5901 Botham Jean Blvd, Dallas, TX 75215
Types of Magnets: What Are the Types of Magnets?
May 20, 2025From the speakers in your smartphone to the motors in electric vehicles, magnets are crucial in powering our modern world. These remarkable objects create invisible forces that attract certain metals and generate electrical currents driving countless technologies we rely on daily.
Understanding magnets starts with recognizing their fundamental categories. There are three main types: permanent magnets, temporary magnets, and electromagnets. Each type serves unique functions across various industries and technologies.
The distinction between these magnetic varieties lies in how they generate and maintain their magnetic fields. Some hold their magnetic properties indefinitely, while others require external conditions to produce magnetic effects. These differences make each type suitable for specific applications, from household devices to advanced medical equipment.
What Are Permanent Magnets and Their Types?

Permanent magnets are materials that maintain their magnetic properties for extended periods without needing an external power source. Unlike temporary magnets, which lose their magnetism once removed from a magnetic field, permanent magnets continuously generate their own magnetic field. This persistent magnetism makes them invaluable for countless applications across industries.
Ceramic/Ferrite Magnets
Ceramic magnets, also known as ferrite magnets, are made of iron oxide combined with barium or strontium carbonate. These magnets offer excellent corrosion resistance and work effectively at temperatures up to 300°C.
While they have lower magnetic strength compared to other permanent magnet types, their affordability makes them widely used in consumer applications. Ceramic magnets are a cost-effective option for everyday devices like refrigerator magnets, speakers, and household appliances.
Their brittleness is a notable drawback, but their low price and high availability make them the most commonly used permanent magnets worldwide. They come in different grades (1, 5, and 8), each offering varying magnetic strengths to suit different applications.
Alnico Magnets
Alnico magnets derive their name from their composition: aluminum (Al), nickel (Ni), and cobalt (Co). Small quantities of other elements are added during production to enhance their properties.
These magnets excel in high-temperature environments, functioning reliably at up to 540°C. They exhibit impressive magnetic stability and moderate corrosion resistance. Alnico magnets are produced through either sintering or casting processes.
Common applications include sensors, measuring instruments, and motors where temperature stability is crucial. Their moderate cost and excellent thermal properties make them ideal for specialized industrial applications requiring consistent performance under heat stress.
Samarium Cobalt (SmCo) Magnets
Samarium cobalt magnets belong to the rare earth magnet family. These high-performance magnets offer exceptional corrosion resistance and can withstand temperatures up to 350°C without significant loss of magnetic properties.
SmCo magnets possess a high coercive force, meaning they strongly resist demagnetization. Their main disadvantages are high cost and brittleness, limiting their use to specialized applications.
These magnets are primarily used in aerospace technology, military equipment, and high-temperature motors where their superior performance justifies the expense. Medical devices and precision instruments also benefit from their stability and strength.
Neodymium Iron Boron (NdFeB) Magnets
Neodymium magnets are the strongest type of permanent magnets available today. Composed of neodymium, iron, and boron, these powerful magnets can generate magnetic fields between 1.0-1.4 teslas.
Despite their impressive strength, NdFeB magnets have limitations. They offer lower corrosion resistance unless coated and can only operate at temperatures up to 200°C. They also possess lower mechanical strength compared to other permanent magnets.
Due to their exceptional magnetic properties, neodymium magnets are widely used in electronics, wind turbines, electric vehicle motors, and hard disk drives. Their strength-to-weight ratio makes them ideal for applications where space and weight constraints exist.
The material used to produce neodymium magnets is relatively costly, so they are used selectively where their superior magnetic performance outweighs the price consideration.
Applications Across Industries
Permanent magnets serve crucial functions across numerous sectors. In electrical and electronic devices, they power motors, generators, speakers, and hard drives. Consumer products like refrigerator magnets, door latches, and toys incorporate permanent magnets of varying strengths.
In healthcare, permanent magnets enable MRI machines, hearing aids, and magnetic therapy devices. The transportation industry relies on them for electric vehicle motors, magnetic levitation trains, and fuel sensors.
Industrial applications include magnetic separators, lifting mechanisms, and manufacturing equipment. Even security systems utilize permanent magnets in credit card strips, magnetic locks, and compasses.
Type | Composition | Outstanding Feature | Applications |
---|---|---|---|
Ceramic/Ferrite | Iron oxide and barium/strontium carbonate | Resistant to demagnetization and corrosion | Electric motors, speakers, household appliances |
Alnico | Aluminum, nickel, cobalt, and other elements | High temperature stability | Sensors, measuring instruments, motors |
Samarium Cobalt (SmCo) | Samarium and cobalt | High resistance to demagnetization | Aerospace, military, high-temperature motors |
Neodymium Iron Boron (NdFeB) | Neodymium, iron, and boron | High magnetic properties | Electronics, wind turbines, electric vehicle motors |
Each type of permanent magnet offers distinct advantages for specific applications. The selection depends on factors like required magnetic strength, operating temperature, environmental conditions, and budget constraints. Understanding these differences helps engineers and manufacturers choose the optimal magnet type for their specific needs.
How Do Temporary Magnets Differ from Permanent Magnets?
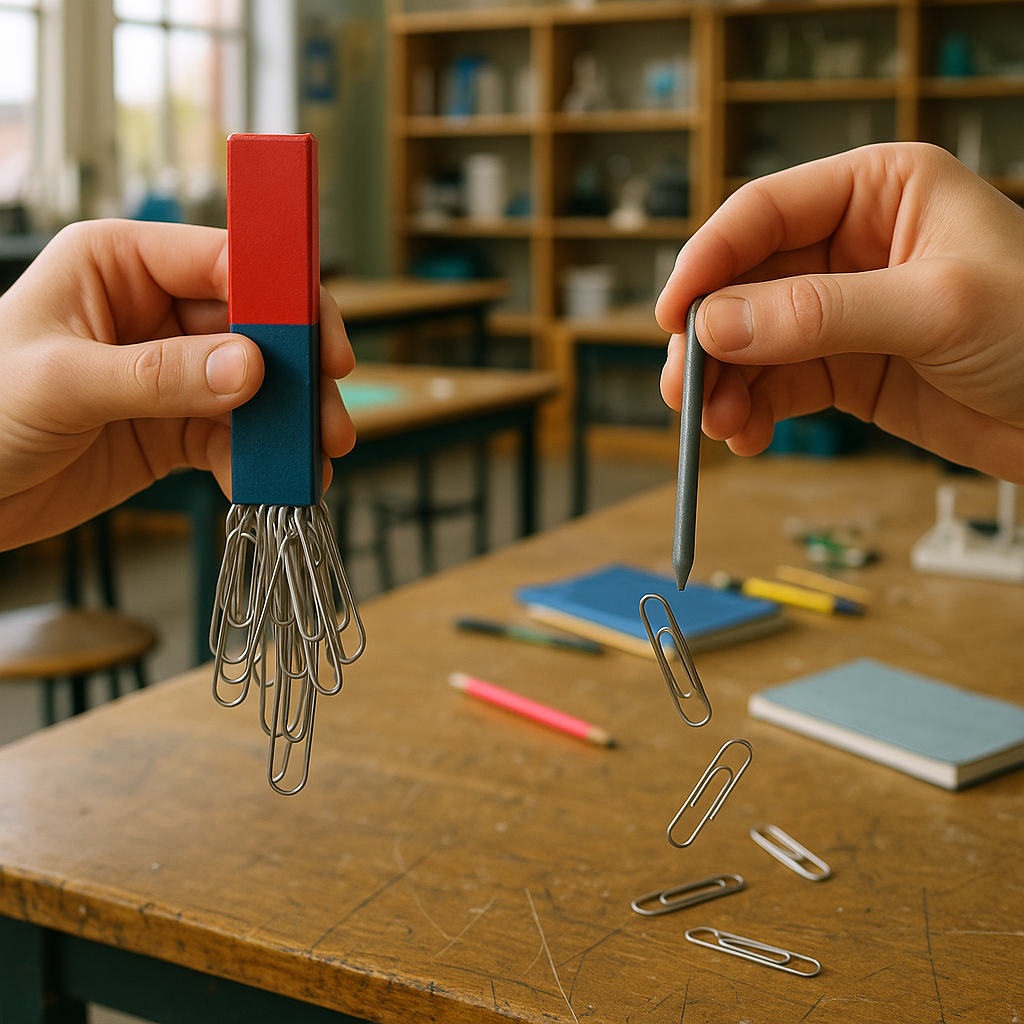
Temporary and permanent magnets serve different roles in waste management and industrial applications. Temporary magnets exhibit magnetic properties only when near a strong magnetic field, losing them once the field is removed.
Soft metals like iron, nickel, and certain alloys often function as temporary magnets. These materials have magnetic domains that easily align when exposed to an external magnetic field but quickly return to random orientation when the field is removed, resulting in a short-lived magnetic effect.
Permanent magnets, however, maintain their magnetic properties for extended periods without external influence. They are made from materials with high coercivity and remanence, allowing them to resist demagnetization. Ferrite, neodymium, and samarium-cobalt are common materials for permanent magnets.
Material Composition Differences
The key difference between temporary and permanent magnets is their material composition. Temporary magnets typically consist of soft ferromagnetic materials with low coercivity, like soft iron, paperclips, and ordinary nails, which can be easily magnetized but quickly lose their magnetic alignment.
Permanent magnets contain hard ferromagnetic substances that maintain their magnetic field strength over time, making them valuable for recycling applications where continuous magnetic separation is needed. Many recycling facilities rely on permanent magnets in their material recovery systems.
The atomic structure of these materials explains their behavior. In temporary magnets, the magnetic domains shift easily, while permanent magnets have domains that remain fixed in alignment after magnetization.
Practical Applications in Recycling
In recycling operations, both temporary and permanent magnets serve critical functions. Temporary magnets provide flexibility in material handling systems where magnetism needs to be switched on and off. Electromagnetic separators used in metal recycling employ temporary magnetism to sort ferrous materials from mixed waste streams.
Permanent magnets offer reliability in continuous sorting operations. They require no power source to maintain their magnetic field, making them energy-efficient for long-running recycling processes. Overband magnets that remove ferrous contaminants from conveyor belts typically use permanent magnets for consistent performance.
The recyclability of both magnet types also differs significantly. Temporary magnets made from common metals are easily recycled through standard metal recovery processes. Permanent magnets, especially those containing rare earth elements, require specialized recycling methods to recover their valuable components.
Simple Temporary Magnetism Experiment
You can observe temporary magnetism through a simple experiment. Take an ordinary steel paperclip and run a permanent magnet along its length about 10-15 times in the same direction. The paperclip will become temporarily magnetized and can pick up small metal objects like staples or other paperclips.
Now, try picking up additional paperclips by touching them to the end of your magnetized paperclip. You’ll create a chain as each paperclip becomes temporarily magnetized. To demonstrate the temporary nature of this magnetism, remove the permanent magnet and observe how the paperclips gradually lose their magnetic properties and drop away from each other.
This experiment illustrates how temporary magnets work in recycling operations, where materials can be magnetized for sorting purposes and then demagnetized for further processing.
Understanding the distinct properties of temporary and permanent magnets allows recycling facilities to select the appropriate magnetic technology for specific material recovery applications. The ability to control magnetism provides valuable flexibility in modern waste management systems.
Characteristic | Temporary Magnets | Permanent Magnets |
---|---|---|
Magnetic Field | Requires external field | Self-sustaining |
Material Composition | Soft ferromagnetic materials | Hard ferromagnetic substances |
Durability | Less durable | More durable |
Applications | Electromagnetic separators | Overband magnets |
Environmental Impact | Lower with common materials | Higher with rare-earth elements |
What Are Electromagnets and How Do They Work?
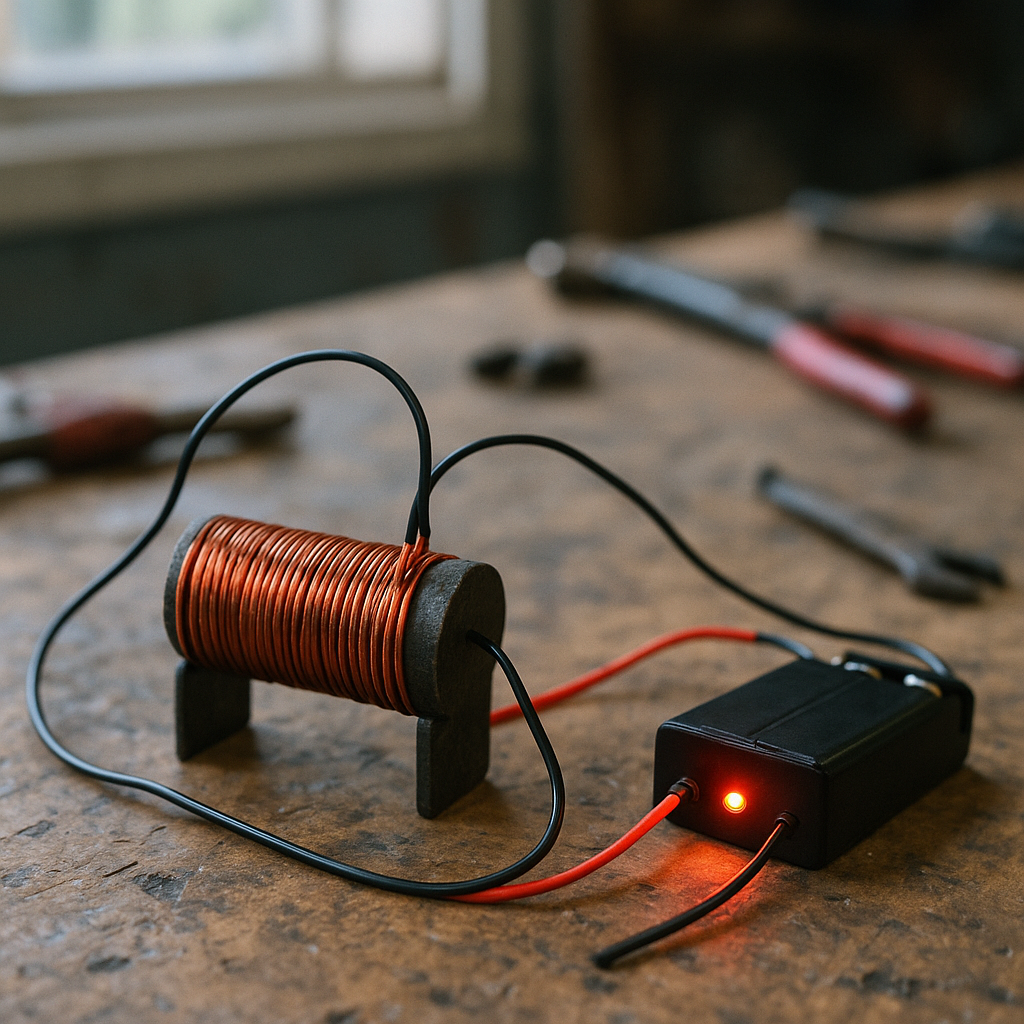
Electromagnets create magnetic fields by using electricity. When an electric current flows through a wire coiled around a metal core, it generates a magnetic field. This principle makes electromagnets versatile in many industrial and everyday applications.
The basic structure of an electromagnet is straightforward. It consists of a conductive wire, typically copper, wrapped around a ferromagnetic core like iron. The core enhances the magnetic field generated by the electric current.
Unlike permanent magnets, electromagnets can be turned on and off by controlling the flow of electricity. When the current flows, the electromagnet becomes magnetized. When the current stops, the magnetic field disappears. This controllability makes electromagnets useful in various applications.
Controlling Electromagnet Strength
The strength of an electromagnet depends on several factors. The number of wire turns around the core directly affects field strength; more turns create a stronger magnetic field. The amount of electric current flowing through the wire also determines the strength.
The core material significantly influences an electromagnet’s power. Iron cores are particularly effective due to their high permeability, allowing them to support a strong magnetic field.
When electric current passes through the coiled wire, it aligns the atoms in the metal core in the same direction, increasing the magnetic field strength. The degree of alignment corresponds to the level of current, enabling precise control of the electromagnet’s power.
Industrial and Technological Applications
Electromagnets have essential functions across various industries. In recycling facilities, powerful electromagnets separate ferrous metals from other materials. These magnets can lift heavy loads of scrap metal when activated and release them by simply turning off the current.
Electric motors rely on electromagnets to convert electrical energy into mechanical motion. The interaction between electromagnets and permanent magnets creates rotational movement that powers everything from small household appliances to industrial machinery.
Medical technology also benefits from electromagnets. MRI machines use powerful electromagnets to generate detailed images of internal body structures by aligning hydrogen atoms within the body and detecting their response to magnetic fields.
Application | Field Strength Required |
MRI Machines | 1.5 – 3 Tesla |
Maglev Trains | ~1 Tesla |
Electric Motors | 0.2 – 0.5 Tesla |
Particle Accelerators | Up to 10 Tesla |
Speakers | 0.1 – 0.2 Tesla |
Particle accelerators use electromagnets to control the trajectory of charged particles. By precisely manipulating the magnetic fields, scientists can propel subatomic particles at near-light speeds for research into fundamental physics.
Even everyday items like doorbells use electromagnets. When someone presses a doorbell button, it completes an electrical circuit. The resulting current activates an electromagnet that pulls a metal clapper against a bell, creating the familiar chime sound.
Audio speakers convert electrical signals into sound through electromagnetic induction. A coil attached to the speaker cone moves within a magnetic field when an electrical audio signal passes through it, causing the cone to vibrate and produce sound waves.
Conclusion: Powering Progress Through Magnetic Innovation
From electronics to recycling, magnets are essential components that quietly drive our modern world. Understanding the differences between permanent, temporary, and electromagnets empowers industries to select the right magnetic technology for everything from efficient waste separation to clean energy solutions and precision medical tools.
If your operation involves metal recovery, equipment dismantling, or recycling rare earth materials, Okon Recycling has the expertise to help. For responsible magnet recycling and material handling solutions, call 214-717-4083 and speak with a specialist today.