5901 Botham Jean Blvd, Dallas, TX 75215
What Are the Key Challenges in Recycling Rare Earth Magnets?
July 24, 2025Less than 1% of end-of-life rare earth magnets are recycled globally—a startling statistic that reveals a major sustainability blind spot in our high-tech economy. These magnets are crucial components in technologies such as electric vehicles, wind turbines, smartphones, and advanced medical equipment.
Despite their widespread use and significance, most of these powerful magnets are discarded rather than recovered, increasing the pressure on finite rare earth resources.
Challenges in Rare Earth Magnet Recycling
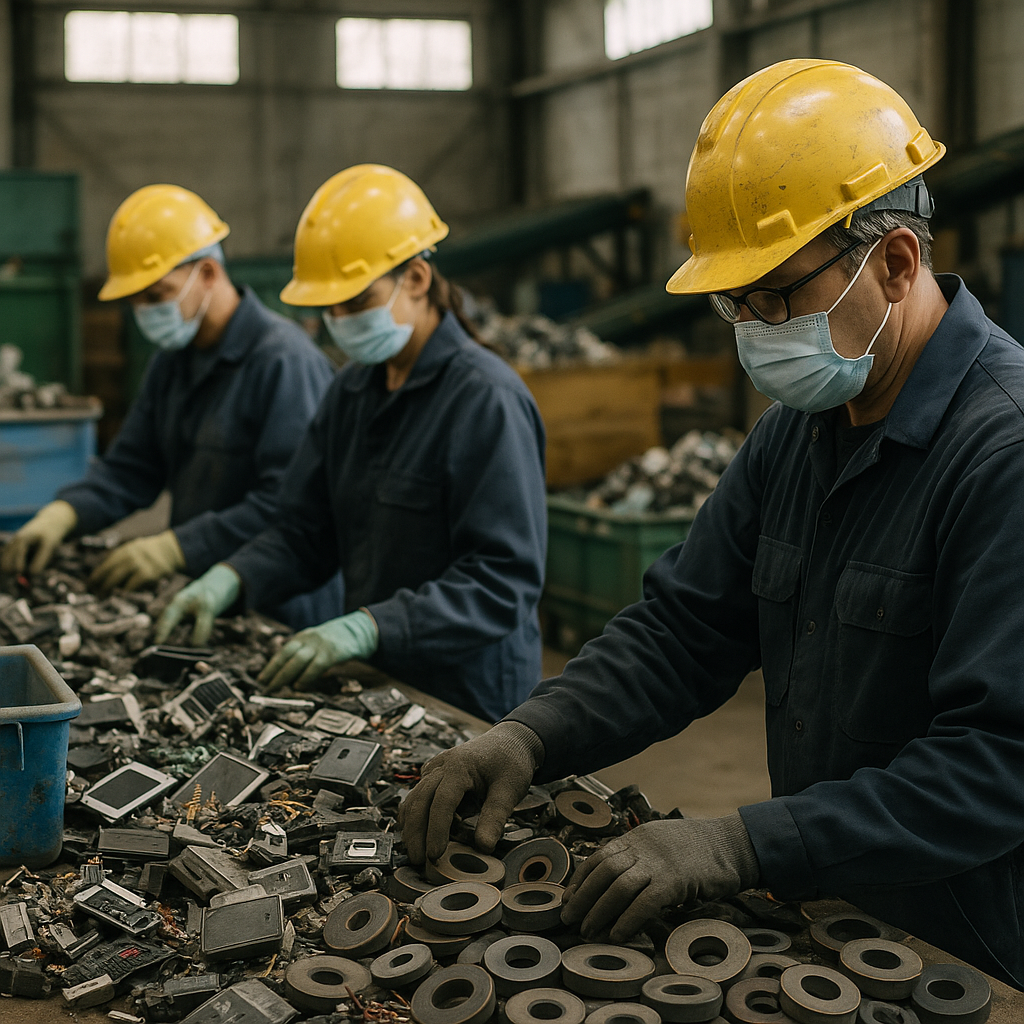
The issue isn’t about a lack of value—rare earth magnets are among the most valuable and hard-to-source materials in today’s economy. The low recycling rate is primarily due to technical, economic, and logistical obstacles. These magnets are often deeply integrated into complex assemblies, secured with adhesives, and protected with coatings, making them difficult to identify, extract, and purify for reuse. Even when recovery is technically feasible, the process is usually cost-prohibitive, especially when compared to importing newly mined materials from countries with lower production costs.
Another significant challenge is the lack of infrastructure. Few established collection systems are specifically designed to capture end-of-life products containing rare earth magnets. Unlike aluminum cans or glass bottles, these items don’t have a dedicated recycling stream. As a result, valuable materials are lost in general e-waste or metal scrap, where they are rarely retrieved. The unpredictable and varied nature of e-waste further complicates the situation—products differ widely in design, magnet type, and material quality, making automated recycling impractical.
Contamination is an additional complication. Magnets often have coatings such as nickel, copper, or epoxy and are surrounded by other materials that can degrade the quality of the recycled product. Even minor impurities can reduce magnetic performance by up to 25%, rendering recycled magnets unsuitable for high-end applications. Without advanced separation and purification methods, the recycled material may not meet stringent manufacturing standards, limiting its usability and market appeal.
In conclusion, recycling rare earth magnets remains one of the most urgent yet under-addressed sustainability challenges. Addressing it requires not only technological innovation but also systemic change across product design, waste collection, processing infrastructure, and policy frameworks. The following sections will explore the specific economic, logistical, and regulatory obstacles to rare earth magnet recycling—and the strategies that could help overcome them.
What are the economic and supply chain barriers?
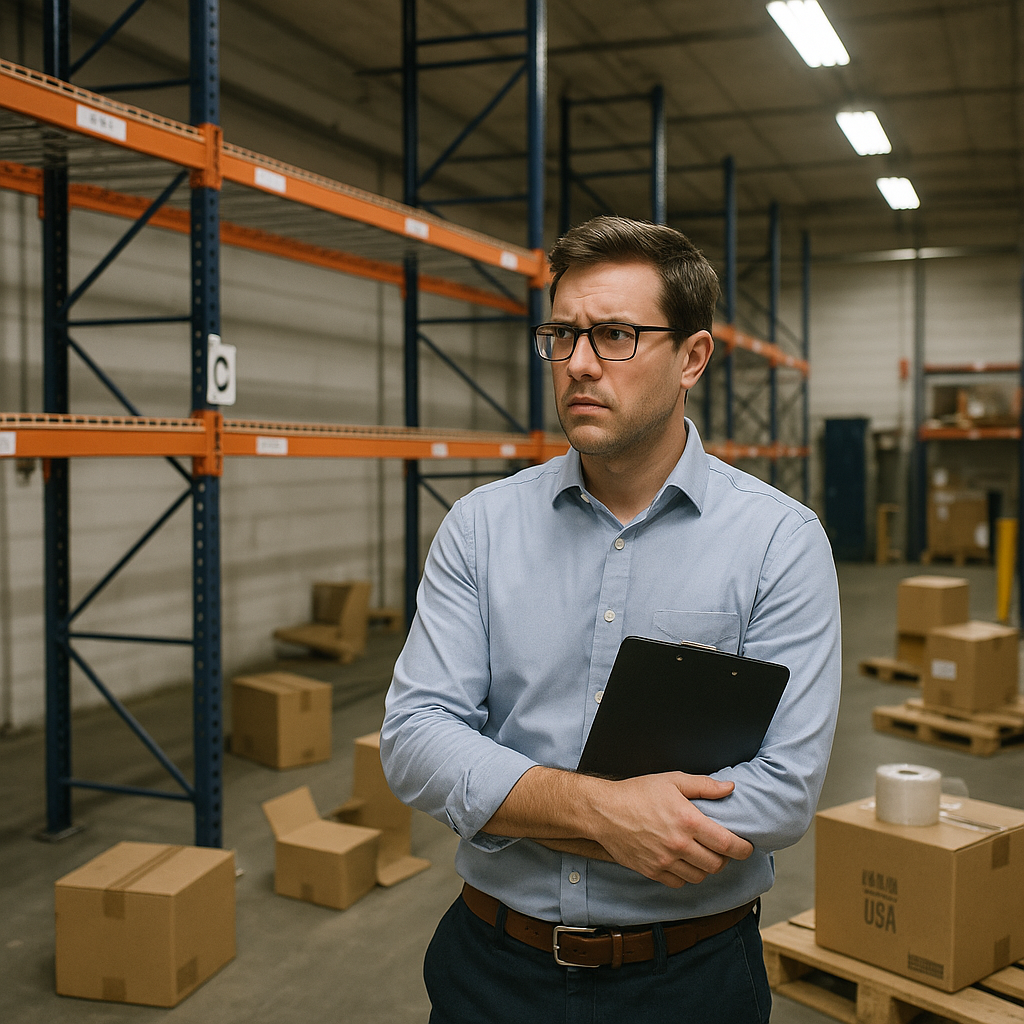
The development of magnet recycling in Europe faces substantial economic and supply chain challenges that hinder scalable adoption. Chief among these are high extraction costs, stemming from the labor-intensive process of disassembling end-of-life products where magnets are firmly embedded and bonded with adhesives. This manual work significantly raises operational costs, making recycled magnets more expensive than their virgin counterparts.
Compounding this issue is the global price competition, particularly with Chinese-sourced primary magnets. China’s dominance in the rare earth industry, supported by an integrated and subsidized supply chain, allows it to offer lower prices that recycled materials from Europe cannot easily match. Consequently, most companies opt for cheaper imports over the premium for recycled content, despite its environmental benefits.
Market volatility further weakens economic feasibility. Prices for rare earth elements are known to fluctuate dramatically, making it difficult for recyclers to forecast revenue or attract long-term investment. When prices drop, the already narrow margins for recycling operations become unsustainable, discouraging further development of the sector.
- High extraction costs due to manual disassembly requirements
- Price competition with cheaper imported primary magnets
- Volatile rare earth prices creating financial uncertainty
- Limited market demand for recycled magnets
- High energy costs impacting process economics
Supply chain fragmentation presents another major obstacle. A robust recycling ecosystem requires coordination among equipment manufacturers, dismantlers, and material processors—yet such collaboration is rare outside pilot projects. Most existing recycling initiatives operate in isolation, lacking the consistent input and shared logistics needed for reliable operations. The absence of standardized recycling loops undermines both material recovery rates and economic efficiency.
Moreover, the current flow of magnet-containing waste is insufficient to support large-scale operations. Many electronic products contain only small amounts of magnet material, and bulkier sources like electric vehicles and wind turbines are just beginning to enter the waste stream in significant volumes. Until this volume increases and becomes more predictable, it remains risky for businesses to invest in specialized magnet recovery processes.
A case in point is the Urban Mining Company in Texas, which pioneered a magnet-to-magnet recycling method but struggled to maintain a steady supply of end-of-life magnets. Despite its technical capabilities, the company faced supply disruptions and fierce competition from lower-cost Chinese producers, illustrating how economic and logistical realities can undercut even the most innovative efforts.
To overcome these barriers, strategic interventions are needed at both industry and policy levels—ranging from supply chain integration and waste stream forecasting to financial incentives and stronger market signals for recycled content. Without such action, rare earth magnet recycling will continue to face uphill economic and logistical battles in Europe and beyond.
How can policy and regulations address magnet recycling challenges?
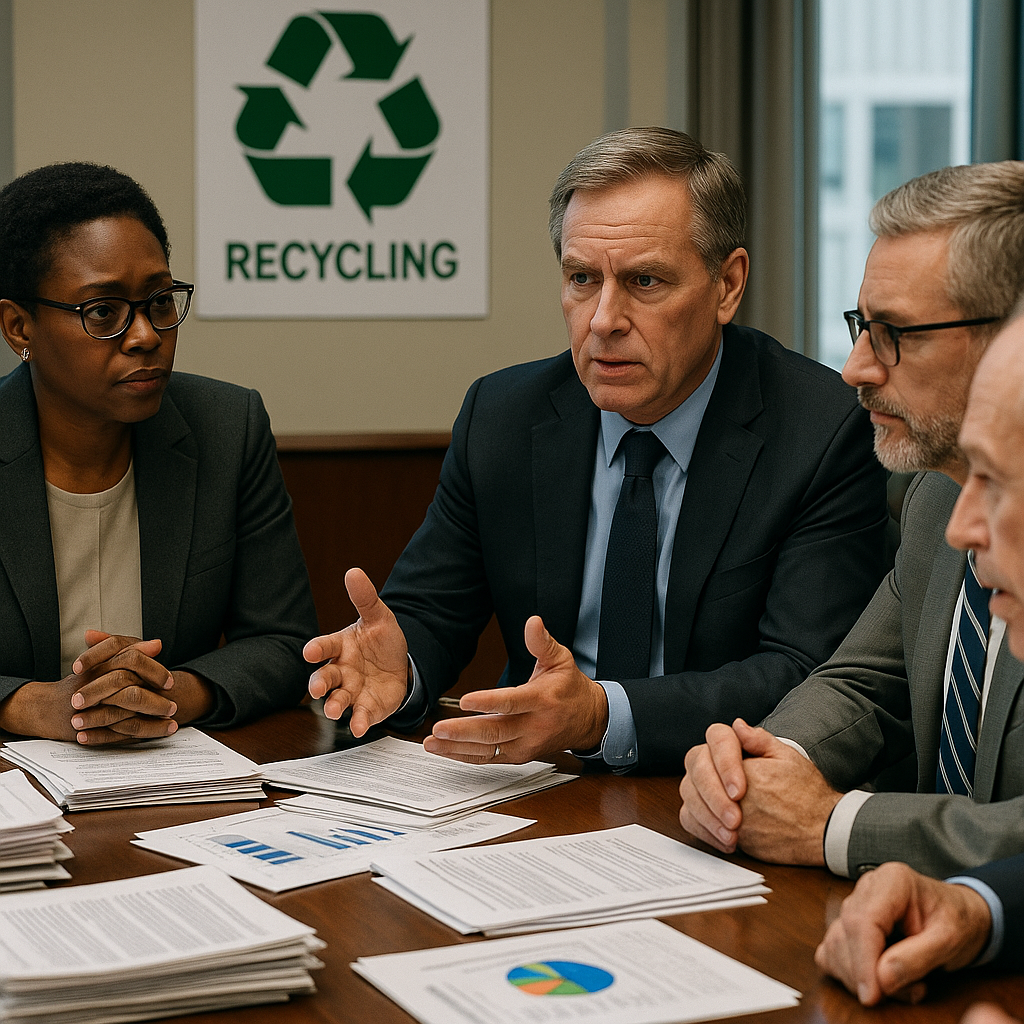
Recycling rare earth magnets presents significant technical and economic challenges that require systemic intervention. Policy and regulation play a crucial role in establishing a viable market for recycled magnets by creating supportive conditions that encourage collection, investment, and innovation. Targeted regulatory measures can help overcome many current obstacles facing this sector.
A promising tool is the implementation of recycled content targets. By mandating that a minimum percentage of new magnets include recycled material, governments can ensure a stable market for recyclers. This approach, already used in battery legislation, promotes a circular economy. The European Union sets a strong example with its Critical Raw Materials Act, aiming to recycle at least 15% of annual rare earth consumption.
Product labeling requirements also offer significant potential. Without clear indicators, recyclers struggle to locate and identify rare earth magnets within complex devices. Mandatory labeling, including digital product passports, could provide essential data such as magnet composition, placement, and size. This transparency would improve dismantling efficiency, reduce labor costs, and increase recovery rates overall.
Increased public investment in research and development (R&D) is another critical element of the policy strategy. Advanced recovery techniques—such as hydrogen-based separation processes—require pilot testing, scale-up, and technical validation, all supported by government grants or subsidies. R&D funding accelerates innovation and can reduce long-term processing costs, bringing recycled magnets closer to price parity with virgin materials.
Certification systems for recycled magnets would help resolve market hesitancy. Manufacturers often avoid secondary materials due to uncertainty about quality and consistency. A formal certification framework verifying the magnetic performance and composition of recycled products could reassure buyers and encourage wider adoption in industrial applications.
Creating a Supportive Policy Environment
Addressing the rare earth magnet recycling challenges demands a comprehensive and coordinated policy approach. Rather than relying on isolated measures, governments should integrate complementary tools into a broader strategy addressing both supply and demand challenges. Key policy elements might include:
- Extended producer responsibility schemes requiring manufacturers to plan for and finance the recycling of products containing magnets
- Streamlined cross-border waste transport rules to facilitate moving end-of-life products to specialized facilities
- Tax credits or financial incentives for businesses investing in magnet recovery technologies
- Design-for-recycling regulations encouraging modular, magnet-accessible product designs
Governments adopting such policies could dramatically alter the economics of magnet recycling. With clearer market signals, reduced financial risk, and stronger technical infrastructure, recycling initiatives could scale more quickly and attract private sector involvement. This would reduce environmental degradation from primary extraction and enhance supply chain resilience for critical materials.
International coordination is also important. Rare earth supply chains are global, and inconsistent regulations across borders can hinder progress. By aligning standards for labeling, certification, and recovery processes, countries can collectively build more robust, transparent, and environmentally sound recycling systems. This multilateral cooperation is crucial for a truly circular economy for rare earth magnets.
Finally, policies must be carefully phased in to balance ambition with practical business realities. Gradual implementation allows companies to adapt while ensuring consistent progress toward environmental goals. Examples like the EU’s Critical Raw Materials Act show that thoughtful regulation can drive innovation and market transformation without imposing undue burden on industry.
What role does product design play in magnet recyclability?
Design choices made during product development significantly impact the recyclability of rare earth magnets. Many products today are not designed for easy disassembly or material recovery, making magnet extraction difficult and inefficient. Embedding magnets within sealed modules, using strong adhesives, or encasing them in non-magnetic components complicates recovery, increasing labor and cost challenges during recycling.
Adopting ecodesign principles can greatly enhance magnet recyclability. These include modular designs with easily separable components, using reversible fasteners rather than glue, and incorporating standardized magnet types and locations within devices. When magnets are easy to identify and access, recovery rates and material quality improve, making the recycling process more economically viable.
Digital tools like CAD-based disassembly maps and product passports can support better recycling outcomes. If recyclers know in advance the exact location, size, and composition of magnets within a product, they can streamline dismantling processes and reduce the need for manual sorting. This also facilitates partial automation, lessening reliance on labor-intensive methods.
Product design also impacts contamination risks. Using coatings or housing materials that are easy to separate without chemical treatments helps maintain the purity of recycled magnets. Some manufacturers are exploring magnet encapsulation methods that provide both protection during use and ease of separation at the end of life, balancing performance and recyclability.
Regulatory incentives and industry standards can expedite the adoption of recyclable design features. Ecodesign directives, procurement criteria favoring recyclable products, and industry certifications can all encourage manufacturers to prioritize recycling in design. Ultimately, integrating recyclability into the design phase reduces environmental impact, supports material circularity, and strengthens supply chain resilience.
Conclusion
Recycling rare earth magnets is one of the most urgent and under-leveraged opportunities for advancing sustainable industry and securing critical material supply chains. The scale of the problem is clear: billions of devices contain rare earth magnets, yet less than 1% are ever recycled. This massive disconnect underscores the need for comprehensive strategies that span policy, technology, economics, and design.
To meet this challenge, manufacturers must design products with end-of-life recovery in mind, embedding disassembly and separation considerations early in the development process. Governments must enact supportive regulations—such as recycled content mandates, extended producer responsibility schemes, and international certification standards—that create demand, reduce financial risk, and support market stability. Meanwhile, investment in advanced separation technologies and collection infrastructure is critical to ensuring recycled magnets meet the quality and consistency needed for industrial reuse.
Importantly, addressing rare earth magnet recycling is not just about resource efficiency—it’s about resilience. As global supply chains become more volatile and geopolitical risks rise, the ability to recover valuable materials domestically becomes a strategic necessity. At the same time, effective recycling reduces the environmental damage caused by mining, cutting greenhouse gas emissions, habitat destruction, and water pollution.
Call Okon Recycling at 214-717-4083 for all your recycling needs.