5901 Botham Jean Blvd, Dallas, TX 75215
What is Electronics Parts Harvesting?
July 2, 2025Electronic waste has reached alarming levels globally, with the world generating 62 million metric tons of e-waste in 2022. This figure is expected to increase to 82 million metric tons by 2030. Amid this growing crisis, electronics parts harvesting has emerged as a practical solution.
Electronics parts harvesting is the systematic recovery of valuable components from discarded electronic devices and circuit boards. This process involves extracting reusable parts such as CPUs, memory modules, power supplies, and custom chips. These salvaged components can be reused in repairs, replacements, or entirely new applications.
The practice extends beyond merely saving costs. Harvesting electronic components plays a crucial role in environmental sustainability by diverting toxic materials like lead, mercury, and cadmium from landfills. It also reduces the demand for new raw material extraction, which often involves environmentally damaging mining practices.
What Tools and Techniques are Used for Parts Harvesting?
Harvesting electronic components requires precision and the right tools to recover valuable parts without causing damage. The process varies depending on whether you’re working with through-hole or surface-mount components, but the approach generally focuses on careful heat application and component extraction.
Essential Harvesting Tools
Successful parts harvesting starts with having the right equipment. These tools are essential for safe and effective component removal:
- Heat sources — Soldering irons, heat guns, or butane torches for melting solder joints.
- Desoldering equipment — Desoldering pumps (solder suckers) and desoldering wick/braid to remove melted solder.
- Hand tools — Pliers, tweezers, and wire cutters for handling and removing components.
- Safety equipment — Anti-static wrist straps, safety glasses, and good ventilation to protect yourself and sensitive components.
- Organizational containers — Small jars, compartment boxes, or anti-static bags for sorting and storing recovered parts.
- Cleaning supplies — Isopropyl alcohol and brushes for removing flux residue after component removal.
Techniques for Through-Hole Component Removal
Through-hole components have pins that pass through the circuit board and are soldered on the opposite side. Removing these components requires melting the solder joints and freeing the pins:
First, heat the solder joint with your soldering iron until the solder becomes liquid. Once melted, use a desoldering pump to vacuum up the liquid solder or apply desoldering braid to absorb it. For components with multiple pins, work on one pin at a time, being careful not to apply heat for too long to avoid damaging the component or board.
After removing enough solder from all pins, gently pull the component from the board using pliers or tweezers. Some resistance is normal, but excessive force indicates remaining solder that needs to be removed.
Surface-Mount Component Harvesting
Surface-mount components present a different challenge as they sit on top of the circuit board rather than passing through it. These smaller components require specialized techniques:
For small SMT components like resistors and capacitors, carefully apply heat to one end of the component while using tweezers to lift that end. Then heat the other end to completely free the component. Larger surface-mount ICs with multiple pins benefit from a hot air rework station that heats all solder joints simultaneously.
One effective technique for harvesting multiple SMT parts is the “brush-off” method. Apply heat evenly across an area of components with a heat gun until the solder liquefies, then carefully brush or tap the components off onto a heat-resistant surface for collection.
Testing and Sorting Harvested Components
After removing components, it’s essential to test their functionality before storage or reuse. Use a multimeter to check resistors, capacitors, and other passive components. For capacitors, visually inspect for bulges or leaks indicating failure. Organize tested components in clearly labeled containers based on type, value, and functionality status.
When harvesting from older electronics, prioritize high-value components like specialty ICs, power transistors, and electrolytic capacitors that are often still functional. Components like heat sinks and fans can also be removed and repurposed for other projects.
By mastering these harvesting techniques, you can recover valuable electronic components from discarded devices, reducing electronic waste while building a useful inventory of parts for repairs and new projects.
Tool | Application |
---|---|
Soldering Iron | Melting solder to remove components from circuit boards |
Desoldering Pump (Solder Sucker) | Removing melted solder after heating to free components |
Desoldering Wick/Braid | Absorbing melted solder from joints |
Pliers | Handling and removing components |
Wire Cutters | Cutting leads and wires during component removal |
Tweezers | Handling small and sensitive components |
Multimeter | Testing the functionality of harvested electronic components |
Anti-static Wrist Strap | Preventing static damage to sensitive components |
What are the Economic Benefits of Parts Harvesting?
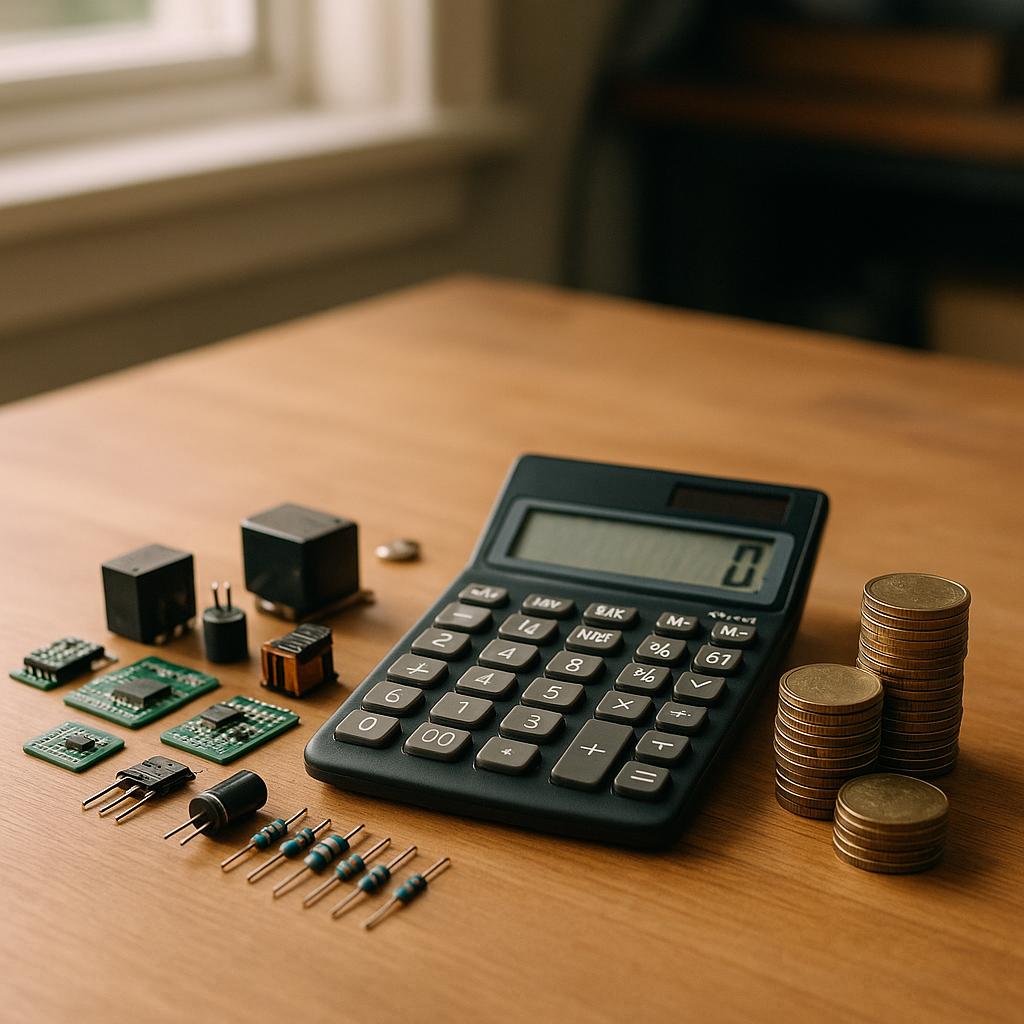
Parts harvesting delivers substantial cost savings across various sectors. Organizations can reduce procurement expenses by reusing components from obsolete or retired equipment instead of purchasing new ones. This is particularly beneficial for high-value items like microprocessors, memory modules, and specialized chips, which are often expensive.
The financial benefits are even more evident when considering energy conservation. Manufacturing new electronic components is highly resource-intensive. For instance, producing a single 300mm semiconductor wafer requires between 1,500 to 2,500 kWh of energy. By reusing existing components, businesses can avoid these significant energy costs and reduce their environmental impact.
For budget-conscious operations, harvested components offer an affordable alternative to original equipment manufacturer (OEM) parts. This cost-effective approach extends the operational life of existing systems. Many organizations find that a strategic parts harvesting program can significantly optimize IT budgets while maintaining performance.
Component reuse also creates business opportunities in the recycling and refurbishment sectors. Companies specializing in electronic component reclamation provide valuable services to organizations looking to maximize hardware investments. These providers use techniques like selective removal of soldered components, reconditioning of leads and pads, and comprehensive testing to ensure reliability.
The economic equation of parts harvesting is especially favorable for high-value components. While harvesting basic components might not always yield positive returns, reclaiming sophisticated items like AI chips and specialized microcontrollers typically offers significant cost savings. Even when accounting for the labor involved in extraction and reconditioning, the savings compared to new manufacturing are substantial.
Beyond direct savings, parts harvesting supports circular economic models that reduce waste management costs. By diverting usable components from waste streams, organizations can minimize disposal expenses. This approach aligns economic benefits with environmental responsibility, providing a sustainable way to manage electronic resources.
Market demand for reclaimed components is growing as more businesses recognize their value. The industry is developing standardized practices to ensure quality and reliability, further enhancing the economic viability of harvested parts. As these standards evolve, buyer confidence rises, expanding market opportunities for recycled components.
From small repair operations to large-scale manufacturing, parts harvesting offers scalable economic benefits. The practice creates employment opportunities due to the specialized, often manual nature of component recovery work. This labor-intensive aspect is not just a cost but an investment in skilled technical jobs within the growing circular economy.
Component Type | Labor Time | Average Cost |
---|---|---|
Chip Components | 8 minutes/component | $14.00/component |
Through-Hole Components | 34 minutes/component | $59.50/component |
SMT Components, up to 10 leads | 19 minutes/component | $33.25/component |
SMT Components, greater than 10 leads | 25 minutes/component | $43.75/component |
BGA Components, up to 100 balls | 27 minutes/component | $47.25/component |
BGA Components, greater than 100 balls | 35 minutes/component | $61.25/component |
How Does Parts Harvesting Support Sustainability?
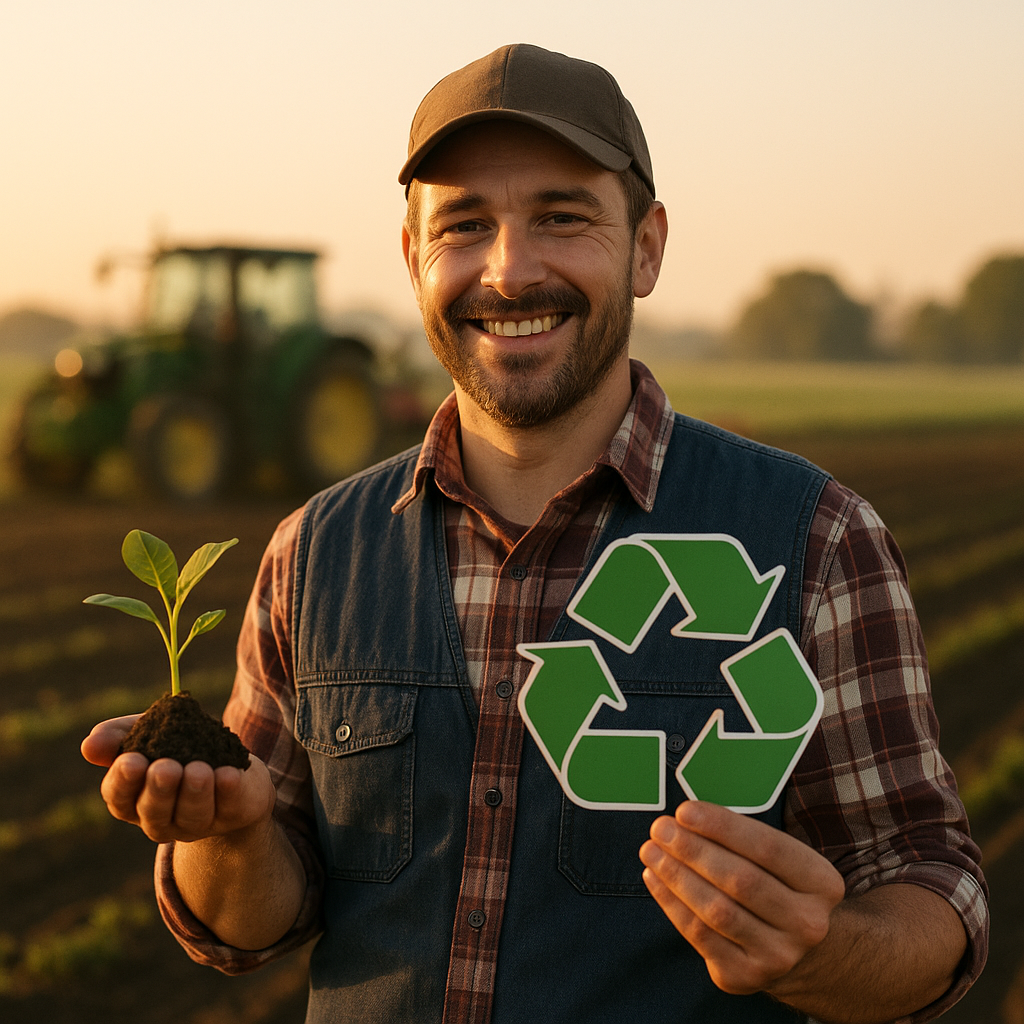
Electronic parts harvesting is one of the most impactful methods for addressing the growing e-waste crisis. The world generated 62 million metric tons of electronic waste in 2022, and projections suggest this could reach 82 million tons by 2030. Harvesting valuable components from discarded devices offers several sustainability benefits beyond waste reduction.
The environmental advantages of electronics parts harvesting are substantial. Recovering components from end-of-life devices requires minimal additional processing compared to producing new parts. This direct reuse approach significantly reduces the carbon footprint associated with electronic components. Industry estimates show that manufacturing a single 300 mm semiconductor wafer consumes between 1,500 to 2,500 kWh of energy. Harvesting and reusing components completely bypasses this energy-intensive process.
Parts harvesting supports sustainability through several key mechanisms:
Resource Conservation and Reduced Raw Material Extraction
Electronic devices contain valuable materials, including gold, silver, palladium, copper, and rare earth elements. By harvesting and reusing components, we reduce the need for mining these finite resources. The U.S. Geological Survey estimates that recycling one million laptops can save enough energy to power over 3,500 homes. Similarly, recovering components from one million recycled phones can reclaim approximately 35,000 pounds of copper, 772 pounds of silver, 75 pounds of gold, and 33 pounds of palladium.
For high-value components like microprocessors, memory modules, and power supplies, harvesting extends their useful life beyond the original device’s lifespan. This is especially valuable for standardized components that can be easily reintegrated into new products or repair operations.
Reduction of Toxic Waste in Landfills
Electronic components often contain hazardous materials such as lead, mercury, and cadmium. When electronics end up in landfills, these substances can leach into soil and groundwater, creating serious environmental and health issues. Parts harvesting prevents these toxic materials from contaminating ecosystems by keeping them in productive use.
According to the United Nations, less than a quarter of the world’s e-waste was properly collected and recycled in 2022, with electronic waste rising five times faster than documented recycling efforts. Component harvesting helps address this alarming gap by redirecting valuable parts back into the supply chain.
Energy and Emissions Savings
Manufacturing new electronic components is energy-intensive and generates significant greenhouse gas emissions. Recycling aluminum, commonly found in many electronic components, saves up to 95% of the energy required to produce it from raw bauxite ore. Similar efficiency gains apply to other metals and materials found in electronic parts.
The energy savings from parts harvesting extend beyond manufacturing. When components are recovered locally, they eliminate the carbon emissions associated with the global shipping of new parts, further reducing the overall environmental footprint.
Support for Circular Economy Principles
Parts harvesting embodies circular economy principles by keeping resources in use for as long as possible, extracting maximum value before recovery and regeneration. This approach transforms the traditional linear model of “take-make-dispose” into a sustainable cycle that minimizes waste and maximizes resource efficiency.
Component harvesting creates additional value streams within the electronics industry. Recovered parts can be used in refurbishment operations, repair services, or as inputs for new manufacturing. This not only reduces waste but also creates economic opportunities and green jobs in the collection, processing, and remanufacturing sectors.
As technology continues to advance, parts harvesting is a critical strategy for building a more sustainable electronics ecosystem. By extending component lifespans and reducing the environmental burden of manufacturing, this practice helps bridge the gap between our growing technological needs and the planet’s finite resources.
Tool/Technique | Application |
Heat sources | Melting solder joints with soldering irons, heat guns, or butane torches. |
Desoldering equipment | Removing melted solder using desoldering pumps and braids. |
Hand tools | Handling and removing components using pliers, tweezers, and wire cutters. |
Safety equipment | Protecting yourself and components with anti-static wrist straps, safety glasses, and good ventilation. |
Organizational containers | Sorting and storing recovered parts in small jars, compartment boxes, or anti-static bags. |
Cleaning supplies | Removing flux residue after component removal with isopropyl alcohol and brushes. |
What Challenges Face Electronics Parts Harvesting?
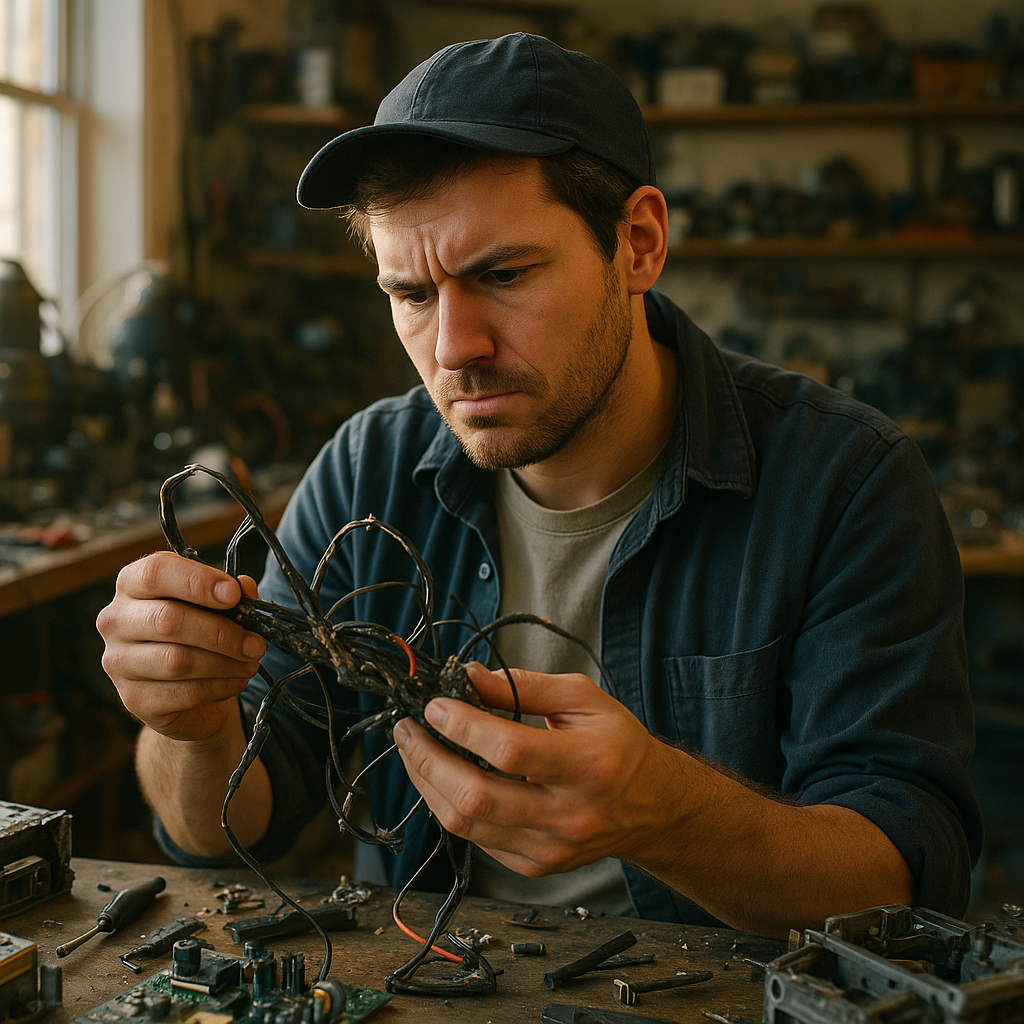
Despite the environmental and economic benefits, electronics parts harvesting faces significant hurdles that limit widespread adoption. The practice requires overcoming technical, reliability, and industry perception challenges to reach its full potential in the circular economy.
Technical Complexity and Removal Risks
Modern electronics are increasingly integrated and miniaturized, making component extraction more difficult than ever. Many devices now feature surface-mount technology with components soldered directly to circuit boards, rather than using traditional through-hole connections. This integration creates significant challenges during the removal process.
The risk of damage during extraction is substantial. Heat application during desoldering can compromise semiconductor functionality, while mechanical removal methods may cause physical damage to delicate pins and connections. Even minor damage can render an otherwise functional component unusable or unreliable in its second application.
Components with thermal paste or adhesives present additional difficulties, as residue removal without damaging the part requires specialized techniques and equipment. Each component type demands specific handling protocols to maintain functionality during the harvesting process.
Reliability Concerns and Testing Limitations
Component reliability is perhaps the most significant barrier to widespread parts harvesting adoption. Unlike new components with manufacturer specifications and testing documentation, harvested parts come with unknown usage histories and potential hidden defects.
Testing harvested components presents unique challenges. While basic functionality testing can identify catastrophic failures, it often cannot detect components operating at the edge of their specifications or with reduced lifespans. Components that have experienced thermal stress or voltage events may work initially but fail prematurely in new applications.
The lack of standardized testing protocols specifically developed for harvested components contributes to uncertainty. Manufacturers accustomed to components with clear specifications and warranties must navigate these uncertainties when considering reclaimed parts.
Documentation and Traceability Issues
Effective parts harvesting requires robust documentation throughout the process. However, tracking component origins, usage history, and extraction methods is challenging without established systems. This lack of traceability creates barriers to quality assurance.
The absence of uniform documentation standards makes it difficult for harvesting operations to communicate component specifications consistently. Potential users of harvested parts need clear information about component origins, previous applications, and remaining useful life to make informed decisions.
Supply chain management systems designed for new components often struggle to accommodate harvested parts with their unique documentation requirements. This integration gap limits the potential market for reclaimed components in formal manufacturing processes.
Challenge | Description | Potential Solutions |
---|---|---|
Technical Complexity | Modern electronics have integrated and miniaturized components, making extraction difficult. | Development of specialized equipment for non-destructive removal; automated systems for component assessment. |
Reliability Concerns | Harvested parts come with unknown histories and potential defects, with limited testing protocols. | Establish standardized testing protocols; advanced analysis techniques for assessing component stress levels. |
Documentation and Traceability | Challenges in tracking component origins and usage history due to lack of established systems. | Implement data management systems for detailed tracking; set uniform documentation standards. |
Industry Acceptance | Manufacturers have concerns over the reliability of harvested components. | Develop industry standards and certification programs for harvested components. |
Industry Acceptance and Standard Development
Gaining industry acceptance remains a significant hurdle. Manufacturing sectors with stringent reliability requirements have valid concerns about incorporating harvested components into their production lines. Without established standards, many manufacturers default to new components despite potential cost savings.
The electronics industry has begun addressing these challenges through standard development efforts. Organizations are working to establish testing protocols, quality metrics, and documentation requirements specifically for harvested components. These emerging standards aim to build confidence in component reliability while acknowledging the unique nature of reclaimed parts.
Several industry groups have initiated certification programs for harvested components, providing a framework for quality assurance. These programs typically include testing requirements, documentation standards, and traceability guidelines to build trust in reclaimed parts. While still evolving, these efforts represent important steps toward broader industry acceptance.
Overcoming Harvesting Challenges
Despite these obstacles, innovations in harvesting techniques are advancing the field. Specialized equipment for non-destructive removal has improved success rates for complex components. Automated systems can now assess components during extraction, reducing the risk of damage while enhancing efficiency.
Testing methodologies are evolving to address the unique needs of harvested components. Advanced analysis techniques can evaluate component stress levels and predict remaining useful life more accurately than traditional testing. This approach helps bridge the gap between new and harvested component reliability assessment.
Data management systems designed specifically for harvested components are improving traceability. These systems track component origins, usage conditions, and testing results throughout the harvesting process. The resulting documentation provides potential users with comprehensive information about component history and condition.
Conclusion: The Future of Electronics Parts Harvesting
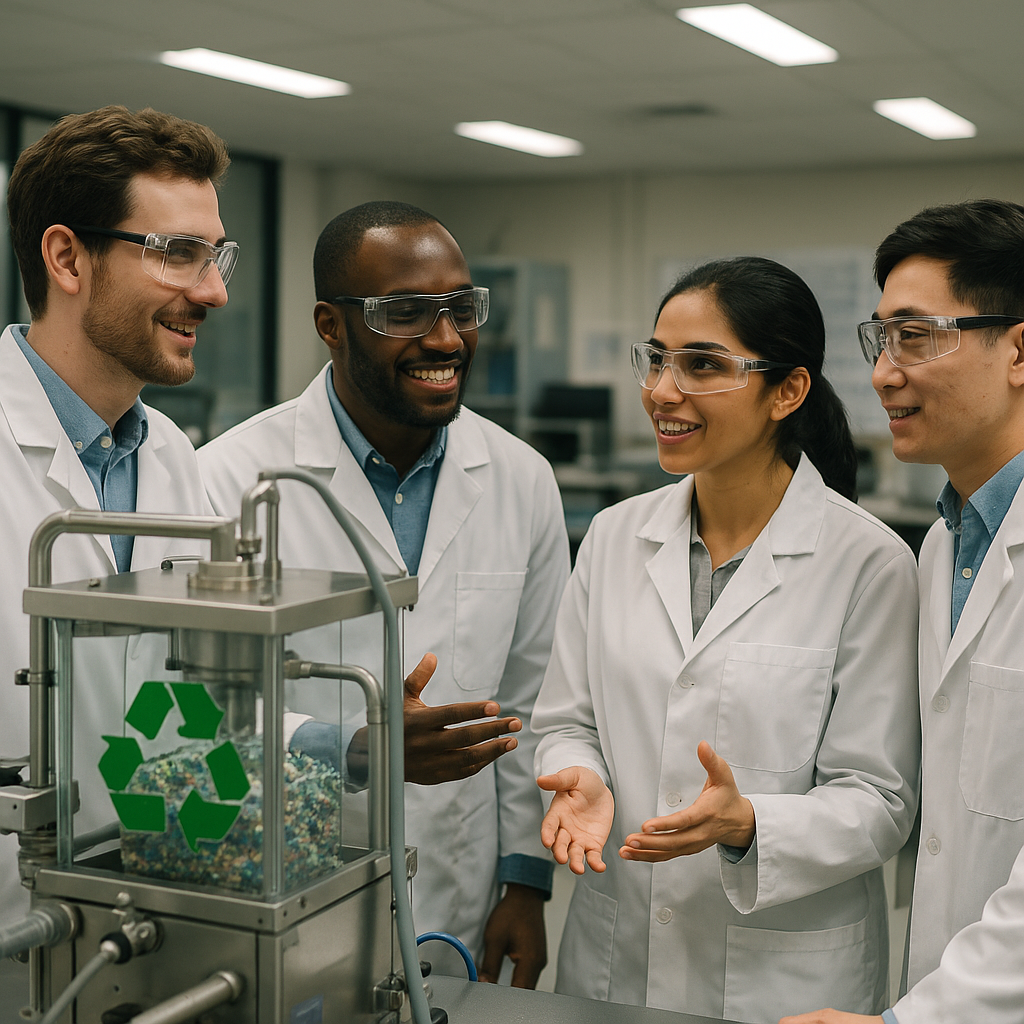
Electronics parts harvesting is at the forefront of sustainable waste management solutions. The practice transforms what was once seen as waste into valuable resources, creating significant economic opportunities. With the global electronics recycling market projected to reach $98.6 billion by 2032, component harvesting from discarded devices will be crucial to meeting sustainability demands and tackling e-waste challenges.
As we progress toward a more circular economy, electronics parts harvesting will evolve through innovations in recycling technology. Advances in automated disassembly, biometallurgy for eco-friendly metal extraction, and improved recovery of rare earth elements will enhance process efficiency. The future envisions harvesting as a standard practice that supports environmental goals and economic growth in the recycling sector.
Want to contribute to the electronics recycling landscape? Contact Okon Recycling at 214-717-4083 for expert guidance on sustainable parts harvesting for your business or organization.