5901 Botham Jean Blvd, Dallas, TX 75215
Understanding What Is a Scrap Electromagnet
July 24, 2025A scrap electromagnet is a specialized industrial device engineered with a particularly deep magnetic field. These powerful tools play a vital role in junkyards and scrapyards worldwide, efficiently sorting and moving ferrous metal scraps throughout the facility.
Unlike standard magnets, scrap electromagnets are specifically designed to handle the irregular shapes and substantial weights typical in metal recycling operations. They operate on the same basic principles as ordinary electromagnets but offer enhanced power and durability to cope with the challenging conditions of scrapyard environments.
These durable magnets are typically attached to heavy machinery such as cranes or excavators. When electricity passes through the coiled wire inside the electromagnet, it generates a strong magnetic field that can attract and secure large quantities of ferrous materials. This capability makes them essential tools for modern recycling operations, where efficient material handling directly impacts productivity.
How Do Scrap Yard Electromagnets Work?
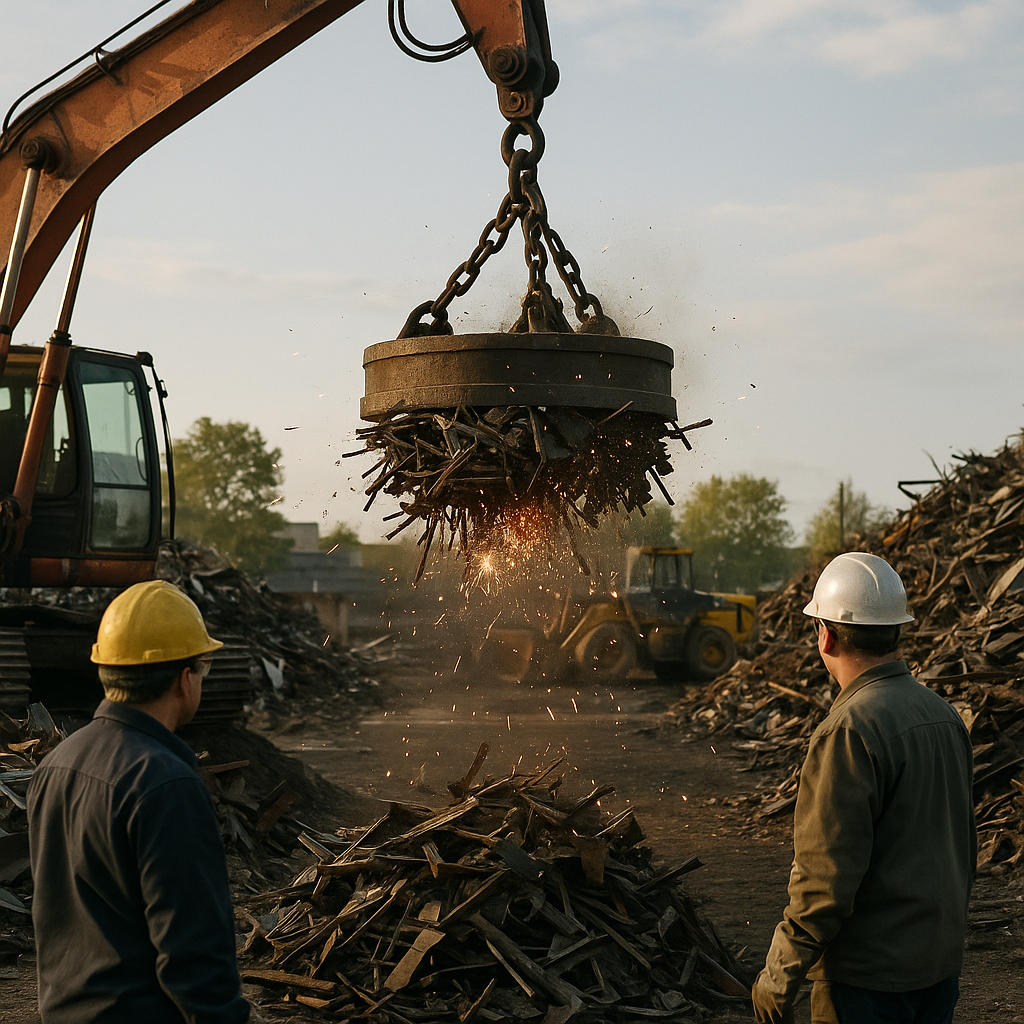
Scrap yard electromagnets operate through a straightforward yet powerful system. These vital recycling tools are powered by generators attached to the material handling machines. The generators create the electrical current needed to activate the magnet’s lifting capabilities.
Operators control these massive magnets from inside their machine cabs. The control system is simple; pressing one button engages the electromagnet, creating a strong magnetic field, while another button disengages it. This on-off capability gives operators precise control when lifting and releasing materials.
The electromagnet creates a magnetic field that specifically attracts ferrous metals—those containing iron, such as steel. The magnetic field penetrates deeply into piles of mixed scrap, allowing the magnet to effectively grab metal from beneath other materials. When activated, the magnetic field magnetizes the ferrous metals as if they were permanent magnets, causing them to stick firmly to the electromagnet’s surface.
Safety is a critical consideration with these powerful tools. If the electrical connection is lost due to a broken wire, generator failure, or belt break, the electromagnet immediately loses its magnetic properties. Operators must always be prepared for the possibility that material could suddenly drop if power is interrupted.
The ability to selectively attract only ferrous metals makes electromagnets invaluable for sorting operations. Non-ferrous materials like aluminum, copper, and debris remain behind, creating a natural separation. This selective attraction enables scrapyards to efficiently sort mixed materials, removing valuable ferrous metals from waste streams with minimal manual intervention.
The lifting capacity of scrapyard electromagnets varies significantly based on their size and power. Smaller units might lift a few hundred pounds, while industrial-grade electromagnets can hoist several tons of metal in a single lift. This versatility makes them adaptable to various recycling operations—from small-scale sorting to large industrial processing.
What makes these electromagnets particularly valuable in modern recycling operations is their ability to create a clean separation between ferrous and non-ferrous materials with minimal human intervention. This technology forms the foundation of efficient metal recycling processes worldwide.
Model | Diameter (in) | Weight (lbs) | Rated Power (W) | Lifting Capacity (lbs) – Light Scrap |
---|---|---|---|---|
EMG 085 SM | 34 | 1550 | 3900 | 400 |
EMG 105 SM | 41 | 1900 | 5500 | 485 |
EMG 115 SM | 45 | 2470 | 6820 | 640 |
EMG 125 SM | 49 | 3100 | 8580 | 770 |
EMG 135 SM | 53 | 3850 | 10120 | 900 |
EMG 145 SM | 57 | 4750 | 11440 | 1060 |
EMG 155 SM | 61 | 5950 | 13400 | 1320 |
EMG 170 SM | 67 | 7100 | 15840 | 1560 |
EMG 185 SM | 73 | 8830 | 18700 | 1850 |
EMG 200 SM | 79 | 9920 | 23100 | 2180 |
What Are the Key Features of Scrap Electromagnets?
Scrap electromagnets are specialized industrial tools designed with several key features that enable them to perform effectively in demanding recycling environments. These powerful magnets must withstand harsh conditions while maintaining reliable performance.
Moisture-Proof Construction
Scrap electromagnets incorporate moisture-proof insulation as a crucial feature. This insulation protects internal components from water damage and prevents operational failures in wet environments common in scrapyards.
The protective insulation often includes multiple layers of waterproof materials. This engineering prevents moisture from reaching the copper coils and electrical connections, which could otherwise cause shorts or corrosion.
Without proper moisture protection, scrap magnets would quickly deteriorate when exposed to rain, snow, or high humidity conditions common in outdoor recycling facilities.
Deep Magnetic Field Design
A defining characteristic of scrap electromagnets is their capability to produce a deep magnetic field. Unlike standard electromagnets, scrap versions are designed to project their magnetic force deeper into material piles.
This deep field allows the magnets to attract ferrous materials buried beneath layers of mixed waste. The field’s strength and depth directly affect how effectively the magnet can sort through and lift metal from recycling streams.
The magnetic field depth varies between models. Larger scrap magnets with stronger fields are ideal for recycling applications with larger-sized materials and higher throughput requirements.
Heat-Resistant Capabilities
Many scrap electromagnets feature heat-resistant designs that withstand temperatures up to 650°C. This capability is essential when handling recently processed metal that remains hot from manufacturing or cutting operations.
Heat-resistant models use specialized materials and insulation techniques to prevent overheating of internal components. These designs ensure the magnet maintains its lifting power even when exposed to extreme temperatures.
Without heat resistance, magnets would fail when handling hot materials from foundries, steel mills, or other industrial operations where metal is processed at high temperatures.
Robust Component Design
Scrap electromagnets incorporate several key components to ensure reliable operation:
- Generator systems that provide consistent power to the electromagnet
- High-strength steel bodies that resist damage from impacts and abrasion
- Heavy-duty terminal boxes protected from environmental exposure
- Reinforced suspension systems with steel chains for secure lifting
- Durable outer shells made from non-magnetic stainless steel or other wear-resistant materials
The robust construction of these components allows scrap electromagnets to withstand the constant stress of industrial recycling operations. The high-strength steel construction provides the durability needed in environments where heavy, sharp metal objects are handled regularly.
Electromagnet Type | Features | Applications |
---|---|---|
Electromagnetic Lifting Magnets | Variable holding capacity, Control over magnetic strength, Suitable for frequent load changes | Scrapyards, Warehouses, Recycling facilities, Steel processing |
Permanent Lifting Magnets | No external power needed, Fixed magnetic strength | Metal fabrication, Machining, Steel manufacturing |
Electro Permanent Lifting Magnets | Energy-saving, Safety in lifting operations, No need for constant power | Construction, Shipbuilding, Remote applications |
These specialized features make scrap electromagnets suitable for the demanding tasks of separating, sorting, and moving ferrous materials in recycling facilities. Their unique design allows them to operate efficiently in conditions that would quickly damage conventional magnets.
Maintenance Best Practices for Scrap Electromagnets
To ensure the long-term performance and safety of scrap electromagnets, routine maintenance is essential. These high-demand tools operate in rugged environments, often exposed to vibration, extreme temperatures, moisture, and metal debris. Proactive upkeep minimizes downtime, prevents costly breakdowns, and extends their service life.
Daily Inspections
Operators should conduct visual inspections before each shift. This includes checking for wear on power cables, inspecting the surface for cracks or deformation, and ensuring that lifting chains and shackles are secure. Any signs of overheating, corrosion, or fluid ingress should prompt immediate servicing.
Coil and Power Checks
The internal coil is the heart of an electromagnet. Regularly testing coil resistance can reveal early signs of degradation or short circuits. Voltage and current levels should also be measured under load to confirm the power system’s performance. Generator belts and fuel levels (if applicable) must be routinely checked.
Terminal Box Sealing
Electromagnets often come with sealed terminal boxes, which should be inspected for gasket integrity, ensuring all electrical connections are tight and corrosion-free. Moisture inside a terminal box can cause shorts or catastrophic failure if not promptly addressed.
Cleaning and Debris Removal
Metal shavings, dust, and grime naturally accumulate on the magnet surface and housing. Regular cleaning reduces the risk of material buildup interfering with magnetic performance or damaging the protective casing. Use non-metallic brushes or compressed air to clean components safely.
Cooling System Maintenance
Some high-duty electromagnets are liquid-cooled and require regular inspection of coolant levels, hose conditions, and pump functionality. Heat buildup from a failing cooling system can quickly degrade coil insulation and reduce lifting power.
By integrating these maintenance practices into daily operations, scrapyards and recycling facilities can protect their equipment investment and avoid unexpected outages. A well-maintained scrap electromagnet delivers consistent performance, enhances operator safety, and supports the overall efficiency of metal recovery workflows.
Conclusion: The Importance of Scrap Electromagnets in Metal Recycling
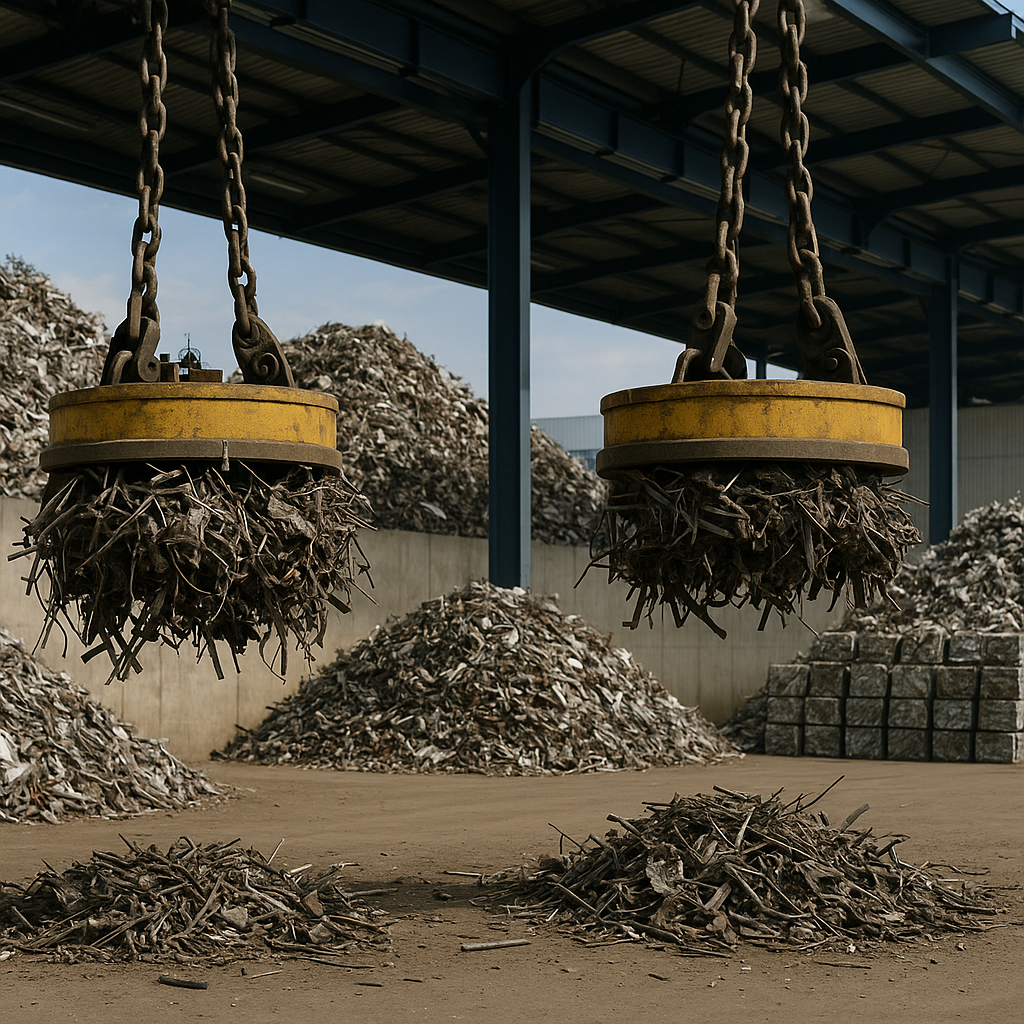
Scrap electromagnets are essential in modern metal recycling operations, enabling the selective lifting and sorting of ferrous metals, which significantly streamlines processes in scrapyards and recycling facilities. By efficiently handling various types and sizes of metal scrap, these electromagnets transform what was once a labor-intensive process into a streamlined operation.
The impact of scrap electromagnets goes beyond operational efficiency. By enhancing metal recovery rates and the purity of recycled materials, they contribute to resource conservation and waste reduction. Their ability to separate ferrous metals from mixed waste streams reduces the need for raw material extraction through mining, helping to minimize environmental degradation, habitat destruction, and greenhouse gas emissions. This technology plays a critical role in the efforts to build a more sustainable, circular economy for metal resources.
For businesses seeking to optimize their metal recycling operations, contact Okon Recycling at 214-717-4083. Our expertise in scrap handling equipment and recycling solutions can help you implement the right electromagnet technology for your specific needs.