5901 Botham Jean Blvd, Dallas, TX 75215
How to Recycle Retired Rail Equipment: An Introduction
May 16, 2025When railcars and locomotives reach the end of their operational life, they still hold significant value. Recycling retired rail equipment transforms these massive steel assets from potential environmental liabilities into valuable resources. This process helps reduce landfill waste while reclaiming metals and components for new uses.
The rail industry generates thousands of tons of recyclable materials annually. From freight cars to locomotives, these machines contain valuable steel, copper, aluminum, and other materials that can be recovered through specialized dismantling and processing techniques. Railway operators benefit from responsibly retiring outdated equipment through proper recycling channels.
Sustainable rail equipment recycling involves specialized processes that maximize material recovery. Companies like Progress Rail and CRMS specialize in these operations, offering comprehensive services from initial assessment to final processing. These specialists employ advanced methods to safely dismantle rail equipment, separate recoverable materials, and process them for reuse in various industries.
What Are the Key Steps in Recycling Rail Equipment?
Rail equipment recycling follows a systematic process designed to maximize resource recovery and minimize environmental impact. This structured approach ensures valuable materials are reclaimed while managing hazardous substances safely.
Assessment and Evaluation
The first critical step involves evaluating retired rail equipment. Specialists assess the condition of components to determine which parts can be refurbished and which require recycling. This examination includes checking for structural integrity, wear patterns, and compliance with safety standards.
Each piece of equipment undergoes documentation to track its components through the recycling process. Technicians identify valuable parts such as engines, wheelsets, and electronics that may have remaining useful life.
Decommissioning and Preparation
Once assessed, the equipment enters the decommissioning phase. Workers safely remove all operating fluids, including oils, hydraulic fluids, and coolants. These substances require special handling to prevent environmental contamination.
Hazardous materials such as batteries, fire extinguishers, and potentially explosive components are carefully extracted. This critical pre-treatment ensures worker safety and environmental protection throughout subsequent processing stages.
Dismantling for Recovery
The dismantling phase involves separating components based on their potential future use. Parts with refurbishment potential are removed first. These typically include bogies, wheel sets, couplings, brake systems, and electronics.
Technicians methodically disassemble the equipment, sorting materials by type. This precision approach maximizes the recovery value. Components requiring specialized handling are tagged and routed to appropriate facilities.
Material Separation and Classification
After dismantling, materials undergo thorough separation and classification. The process typically divides materials into ferrous metals (steel and iron), non-ferrous metals (aluminum, copper, zinc), glass, plastics, rubber, and composite materials.
Advanced sorting technologies ensure high recovery rates. Materials are classified according to industry standards to meet the specifications of recycling facilities and manufacturers who will ultimately use the reclaimed resources.
Processing and Transformation
The final step involves processing separated materials for reintroduction into manufacturing streams. Metals are typically shredded and melted to create new raw materials. Non-metallic components undergo specialized recycling processes based on their composition.
Parts identified for reuse undergo refurbishment to meet quality standards. This might include cleaning, reconditioning, testing, and certification before being added back into inventory for future use.
Type of Material | Recovery Rate for Calculation | Recovery Rate from Network | Recovery Method |
---|---|---|---|
Ferrous metals – Steel | 98% | 90–98% | Shredding and remelting |
Ferrous metals – Cast iron | 98% | 80–90% | Shredding and remelting |
Non-ferrous metals – Pb | 98% | 80–98% | Dismantling, mechanical separation and remelting |
Non-ferrous metals – Al | 98% | 80–95% | Dismantling, mechanical separation and remelting |
Non-ferrous metals – Cu, Zn | 98% | 60–80% | Dismantling, mechanical separation and remelting |
Polymers (excluding elastomers) | 100% | 50–70% | Dismantling, separation and dedicated recycling processes |
Elastomers | 100% | 50–70% | Dedicated recycling processes |
Glass | 100% | 50–100% | Remelting |
Safety glass | 94% | 50–94% | Separation and remelting |
Oils | 100% | 50–100% | Refining, Incineration |
Integrated Recycling Approach
Companies specializing in rail equipment recycling, such as Progress Rail, apply an integrated approach that maximizes value recovery. When locomotives and railcars reach end-of-life, these specialists refurbish reusable parts and incorporate them into their inventory.
The remaining materials enter appropriate recycling streams. This comprehensive process creates a closed-loop system that supports sustainability while recovering economic value. The proceeds from recycled materials often offset the costs of new equipment purchases.
This systematic approach to rail equipment recycling significantly reduces landfill waste while conserving valuable resources. Modern recycling techniques can achieve recovery rates up to 95% for most rail vehicles, making this process essential to sustainable transportation infrastructure management.
What Are the Benefits of Recycling Rail Equipment?
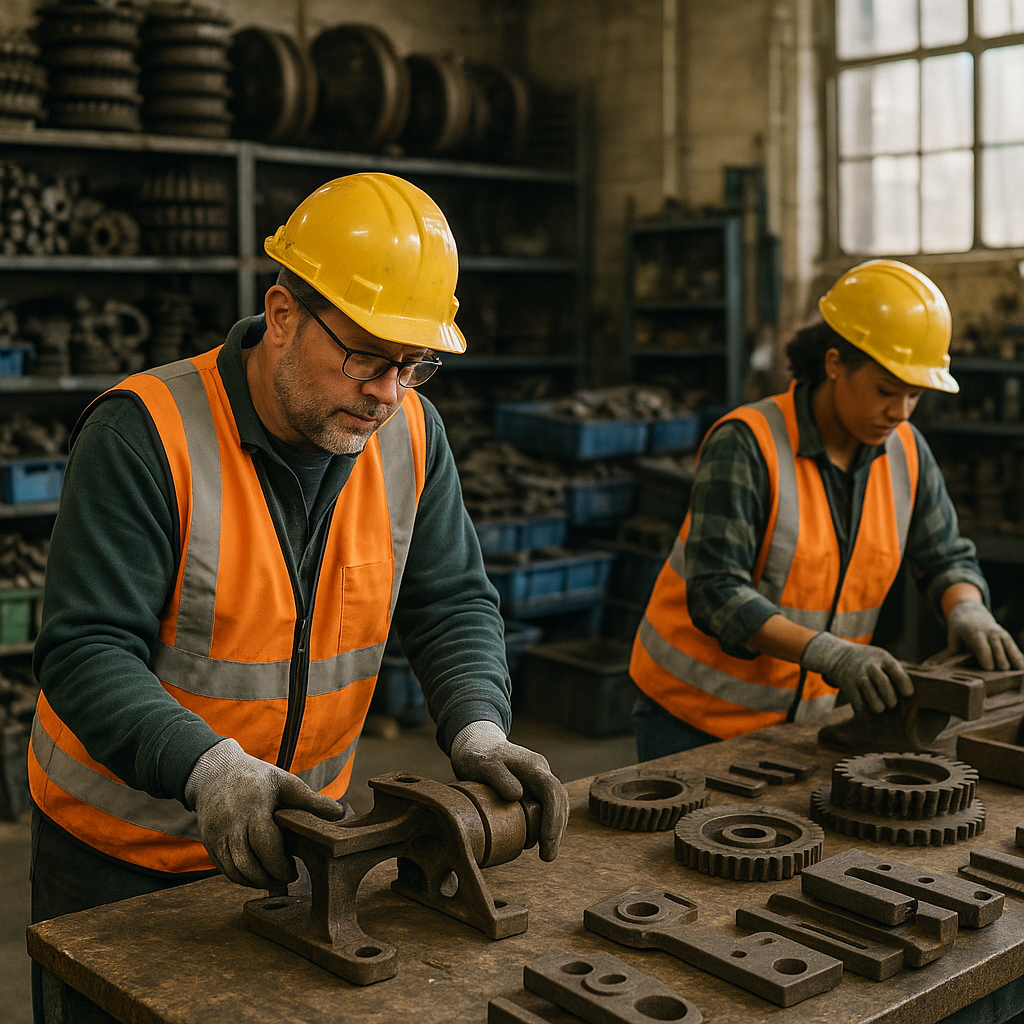
Recycling retired rail equipment transforms obsolete assets into valuable resources. This process converts large amounts of metal and components into immediate financial returns. Companies receive payouts based on the net weight of recoverable materials, turning potential disposal costs into revenue.
The environmental benefits of rail equipment recycling are substantial. Steel recycling from locomotives and railcars conserves natural resources significantly. A single locomotive contains enough steel to build over 100 cars, reducing the need for raw material extraction by up to 90% and preserving resources.
Recycling rail equipment significantly reduces pollution compared to manufacturing new components. Industry data shows that recycling steel from old rolling stock cuts CO2 emissions by up to 58% compared to new steel production, aiding rail companies in meeting sustainability goals.
From an operational standpoint, recycling rail equipment removes the ongoing costs of storing obsolete assets. Unused locomotives and railcars occupy valuable space in rail yards, and their removal eases congestion and improves operational efficiency. Companies also avoid demurrage fees for idle equipment.
The economic advantages extend beyond immediate cash returns. Recycling offsets decommissioning costs while supporting a circular economy. Nearly every part finds new life—from steel frames to copper wiring and aluminum components. Even batteries containing valuable metals like lead and lithium can be properly processed.
Regulatory compliance is another significant benefit. Environmental regulations are tightening regarding the disposal and management of industrial equipment. Professional recycling ensures all hazardous materials are handled according to current laws, preventing potential fines and legal issues.
The recycling process itself has become increasingly sophisticated. Advanced sorting technologies use artificial intelligence and specialized sensors to identify and separate different materials with high precision. These innovations maximize recovery rates while ensuring proper handling of each component.
Component | Material Recovery Rate | Processing Method |
Steel | 95% | Shredding and Melting |
Aluminum | 90% | Separation and Melting |
Copper | 85% | Sorting and Melting |
Glass | 80% | Crushing and Cleaning |
Plastics | 70% | Sorting and Reprocessing |
Rubber | 60% | Grinding and Reprocessing |
For rail companies looking to the future, incorporating recycling into their asset management strategy aligns with broader industry sustainability initiatives. It demonstrates environmental responsibility to stakeholders and supports compliance with corporate sustainability reporting requirements. As pressure increases to reduce industrial carbon footprints, proper end-of-life management of rail equipment becomes increasingly important.
Who Are the Key Players in Rail Equipment Recycling?
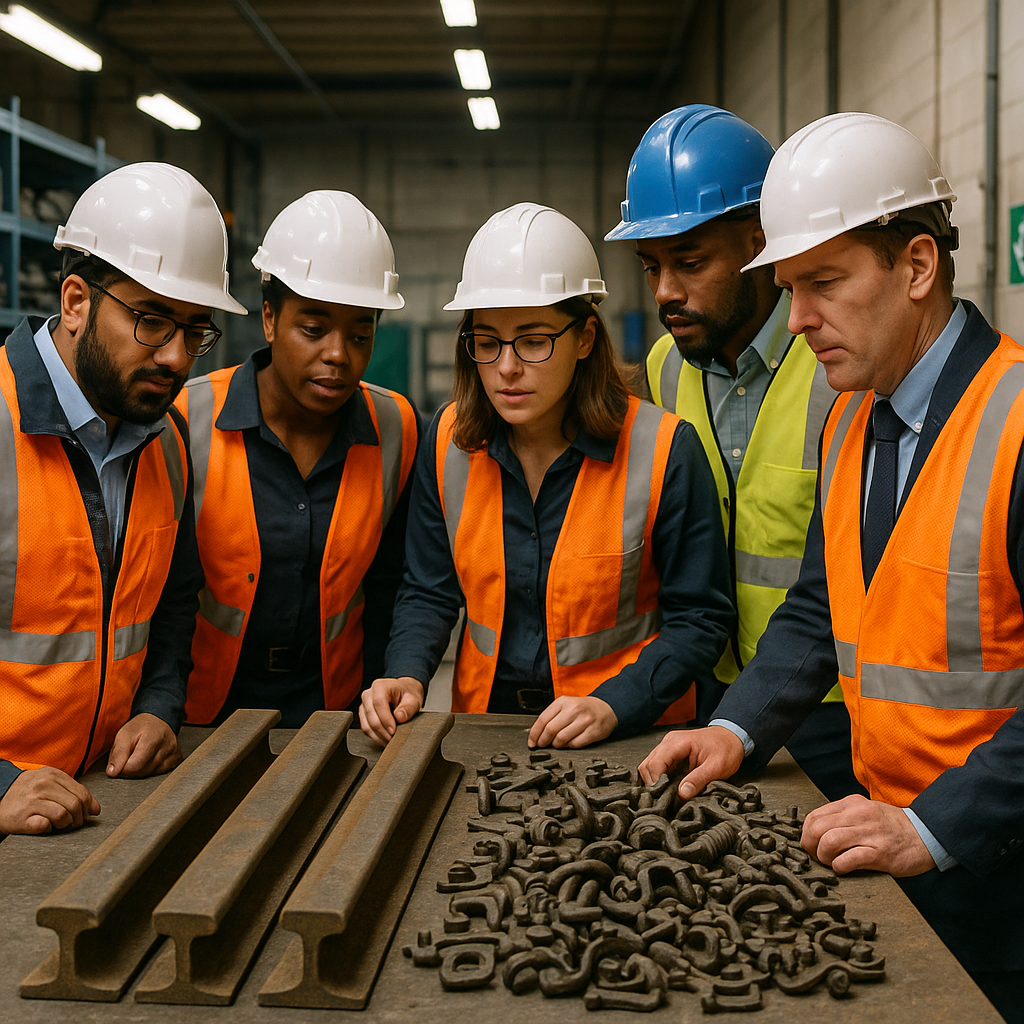
Several companies specialize in recycling retired rail equipment, each bringing unique capabilities to this specialized industry. These organizations combine extensive expertise with strategic facilities to handle complex rail recycling projects effectively.
Progress Rail
Progress Rail, a subsidiary of Caterpillar since 2006, is a major player in rail equipment recycling. The company traces its roots to a recycling business founded in 1982 in Albertville, Alabama, making recycling the foundation of its operations.
Progress Rail is distinguished by its comprehensive integration across the recycling process. When locomotives and railcars reach end-of-life, they refurbish reusable components and incorporate them into their inventory while recycling the remaining materials. This creates a circular approach that maximizes value recovery.
Their Recycling Division specializes in several critical services, including derailed equipment cleanup, removal of retired railcars, and over-the-road railcar transportation. With a central U.S. location, they service all 48 contiguous states and handle approximately 90 percent of derailments and retired cars from the Atlantic to the Rocky Mountains.
CRMS
CRMS offers specialized railcar scrapping and marketing services across the United States. Their business model centers on maintaining a robust network of partners that enables efficient processing of rail equipment regardless of location or condition.
The company has developed expertise in evaluating railcars to determine optimal recycling approaches. They assess whether units should be dismantled for parts recovery or processed as complete units based on market conditions and material values.
Pacific Steel & Recycling
Pacific Steel & Recycling focuses its rail equipment recycling operations primarily in the Northwestern United States. Headquartered in Great Falls, Montana, they have established a strong regional presence with specialized capabilities for handling both entire fleets and individual railcars.
Their approach emphasizes flexibility in recycling solutions. Customers can work with Pacific Steel & Recycling whether they have a single damaged railcar or an entire fleet requiring decommissioning. This adaptability makes them particularly valuable for regional railroads and industrial operations with varying recycling needs.
For comprehensive recycling projects, they provide coordinated services through their Rail Transportation Manager, ensuring efficient logistics and processing.
These key industry players possess the specialized equipment, transportation networks, and processing facilities necessary to manage large-scale rail equipment recycling efficiently. Their expertise ensures that valuable materials are recovered properly while adhering to environmental regulations and industry standards.
Conclusion: The Future of Rail Equipment Recycling
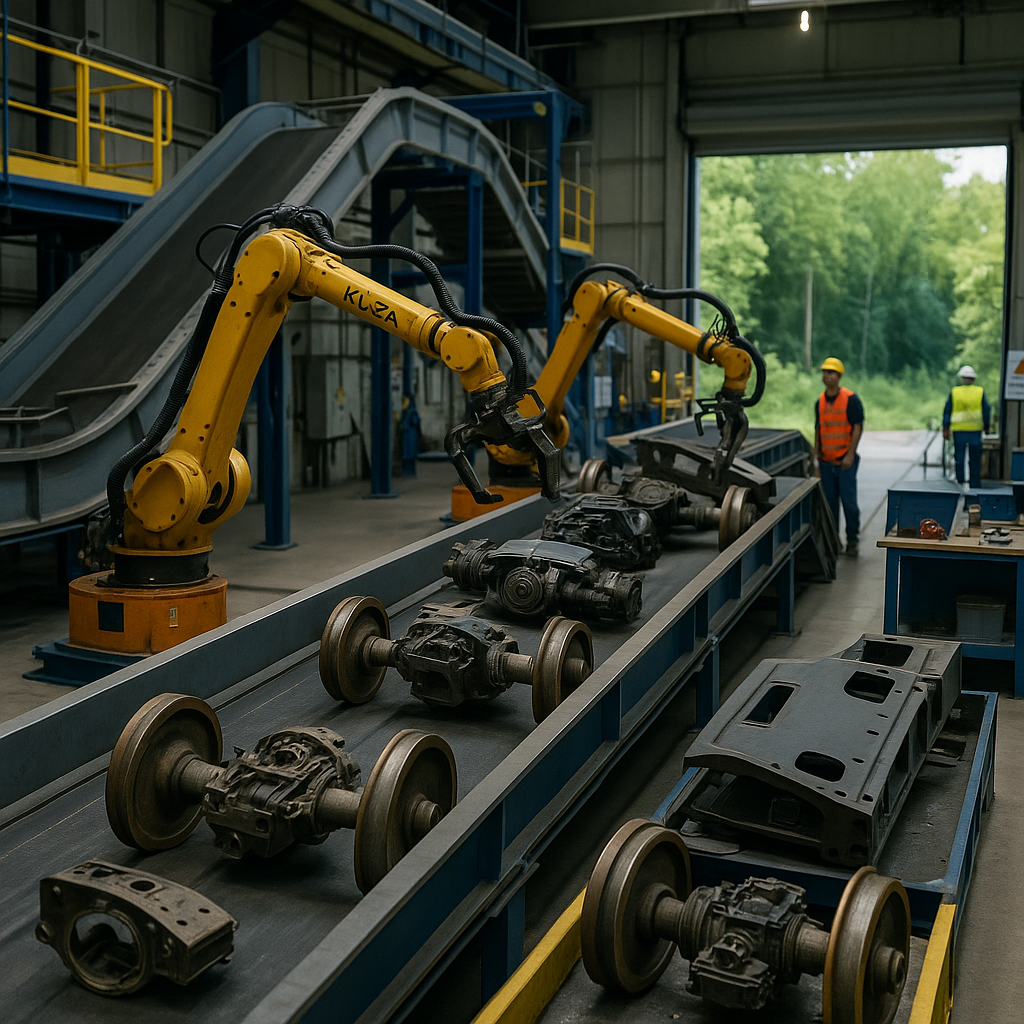
The rail industry is at a crucial point in its sustainability efforts. As aging infrastructure needs replacement and modernization, responsible recycling practices are now essential. Effective rail equipment recycling offers dual benefits: conserving resources by recovering valuable metals and materials, and reducing the environmental impact of this critical transportation sector.
The future of rail equipment recycling is promising. Technological innovations in material sorting and recovery are improving efficiency. Industry-wide collaboration is creating standardized methods for handling complex components. These advancements position the rail sector as a leader in industrial sustainability. Contact Okon Recycling at 214-717-4083 for specialized expertise in rail equipment recycling solutions.