5901 Botham Jean Blvd, Dallas, TX 75215
Scrap Metal Baler: Everything You Need to Know
July 20, 2025A scrap metal baler is a specialized machine designed to efficiently compress scrap metal into compact, regular-shaped blocks, such as rectangular or cylindrical forms. This process significantly reduces the volume of scrap metal, enhancing storage and transportation efficiency. Scrap metal balers, also known as metal scrap baling machines or compactors, play a crucial role in the metal recycling industry by transforming loose metal scraps into manageable, dense bales.
In Europe, more than half of steel production comes from recycled materials. The metal recycling industry relies heavily on these powerful machines to process the enormous quantities of scrap generated daily.
Whether handling aluminum cans from municipal recycling programs or processing industrial metal waste, these robust machines serve as the backbone of efficient metal recovery operations.
How Does a Scrap Metal Baler Work?
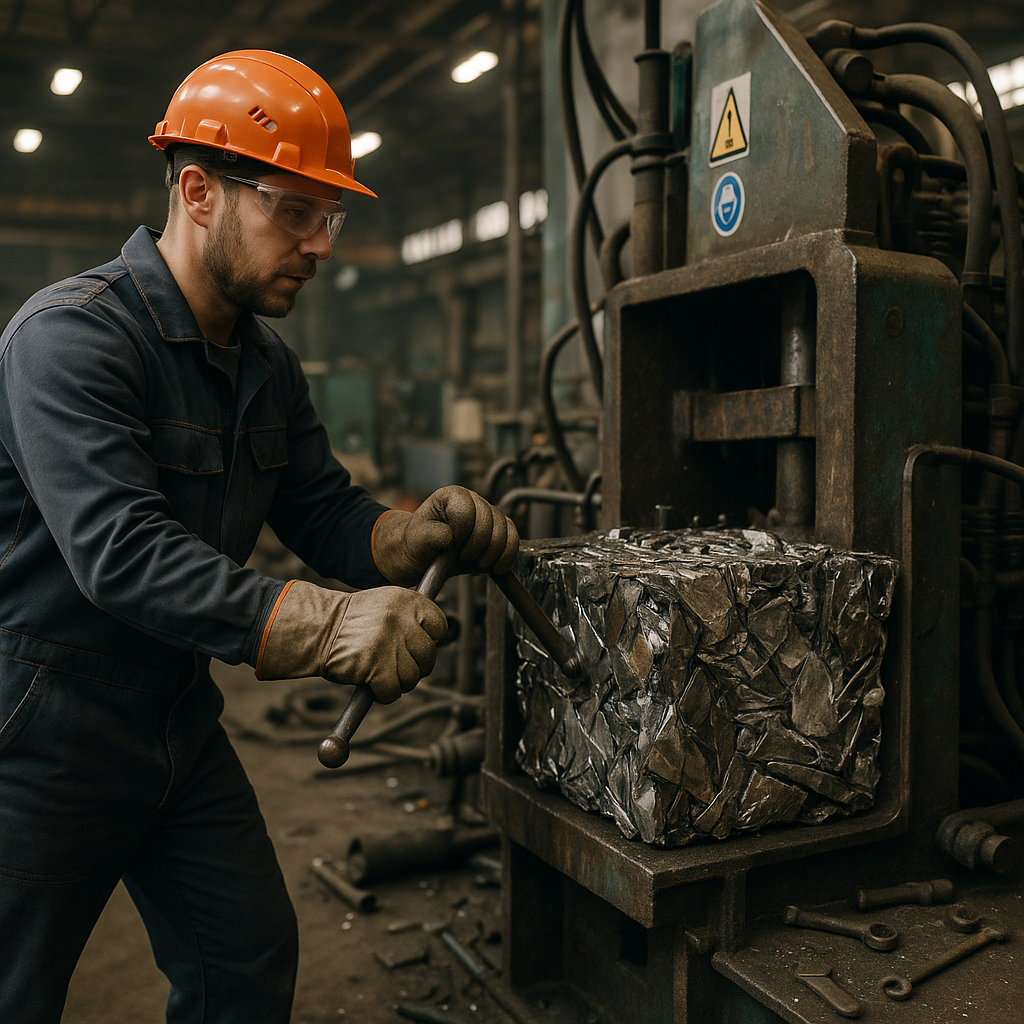
Scrap metal balers transform loose metal into compact, manageable bales using powerful hydraulic systems. These machines play a crucial role in the recycling industry by making scrap metal easier to transport, store, and process.
Operation begins with loading. Operators feed loose scrap metal into the baler’s hopper or chamber. This can be done manually or through automated conveyor systems, depending on facility setup and volume requirements.
Once loaded, the hydraulic system activates. Hydraulic cylinders generate immense pressure, pushing a ram or pressure head toward the metal. Hydraulic fluid transfers force from electric motors to the compression components.
Inside the compression chamber, also known as the baling chamber, the scrap undergoes intense pressure. The ram compresses the metal from one or multiple directions. Some advanced models feature three-sided compression for maximum density.
Compression continues until the metal forms a dense block. The baler applies thousands of pounds of pressure per square inch to compact even the toughest metals, creating uniform bales that maximize transportation efficiency.
Control systems regulate the entire process. Modern balers include sophisticated safety features, pressure monitoring, and automatic cycling capabilities. These systems ensure consistent bale density while protecting operators.
After compression completes, the finished bale ejects from the machine. The dense metal block is now ready for transportation to a processing facility. Some balers include automatic ejection systems, while others require crane assistance.
The hydraulic system is the core of any scrap metal baler, withstanding extreme pressure while maintaining precise control. Quality balers feature durable sealing elements that resist high pressure and temperature conditions.
The complete baling cycle typically takes just minutes. This efficiency allows recycling facilities to process large volumes of scrap metal quickly. Continuous-feed models can handle even higher throughput requirements.
Different types of scrap need specific baler configurations. Ferrous metals (containing iron) require more robust hydraulic systems than non-ferrous metals like aluminum. The baler’s design matches the intended application.
What Are the Different Types of Scrap Metal Balers?
Scrap metal balers come in various designs to accommodate different recycling needs. Each type offers unique features optimized for specific materials, volumes, and operational environments. Understanding these differences helps recycling operations select the right equipment for maximum efficiency.
Lid-style balers feature a top-loading design with a hydraulic lid that closes over the chamber. These balers excel at processing larger scrap metal pieces like automobile parts and bulky sheet metal. The lid applies initial compression from the top while the main ram provides horizontal force. This configuration creates dense, uniform bales from materials that could overwhelm standard balers.
Hopper-type balers are engineered specifically for lightweight metals such as aluminum cans, small components, and thin gauge materials. These machines feature a large feeding hopper that allows continuous loading without frequent shutdowns, providing efficient operation for high-volume, low-density materials commonly processed in beverage recycling operations and manufacturing facilities.
Fully automatic balers represent the highest tier of recycling technology. These systems handle the entire process with minimal operator intervention. Material loading, compression, bale tying, and ejection all occur automatically, enabling continuous operation in high-throughput environments. Although they require a higher initial investment, automatic balers significantly reduce labor costs and maximize productivity in large recycling centers.
Heavy-duty balers incorporate reinforced components and powerful hydraulic systems to compress tough industrial scrap. These machines typically feature thicker steel walls, enhanced cylinder capacity, and specialized wear plates to withstand the demands of processing heavy-gauge metals, cast iron, and industrial waste. Their robust construction ensures reliable performance even with the most demanding materials.
Double-plunger balers utilize two hydraulic rams operating at different angles to create more uniform compression. This design achieves higher density bales by applying pressure from multiple directions. The additional compression capability makes these balers particularly effective for materials that tend to spring back or resist standard compression methods, resulting in more stable bales that maintain their shape during transportation.
Stationary balers remain permanently installed at recycling facilities. Their fixed position allows for integration with conveyor systems, shredders, and other processing equipment to create efficient recycling lines. These balers typically offer higher capacity and more robust construction than portable models, making them ideal for operations with consistent, high-volume material streams.
Portable balers bring recycling capability directly to the waste source. Mounted on trailers or skid frames, these mobile units can be transported to construction sites, demolition projects, or temporary collection points. This mobility eliminates transportation costs for loose scrap while producing compact bales that maximize shipping efficiency. Portable models sacrifice some capacity and features for mobility but provide valuable flexibility for contractors and remote operations.
Shear/baler combinations incorporate cutting mechanisms that allow them to process oversized materials before baling. These versatile machines can shear larger metal pieces to manageable sizes and then compress them into uniform bales in a single operation. This dual functionality makes them particularly valuable for scrapyards and demolition operations that receive varied material types and sizes.
Type of Scrap Metal Baler | Primary Application |
---|---|
Lid-Style Balers | Processing larger scrap metal pieces like automobile parts and bulky sheet metal. |
Hopper-Type Balers | Lightweight metals such as aluminum cans, small components, and thin gauge materials. |
Fully Automatic Balers | High-throughput environments with minimal operator intervention. |
Heavy-Duty Balers | Compressing tough industrial scrap with reinforced components. |
Double-Plunger Balers | Materials that tend to spring back or resist standard compression, achieving higher density bales. |
Stationary Balers | Consistent, high-volume material streams in recycling facilities. |
Portable Balers | Recycling capability directly to construction sites, demolition projects, or temporary collection points. |
Shear/Baler Combinations | Processing oversized materials before baling in scrapyards and demolition operations. |
When selecting a scrap metal baler, consider not only your current material volume but also anticipated future needs. Factors such as material type, desired bale density, operational space, and processing speed all influence which baler configuration will deliver optimal results for your specific recycling operation.
What Are the Benefits of Using a Scrap Metal Baler?
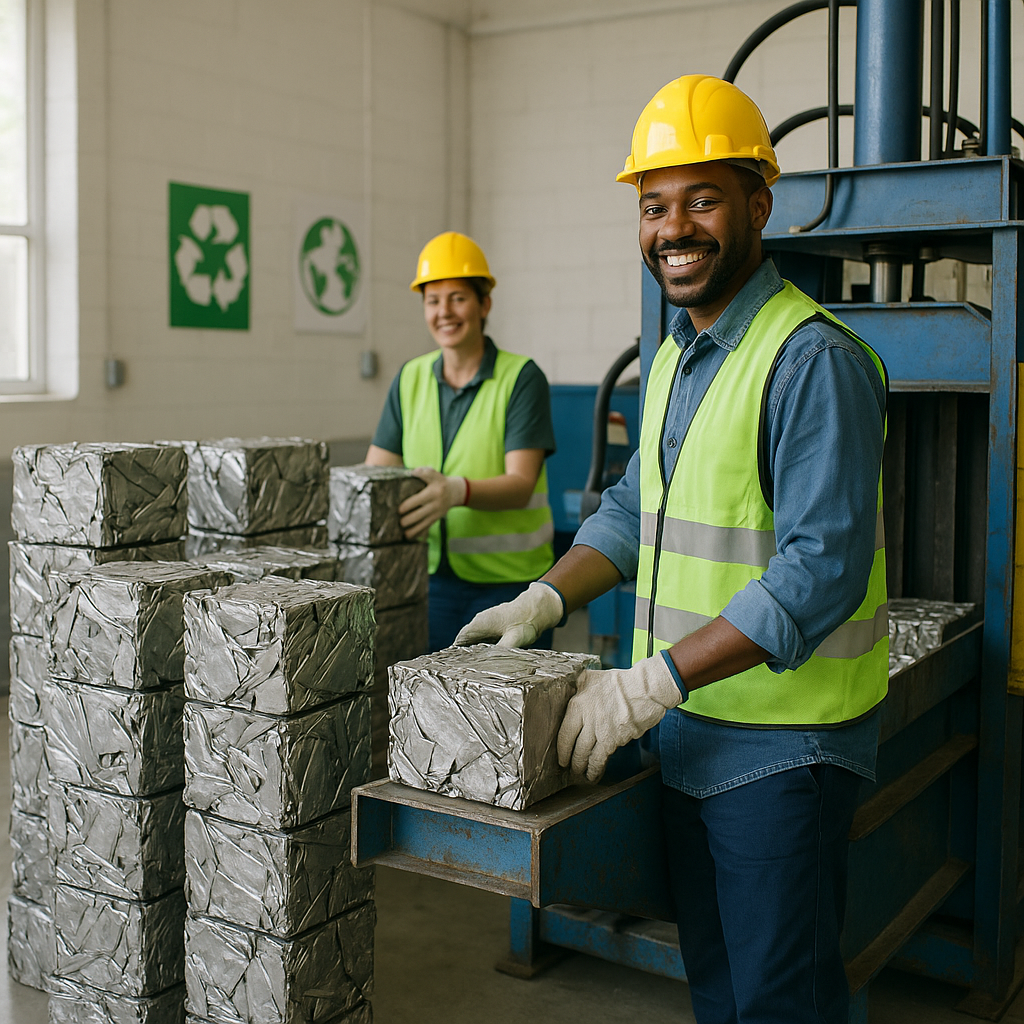
Scrap metal balers are essential in the recycling and waste management industries. These machines compress loose metal scraps into dense, manageable bales, optimizing storage, transportation, and recycling processes. Here are the key advantages that make metal balers valuable investments for recycling operations.
Storage Space Optimization
One immediate benefit of using a scrap metal baler is the reduction in storage space requirements. Loose scrap metal can occupy significant floor space in recycling facilities, causing operational inefficiencies. When compressed into compact bales, the same volume of material needs up to 30% less storage area.
This efficiency allows recycling facilities to process larger quantities of scrap without expanding their physical footprint. Balers enable businesses with limited space to manage higher volumes of recyclable metals without adding costly facility expansions. The organized, stackable nature of metal bales also improves inventory management and material tracking.
Reduced Transportation Costs
Transportation is a major expense in the metal recycling process. Uncompressed scrap metal is bulky and inefficient to transport, leading to fewer tons per shipment and higher fuel costs per unit of material moved. Baled scrap changes this scenario dramatically.
Densely packed metal bales enable trucks to carry more weight while complying with legal load limits, resulting in fewer trips to transport the same amount of material. Studies indicate that businesses using balers can lower transportation costs by up to 20% through more efficient loading and reduced fuel consumption per ton of material. The standardized shape of bales also speeds up loading and unloading, reducing labor costs and turnaround times.
Higher Market Value
Compacted scrap metal fetches higher prices in the recycling market than loose scrap for several practical reasons. Recycling facilities and metal processors favor baled scrap because it integrates more efficiently into their operations. The uniform density and shape of bales reduce processing time and costs for buyers.
Moreover, baled material typically contains less contamination than loose scrap, making it more valuable to end processors. The density of properly baled scrap ensures consistent melting performance in foundries and mills. This increased value can lead to a 10-20% price premium, significantly improving profit margins for recycling operations.
Enhanced Workplace Safety
Safety considerations strongly support the use of scrap metal balers. Loose metal scraps present hazards in recycling facilities, such as sharp edges that can cause injuries, unstable piles that risk collapse, and scattered pieces creating trip hazards. These issues increase the risk of workplace accidents and potential liability.
Baled scrap metal reduces these risks by containing sharp edges within compact blocks. The uniform shape of bales allows for safer stacking and storage. Equipment operators face fewer hazards when moving baled material with machinery. This improved safety profile can lead to fewer workplace incidents, reduced insurance costs, and better regulatory compliance.
Environmental Benefits
The environmental benefits of using scrap metal balers go beyond the obvious recycling advantages. By optimizing the recycling process, balers help reduce the environmental footprint of metal recovery operations in several ways.
More efficient transportation results in fewer truck miles and lower carbon emissions per ton of recycled material. The improved economics of baled scrap also boosts recycling rates by making metal recovery more profitable, diverting more material from landfills. Additionally, the higher quality of baled scrap often leads to more efficient melting processes at mills and foundries, further reducing the energy consumption and emissions associated with recycled metal processing.
Operational Efficiency Improvements
Metal balers streamline the entire recycling workflow. The baling process creates a more organized operation where material moves predictably through collection, processing, and shipping phases. This structured approach improves labor efficiency and reduces bottlenecks in the recycling process.
Modern balers offer various automation features that further enhance operational efficiency. Many models include automated tying systems, ejection mechanisms, and digital controls that minimize manual handling and increase throughput. These efficiency gains allow recycling operations to process more material with the same workforce, improving overall productivity and profitability.
Compliance With Regulations
The metal recycling industry faces growing regulatory requirements regarding material handling, transportation, and environmental impact. Scrap metal balers help businesses meet these compliance standards more easily. The contained nature of baled material reduces the risk of contaminant release during storage and transport, an important consideration under environmental regulations.
Additionally, the improved documentation and tracking possible with standardized bales help meet chain-of-custody requirements that many jurisdictions now impose on recycled materials. For businesses managing potentially hazardous materials, the controlled processing that balers provide offers an additional layer of regulatory protection.
Conclusion
Scrap metal balers are indispensable tools in modern recycling operations, offering substantial benefits in efficiency, safety, profitability, and environmental responsibility. From reducing storage and transportation costs to improving material quality and regulatory compliance, these machines enable recyclers to handle scrap metal more effectively at every stage of the process. Choosing the right baler tailored to your material type and volume is a strategic investment that pays dividends in operational performance and sustainability.
If you’re looking to streamline your metal recycling process or need help managing large volumes of scrap, contact Okon Recycling at 214-717-4083. Our team is ready to assist with your recycling needs and ensure you get the most value out of your metal waste.
Â