5901 Botham Jean Blvd, Dallas, TX 75215
Comparing Ferrite and Neodymium Magnets in Industrial Applications
April 29, 2025Magnets play vital roles in numerous industrial systems. From manufacturing to recycling, transportation to energy generation, these powerful components drive the machinery that keeps modern industry advancing. Two key magnetic types dominate this landscape: Neodymium and Ferrite magnets.
Neodymium magnets, developed in the early 1980s, offer exceptional strength in compact sizes. This rare-earth composition delivers magnetic fields up to 1.4 Tesla, making them ideal for applications where space is limited but power needs are high. Ferrite magnets, composed of iron oxide and various carbonates, provide reliable performance with notable durability and temperature resistance.
Understanding the distinct properties of these two magnetic materials helps engineers and facility managers make informed decisions. This comparison will examine their composition, magnetic strength, temperature tolerance, durability, and cost-effectiveness across various industrial applications.
The right choice between these magnetic workhorses can significantly impact equipment performance, operating costs, and system longevity.
What are the Key Differences in Composition and Strength?
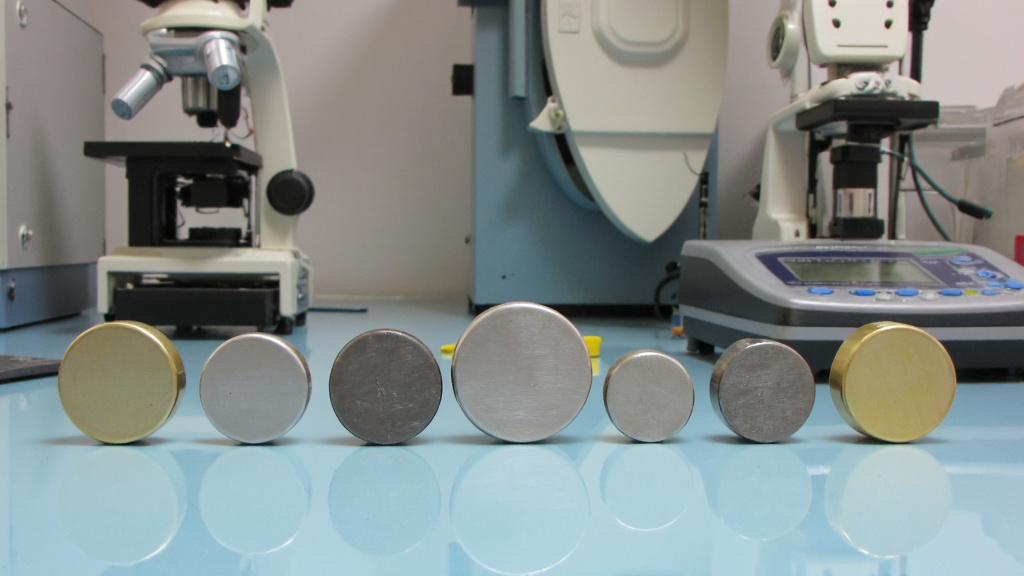
Neodymium magnets consist of an alloy of neodymium, iron, and boron (NdFeB). This specialized composition results from a powder metallurgy process where materials are compressed into molds and sintered at high temperatures. The rare earth element neodymium gives these magnets their exceptional magnetic properties.
Ferrite magnets, also known as ceramic magnets, have a fundamentally different composition. They contain iron oxide (Fe2O3) combined with either strontium carbonate or barium carbonate. Their ceramic nature makes them brittle but more resistant to environmental factors than neodymium magnets.
Magnetic Field Strength Comparison
The most significant difference between these magnets lies in their strength. Neodymium magnets produce magnetic fields up to 1.4 Tesla, making them the strongest permanent magnets available today. This impressive strength allows even small neodymium magnets to hold objects many times their weight.
Ferrite magnets generate weaker magnetic fields, typically ranging between 0.2 and 0.5 Tesla, making them 2-7 times less powerful than neodymium magnets of similar size. This strength difference is immediately noticeable in practical applications.
Real-World Applications Based on Strength
The superior strength of neodymium magnets makes them essential in applications where powerful magnetic force is needed in limited space. Hard drives, headphones, electric vehicle motors, and MRI machines rely on neodymium magnets. Their exceptional strength enables manufacturers to design smaller, more efficient devices.
Ferrite magnets are effective in applications where moderate magnetic strength is sufficient. Common uses include refrigerator magnets, speakers, magnetic separators, and holding magnets for doors and cabinets. Their lower strength is often offset by larger size to achieve necessary performance.
When choosing between these magnet types, the strength-to-size ratio is a crucial consideration. For projects requiring maximum magnetic force in minimal space, neodymium magnets are the clear technical choice despite their higher cost. Applications with fewer space constraints or lower magnetic requirements often benefit from the economic advantages of ferrite magnets.
How Do Temperature and Environmental Factors Affect Performance?
Temperature significantly impacts magnet performance, and ferrite and neodymium magnets respond differently to thermal changes.
Ferrite magnets perform well in high-temperature environments, with an operating range of -40°C to 250°C. Neodymium magnets typically function within a more limited range of 80°C to 200°C.
Temperature Response Characteristics
Ferrite magnets have a unique property that sets them apart from rare earth alternatives. As temperature rises, their resistance to demagnetization increases due to higher coercivity. For every degree of temperature increase, ferrite magnets gain about 0.4% in coercivity.
This characteristic makes ferrite magnets valuable in high-temperature applications. However, they experience a decrease in magnetic output of about 0.2% per degree Celsius increase. These effects are generally reversible when temperatures return to normal ranges.
Neodymium magnets react differently to heat. They can lose magnetic strength when exposed to temperatures near their maximum operating threshold. Different grades offer varying temperature resistance, indicated by letters following the grade number:
- N grade: Maximum operating temperature of 80°C
- M grade: Maximum operating temperature of 100°C
- H grade: Maximum operating temperature of 120°C
- SH grade: Maximum operating temperature of 150°C
- UH grade: Maximum operating temperature of 180°C
- EH grade: Maximum operating temperature of 200°C
- AH grade: Maximum operating temperature of 230°C
Corrosion and Environmental Resistance
Environmental factors beyond temperature also impact magnet performance and longevity. Ferrite magnets demonstrate excellent corrosion resistance due to their ceramic composition, withstanding moisture and oxidizing environments without significant degradation.
Neodymium magnets contain iron and are vulnerable to corrosion. Without protection, they can corrode from both external exposure and internal degradation. Most neodymium magnets require protective coatings to prevent rusting and performance loss.
The standard coating for neodymium magnets is a three-layer nickel-copper-nickel plating, providing effective corrosion protection. Other specialized coatings are available for particularly harsh environments.
Cold Weather Performance
While ferrite magnets excel in high temperatures, they become less effective in cold environments, particularly below 0°C. The reduction in magnetic pull force varies depending on the magnet’s size, shape, and application context. With proper design considerations, ferrite magnets can function effectively down to -40°C.
Neodymium magnets maintain better performance in cold temperatures, making them preferable for applications in refrigeration, outdoor winter equipment, and cold-region installations where consistent magnetic performance is required.
Industrial Application Considerations
The temperature and environmental performance differences between these magnet types directly impact their industrial applications. Motors and generators in high-temperature environments often utilize ferrite magnets due to their thermal stability and cost-effectiveness.
Outdoor equipment exposed to varying weather conditions may benefit from either magnet type depending on specific requirements. Ferrite magnets offer natural weather resistance without additional treatments. Neodymium magnets provide stronger magnetic fields but require proper coating selection to ensure durability.
For waste management and recycling operations, these environmental considerations are particularly relevant. Material separation systems operating in varied conditions must account for how temperature fluctuations might affect magnet performance to maintain consistent separation efficiency.
Understanding these environmental response characteristics helps engineers and system designers select the appropriate magnet type for specific applications, weighing magnetic strength requirements against environmental conditions, cost considerations, and expected service life.
What are the Cost and Economic Considerations?
Cost is a major factor distinguishing ferrite from neodymium magnets. Ferrite magnets are much more economical due to their composition of abundant materials like iron oxide. Their simple production process further decreases manufacturing costs. Typically, a ferrite magnet costs about 80% less than a similarly sized neodymium magnet.
Neodymium magnets use rare earth elements, which experience frequent price fluctuations in global markets. The extraction process for these elements is resource-intensive and environmentally challenging. A standard 40x20x10mm neodymium N35 block costs about five times more than a ferrite magnet of the same size.
For budget-sensitive projects or applications needing large volumes of magnets, ferrite options offer 2-3 times more magnetic field per dollar compared to neodymium. This makes ferrite magnets valuable for consumer products with tight profit margins or industrial applications requiring numerous units.
The economic equation becomes more nuanced when considering specific applications. While neodymium magnets have higher upfront costs, they may prove more economical where size and efficiency are critical. For example, in electric motors with continuous operation, neodymium magnets’ higher efficiency translates to reduced energy consumption and lower lifetime operational costs.
Processing considerations also affect cost calculations at different scales. Neodymium is relatively brittle but generally easier to machine than ferrite. For very small or precision components, manufacturing complexity can make ferrite parts more expensive to produce than equivalent neodymium components, despite the lower raw material cost.
Size-related processing costs present an interesting economic consideration. As components get smaller, total costs are increasingly dominated by machining and surface treatment rather than raw materials. The increased ratio of surface area to volume in smaller parts makes processing expenses proportionally higher. This explains why miniature applications like smartphone speakers often use neodymium despite its higher material cost.
For large-scale industrial applications with less strict space constraints, ferrite magnets usually provide the most economical solution. Applications like large stationary speakers, refrigerator magnets, and general-purpose holding mechanisms benefit from ferrite’s cost efficiency without needing neodymium’s superior magnetic strength.
Type of Magnet | Average Price per Kilogram |
---|---|
Neodymium Magnet | $30 – $40 |
Ferrite Magnet | $5 – $10 |
When evaluating magnet selection economically, lifecycle costs deserve careful consideration. In high-duty-cycle applications like air conditioning units or renewable energy systems, neodymium magnets’ higher efficiency may justify their increased upfront investment through reduced operational costs over the system’s lifetime.
National energy efficiency standards increasingly influence economic considerations for manufacturers. As regulatory bodies enforce stricter efficiency requirements for motors and electrical equipment, the performance advantages of neodymium magnets can outweigh their cost premium, especially for continuously operating systems where energy consumption is a significant expense.
Conclusion: Selecting the Right Magnet for Industrial Needs
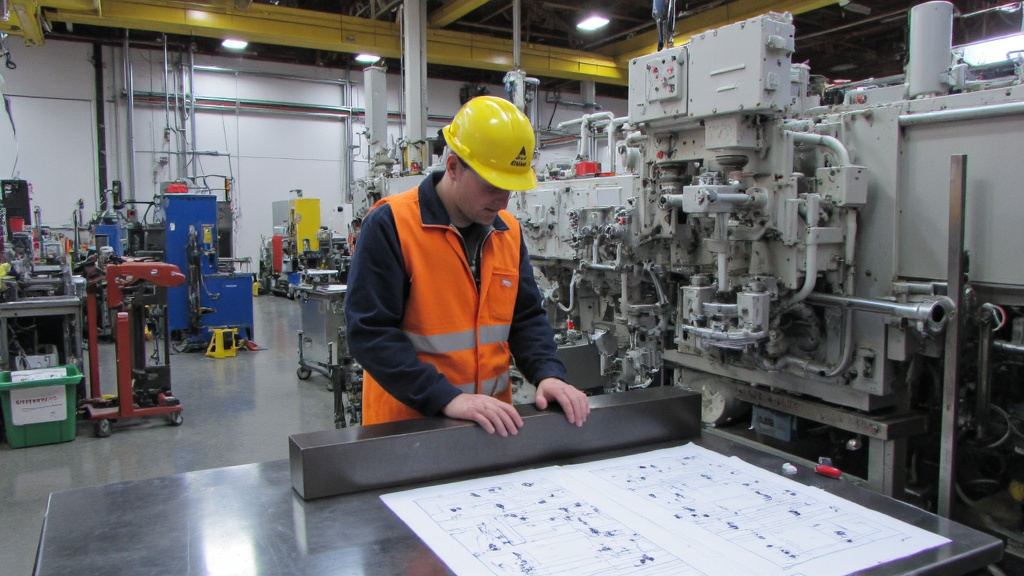
Selecting between Neodymium and Ferrite magnets involves assessing your industrial application requirements. Neodymium magnets provide superior magnetic strength in compact sizes, ideal for high-performance applications with limited space. Ferrite magnets offer a cost-effective solution with excellent temperature stability and corrosion resistance for less demanding uses.
Your decision should balance magnetic strength, environmental conditions, budget, and specific performance needs. Temperature is crucial, as Ferrite magnets perform well at higher temperatures, while Neodymium options may need special treatment.
For expert guidance on recycling your industrial magnets, contact Okon Recycling at 214-717-4083.