5901 Botham Jean Blvd, Dallas, TX 75215
Discover the Average Cost to Dispose of Construction Materials?
July 20, 2025In 2024, construction waste disposal costs range from $66.70 to $78.00 per cubic yard on average. This pricing reflects the specialized handling and processing needed for construction and demolition materials. Concrete, bricks, scrap metal, and lumber each require different disposal methods, contributing to these costs.
Construction waste management expenses vary significantly across the country. Pricing is influenced by geographical location, total waste volume, and the types of materials being disposed of. Urban areas typically have higher disposal fees due to limited landfill space and stricter regulations, while rural locations may offer more affordable rates.
For smaller construction projects or partial loads, expect to pay between $15 and $30 per cubic yard. Many disposal facilities also implement minimum charges ranging from $40 to $51 depending on the region, ensuring operational costs are covered even for minor disposal needs. Understanding these baseline costs helps contractors and property owners budget effectively for waste management.
How Are Construction Waste Disposal Costs Calculated?
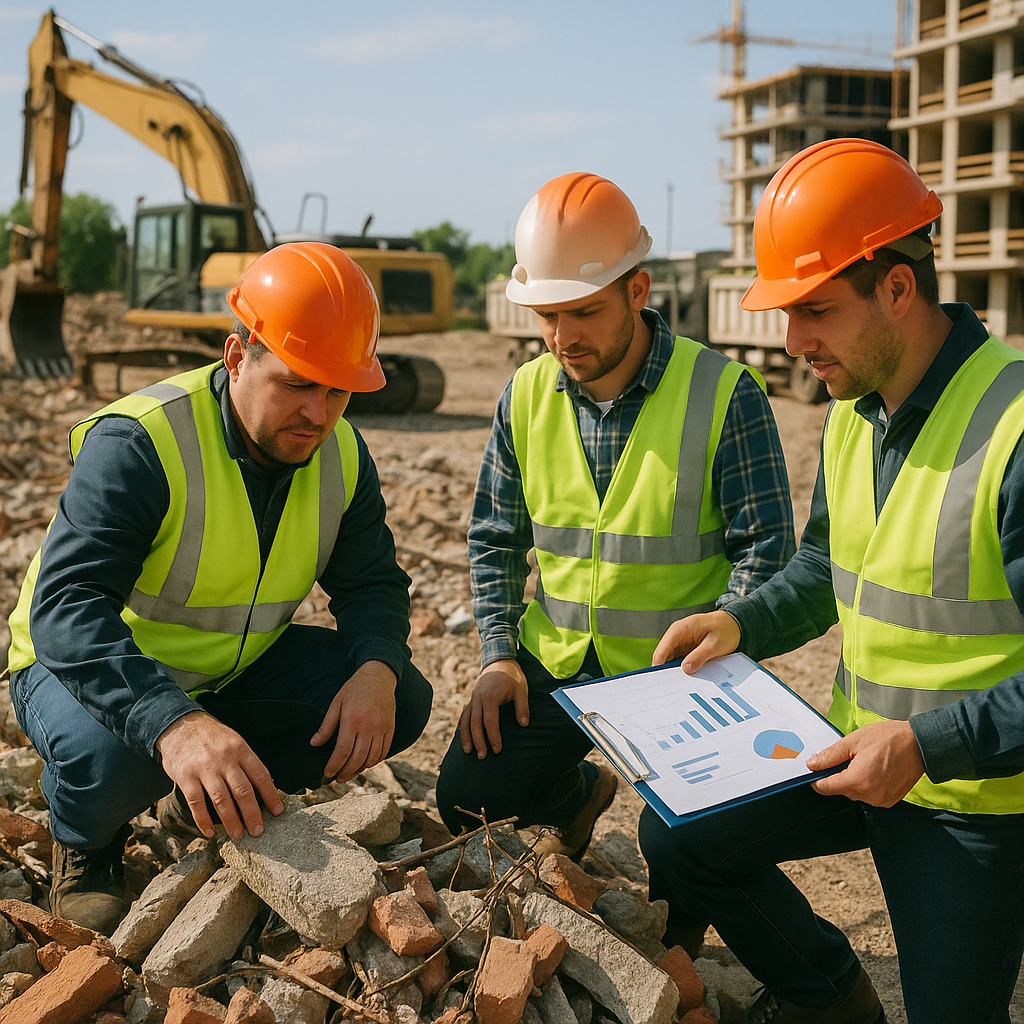
Construction waste disposal costs are calculated primarily based on the volume or weight of debris removed. Unlike other construction expenses estimated per square foot, waste disposal focuses on the actual amount of waste generated. This method provides a more accurate representation of the true cost associated with managing construction debris.
The basic formula for calculating construction waste disposal costs is straightforward: Removal Cost = (Volume or Weight) × Rate + Labor. This formula considers both the physical amount of waste and the human effort required to manage it. Understanding this calculation helps contractors and project managers budget more effectively for waste management.
Volume-Based Pricing
Volume-based pricing uses standardized container sizes to determine costs. Companies often charge fixed rates for different dumpster sizes, ranging from 10 to 40 cubic yards, regardless of the material’s density. Volume is typically measured in cubic yards, with one cubic yard being roughly the size of a washing machine. This method is commonly used for mixed construction waste.
With volume-based pricing, contractors pay for the space their waste occupies rather than its actual weight. This can be advantageous for projects generating large amounts of lightweight materials like wood scraps or packaging. However, it may not be as cost-effective for denser materials like concrete or brick.
Weight-Based Pricing
With weight-based pricing, disposal facilities charge by the ton. This method more accurately represents the true cost of waste management since landfill tipping fees are typically weight-based. Weight measurements are calculated in tons and are particularly relevant for heavier materials such as concrete, bricks, and soil.
Weight-based pricing provides a clearer cost signal and helps companies budget more accurately. It is especially beneficial when dealing with recyclable materials, as many recycling facilities charge based on the weight of materials processed. This approach aligns costs directly with the physical burden placed on disposal facilities.
Key Factors Affecting Disposal Costs
- Volume and Weight of Debris: The amount of waste directly impacts costs. Heavier materials like concrete and bricks cost more to dispose of than lighter materials like wood or drywall.
- Type of Waste: Different materials require different handling methods. Hazardous materials, such as asbestos or those containing lead paint, require specialized disposal methods and permits, significantly increasing costs.
- Recyclability: Recyclable materials might cost less to dispose of or even generate returns in some cases. Metal, clean wood, and concrete can often be recycled, potentially reducing overall expenses.
- Project Size: Larger projects typically generate more waste, increasing total costs. However, bulk rates may apply, reducing per-unit disposal expenses.
- Location: Projects in urban areas often face higher disposal costs due to limited landfill space and stricter regulations. Distance to disposal facilities also matters, as remote projects require longer transportation routes.
- Local Regulations: Disposal fees vary significantly by region. Some municipalities impose additional taxes or fees on construction waste.
Construction companies can optimize waste disposal costs by accurately estimating the volume or weight of expected debris before starting a project. Using standardized containers and separating recyclable materials can also lead to significant savings. Regular monitoring of waste generation throughout the project allows for adjustments to disposal strategies as needed.
Understanding how disposal costs are calculated empowers project managers to make informed decisions about waste management approaches. This knowledge can lead to more accurate budgeting and potentially significant cost savings throughout the construction process.
Material Type | Cost per Cubic Yard | Cost per Ton |
---|---|---|
General Construction Debris | $66.70 – $78.00 | N/A |
Concrete | N/A | $114.91 |
Bricks | N/A | $114.91 |
Metal | Recyclable – Potential Returns | N/A |
Wood | Recyclable – Potential Returns | N/A |
Hazardous Materials (Asbestos, Lead Paint) | Specialized Disposal Required | Specialized Disposal Required |
What Are the Different Types of Construction Waste and Their Disposal Costs?
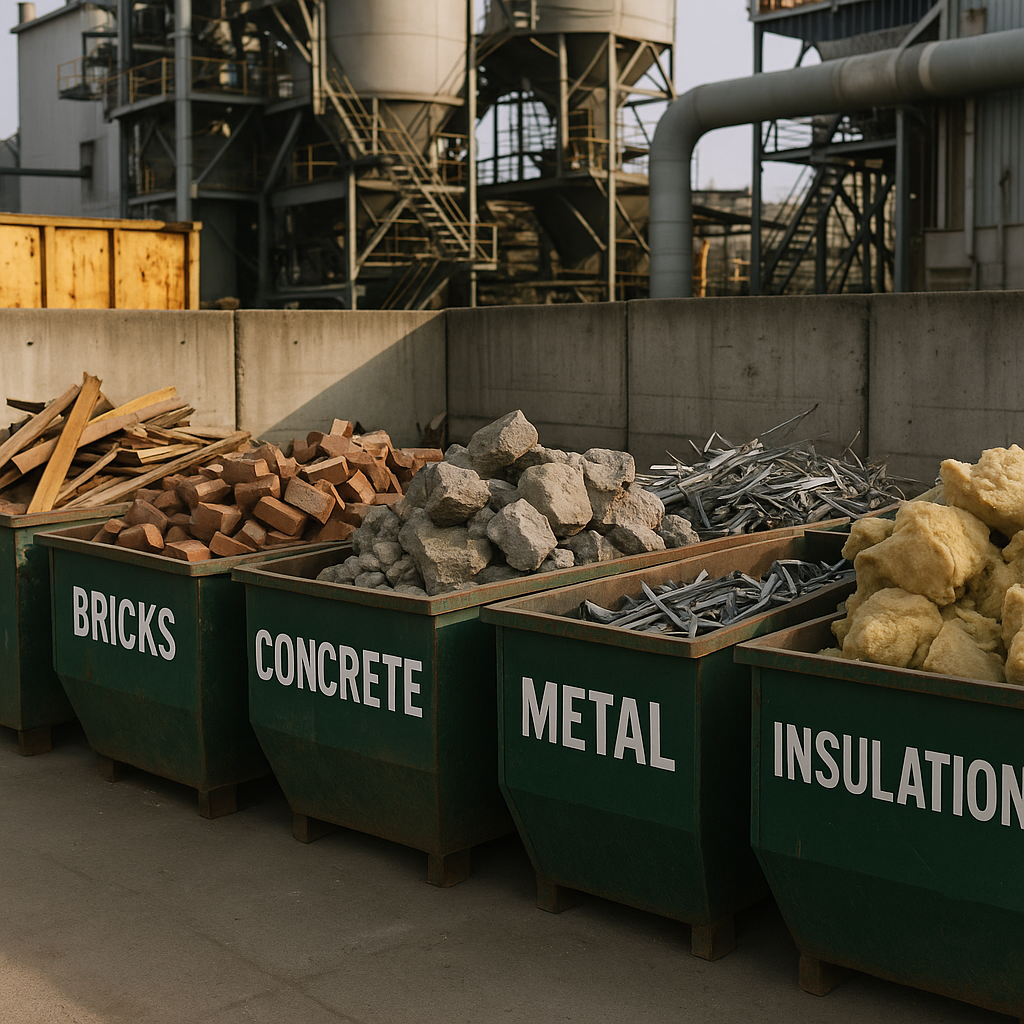
Construction and demolition (C&D) waste makes up a significant portion of waste streams, with disposal costs varying widely based on material type and local regulations. Understanding these costs is essential for effective waste management planning and savings through recycling options.
Common Construction Waste Materials and Their Disposal Costs
Construction projects generate diverse waste streams, each with distinct handling requirements and costs. Properly categorizing these materials is the first step toward cost-effective disposal management.
General construction debris typically costs between $66.70 and $78.00 per cubic yard for standard disposal. This category includes mixed materials commonly found on construction sites that don’t require specialized handling. For larger projects, costs may be calculated by weight rather than volume, with some facilities charging $40 to $60 per ton.
Heavy materials like concrete and bricks are usually priced differently due to their weight and processing requirements. These materials cost approximately $114.91 per ton for disposal. However, when recycled, concrete can be crushed and repurposed as aggregate for new projects, potentially reducing expenses.
Wood waste varies in disposal costs depending on its treatment status. Untreated wood can often be recycled as mulch or biomass fuel, while treated wood requires more careful handling due to chemical content. Recycled wood products in the U.S. market can sell for $5.00 to $17.50 per ton when used as cogeneration fuel.
Metal waste is among the most valuable recyclable materials from construction sites. Scrap metal dealers often pay for materials like copper wiring, steel beams, and aluminum siding, generating returns rather than expenses. This makes metal separation financially advantageous on construction sites.
Material Type | Cost per Cubic Yard | Cost per Ton |
---|---|---|
General Construction Debris | $66.70 – $78.00 | N/A |
Concrete | N/A | $114.91 |
Bricks | N/A | $114.91 |
Metal | Recyclable – Potential Returns | N/A |
Wood | Recyclable – Potential Returns | N/A |
Hazardous Materials (Asbestos, Lead Paint) | Specialized Disposal Required | Specialized Disposal Required |
Hazardous Construction Waste and Specialized Disposal
Hazardous construction waste requires specialized handling and disposal methods that significantly increase costs due to their environmental and health risks.
Asbestos-containing materials (ACM) must be removed by qualified personnel with appropriate protective equipment. The disposal costs for asbestos waste can range from $75 to over $200 per cubic yard depending on the region. Federal regulations require specific handling procedures when disturbing certain amounts of asbestos.
Lead-based paint (LBP) waste must be tested using the Toxicity Characteristic Leaching Procedure (TCLP) to determine if it qualifies as hazardous waste. If lead concentrations exceed regulatory thresholds, specialized disposal is required, potentially costing two to three times more than standard construction waste disposal.
Other hazardous materials commonly found in construction waste include mercury from fluorescent lighting, PCBs from old transformers and capacitors, and chemically treated lumber. Each requires specific handling protocols and disposal at permitted facilities, with costs reaching $250 to $500 per ton.
Recycling Options and Cost Savings
Recycling strategies for construction waste can significantly reduce disposal expenses while supporting sustainability goals. The economics of recycling improve in areas with high landfill tipping fees.
On-site material separation increases the value of recyclables, though it adds labor costs of about $1 to $2 per square foot of building area, often offset by reduced disposal fees and potential revenue from recyclables.
Concrete recycling represents a major opportunity for cost savings. Recycled concrete aggregate can be used for road base, with U.S. sales prices ranging from $2.76 to $6.70 per ton. Crushing concrete on-site eliminates hauling and dumping charges while providing usable fill material.
Wood recycling can transform waste into marketable products. Clean, untreated wood can be processed into mulch, animal bedding, or biomass fuel. Even with processing costs, recycling wood typically costs less than landfill disposal in regions with high tipping fees.
Metal recycling nearly always provides financial benefits. Separating high-value metals like copper and aluminum from general debris can generate significant returns. Even structural steel and rebar have established recycling markets that offset disposal costs.
Regional Variations in Disposal Costs
Construction waste disposal costs vary by location, influenced by local regulations, landfill capacity, and market conditions for recycled materials.
Urban areas typically have higher disposal costs due to limited landfill space and stricter regulations. In densely populated regions like northern New Jersey, tipping fees can exceed $140 per ton. This makes recycling more economically attractive in these areas.
Rural locations generally have lower disposal costs, with some areas charging as little as $20 per ton for construction debris. The economics of recycling may be less favorable here unless materials have high intrinsic value.
Transportation distance significantly impacts total disposal costs. Each kilometer that aggregates are hauled can add 10 to 20 cents per ton to costs. Local recycling options are more appealing when available, especially for heavy materials like concrete.
By understanding the disposal costs for different types of construction waste and exploring recycling options, project managers can make informed decisions that reduce expenses while promoting sustainable practices. In many cases, the most cost-effective approach combines selective recycling of high-value materials with efficient disposal of remaining waste.
What Additional Fees and Charges Should Be Considered?
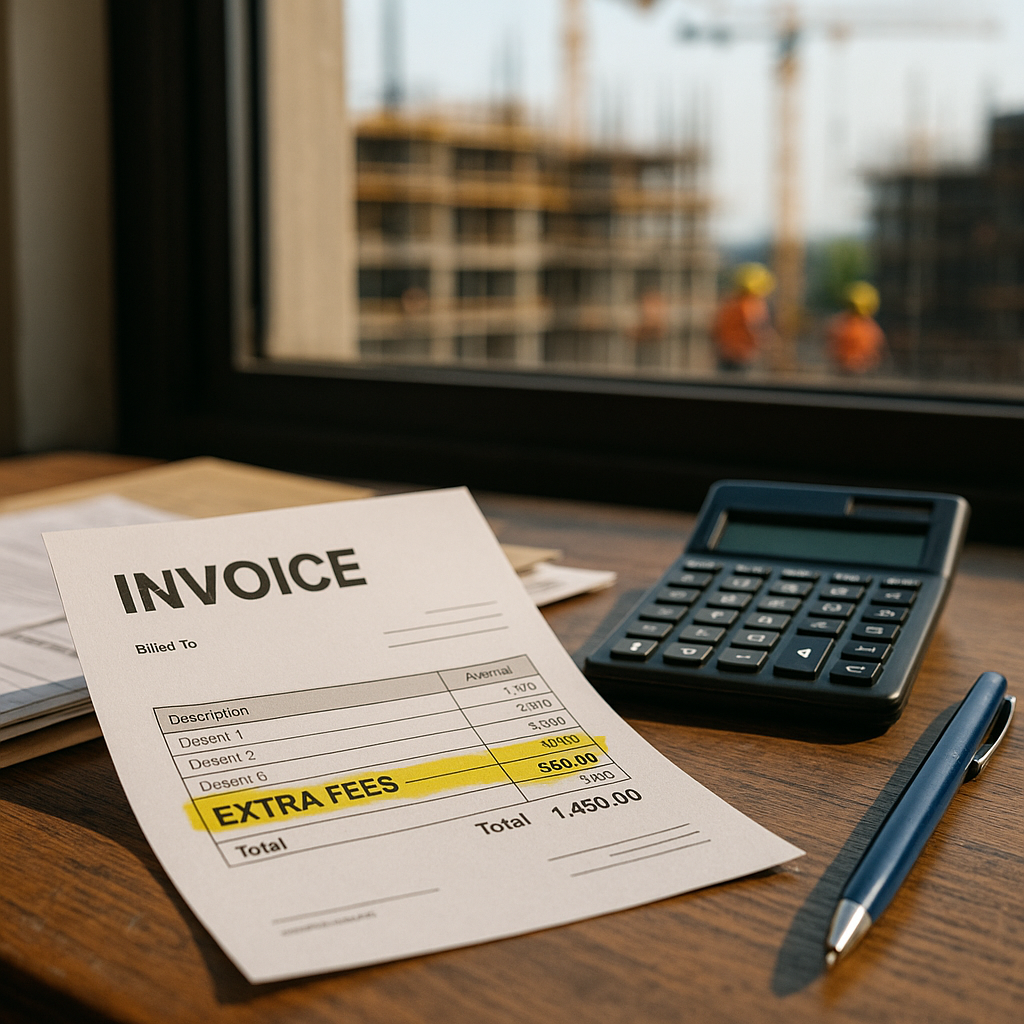
When planning waste disposal, the base cost is just the beginning. Several additional fees can significantly impact your final bill if you don’t account for them in advance. Understanding these potential charges helps you create a more accurate budget and avoid unforeseen expenses.
Dumpster rental services often include various supplementary fees not typically anticipated by customers. Similarly, junk removal companies and landfills have their own set of charges beyond the basic service cost. Let’s explore these additional expenses in detail.
Common Additional Disposal Fees
- Dumpster rental charges: Expect to pay between $300 and $500 for a standard dumpster rental, which usually includes a specified rental period (typically 7-10 days) and a weight allowance.
- Junk removal services: Professional junk hauling ranges from $100 to $800, depending on volume and type of waste. Prices increase with the amount of truck space your debris occupies.
- DIY landfill disposal: If you transport waste yourself, landfill fees generally run $20 to $50 per ton, with minimum charges often applying regardless of weight.
- Overweight fees: Exceeding your dumpster’s weight limit can trigger charges of $50 to $250 per additional ton.
- Rental extension fees: Keeping a dumpster beyond the included rental period typically costs $15 to $50 per additional day.
- Trip fees: If a disposal company arrives for pickup but can’t access the dumpster or finds it improperly loaded, you may face trip fees of $195 to $350.
Special Material Handling Charges
Certain waste types require special processing, resulting in additional charges. These materials often can’t be mixed with regular waste and may need separate containment or processing.
- Hazardous waste: Materials like paint, chemicals, batteries, and electronics incur surcharges of $25 to $200 per item for proper disposal.
- Mattresses and furniture: Large bulky items typically cost $75 to $150 each for proper disposal due to their size and difficulty in compacting.
- Appliances: Items containing refrigerants (like air conditioners and refrigerators) often require an additional $50 to $150 for environmentally safe processing.
- Construction debris: Some localities charge special rates or taxes for construction and demolition waste.
Location-Based Additional Charges
Your geographical location can introduce several other cost factors affecting your final waste disposal bill.
- Transportation surcharges: Remote locations often incur additional fees to cover the increased travel distance for service vehicles.
- Permit fees: Placing a dumpster on public property like streets or sidewalks typically requires a permit costing $10 to $100 per week, depending on the municipality.
- Local taxes and environmental fees: Many jurisdictions impose special waste taxes or environmental recovery fees that are passed on to customers.
- Seasonal charges: In colder climates, winter conditions can lead to “dig out fees” of $75 to $150 if waste freezes to the container.
Planning for these potential charges helps create a realistic waste disposal budget. Before booking any service, ask for a complete breakdown of all possible fees and understand what triggers them. Many companies will work with you to find the most cost-effective solution if you discuss your specific needs upfront.
Remember that the lowest quoted price isn’t always the best deal if it excludes potential additional charges. Factor these costs into your project planning to avoid budget surprises and ensure smooth waste management throughout your project.
Fee Type | Description | Cost Range |
Dumpster Rental | Standard rental period with weight allowance | $300 – $500 |
Junk Removal | Based on volume and type of waste | $100 – $800 |
DIY Landfill Disposal | Self-transport to landfill | $20 – $50 per ton |
Overweight Fees | Exceeding dumpster limits | $50 – $250 per additional ton |
Rental Extension | Extra day beyond rental period | $15 – $50 per day |
Trip Fees | Access issues or improper loading | $195 – $350 |
Hazardous Waste | Processing for special waste | $25 – $200 per item |
Bulky Items | Disposal of large items like furniture | $75 – $150 each |
Appliances | Processing for refrigerant-containing items | $50 – $150 each |
Transportation Surcharges | Fees for remote locations | Varies |
Permit Fees | For public property placements | $10 – $100 per week |
How Can Construction Companies Reduce Waste Disposal Costs?
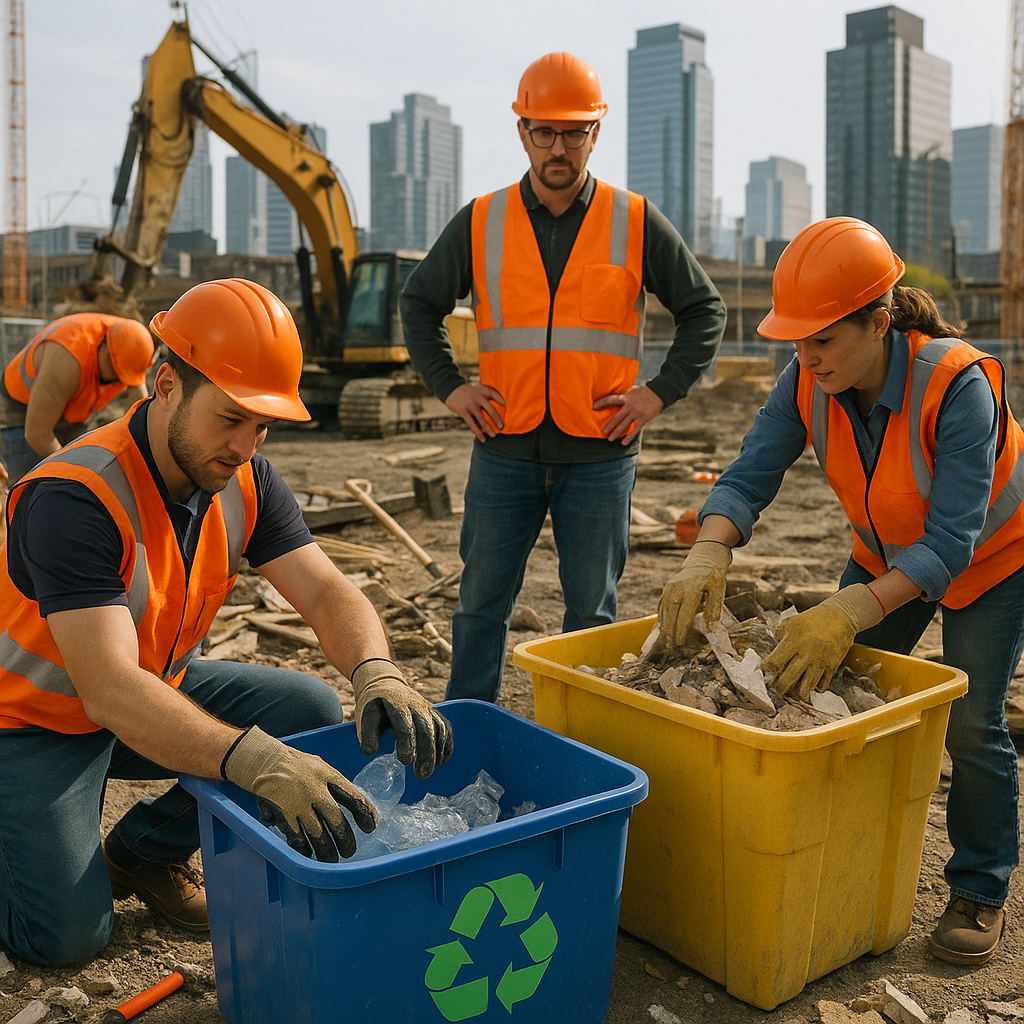
Construction and demolition waste make up nearly a quarter of the annual waste in the United States. Reducing disposal costs provides a significant opportunity for construction companies to boost profit margins. The construction industry produces approximately 600 million tons of waste annually, much of which ends up in landfills at considerable cost. Implementing strategic waste management practices can substantially lower these expenses.
Implement On-Site Recycling Systems
On-site recycling systems enable materials to be sorted and processed directly at the construction site, eliminating transportation costs for many materials and creating immediate savings. Designate specific collection areas for different recyclable materials like concrete, wood, metal, and drywall.
Source separation—sorting waste where it’s generated—is particularly effective. This approach reduces contamination between materials and increases their recyclability value. Workers can easily separate recyclable materials from non-recyclable waste when proper bins and clear signage are provided throughout the site.
For concrete and asphalt, consider on-site crushing equipment that converts these materials into usable aggregate for road bases or new concrete mixtures. This eliminates disposal fees while creating valuable building materials for current or future projects.
Adopt Lean Construction Methods
Lean construction techniques focus on minimizing waste by improving efficiency throughout the building process. This approach reduces both material waste and labor costs. Just-in-time purchasing prevents excess materials from accumulating on-site, which often end up as waste.
Better site management also plays a crucial role in waste reduction. According to industry data, construction site labor inefficiency totaled approximately $177 billion in 2018. Improving workflows, communication, and training helps reduce material waste while increasing overall productivity.
Material optimization software can help calculate precise material needs, reducing over-ordering that leads to excess waste. These tools analyze building plans to determine the most efficient use of materials with minimal scrap.
Develop a Comprehensive Waste Management Plan
Creating a detailed waste management plan before starting a project helps identify opportunities for waste reduction and cost savings. This plan should include waste audits to understand what types of waste your sites generate most frequently.
Train workers on proper material handling and waste sorting procedures. When everyone understands the economic and environmental benefits of proper waste management, compliance improves significantly. Regular training sessions keep waste management priorities top of mind.
Choose building products with minimal packaging or packaging that can be returned to suppliers. Some manufacturers offer take-back programs for packaging materials or unused products, which can significantly reduce disposal costs.
Explore Innovative Recycling Technologies
New recycling technologies make it possible to process previously difficult-to-recycle construction materials. Gypsum from drywall can now be extracted and recycled into new drywall products, with some manufacturers offering boards containing up to 96% recycled content.
Crushed glass from damaged windows can be processed into “glassphalt” for use in road construction or as decorative aggregate. Wood waste can be converted into engineered wood products, mulch, or biomass fuel.
Partnering with specialized recycling facilities that handle construction materials can open new avenues for waste diversion. These facilities often accept mixed construction waste and manage the sorting process, although separation at the source typically yields better financial returns.
Cost Component | Description | Cost Range (CAD) |
---|---|---|
Total Construction Costs | Average total building cost for a house | 97,535.21 |
Savings from Waste Reduction | Potential savings per house from effective waste reduction strategies | 2,717.05 |
Minimum Waste Cost | Minimum estimated waste-related costs per house | 1,196.10 |
Average Waste Cost | Average estimated waste-related costs per house | 1,956.72 |
Maximum Waste Cost | Maximum estimated waste-related costs per house | 2,717.34 |
Transport Costs | Average transportation costs per house | 169.45 |
Disposal Fees | Average landfill disposal fees per house | 221.08 |
Reuse and Repurpose Materials
Salvaging materials from demolition sites for reuse in new construction creates significant savings. Reclaimed wood, bricks, fixtures, and architectural elements often have higher value than new materials due to their unique character.
Establish material storage areas on larger projects to save usable materials for later phases. Items like excess lumber cuts, drywall pieces, and tile can often find uses elsewhere in the project rather than becoming waste.
For materials you cannot use, consider selling or donating them. Organizations like Habitat for Humanity ReStore accept construction materials donations, which can qualify for tax deductions while reducing disposal costs.
By implementing these strategies, construction companies can significantly reduce waste disposal expenses while supporting environmental sustainability. The initial investment in better waste management systems typically pays for itself through reduced disposal fees, material savings, and improved operational efficiency.
Conclusion: Balancing Cost and Environmental Responsibility in Construction Waste Disposal
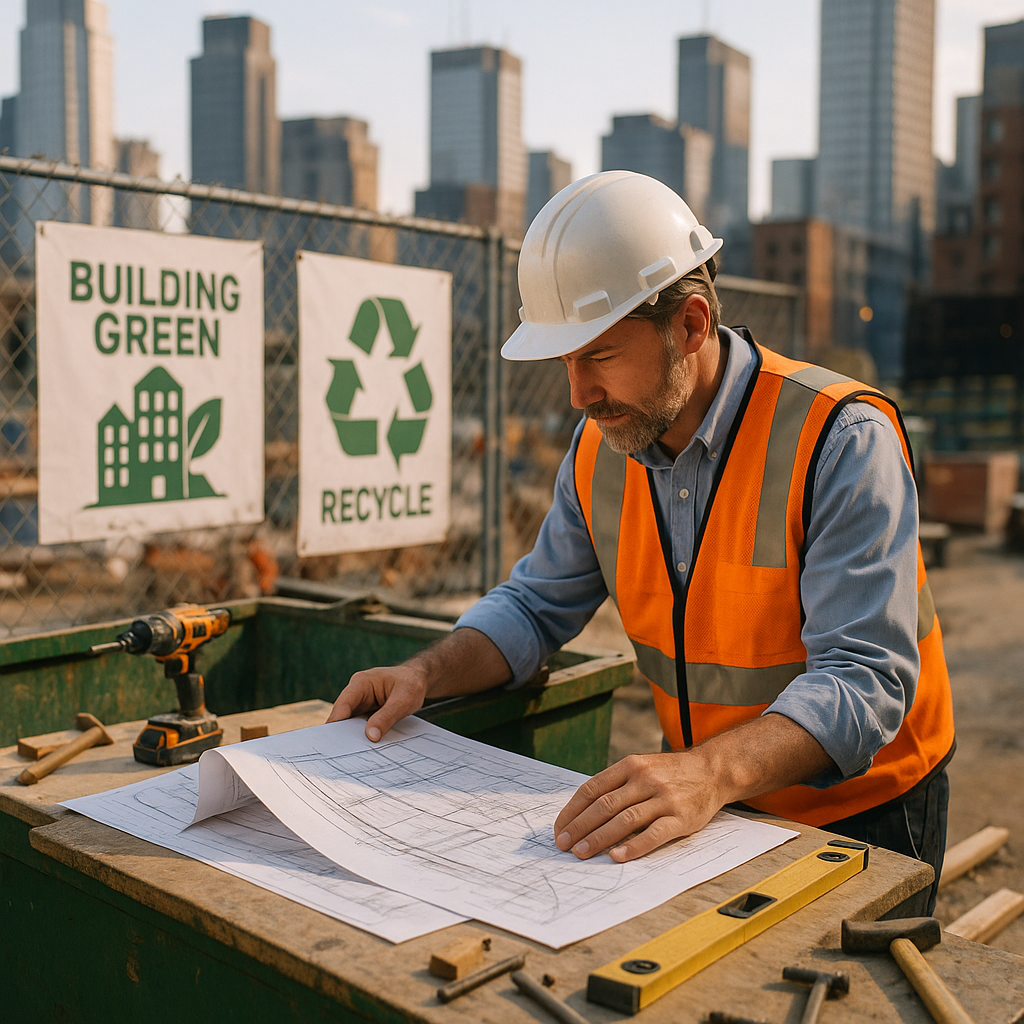
Managing construction waste disposal costs demands a careful balance between financial considerations and environmental responsibility. The construction industry generates approximately 600 million tons of waste annually in the United States alone, presenting both economic and ecological challenges. Successful construction companies understand that effective waste management is not only an environmental obligation but also a financial opportunity.
By implementing strategies such as source reduction, material segregation, and recycling programs, construction firms can significantly reduce disposal fees while conserving valuable resources. Understanding factors like regulatory requirements and transportation logistics helps companies make informed decisions that benefit both their bottom line and the planet. Properly sorted, recycled, and repurposed construction waste transforms from a costly burden into a valuable resource, creating a circular economy that supports sustainability goals and reduces expenses.
For assistance with implementing cost-effective and environmentally responsible waste management solutions for your construction projects, contact Okon Recycling at 214-717-4083.