5901 Botham Jean Blvd, Dallas, TX 75215
What is Recycling CNC Machines and Why is it Important?
May 14, 2025Did you know that electronic waste is one of the fastest-growing waste streams globally, with over 50 million tons generated annually? CNC machines significantly contribute to this challenge. Recycling CNC machines is a crucial strategy in modern manufacturing’s push toward sustainability and environmental protection.
CNC machines are precision tools that shape materials like metal and wood through computer-controlled processes. Despite their technological sophistication, these machines eventually become outdated or inefficient. When this happens, they turn into electronic waste containing hazardous materials such as lead, cadmium, and mercury that can contaminate soil and water sources.
Recycling CNC machinery involves systematically reusing, refurbishing, or repurposing components to extend their lifecycle. This process addresses environmental risks while conserving valuable resources embedded in these complex machines. The practice aligns manufacturing with circular economy principles, where materials remain in productive use rather than ending up in landfills.
How Does CNC Machine Recycling Contribute to a Circular Economy?
CNC machine recycling is essential for fostering a circular economy in manufacturing. Traditionally, production followed a take-make-dispose model. The circular economy transforms this into a regenerative system that prolongs the use of materials.
When CNC machines reach the end of their life, they contain high-value components ready for reuse. Motors can be refurbished for new equipment. Metal frames, often aluminum and steel, can be melted and reformed into new components. Even circuit boards contain precious metals like gold, silver, and copper, which can be extracted through specialized recycling processes.
The recycling process involves several steps. First, decommissioned machines are assessed for reusable components. Technicians disassemble the equipment, sorting parts by material. Functional components like power supplies and control systems often find immediate reuse. Other materials enter specific recycling streams.
Consider recycling one CNC milling machine. Its steel frame alone may contain several hundred pounds of high-grade metal, recoverable at a fraction of the environmental cost of mining new ore. Cutting tools, often tungsten carbide, offer another valuable recovery opportunity, as tungsten mining causes significant environmental disruption.
This approach provides substantial environmental benefits. By reducing the demand for virgin resources, CNC recycling limits ecological damage from mining. Processing recycled metals uses 60-95% less energy than extracting and refining new materials, leading to significant carbon emission reductions in manufacturing.
Resource conservation extends beyond metals. CNC machines contain plastics in control panels and covers. Recovering these plastics prevents landfill accumulation, allowing them to be reprocessed into new products, completing the circular loop.
The circular economy also creates economic opportunities. Recycling facilities generate jobs in dismantling and remanufacturing. Manufacturers benefit from reduced material costs by using recycled components, encouraging the adoption of sustainable practices.
Broadly, CNC machine recycling is part of a larger movement toward sustainable manufacturing. Combined with practices like energy-efficient production and waste minimization, it contributes to industrial sustainability that benefits both businesses and the environment.
What Are the Key Strategies for Sustainable CNC Machine Recycling?
Sustainable CNC machine recycling focuses on extending equipment life and minimizing environmental impact. The manufacturing industry increasingly recognizes these precision tools contain valuable resources that shouldn’t end up in landfills. Several effective strategies have emerged as best practices for responsible recycling.
Reuse and refurbishment are among the most impactful approaches. Manufacturers can assess older machines, replace worn components, and upgrade control software to restore performance. This process not only reduces waste but significantly extends machine lifespan. The European Commission‘s recent circular economy initiatives specifically highlight refurbishment as a priority for industrial equipment.
Component extraction becomes essential when machines reach end-of-life status. Critical parts like motors, enclosures, and circuit boards can be carefully removed and reprocessed. Metal components can be melted down for new manufacturing applications, creating a circular material flow that reduces demand for virgin resources.
- Conduct thorough machine assessments to identify refurbishment opportunities
- Replace only worn parts rather than entire systems
- Upgrade control software to improve performance and efficiency
- Implement systematic parts recovery processes
- Partner with specialized electronics recyclers for circuit boards
Proper hazardous material handling remains crucial throughout recycling processes. CNC machines often contain substances like coolants, lubricants, and electronic components with potentially harmful materials. Establishing protocols for safe removal, containment, and disposal prevents environmental contamination and protects worker safety.
Integrating eco-friendly production practices into the entire machine lifecycle further enhances sustainability. Manufacturers can embrace renewable energy sources for both production and recycling operations. Leading facilities have implemented solar and wind power systems that significantly reduce carbon emissions. Water conservation measures, including closed-loop cooling systems, minimize another critical environmental impact.
The carbon footprint reduction potential extends beyond energy considerations. Transportation logistics for recycled materials can be optimized to minimize emissions. Some manufacturers now conduct lifecycle assessments to quantify and address environmental impacts across all stages of machine production and recycling. These data-driven approaches identify the most effective sustainability improvements.
Adopting sustainable CNC machine recycling strategies delivers both environmental and economic benefits. By implementing comprehensive approaches to reuse, component recovery, and eco-friendly operations, manufacturers can significantly reduce waste while conserving valuable resources. The growing focus on circular economy principles continues driving innovation in this essential area of manufacturing sustainability.
How Does CNC Machining Technology Contribute to Sustainability?
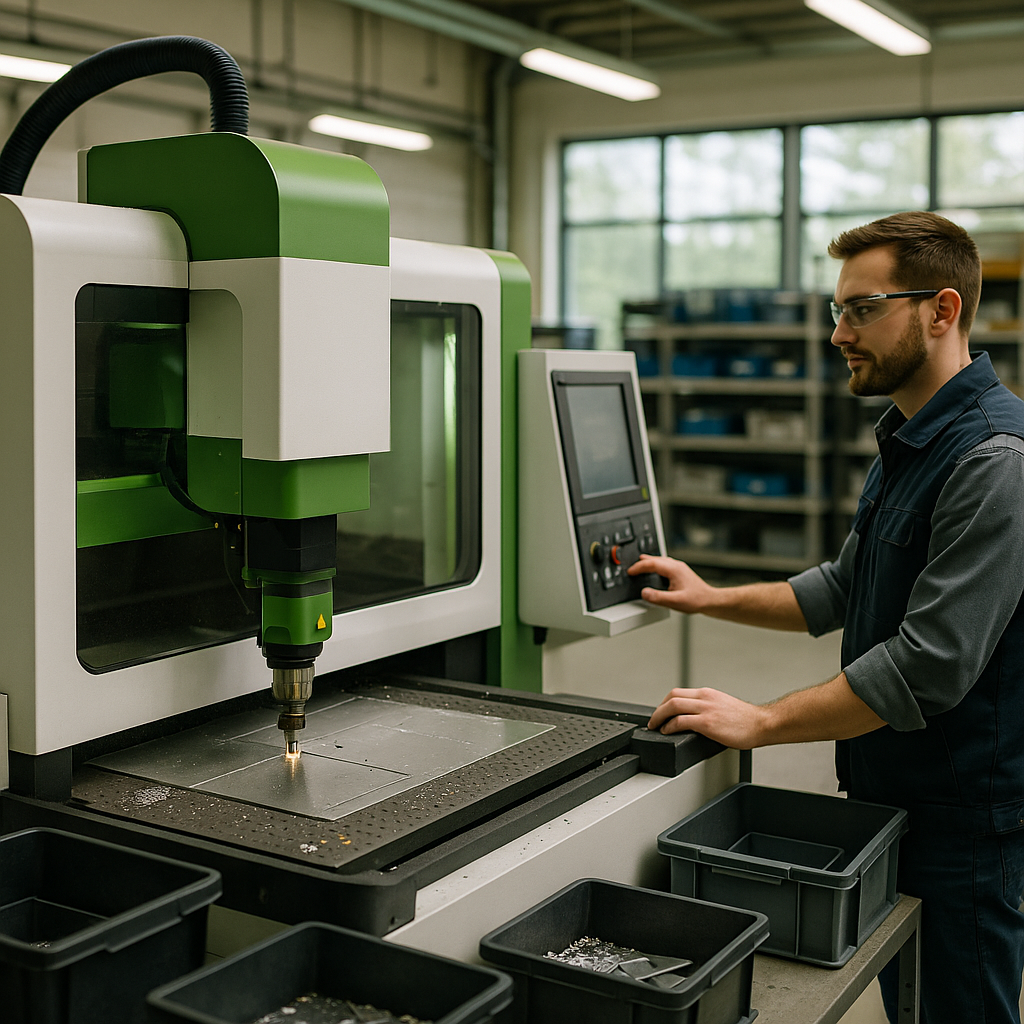
The integration of Computer Numerical Control (CNC) technology into manufacturing marks a significant advancement for sustainability across industries. CNC machining employs precise digital instructions to guide cutting tools along optimal paths, reducing material waste by up to 30% compared to traditional methods.
Traditional machining often relies on manual operation, leading to inconsistent cuts and higher error rates. CNC machines address these issues through automated, computer-guided processes that execute exact specifications repeatedly. When a CNC machine cuts materials, it follows programmed routes with accuracy measured in thousandths of an inch.
Material efficiency is a primary sustainability benefit of CNC technology. Programming capabilities allow manufacturers to nest components optimally, maximizing raw material use. This efficient utilization directly reduces resource consumption and lessens waste sent to landfills.
Energy Optimization in CNC Operations
Modern CNC machines feature advanced energy management systems that significantly cut power consumption. Variable frequency drives (VFDs) adjust power usage based on operational needs rather than running at full capacity continuously. This smart power management can reduce energy consumption by up to 25% compared to older machines.
Many contemporary CNC systems also include regenerative braking systems that capture and reuse energy during deceleration. Automated standby modes activate during idle periods, reducing unnecessary power usage. These energy-saving features contribute to lower carbon emissions and operational costs.
The adoption of dry machining techniques further enhances sustainability by reducing or eliminating cutting fluids, decreasing water usage, and minimizing the environmental impact of fluid disposal. Dry machining supports cleaner production while maintaining cutting efficiency where applicable.
Material Compatibility and Recycling Potential
CNC machines are remarkably versatile in processing various materials, including recycled and sustainable options. This compatibility extends to reclaimed metals, recycled plastics, and other repurposed materials that might otherwise become waste. Manufacturers can integrate these recycled inputs without sacrificing precision or quality.
The scrap material generated during CNC operations also contributes to sustainability through recycling programs. Metal chips and shavings can be collected, processed, and reintroduced into the manufacturing cycle. This closed-loop approach aligns with circular economy principles and reduces reliance on virgin materials.
Advanced monitoring systems in CNC machines track material usage with exceptional accuracy, enabling manufacturers to identify waste patterns and implement targeted improvements. Real-time monitoring also helps prevent defects that would lead to scrapped parts.
Renewable Energy Integration
Forward-thinking manufacturers are now powering their CNC operations with renewable energy sources. Solar panels, wind turbines, and hybrid energy systems can significantly reduce the carbon footprint of CNC machining. Some facilities have reported carbon emission reductions of up to 40% after transitioning to renewable power sources.
The precision of CNC technology also facilitates the creation of components for renewable energy systems themselves. CNC machines produce the exact parts needed for solar arrays, wind turbines, and energy storage systems. This creates a positive feedback loop where sustainable manufacturing supports the development of more sustainable energy technologies.
The integration of IoT (Internet of Things) capabilities with CNC systems further enhances their sustainability profile. Smart, connected machines can optimize production scheduling, predict maintenance needs, and minimize downtime. These improvements translate to more efficient resource use and less waste throughout the manufacturing process.
Conclusion: The Future of Sustainable CNC Machine Recycling
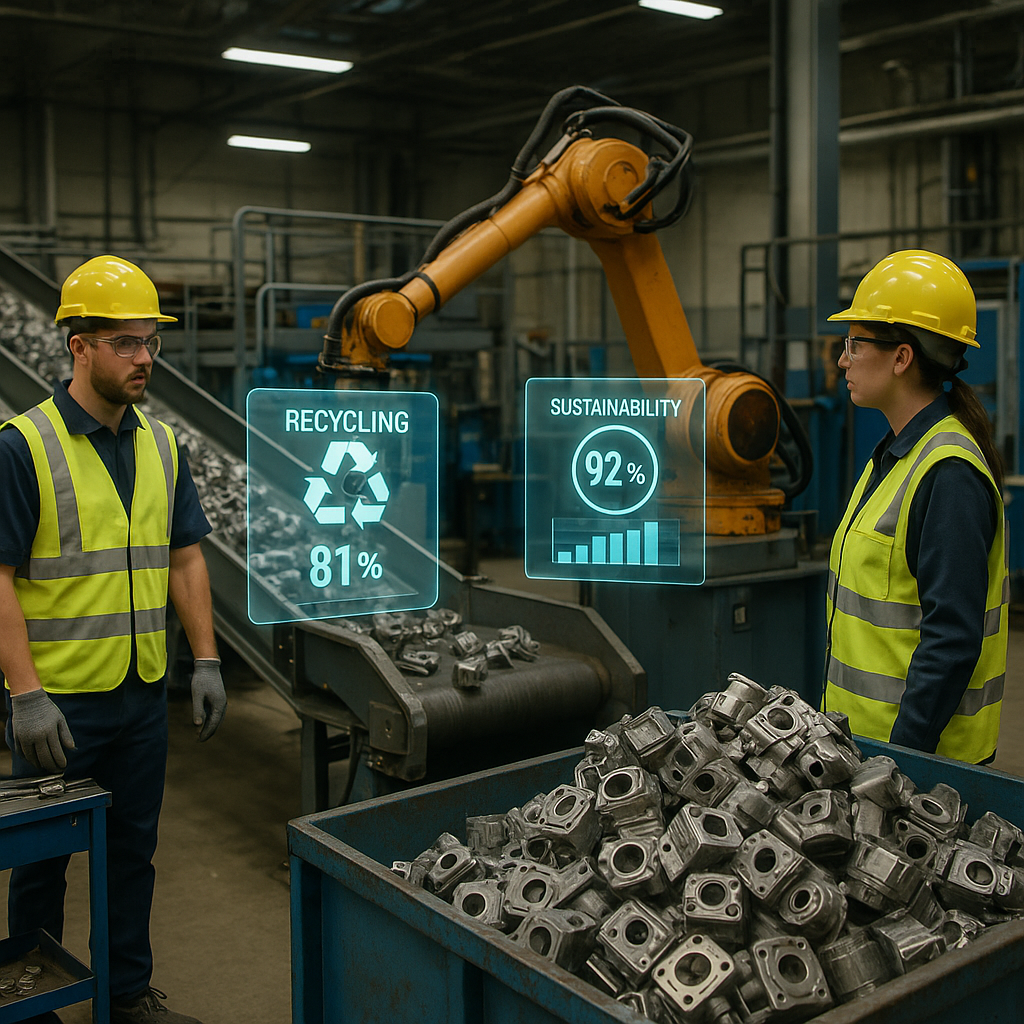
Sustainable CNC machine recycling marks a significant shift in manufacturing practices. Adopting environmentally conscious methods for managing end-of-life CNC equipment offers substantial benefits for both businesses and the planet. By implementing effective recycling protocols, companies can greatly reduce landfill waste while reclaiming valuable materials like aluminum, steel, copper, and rare earth elements from outdated machinery.
The economic benefits of sustainable CNC recycling are noteworthy. Businesses that adopt these practices often achieve cost savings through resource recovery and enhanced operational efficiency. Many manufacturers find that sustainable recycling aligns well with broader business goals, creating a balance between environmental responsibility and financial success.
For your CNC machine recycling needs, contact Okon Recycling at 214-717-4083. Our specialized services ensure your equipment is recycled responsibly, maximizing resource recovery while minimizing environmental impact.