5901 Botham Jean Blvd, Dallas, TX 75215
The Case for Reusing Electronic Components in a Circular Economy
July 6, 2025Every year, millions of electronic devices become obsolete or break down, creating mountains of e-waste. Hidden within these discarded products is untapped value. Reusable electronic components are salvageable parts from these discarded electronics that can function effectively in new products or repairs.
These components include fundamental building blocks of modern electronics such as resistors, capacitors, transistors, integrated circuits, and microprocessors. They are found on printed circuit boards inside smartphones, computers, televisions, and numerous other devices that surround us daily. The practice of component recovery involves careful extraction, testing, and reconditioning to ensure functionality.
Recovering and reusing electronic components extends their operational lifespan well beyond the original product’s lifecycle. This practice provides significant environmental benefits by reducing the approximately 62 million metric tons of electronic waste generated globally each year. Rather than mining raw materials for new component manufacturing—which requires substantial energy and creates pollution—component reuse conserves these resources while diverting harmful substances like lead, mercury, and cadmium from landfills.
How Are Electronic Components Salvaged and Reconditioned?
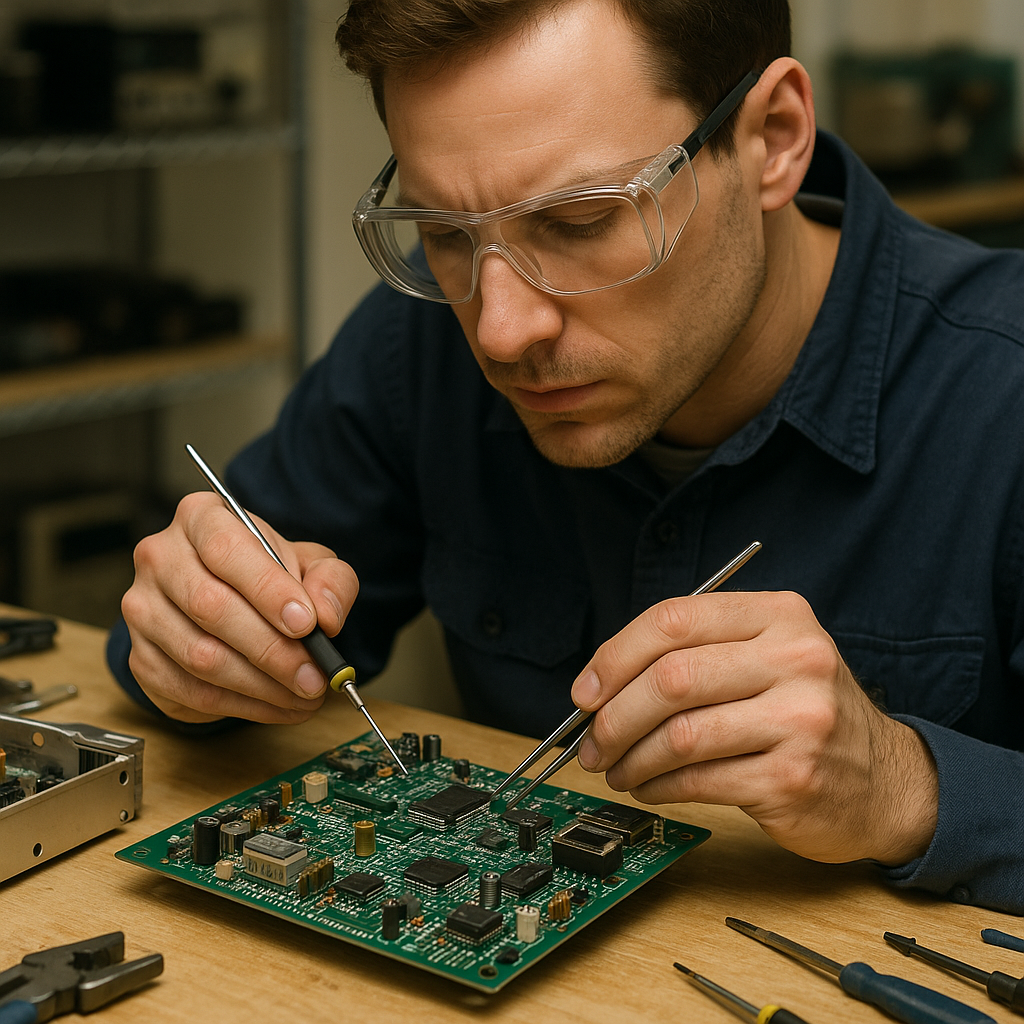
The salvage and reconditioning of electronic components is a precise, multi-stage process that requires specialized equipment and expertise. These valuable parts are carefully extracted from obsolete devices or scrap circuit boards, then restored to meet quality standards for reuse in new applications.
Component Removal Techniques
The first step in the salvage process involves carefully removing components from printed circuit boards. Technicians use several methods depending on the component type and mounting technique. Hot air removal is among the most common approaches for surface-mounted components.
With hot air removal, technicians direct a controlled stream of heated air to melt the solder connecting the component to the board. Once the solder liquefies, the component can be lifted away without damage. For more delicate or valuable components, specialized tools maintain precise temperature control to prevent thermal damage.
Through-hole components require different removal techniques. Mini solder wave systems or manual desoldering tools are used to remove the solder from connection points before the component can be safely extracted. The goal is always to preserve the component’s functionality during removal.
Lead and Pad Reconditioning
After removal, most components require reconditioning of their connection points. Leads, pins, or pads often have excess solder or may be damaged during the removal process. This reconditioning stage is critical to ensure proper function when the component is reused.
Robotic hot solder dip systems are the industry standard for this process. These systems precisely control the immersion depth, dwell time, and temperature while components are dipped in solder baths. This process restores proper solder plating to the leads and ensures uniform coating.
For ball grid array (BGA) components, the process is more complex. The old solder balls must be removed completely, the pads prepared, and new solder balls attached. This “reballing” process requires specialized fixtures and precise temperature control to maintain the exact spacing and height of each solder ball.
Cleaning and Testing
Once leads and connection points are reconditioned, components undergo thorough cleaning to remove any flux residues or contaminants. This typically involves batch or inline cleaning systems using appropriate solvents or aqueous cleaning agents.
Components sensitive to moisture are baked in specialized ovens to remove any absorbed moisture that could cause damage during future soldering processes. This step is crucial for meeting the component’s Moisture Sensitivity Level (MSL) requirements.
Testing follows cleaning and represents perhaps the most critical stage in the reconditioning process. Each component undergoes electrical testing to verify its functionality and performance characteristics. Additional tests may include solderability testing, curve tracing, and in some cases, functional testing to ensure the component operates within specified parameters.
Quality Standards and Documentation
The entire reconditioning process must adhere to strict industry standards. Components are often processed according to specifications like J-STD-002 for solderability and J-STD-020F for moisture sensitivity handling. These standards ensure reconditioned components will perform reliably in new applications.
Documentation is maintained throughout the process, tracking the component’s origin, the procedures performed, and test results. This documentation provides traceability and verification that proper processes were followed, building trust in the reconditioned components.
After passing all quality checks, components may be repackaged in tubes, trays, or tape and reel packaging for use with automated assembly equipment. Some facilities add markings to distinguish reclaimed components from new ones while maintaining original part identification.
Economic and Environmental Benefits
The economic value of component salvage varies based on the component type and current market conditions. High-value components like microprocessors and specialized integrated circuits often justify the salvage costs. The environmental benefits are significant regardless of economic considerations.
Salvaging and reconditioning electronic components conserves the substantial energy used in manufacturing new components. A single semiconductor wafer can require 1,500 to 2,500 kWh of energy to produce. Reusing components reduces this energy demand and minimizes the environmental impact of electronic manufacturing.
What Challenges Face the Reuse of Electronic Components?
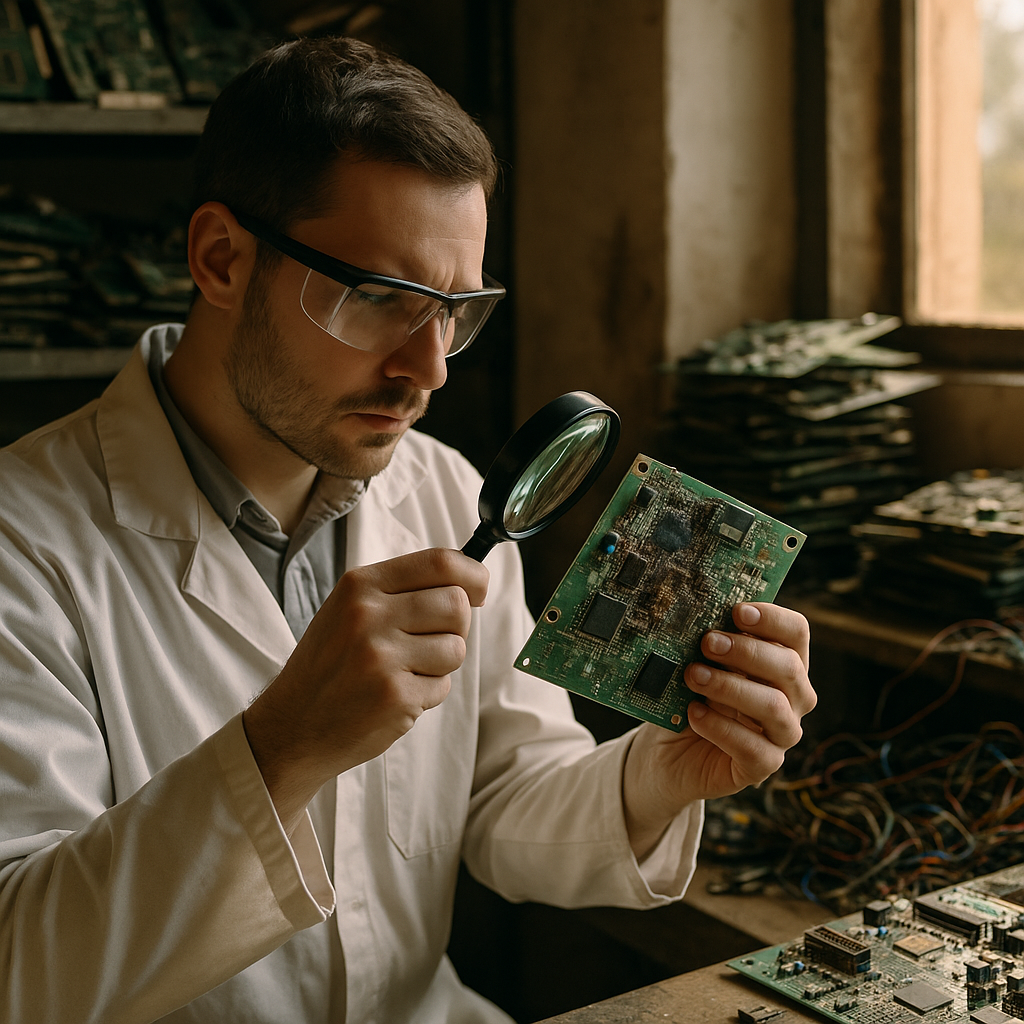
Compatibility issues represent a major hurdle in electronic component reuse. Components salvaged from different devices often vary in specifications, form factors, and technical standards. This diversity complicates integration into new systems and can lead to unpredictability. Many recycled components come from various batches and devices, creating inconsistency in performance characteristics. Organizations addressing this challenge have developed advanced testing protocols to verify compatibility before integration, reducing potential failures in finished products.
Technological obsolescence in the electronics industry accelerates rapidly. What was once cutting-edge quickly becomes outdated as technology evolves. The lifecycle of semiconductors highlights this trend – components that once lasted 30 years now typically become obsolete within a decade. This rapid turnover creates barriers to reuse, as older components may not meet the performance requirements of modern applications. Some forward-thinking companies design systems with modular architectures that can accommodate both new and reclaimed components.
Safety and reliability concerns remain paramount when reusing electronic components. Without proper testing and verification, reclaimed components may pose risks, from simple malfunctions to catastrophic failures. Thorough quality control measures are essential but add cost and complexity to the reuse process. The challenge lies in establishing cost-effective testing methods while maintaining high standards. Several electronic manufacturers have developed streamlined testing procedures to quickly identify faulty components while upholding rigorous safety standards.
Trust in reclaimed components is another significant barrier. Many manufacturers and consumers remain skeptical about the performance and longevity of recycled electronic parts. This perception issue hampers widespread adoption despite the environmental benefits. Industry leaders are working to overcome this by demonstrating successful implementation cases and providing performance guarantees for refurbished components.
The lack of universal industry standards specifically for reclaimed electronic components creates inconsistency across the sector. While regulations exist for new components, the reclaimed market operates with fewer standardized guidelines. This regulatory gap complicates quality assessment and integration. Industry associations have begun developing certification programs to verify the quality and performance of recycled components, helping to establish clearer standards.
Economic factors also significantly impact electronic component reuse. The cost of thorough testing, refurbishment, and recertification can sometimes exceed the price of new components, particularly for common parts. This economic imbalance discourages widespread adoption. Innovative companies are developing automated testing systems to reduce these costs while maintaining quality.
In high-reliability sectors like healthcare, aerospace, and defense, regulatory requirements create additional barriers. These industries must undergo costly recertification processes even when using functionally equivalent reclaimed components. Some organizations are collaborating with regulatory bodies to create streamlined approval pathways for verified reclaimed components, potentially opening these markets to greater reuse practices.
Despite these challenges, the electronic component reuse market continues to grow as manufacturers seek sustainable alternatives. The industry is gradually shifting from viewing these challenges as barriers to seeing them as opportunities for innovation. As testing technologies improve and standards evolve, the potential for integrating reclaimed components into mainstream manufacturing increases substantially, creating both environmental and economic benefits.
Conclusion: The Future of Electronic Component Reuse
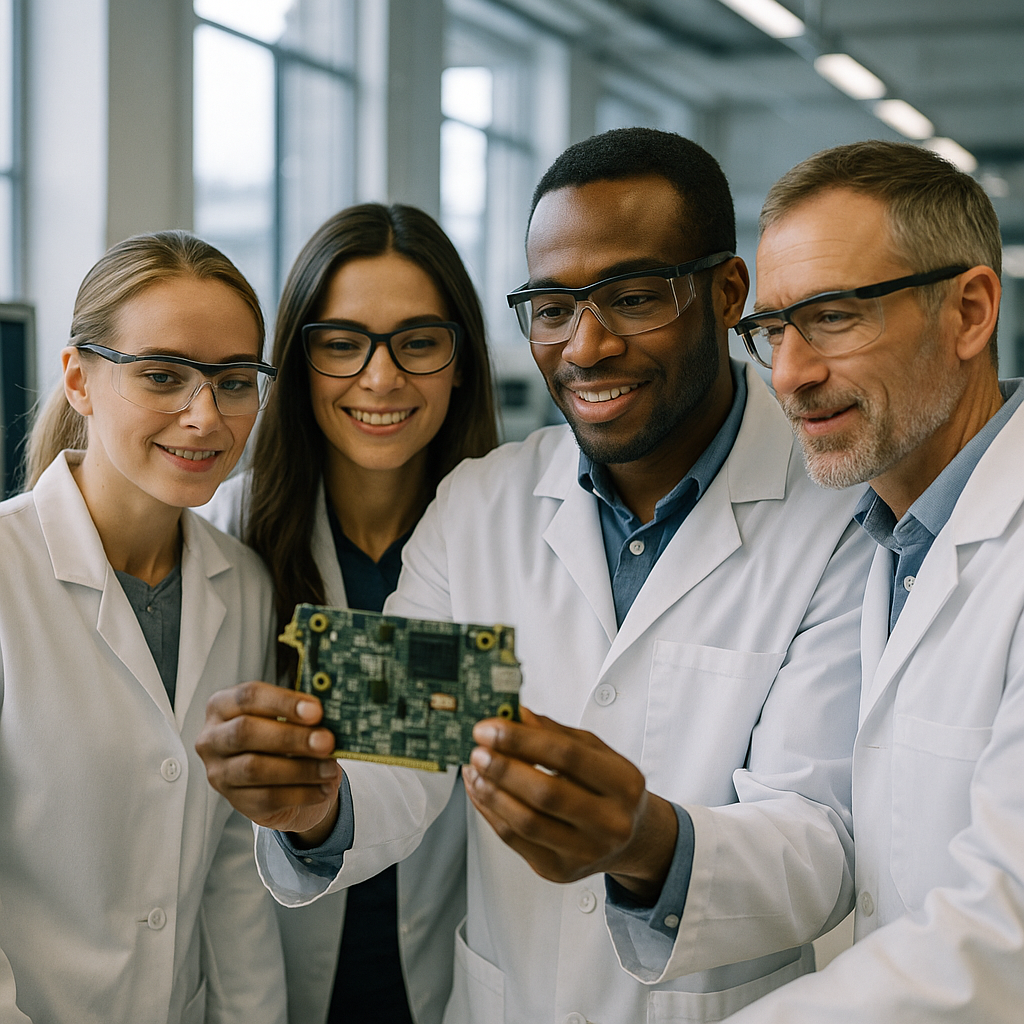
Reusing electronic components is a powerful solution to the growing e-waste crisis. With global electronic waste generation expected to reach 82 million metric tons by 2030, component reuse provides multiple ways to reduce environmental impact while offering economic benefits. Recovering and reconditioning high-value components like microprocessors and AI chips help preserve precious resources and minimize the need for energy-intensive manufacturing processes.
Although challenges exist in standardization, compatibility, and technological obsolescence, the advantages far outweigh these obstacles. Component reuse significantly reduces hazardous materials in landfills, decreases the demand for raw material extraction, and creates economic opportunities in processing, collection, and refurbishment. As industries move toward circularity and eco-friendly practices, electronic component reuse will increasingly become central to sustainable electronics manufacturing.
For your electronic recycling needs, contact Okon Recycling at 214-717-4083.