusing on metals, wiring, and refrigerants. This evaluation determines the most efficient recycling pathway for each component.
Material separation is a crucial step. Workers methodically disassemble the units and sort materials by type. Copper coils, aluminum fins, steel casings, and other metals are organized separately to maximize recycling efficiency and value.
Refrigerant Recovery and Processing
Refrigerant management is one of the most environmentally significant aspects of chiller recycling. Certified technicians extract refrigerants using specialized recovery equipment that prevents atmospheric release. This step requires precision to capture all refrigerant without leakage.
The recovered refrigerants undergo testing to determine purity levels and identify contaminants. Oil separation equipment removes any lubricants that might have mixed with the refrigerant during operation, creating a cleaner product for further processing.
Many facilities employ distillation for refrigerant purification. This process involves heating the refrigerant to separate different compounds based on their boiling points, effectively removing impurities and restoring the refrigerant to its original specifications for reuse.
Final Processing and Compliance
After refrigerant recovery, remaining components undergo further processing. Circuit boards and electronic controls are sent to specialized e-waste recyclers. Insulation materials and non-recyclable components are properly disposed of according to regulations.
Throughout the process, strict documentation maintains EPA compliance. Records track the quantity of recovered refrigerants, their ultimate disposition, and the handling of potentially hazardous materials, forming an essential part of regulatory adherence.
The final step involves reporting and certification. Recycling facilities provide documentation confirming proper handling and processing of all materials. These certificates help commercial building owners demonstrate their environmental compliance and commitment to sustainable practices.
Component | Recyclability | Notes |
---|---|---|
Steel Frames | Recyclable | Structural support, fully recyclable |
Copper Tubing and Coils | Recyclable | High value due to conductivity |
Aluminum Heat Exchangers | Recyclable | Saves up to 90% energy in recycling |
Brass Fittings and Valves | Recyclable | Good value due to metal content |
Motors | Recyclable | |
Compressors | Recyclable | |
Sheet Metal Components | Recyclable | |
Metal Ductwork | Recyclable | |
Furnaces | Recyclable | |
Fiberboard Materials | Non-Recyclable | Requires special handling |
Capacitors | Non-Recyclable | Requires special handling |
Small Plastic Components | Non-Recyclable | Requires special handling |
Flex Ducts | Non-Recyclable | Requires special handling |
Conclusion: The Impact of HVAC Chiller Recycling
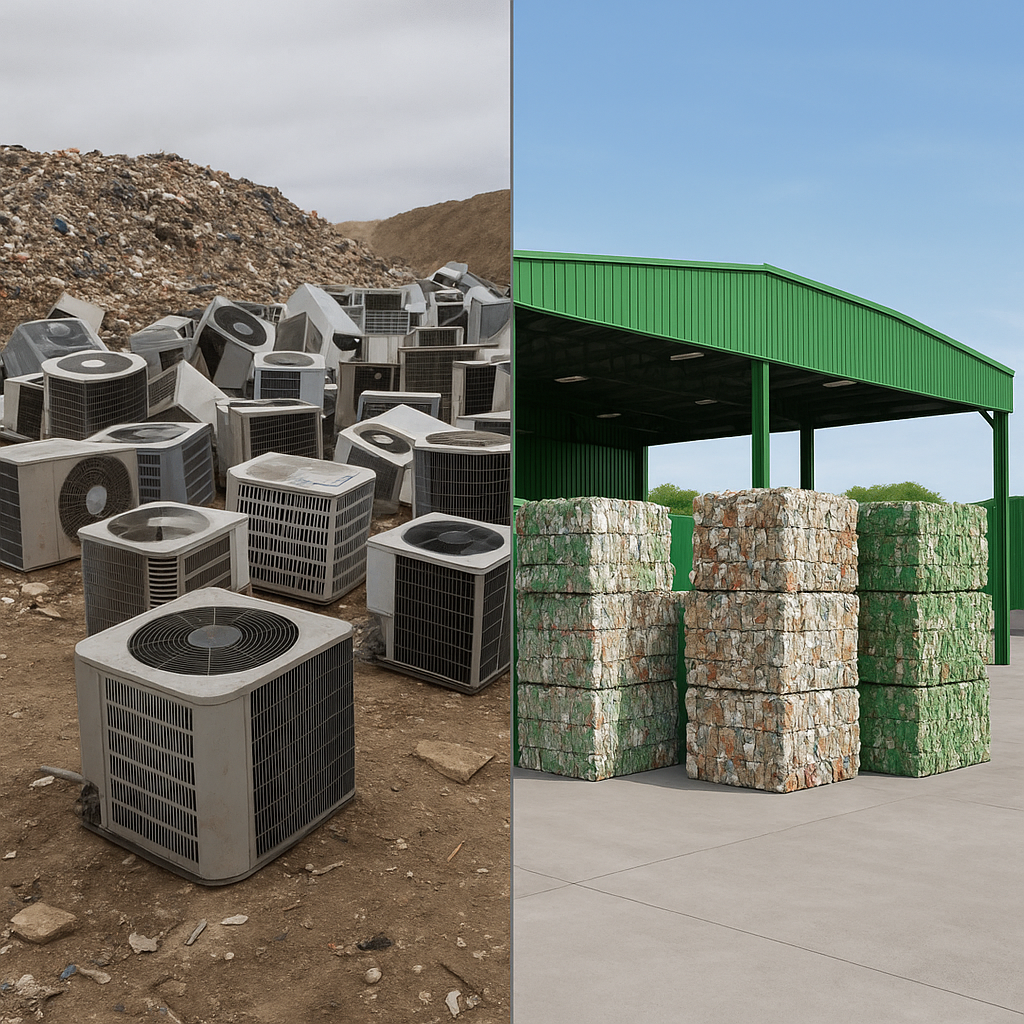
A visual comparison of a landfill filled with discarded HVAC units and a green recycling facility with processed materials, highlighting the contrast between waste and sustainability.
HVAC chiller recycling is crucial for reducing industrial waste. By recovering components and managing refrigerants, this process keeps significant amounts of materials out of landfills while reclaiming valuable metals for reuse. The environmental benefits also include preventing harmful refrigerant emissions, which can have a global warming potential far greater than carbon dioxide.
For organizations dedicated to sustainability and compliance, effective HVAC chiller recycling is essential. When your facility needs professional recycling solutions for cooling equipment, contact Okon Recycling at 214-717-4083 for responsible disposal services that align with your sustainability goals and regulatory requirements.