5901 Botham Jean Blvd, Dallas, TX 75215
Manufacturing Waste: What It Means and Why Reducing It is Important
July 13, 2025Manufacturing waste includes any inefficiency in production processes that does not add value to the final product. This encompasses excess material usage, wasted time, unnecessary movement, and production errors. Identifying and eliminating these inefficiencies is essential for sustainable operations in the competitive manufacturing landscape.
Every manufacturer generates some form of waste. From scrap materials on the factory floor to time spent waiting for machine repairs, these inefficiencies directly impact a company’s bottom line. Manufacturing waste extends beyond physical byproducts to include operational inefficiencies like overproduction, excessive inventory, and unnecessary transportation of materials.
Reducing manufacturing waste offers substantial benefits for businesses. It leads to lower production costs, improved resource utilization, and enhanced operational efficiency. Companies that effectively minimize waste typically experience increased productivity, better product quality, and stronger market positioning. From an environmental perspective, waste reduction also supports sustainability goals by decreasing resource consumption and limiting environmental impact.
What Are the Eight Types of Manufacturing Waste?
The eight types of manufacturing waste, known as the ‘8 Wastes of Lean’ or ‘TIMWOODS,’ represent activities that do not add value and increase costs while reducing efficiency in production processes. Originally identified in the Toyota Production System, these wastes were introduced by Taiichi Ohno, with an eighth waste added as lean methodology expanded to Western manufacturing. Identifying and eliminating these wastes is essential for creating more efficient recycling and manufacturing operations.
1. Overproduction
Overproduction happens when items are manufactured before they are needed or in greater quantities than necessary. This leads to excess inventory and often conceals underlying process problems. It is considered the most serious waste as it contributes to all other forms of waste.
Overproduction ties up valuable resources and capital that could be better used elsewhere. In recycling operations, processing more materials than can be effectively sorted or marketed results in backlogs and quality issues in the recovered materials stream.
2. Waiting
Waste from waiting occurs when work stops because people, equipment, or materials aren’t ready. This includes machine downtime, information delays, or approval bottlenecks that interrupt workflow. Any time operators stand idle waiting for materials, instructions, or equipment repairs represents lost productivity.
In material recovery facilities, waiting occurs when sorting lines stop due to equipment breakdowns or when trucks wait in long queues to unload recyclable materials.
3. Transportation
Transportation waste involves unnecessary movement of materials, products, or information. Every time materials are moved, there is a risk of damage, delay, loss, and added costs without adding value to the product.
Excessive transportation in recycling plants often results from poor facility layout. When materials need to be moved long distances between sorting stages or storage areas, operational costs increase while processing efficiency decreases.
4. Overprocessing
Overprocessing means doing more work than necessary to produce what the customer requires. This includes using more expensive equipment than needed, adding unnecessary features to products, or performing redundant steps in a process.
In recycling, overprocessing might involve sorting materials to a higher purity standard than markets require or using overly complex technology when simpler solutions would suffice.
5. Inventory
Excess inventory ties up capital, requires storage space, and often hides quality problems. Inventory waste includes raw materials, work-in-progress, and finished goods that aren’t immediately needed for customer orders.
For recycling operations, stockpiles of unsorted materials or processed commodities waiting for buyers represent inventory waste that increases handling costs and reduces material quality over time.
6. Motion
Motion waste refers to any unnecessary movement of people or machines that does not add value. This includes reaching, bending, lifting, or walking that could be eliminated through improved workplace design.
Recycling workers often experience motion waste when they must reach across sorting lines, walk to retrieve tools, or perform repetitive movements that could be automated or redesigned for greater efficiency.
7. Defects
Defects represent products or services that don’t meet specifications, requiring rework or disposal. These quality failures consume resources without creating value and often necessitate additional inspection processes.
In recycling, contamination is the primary defect. When non-recyclable items enter the stream or materials are improperly sorted, the result is downgraded material quality and potential rejection by end markets.
8. Unused Talent
The waste of unused talent occurs when organizations fail to fully utilize employees’ skills, knowledge, and creativity. This waste was added to the original seven when lean principles spread beyond Japan, recognizing that frontline workers often have the best insights for process improvement.
Recycling facilities benefit significantly when sorters and equipment operators contribute their ideas for improving material recovery rates and reducing contamination.
Identifying and Eliminating Waste
Value Stream Mapping is an effective tool for identifying these wastes in manufacturing and recycling operations. This process involves visualizing the entire workflow from raw material to finished product, making it easier to spot inefficiencies.
By systematically addressing each waste category, manufacturers and recycling facilities can significantly improve productivity, reduce costs, and enhance sustainability outcomes. The most successful waste reduction efforts engage frontline workers in identifying problems and developing solutions, creating a culture of continuous improvement.
How Can Manufacturers Identify and Reduce Overproduction Waste?
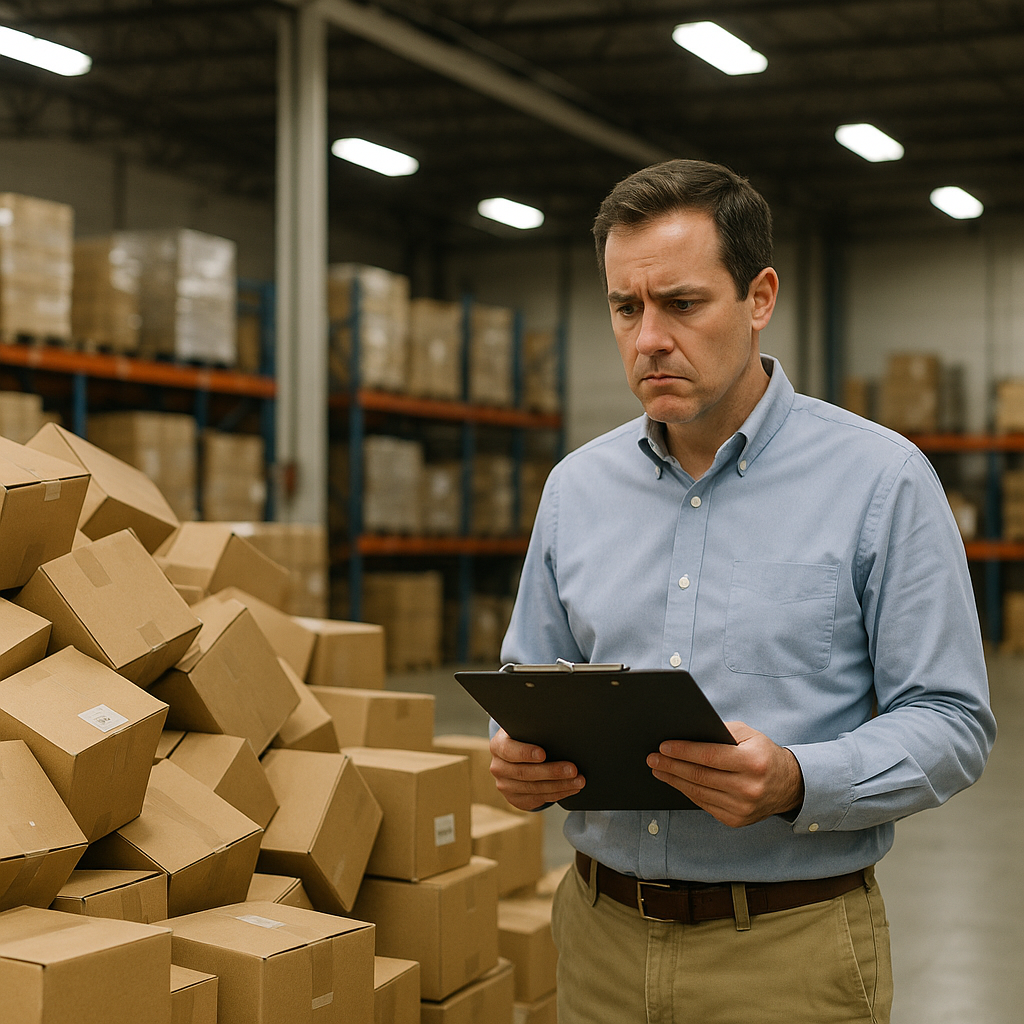
Overproduction occurs when manufacturers produce items in quantities that exceed current demand or before they are actually needed. This form of waste ranks among the most costly in manufacturing operations since excess production ties up capital in unsold inventory, increases storage costs, and risks product obsolescence.
Identifying overproduction waste starts with a careful analysis of production cycles. Look for signs such as large batches of finished goods sitting in warehouses, products gathering dust on shelves, or high levels of work-in-progress inventory. Regular audits comparing production volumes against actual sales can quickly reveal overproduction issues.
Just-in-time (JIT) production systems offer a powerful solution to overproduction waste. Unlike traditional just-in-case approaches, where manufacturers maintain buffer inventories, JIT aligns raw material deliveries and production schedules with actual customer demand. This pull-based system produces goods only when needed and in quantities that match current orders.
The core principle of JIT manufacturing is to create a smooth flow of materials and information throughout the production process. By triggering production based on actual demand rather than forecasts, manufacturers avoid accumulating excess inventory and minimize the risk of producing unwanted goods.
Implementing JIT requires building strong supplier relationships that can deliver smaller, more frequent batches of materials when needed. Factory layouts may need redesigning to reduce movement and handling, while cross-training employees increases workforce flexibility to adapt to changing production needs.
Accurate demand forecasting is another crucial tool for reducing overproduction. By analyzing historical data and market trends, manufacturers can better predict future demand and adjust production levels accordingly. Advanced analytics and artificial intelligence now provide more sophisticated forecasting capabilities than ever before.
Inventory optimization complements these strategies by maintaining appropriate stock levels throughout the supply chain. Real-time inventory tracking systems provide visibility into stock levels, preventing both stockouts and excess inventory. Such systems can also identify slow-moving or obsolete items that need attention.
Companies like Dell exemplify successful JIT implementation in technology manufacturing. Dell’s sophisticated supply chain system procures and assembles components only as needed to produce customized computers. This approach allows Dell to maintain minimal inventory, reduce waste, and respond rapidly to market changes.
Toyota’s renowned production system offers another example of waste reduction through lean manufacturing principles. By eliminating overproduction and other forms of waste, Toyota has set industry benchmarks for efficiency, production times, and product quality improvement.
For manufacturers serious about tackling overproduction waste, the first step involves training employees to recognize and report it. Cultivate a culture that views overproduction as wasteful rather than productive. Implement regular production reviews comparing output to sales, and establish metrics that track inventory levels, turnover rates, and storage costs.
What Strategies Can Address Waiting and Transportation Waste?
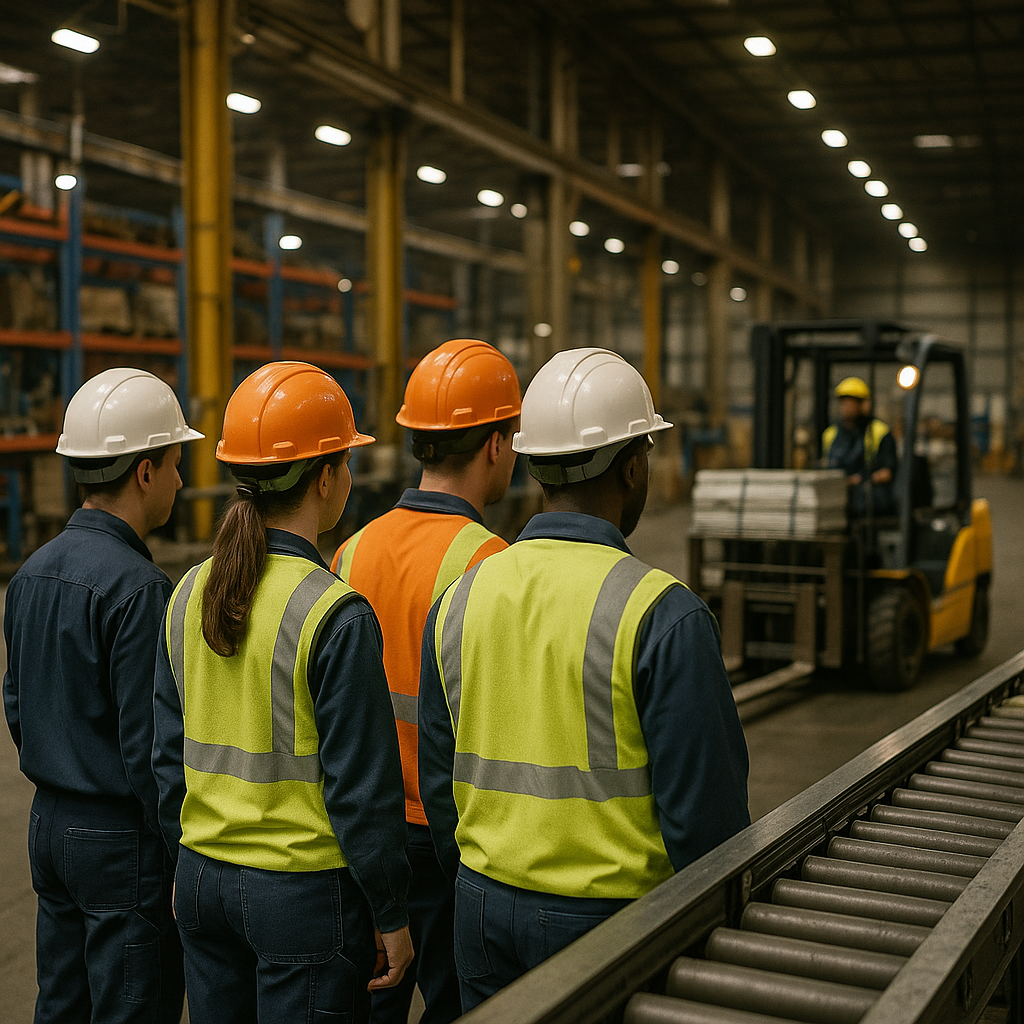
Waiting and transportation waste pose significant challenges to manufacturing efficiency. When products sit idle between processing steps or workers wait for materials, valuable time is lost. Similarly, unnecessary movement of materials across a facility adds costs without improving value.
Tackling waiting waste starts with a balanced production flow. When one workstation consistently outpaces the next, bottlenecks form, causing delays. Evaluating your production line for such imbalances can help you redistribute work more effectively.
Production scheduling tools offer powerful solutions for minimizing wait times. These systems can sequence orders optimally, forecast resource needs, and maintain consistent work pacing. Modern scheduling software adapts to changing conditions in real-time, preventing unnecessary downtime.
For transportation waste, the physical layout of your facility is crucial. Many manufacturers operate with layouts that evolved over time rather than being purposefully designed. Strategically reorganizing the facility to place sequential processes adjacent to each other can significantly reduce transportation distances.
Point-of-use storage systems deliver materials directly to where they are needed, eliminating time-consuming trips to central storage areas and preventing work interruptions. For regularly used components, consider implementing kanban systems that automatically trigger replenishment when supplies run low.
Automation can address both transportation and waiting waste simultaneously. Automated guided vehicles (AGVs) move materials efficiently along optimized routes. Conveyor systems, when properly integrated, keep products moving steadily between stations without manual handling.
Cellular manufacturing groups machines and workers completing similar processes, minimizing the distance materials travel. This approach allows team members to seamlessly switch between tasks, reducing both waiting and transportation waste.
Cross-training employees provides flexibility to redistribute labor during bottlenecks. Workers skilled in multiple positions can move to where they’re most needed, preventing idle time and ensuring continuous production flow.
Many companies benefit from single-minute exchange of dies (SMED) techniques. These methods reduce changeover times between production runs, minimizing waiting periods when equipment transitions between products. Quick changeovers mean more production time and less waiting.
Visual management systems help workers identify and address potential waiting issues before they cause significant delays. Simple signals like colored lights can alert team members to emerging bottlenecks, allowing for immediate response.
Finally, regular data collection and analysis reveal patterns in waiting and transportation waste. Time studies and spaghetti diagrams that track material movement highlight improvement opportunities that might otherwise go unnoticed.
Conclusion: Implementing a Holistic Approach to Reducing Manufacturing Waste
Reducing manufacturing waste requires a comprehensive strategy that tackles all eight types of waste identified in lean manufacturing. This journey is an ongoing commitment permeating every aspect of manufacturing operations. By systematically addressing overproduction, transportation inefficiencies, inventory excess, motion waste, waiting time, overprocessing, defects, and underutilized talent, manufacturers can transform their operations from wasteful to efficient.
The benefits of a holistic waste reduction approach extend beyond environmental sustainability. Successfully minimizing waste leads to substantial operational improvements, such as lower production costs, enhanced quality, increased productivity, and stronger market competitiveness. The circular economy concept, where materials are reused, repurposed, and recycled, further strengthens these benefits by creating closed-loop systems that capture additional value from otherwise discarded resources.
For your recycling and waste management needs, contact Okon Recycling at 214-717-4083. Our team of experts can help your manufacturing facility implement effective waste reduction strategies and develop sustainable recycling solutions tailored to your production processes.