5901 Botham Jean Blvd, Dallas, TX 75215
What Happens When Magnets Lose Their Strength?
July 23, 2025Magnets can gradually lose their strength over time due to a process called demagnetization. This occurs when the alignment of magnetic domains within the material is disrupted, leading to a weakened magnetic field and reduced pulling force. When these tiny magnetic regions become misaligned, the once-powerful magnetic field diminishes, reducing the magnet’s ability to attract or repel other materials.
While permanent magnets are designed to maintain their magnetism for long periods, various factors can accelerate this loss. Heat is a common culprit. Each magnet has a maximum temperature threshold, and exposure beyond this point can permanently misalign the magnetic domains. Physical damage from impacts or drops can also disrupt the internal structure, causing the magnet to lose power.
Even without external influences, magnets experience natural degradation known as magnetic creep. Neodymium magnets, for instance, typically lose about 1% of their strength per decade. Environmental factors such as corrosion and oxidation can further compromise magnetic integrity when protective coatings are damaged, allowing moisture to penetrate and react with the magnetic material.
How Does Temperature Affect Magnet Strength?
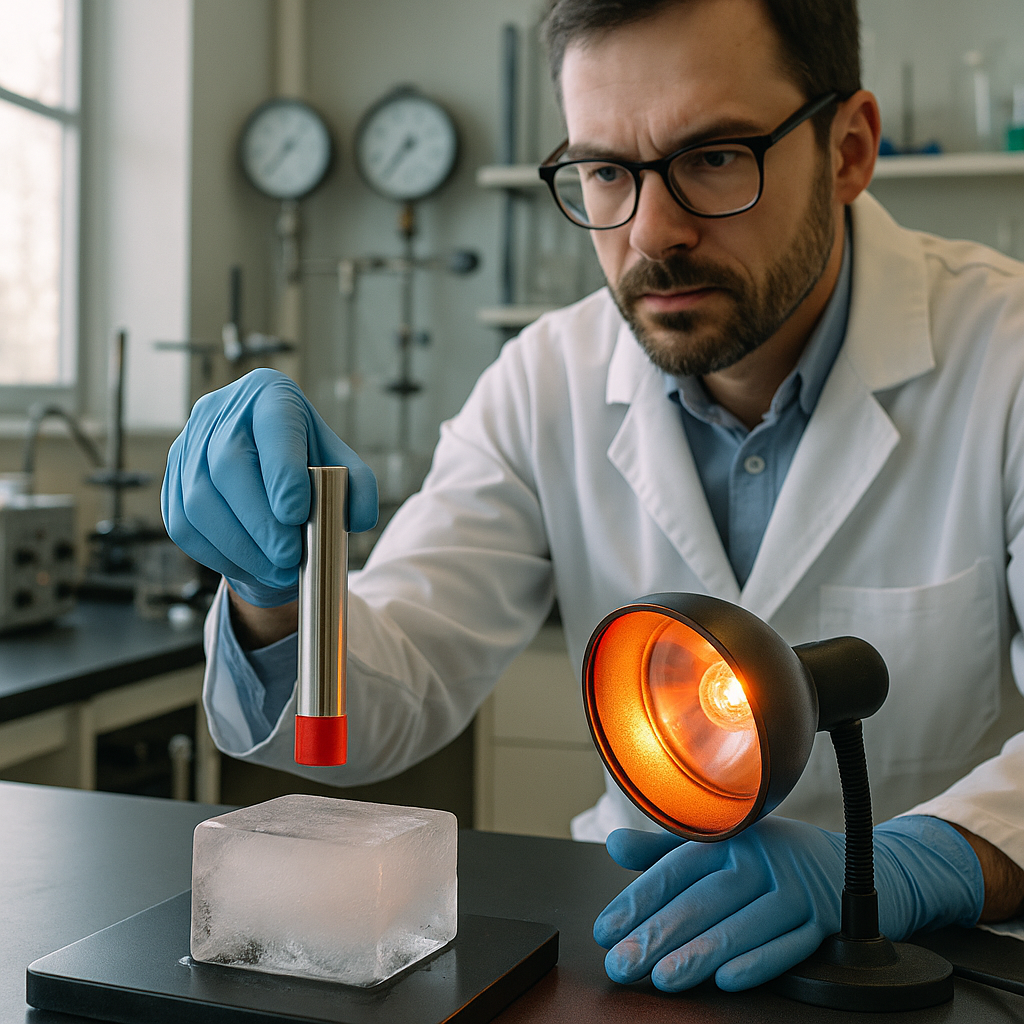
Temperature significantly influences magnet performance. When magnets are subjected to heat, the atoms within the material move faster and more erratically. This increased atomic movement disrupts the alignment of magnetic domains that contribute to a magnet’s strength.
Under normal conditions, most magnets maintain their full magnetic field. However, as temperatures increase, the magnetic domains start to misalign. This misalignment weakens the magnet’s overall strength and its ability to attract or repel other magnetic materials.
Each magnet type has a specific maximum operating temperature. Below this threshold, any temperature-related strength loss is typically reversible, meaning the magnet regains its original strength once cooled. For instance, if a magnet is heated to 80°C, but its maximum operating temperature is 100°C, it will likely return to full strength after cooling down.
If a magnet is heated beyond its maximum operating temperature, permanent demagnetization can occur. The magnetic domains become permanently misaligned, causing the material to lose its magnetic properties. This loss is irreversible without remagnetizing the material.
Different magnetic materials have varying levels of temperature sensitivity. Neodymium magnets usually have maximum operating temperatures around 80-100°C, making them more prone to heat damage. Samarium cobalt magnets can withstand temperatures up to 350°C, while alnico magnets can function at even higher temperatures, around 540°C. Ceramic (ferrite) magnets are unique in that they become more resistant to demagnetization at higher temperatures.
The shape of a magnet also affects its temperature resistance. Longer magnets generally resist demagnetization at elevated temperatures better than shorter ones made of the same material. This is especially important for neodymium magnets, which show the most significant change in demagnetization resistance with temperature.
Cold temperatures have the opposite effect. When cooled, atoms move more slowly, allowing for stronger alignment of magnetic domains. This results in increased magnetic field strength, making magnets stronger in cold environments than in warm ones.
Understanding how temperature affects magnetic strength is crucial for proper magnet selection in various applications. Engineers must consider the environmental conditions in which the magnet will operate to ensure optimal performance and longevity.
Magnet Type | Approx Max Operating Temperature (°C) |
---|---|
Standard NdFeB | ~80–150 |
High-Temp NdFeB | ~150–200 |
Samarium Cobalt (SmCo) | ~250–300 (some up to 350) |
Alnico | ~450–550 |
Ferrite | ~250 |
What Other Factors Cause Magnets to Weaken?
Physical damage is among the most common causes of magnet demagnetization. When magnets are dropped, struck, or subjected to sharp impacts, the internal magnetic domains become misaligned. This disruption breaks the uniform arrangement of atoms that creates the magnetic field, leading to weakened magnetic properties.
Exposure to opposing magnetic fields can significantly reduce magnet strength. When magnets come into contact with other magnets or ferromagnetic materials with conflicting polarities, their domains can realign in different directions. This realignment directly diminishes the overall magnetic field strength.
Improper storage conditions accelerate strength loss in magnets. Bar magnets particularly suffer when stored incorrectly, such as without their keepers or with north poles facing north poles. For optimal magnetic preservation, always store magnets with opposite poles connected or with soft iron keepers across their poles.
- Physical shock or vibration: Dropping, striking, or repeatedly subjecting magnets to vibration disrupts domain alignment.
- Adverse magnetic fields: Proximity to strong opposing magnets or electric currents can realign magnetic domains.
- Corrosion and oxidation: Exposure to moisture or corrosive environments damages the physical structure.
- Volume loss: Chipping, cracking, or erosion from abrasive materials reduces the volume of magnetic material.
- Natural aging: Over long periods, magnets experience gradual magnetic creep at about 1% loss per decade.
Even without external factors, all magnets undergo a natural aging process called magnetic creep. Most permanent magnets lose approximately 1% of their strength every decade through this process. While this degradation happens slowly, it remains an inevitable aspect of magnetic materials.
Neodymium magnets, while extremely powerful, are more susceptible to external demagnetizing factors than some other types. Samarium cobalt magnets generally maintain their strength better against physical and environmental challenges, making them suitable for demanding applications despite their higher cost.
Magnet Type | Max. Operating Temperature (°C) | Curie Temperature (°C) |
---|---|---|
Neodymium (N Series) | 80 | 310 |
Neodymium (M Series) | 100 | 340 |
Neodymium (H Series) | 120 | 340 |
Neodymium (SH Series) | 150 | 340 |
Neodymium (UH Series) | 180 | 350 |
Neodymium (EH Series) | 200 | 350 |
Samarium Cobalt | 350 | |
Alnico | 540 |
How Can Magnet Strength Loss Be Prevented?
Magnets will naturally lose some strength over time, but proper maintenance can significantly extend their lifespan and preserve their magnetic properties. Implementing optimal storage, temperature management, and handling techniques ensures magnets retain their power for years.
Proper Storage Techniques
Storage conditions are crucial in maintaining magnet strength. Store magnets in a dry environment to prevent corrosion, particularly if they aren’t coated. Magnets left in damp conditions may corrode, diminishing their magnetic properties.
For optimal storage of permanent magnets, keep opposite poles together by storing them in pairs to create a closed magnetic circuit that helps preserve their strength. For horseshoe magnets, use metal ‘keepers’ to connect both poles, redirecting the magnetic fields and preventing demagnetization.
Keep magnets away from electronic devices and magnetic storage media to avoid damaging devices and potentially weakening the magnets through interaction with other magnetic fields.
Temperature Management
Temperature extremes are among the most common causes of magnet strength loss. High temperatures can alter a magnet’s physical and chemical properties, causing them to lose strength. Each type of magnet has its own temperature threshold.
Neodymium magnets can lose magnetic properties at temperatures above 80°C (175°F). Ceramic magnets are vulnerable to cracking in cold temperatures. Alnico magnets are less affected by temperature but should still be kept under moderate conditions.
For magnets used in manufacturing or industrial processes, ensure they operate within their specified temperature range. If exposure to temperature fluctuations is unavoidable, select magnets with appropriate temperature ratings for your application.
Careful Handling Practices
Physical damage is a common cause of magnet strength loss. Magnets, especially rare earth types like neodymium, can be brittle. Dropping or allowing them to snap together may cause chips or cracks that compromise their strength.
When handling strong magnets, use non-metallic tools like plastic wedges to separate them rather than relying on manual force. Wear protective gear such as gloves and safety glasses to prevent injuries from flying chips or pinched skin.
For brittle magnets protected by casings or coatings, inspect these protective layers regularly. If the outer casing shows wear and tear, repair it to protect the interior magnet from damage and exposure to harmful elements.
Appropriate Magnet Selection
Prevention begins with selecting the right magnet for your specific application. Different environments require different magnetic materials:
For high-temperature applications, samarium cobalt magnets offer better temperature resistance than neodymium. In corrosive environments, choose magnets with appropriate protective coatings or inherent corrosion resistance.
Consider the geometry of your magnets, as some shapes resist demagnetization better than others. Longer magnets with smaller cross-sections are more vulnerable to demagnetization than shorter, thicker magnets of the same volume.
When purchasing magnets for critical applications, select appropriate grades designed to resist demagnetization in your intended operating conditions.
Magnet Type | Maximum Operating Temperature (°C) | Maximum Operating Temperature (°F) | Best Practices for Preserving Strength |
Neodymium | 80-100 | 175-212 | Store in dry, low-humidity environment; avoid exposure above 80°C |
Samarium Cobalt | 350 | 662 | Resistant to corrosion, maintain in low-humidity environment near room temperature |
Alnico | 540 | 1004 | Minimize humidity; avoid placing near strong opposing magnetic fields |
Ceramic (Ferrite) | – | – | Becomes more resistant at higher temperatures, store with consideration for cold temperature cracking |
By following these preventative measures, you can significantly extend the useful life of your magnets. While some strength loss over very long periods is inevitable, proper care can ensure that this loss remains minimal enough not to affect performance in most applications. Rare earth magnets stored in optimal conditions will lose only a small percentage of their strength over a century, making proper storage and handling well worth the effort.
Conclusion: Managing Magnet Strength for Optimal Performance
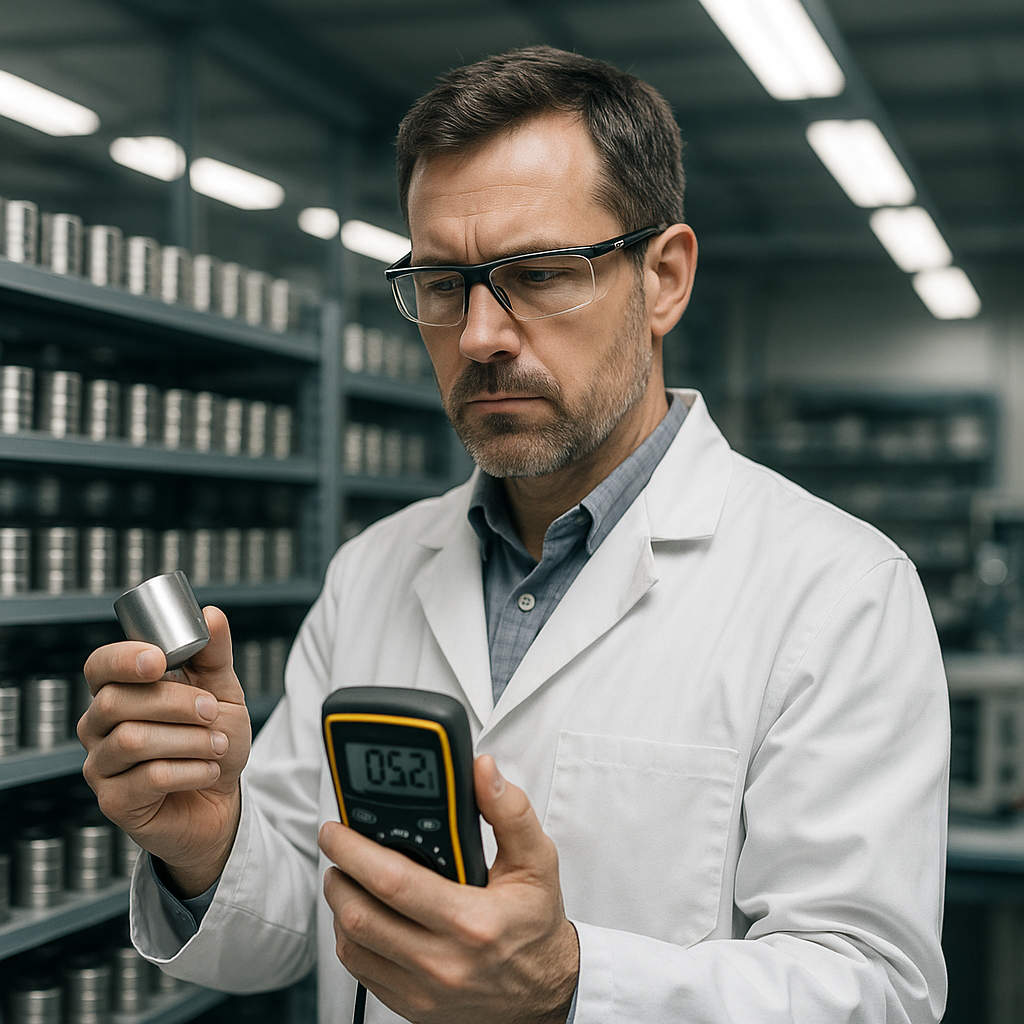
Understanding the factors that affect magnet strength is essential for maintaining optimal performance throughout a magnet’s lifecycle. Temperature fluctuations, improper storage, physical damage, and exposure to external magnetic fields can all contribute to diminished magnetic strength over time. By implementing proper handling and storage practices, users can significantly extend their magnets’ useful life and ensure consistent performance.
Proactive magnet maintenance is vital not just for preserving an investment but also for ensuring reliability in critical applications. Storing magnets in dry environments, using keepers between poles, avoiding extreme temperatures, and handling them with care prevent unnecessary degradation. In applications where precision is paramount, regular strength testing and occasional remagnetization may be necessary to maintain optimal performance. It is important to remember that different magnet types respond differently to environmental factors, so tailoring your maintenance approach to your specific magnets will yield the best results. For expert guidance on recycling magnets and other materials in your operation, contact Okon Recycling at 214-717-4083.