5901 Botham Jean Blvd, Dallas, TX 75215
How to Prepare Specialty Metals for Recycling
May 7, 2025Specialty metals—including superalloys, titanium, high-grade stainless steel, and rare earth metals—require more sophisticated recycling approaches than common metals like steel or aluminum. The unique properties that make these metals valuable in their original applications can be preserved through proper recycling techniques, enhancing their value in the circular economy.
The environmental benefits of specialty metal recycling are significant. Recycling these materials greatly reduces the need for environmentally harmful mining operations and requires far less energy than processing virgin materials. One ton of recycled specialty metals can save enough energy to power multiple households for months while significantly reducing carbon emissions.
What Are the Key Steps in Sorting and Identifying Specialty Metals?
Proper sorting and identification are critical first steps in recycling specialty metals. The accuracy of these processes directly impacts recovery rates and the value of recyclable materials. A systematic approach ensures maximum efficiency.
Start With the Magnet Test
Begin your sorting process with a simple yet effective magnet test. Hold a strong magnet near each metal piece. Materials that stick contain iron and are classified as ferrous metals. Those that don’t respond are non-ferrous and typically more valuable.
This basic step immediately divides your specialty metals into two major categories. It forms the foundation of all effective metal sorting systems.
Implement Visual Identification
For non-magnetic metals, use visual characteristics to further categorize your materials. Look for distinctive colors such as the reddish-brown of copper, the lightweight silver of aluminum, or the yellowish tint of brass.
Advanced sorting requires attention to details like weight, texture, and luster. A small metal file can help reveal the true color beneath surface coatings or oxidation when visual identification is difficult.
Use Advanced Analytical Tools
For precise identification of specialty metals and alloys, advanced technology is essential. Handheld XRF analyzers and spectrometers provide detailed elemental analysis within seconds.
XRF analyzers work by emitting X-rays that cause atoms in the sample to fluoresce, releasing energy specific to each element present. These devices accurately identify the full chemical composition of materials, detecting even trace elements that affect recycling value.
Optical Emission Spectrometry (OES) offers another effective option. This technology uses electrical energy in the form of a spark to excite metal atoms. The unique light emission patterns are then analyzed to determine exact composition.
Method | Type | Advantages | Disadvantages |
---|---|---|---|
Appearance Test | Traditional | No equipment needed | Limited information |
Spark Test | Traditional | Classifies metal | Requires trained technician |
Rockwell Test | Traditional | Tests metal hardness | Needs prepared surface |
Brinell Test | Traditional | Tests metal hardness | Used for rough surfaces |
X-Ray Fluorescence (XRF) | Modern | Accurate element analysis | Requires equipment |
Optical Emission Spectrometry (OES) | Modern | Fast and versatile | Requires equipment |
Organize by Grade and Quality
Once identified, separate your specialty metals by both type and grade. Higher-purity materials command premium prices, so sorting by quality significantly increases value.
Create dedicated containers for each metal category. Keep different grades separate, especially for valuable materials like copper or specialty alloys used in aerospace applications.
The difference in value between properly sorted and mixed metals can be substantial. Mixed metals typically sell for 20-40% less than properly sorted materials.
Remove Contaminants
Contamination reduces the value of specialty metals. Remove non-metallic components like plastic casings, rubber attachments, or insulation from copper wiring.
For electronic components containing valuable specialty metals, careful disassembly yields the highest returns. Circuit boards from computers and telecommunications equipment often contain precious metals worth recovering separately.
Wipe down greasy or oily metal parts, as excessive oil can be considered a contaminant and might lead to rejection or reduced pricing.
Label and Document
Create a clear labeling system for your sorted materials. Proper documentation ensures you receive fair value and helps streamline the recycling process.
Record information about metal types, approximate weights, and any relevant details about source or quality. This documentation proves valuable when negotiating with buyers or tracking your recycling program’s effectiveness.
For industrial applications, implementing a consistent inventory system for scrap specialty metals can yield significant financial benefits over time.
How Can Contaminants Be Effectively Removed from Specialty Metals?
Contamination is a major challenge in specialty metal recycling. Foreign substances like oils, paints, or coatings significantly reduce the value and recyclability of these materials. The purity of recycled specialty metals directly impacts their performance in high-tech applications where even small impurities can compromise structural integrity or specialized properties.
Proper preprocessing to remove contaminants is essential before specialty metals enter the main recycling process. These steps ensure that the final recycled product meets the stringent quality standards required by industries like aerospace, electronics, and medical device manufacturing.
Mechanical Cleaning Methods
Physical removal techniques provide the first line of defense against surface contaminants. These methods physically separate unwanted substances without altering the metal’s chemical composition.
Grinding and abrasive blasting effectively remove paints, coatings, and surface oxidation. The process uses abrasive materials propelled at high velocity to strip away contaminants while preserving the base metal. This technique works particularly well for removing paint from titanium components or surface oxides from specialty alloys.
Ultrasonic cleaning represents another effective mechanical approach. Parts are immersed in a liquid bath while high-frequency sound waves create microscopic cavitation bubbles. When these bubbles collapse, they generate intense localized scrubbing that dislodges contaminants from even the most intricate geometries. This gentle yet thorough technique is ideal for cleaning complex parts with blind holes or deep recesses where other methods might leave residues.
Chemical Treatment Processes
Chemical cleaning solutions target specific contaminants through selective dissolution. These treatments can reach areas inaccessible to mechanical methods.
Vapor degreasing excels at removing oils, waxes, and greases from specialty metal surfaces. The process uses a solvent that vaporizes, condenses on the metal parts, and dissolves nonpolar contaminants. Modern vapor degreasing fluids offer effective cleaning power with reduced environmental and health impacts compared to traditional solvents.
For more stubborn impurities, acid treatments provide targeted cleaning action. Different acids dissolve specific contaminants—sulfuric acid removes rust and scale, while hydrofluoric acid tackles silicon-based impurities. These treatments require careful control to prevent damage to the base metal.
Chemical cleaning methods follow the principle that “like dissolves like.” Polar contaminants such as salts, rust, and certain emulsion residues respond best to water-based (aqueous) cleaning solutions. In contrast, nonpolar substances like machining oils and waxes require solvent-based approaches.
Thermal Treatment Techniques
Heat-based methods break down organic contaminants that resist other cleaning approaches. These techniques transform unwanted compounds without melting or altering the base metal.
Controlled pyrolysis uses heat to decompose organic materials like plastics, adhesives, and certain coatings. The process occurs in a low-oxygen environment to prevent oxidation of the specialty metal. The organic contaminants break down into gaseous byproducts that vent from the system, leaving clean metal behind.
Thermal desorption applies precise heating to volatilize contaminants with lower boiling points than the metal itself. This technique works well for removing moisture, solvents, and certain oils that can compromise downstream recycling processes.
Selecting the Right Cleaning Approach
The choice between cleaning methods depends on several factors, including the type of contamination, the specific specialty metal, and its geometry. Most effective cleaning protocols combine multiple approaches in sequence.
Part geometry significantly influences cleaning method selection. Complex parts with intricate shapes or hard-to-reach areas present special challenges. The lower surface tension of solvent-based cleaning helps it penetrate and move out of small crevices more effectively than water-based solutions, which may become trapped and increase corrosion risk.
The specific specialty metal also dictates appropriate cleaning options. Reactive metals like titanium and magnesium require specially formulated cleaning agents that won’t damage their surfaces. Precious metals benefit from techniques that preserve every gram of material during the cleaning process.
Throughput requirements factor into the decision as well. Vapor degreasing cleans, rinses, and dries parts in one step, making it suitable for high-volume operations. Aqueous systems use a multistage process that may take longer but offers excellent results for certain contaminant types.
Properly cleaned specialty metals maintain their valuable properties through the recycling process. This preservation of material integrity ensures that recycled metals can meet the same demanding specifications as virgin materials, supporting both environmental sustainability and economic viability in specialty metal recycling operations.
What Advanced Technologies Are Used in Specialty Metal Recycling?
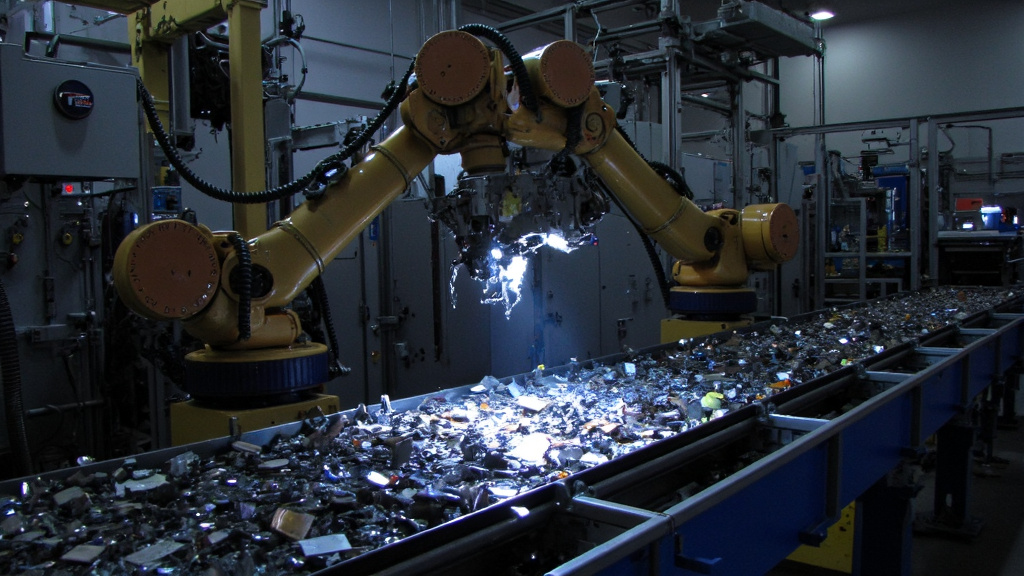
Advanced recycling technologies are crucial for maximizing recovery rates and ensuring high-quality recycled specialty metals. These processes set modern metal recycling apart through precision, efficiency, and the ability to handle complex alloys.
Vacuum Induction Melting (VIM)
Vacuum Induction Melting operates in a vacuum to remove atmospheric gases during melting, preventing oxidation and contamination that could compromise metal purity. Electromagnetic induction heats and melts the metal without direct contact.
The vacuum environment efficiently removes dissolved gases like hydrogen, nitrogen, and oxygen from molten metal, producing high-purity recycled materials with superior mechanical properties and structural integrity.
VIM technology allows precise control over the chemical composition of recycled alloys. Technicians can add specific elements in exact amounts to meet desired specifications, making VIM valuable for recovering high-value specialty alloys used in aerospace, medical, and other demanding applications.
Electroslag Remelting (ESR)
Electroslag Remelting is another advanced technology transforming specialty metal recycling. It involves passing an electric current through molten slag, generating heat that melts the metal electrode above. As droplets of molten metal fall through the slag, impurities are removed through chemical reactions.
ESR excels at removing non-metallic inclusions and improving the microstructure of recycled alloys. Controlled solidification yields metals with greater homogeneity and fewer defects, resulting in recycled materials with enhanced mechanical properties and reliability.
This technology is particularly effective for processing specialty steels, superalloys, and other high-performance metals. ESR-recycled materials show improved fatigue strength, better corrosion resistance, and superior performance under extreme conditions, making them suitable for critical applications.
Technology | Process Description | Advantages |
---|---|---|
Bioleaching | Uses microorganisms to dissolve metals | Lower environmental impact, reduced energy use |
Vacuum Induction Melting (VIM) | Melting in a vacuum to prevent oxidation | High-purity materials, precise chemical composition control |
Electroslag Remelting (ESR) | Electric current through molten slag to refine metals | Improved microstructure and mechanical properties |
Additional Advanced Technologies
Beyond VIM and ESR, several other innovative technologies are advancing specialty metal recycling. Plasma Arc Recycling uses temperatures up to 20,000 degrees Celsius to separate metals from complex waste streams with precision, effectively treating electronic waste and other challenging materials.
Hydrometallurgical processes use aqueous solutions to selectively dissolve and recover metals from complex mixtures, offering lower energy consumption than traditional methods while achieving high recovery rates for precious and rare earth metals from electronic waste.
Bioleaching is a promising biological approach using microorganisms to extract metals from ores and waste materials. Operating at ambient temperatures with minimal chemical inputs, this eco-friendly process achieves recovery rates exceeding 90% for certain metals.
Environmental and Economic Benefits
These advanced technologies provide substantial environmental benefits by efficiently recovering metals that would otherwise end up in landfills, conserving valuable resources, and reducing the need for environmentally harmful mining. Recycling aluminum through advanced methods saves 95% of the energy required for primary production.
The economic benefits extend beyond energy savings. The specialty metal recycling sector creates high-quality jobs spanning various skill levels, from engineers developing new technologies to technicians operating advanced machinery. These technologies also provide manufacturers with steady streams of high-quality recycled materials, reducing production costs while enhancing sustainability credentials.
Conclusion: Maximizing Value in Specialty Metal Recycling
Specialty metal recycling offers more than just environmental benefits—it’s a strategic business move that provides substantial value. By employing proper sorting techniques, systematic cleaning, contaminant removal, and size reduction procedures, businesses can greatly improve the recovery rates and quality of these valuable materials. Utilizing data-driven approaches and advanced technologies further enhances the recycling process, maximizing returns while contributing to resource conservation.
For your specialty metal recycling needs, contact Okon Recycling at 214-717-4083. Our expert team will help you implement effective recycling strategies tailored to your specific materials, ensuring you maximize value while supporting sustainable practices in the specialty metals industry.