5901 Botham Jean Blvd, Dallas, TX 75215
What Are Magnetic Separators and Why Repurpose Them?
July 24, 2025Magnetic separators play a crucial role in recycling facilities worldwide, using magnetic fields to efficiently extract ferrous metals like iron and steel from mixed waste streams. These devices range from simple suspended magnets to sophisticated rotating drum systems that sort materials with remarkable precision. They operate on a straightforward principle: as materials pass through the separator, ferrous items are attracted to the magnetic surface while non-magnetic materials continue along their original path.
With recycling technology advancing rapidly, many facilities have older magnetic separator models that no longer meet current efficiency standards. Yet, these outdated units contain valuable components, including powerful magnets, durable metal frameworks, and specialized materials, which shouldn’t simply be discarded. The growing focus on circular economy principles has many waste management professionals reconsidering the potential of these aging units.
Repurposing outdated magnetic separators offers significant environmental and economic benefits. Financially, refurbishing or retrofitting an existing separator generally costs 40–60% less than purchasing a new model. Companies can extract valuable components like rare earth magnets for use in other applications or upgrade specific parts to improve performance without complete replacement. Beyond cost savings, repurposing reduces environmental impact by keeping valuable resources in use and minimizing the carbon footprint associated with manufacturing new equipment.
How Can Old Magnetic Separators Be Repurposed in Recycling?
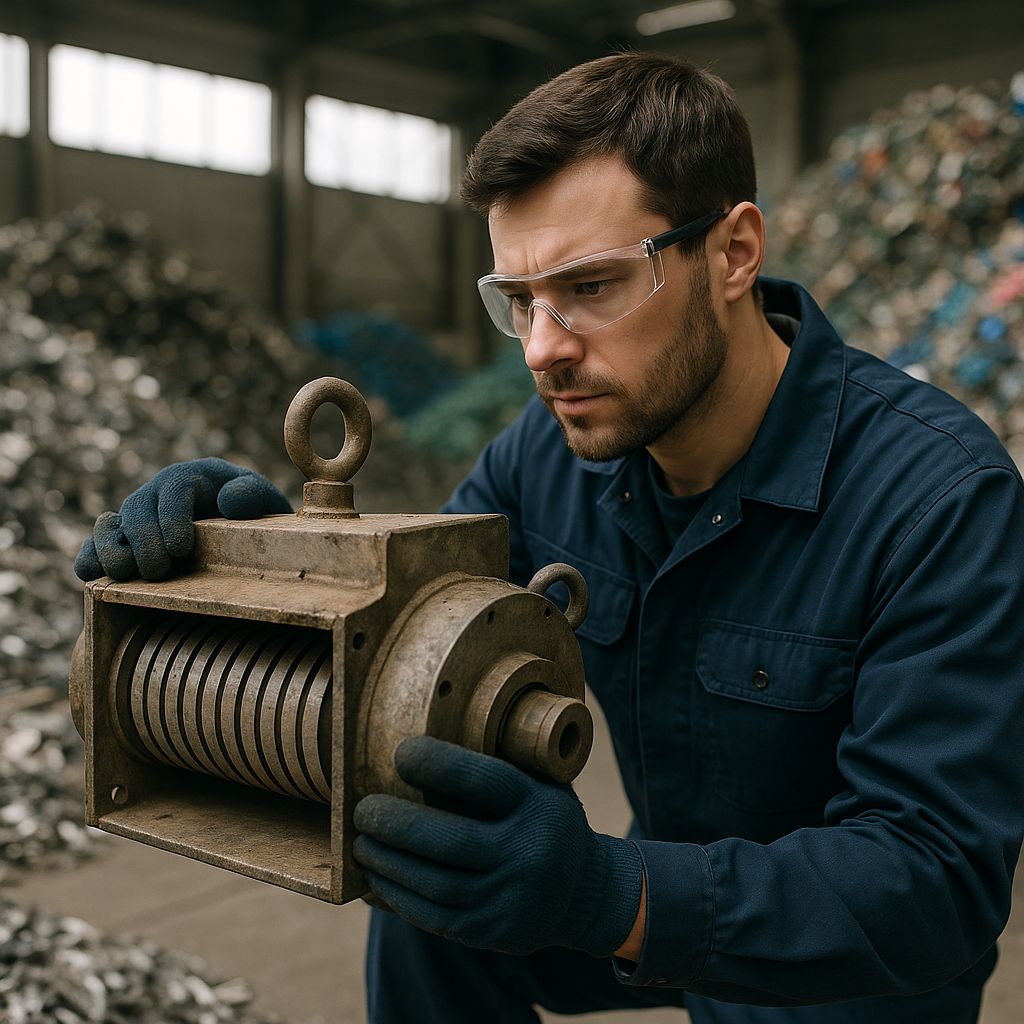
Older magnetic separators remain valuable assets in recycling operations even after years of service. With proper refurbishment and strategic modifications, these workhorses of the recycling industry can gain extended life and improved performance. Instead of opting for replacement, facilities can take practical steps to rejuvenate existing equipment.
Upgrading Magnet Strength
One effective way to repurpose old magnetic separators is by upgrading the magnetic components. The magnetic field strength directly affects separation efficiency and can often be enhanced without replacing the entire unit.
Older ferrite or ceramic magnets can be replaced with newer neodymium rare earth magnets. These powerful magnets, available since the late 1980s, provide much higher magnetic field intensity and better separation capability for the same physical size.
Facilities can also add supplementary magnetic elements to increase the effective magnetic zone without a complete overhaul. This upgrade benefits operations handling materials with weak magnetic properties.
Modifying Separator Design Systems
Adjusting the design configuration of older separators can improve functionality significantly. Several modifications can transform performance without major investments.
The positioning of magnetic elements can be reconfigured to create a more efficient separation pattern. For drum systems, adjusting the internal magnet assembly angle can enhance separation effectiveness for specific material types.
Converting a stationary magnetic separator to a self-cleaning model adds automation. This involves installing multi-ply rubber belts with vulcanized cleats that automatically discharge captured ferrous metals.
Integrating modern control systems can allow for precise adjustments based on material flow characteristics. Simple sensor additions can help optimize the separation process by providing real-time feedback.
Repurposing Individual Components
Sometimes the most practical approach is to salvage and repurpose specific components rather than refurbishing the entire unit.
Conveyor belts from older separators can be reused for other material handling applications within the facility. Durable components like rollers, motors, and frames often outlast the separator’s magnetic elements.
The structural frame can serve as a foundation for different separation technologies. For example, an older magnetic separator frame might be converted to support an eddy current separator for non-ferrous metal recovery.
Control panels and electrical systems can be updated with modern components while retaining the existing housing and connections. This hybrid approach combines the durability of older equipment with the precision of newer technology.
Performance Enhancement Through Maintenance
Beyond modifications, thorough maintenance can significantly improve the performance of aging magnetic separators.
Deep cleaning of magnetic faces removes accumulated fine particles that diminish magnetic effectiveness. Over time, these particles can create a barrier that reduces magnetic field penetration.
Replacing worn belts and mechanical components addresses operational inefficiencies before they cause downtime. Worn components often contribute to poor separation results more than magnetic field strength.
Regular magnetic strength testing helps identify when specific areas need reinforcement. Pull test kits can verify whether magnetic field strength meets operational requirements.
Applying corrosion-resistant coatings extends equipment life, particularly in facilities processing materials with high moisture content or corrosive properties.
By implementing these practical refurbishment approaches, recycling facilities can extend equipment life cycles, improve operational efficiency, and maximize return on their original investment in magnetic separation technology.
What Role Do Magnetic Separators Play in Optimizing Recycling Streams?
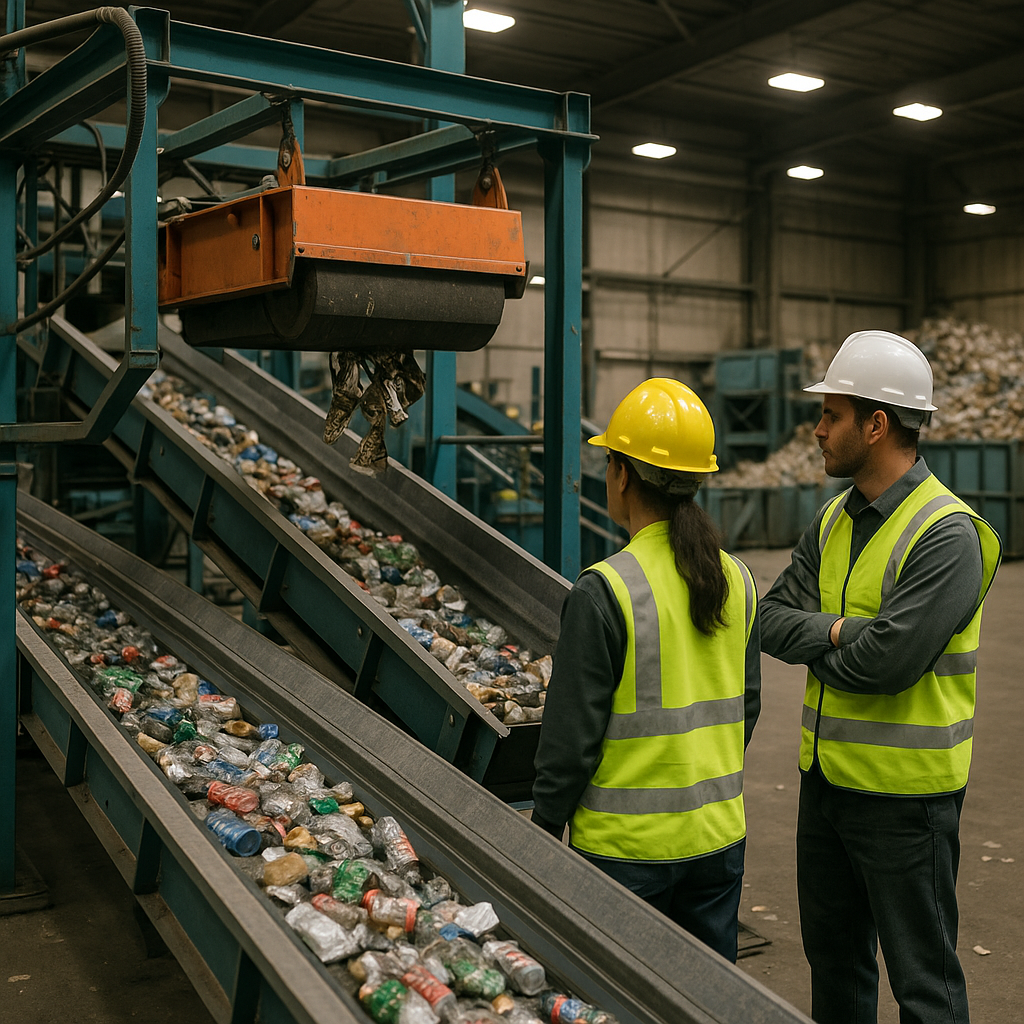
Magnetic separators are crucial for streamlining recycling workflows and enhancing material purity. These devices serve as the first line of defense in mixed material recovery, helping separate recyclable metals before materials move to more specialized processing steps. This function not only enhances the effectiveness of downstream systems like eddy current separators and optical sorters but also reduces wear on mechanical equipment by removing abrasive ferrous debris early in the process.
In multi-material recycling facilities, magnetic separators are strategically placed at various stages. Suspended magnets above conveyor belts remove ferrous contaminants from shredded plastics or paper, while drum magnets efficiently separate metals from glass cullet. These placements reduce cross-contamination between material types, improving the quality and marketability of recovered resources.
Advanced systems allow for fine-tuned separation of weakly magnetic metals such as stainless steel or contaminated ferrous materials. This capability supports the growing demand for high-purity recycled content in industries like automotive manufacturing and electronics, where consistent input quality is critical.
Ultimately, magnetic separators not only contribute to efficient metal recovery but also optimize the entire recycling operation by ensuring cleaner input streams, reducing equipment downtime, and enabling higher throughput. Repurposing or upgrading these devices extends these benefits while reducing capital expenditure and environmental impact.
Environmental Benefits of Repurposing Magnetic Separation Equipment
Recycling facilities that repurpose magnetic separators contribute to environmental goals beyond operational savings. Each refurbished or upgraded separator reduces the environmental impact linked to manufacturing new equipment, such as energy use, raw material extraction, and emissions from transportation.
Producing a new magnetic separator requires energy-intensive processes like steel fabrication, coil production, and rare earth magnet mining. In contrast, repurposing old equipment conserves these resources and often extends the life of key components, such as motors and structural frames, by several years.
Furthermore, reusing magnetic elements—particularly rare earth magnets—reduces the need for newly mined neodymium or dysprosium, often sourced through environmentally harmful mining practices. Refurbishing equipment supports circular economy goals by prolonging the use of valuable materials and minimizing waste.
Facilities that choose refurbishment over disposal avoid adding to the growing industrial equipment waste stream. Magnetic separators, which can weigh several tons, contain mixed materials that are challenging to recycle. Repurposing alleviates landfill pressure and conserves space in systems not designed for large-scale industrial machinery.
Incorporating repurposed equipment into operational strategies reflects environmental leadership. It supports sustainability reporting goals, contributes to lower emissions per ton of processed material, and effectively reduces the overall carbon footprint of recycling operations.
Conclusion
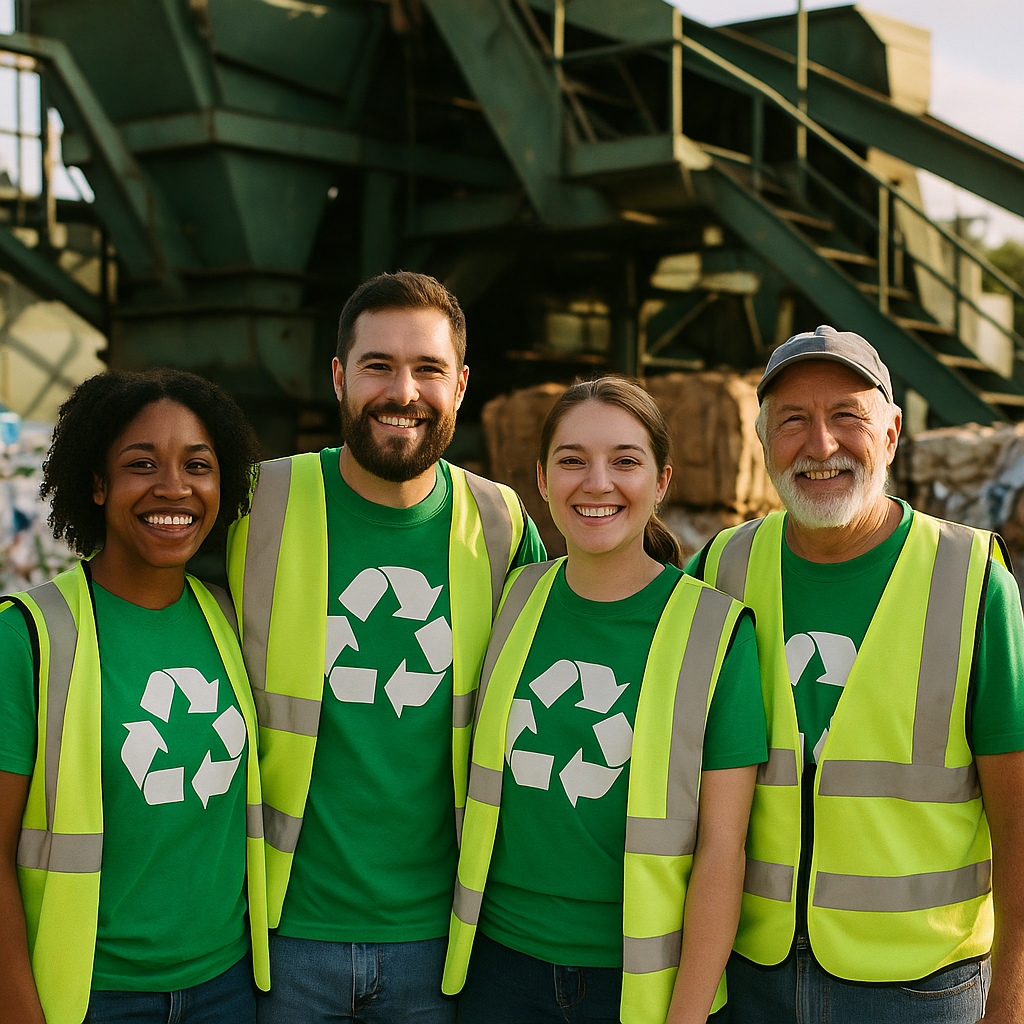
Magnetic separators are essential tools in recycling, and their value remains intact with age. Through refurbishment, component repurposing, and targeted upgrades, facilities can rejuvenate these machines, saving costs and reducing environmental impact. Enhancing separation efficiency and supporting circular economy goals, extending the lifecycle of magnetic separation equipment is both practical and sustainable.
For expert support in evaluating and repurposing your magnetic recycling equipment, contact Okon Recycling at 214-717-4083.