5901 Botham Jean Blvd, Dallas, TX 75215
Manufacturing Scrap Recycling: A Complete Guide to Process, Benefits, and Optimization
July 4, 2025Manufacturing scrap recycling involves collecting, sorting, and reprocessing leftover metal materials from industrial manufacturing operations. Factories generate millions of tons of metal waste each year during their production processes. However, this valuable material doesn’t have to end up in landfills.
Manufacturing scrap includes two main categories: ferrous metals like steel and iron, which possess magnetic properties, and non-ferrous metals such as aluminum, copper, and brass, which do not attract magnets. These materials originate from excess cuttings, trimmings, turnings, stampings, and defective products that fail to meet quality standards.
The recycling process transforms potential industrial waste into valuable raw materials. It helps manufacturers reduce waste disposal costs, conserve natural resources, and lower energy consumption. For many industries, scrap recycling is both an environmental responsibility and a smart business practice that enhances their bottom line.
What Are the Steps in the Manufacturing Scrap Recycling Process?
Manufacturing scrap recycling follows a systematic process that transforms industrial waste into valuable resources. This process ensures metals are properly recovered and prepared for reuse in new manufacturing applications. Let’s examine each step in detail.
Collection
The first crucial step involves gathering scrap metal from various industrial sites. Manufacturers typically set up designated collection areas within their facilities to accumulate metal waste from production processes, including excess material from stamping operations, trimmings, and rejected parts.
Some facilities implement specialized collection systems with segregated bins for different metal types. This initial organization streamlines the subsequent sorting process and maximizes material recovery efficiency. Regular collection schedules prevent excessive waste accumulation on factory floors.
Sorting and Separation
Once collected, the scrap undergoes thorough sorting based on metal type. This critical phase ensures proper recycling and maintains end-product quality. Modern facilities employ several techniques for effective separation:
Manual inspection by trained personnel identifies obvious material differences. Magnetic separators isolate ferrous metals like steel and iron from non-ferrous materials such as aluminum, copper, and brass. Advanced recycling operations may utilize eddy current separators, which create repelling magnetic fields to sort non-ferrous metals.
Some facilities implement sensor-based sorting technologies, including optical scanners and X-ray fluorescence (XRF) analyzers, to identify specific metal compositions with remarkable precision. Proper sorting dramatically improves the efficiency of subsequent processing steps.
Processing
After sorting, the scrap requires processing to reduce its size and prepare it for melting. This typically involves shredding, crushing, or compacting the metal. Industrial shredders can handle large volumes of material, transforming bulky scrap into manageable pieces. For thin sheet metal waste, balers compress the material into dense blocks that are easier to transport and melt.
Processing creates uniformly sized pieces that melt more efficiently. It also increases the density of the scrap, optimizing transportation costs, and furnace loading. Some facilities use specialized equipment like hammer mills for specific metal types or applications.
Melting
The processed scrap enters furnaces where it’s melted at temperatures exceeding 2,700°F (1,500°C). Different furnaces serve specific purposes in the recycling industry. Electric arc furnaces are commonly used for steel scrap, while reverberatory or induction furnaces handle non-ferrous metals like aluminum.
The melting process requires precise temperature control and timing to ensure complete liquefaction without degrading the metal’s properties. Modern furnaces incorporate energy recovery systems to improve efficiency and reduce environmental impact. This stage transforms the solid scrap into molten metal ready for purification.
Purification
Melted scrap often contains impurities that must be removed to meet quality standards. Purification methods vary by metal type but typically include adding flux materials that bind with contaminants to form slag for removal. For aluminum recycling, chlorine gas or nitrogen bubbling helps eliminate hydrogen and other dissolved gases.
Chemical analysis during this stage ensures the metal meets composition specifications. Samples may be tested using spectrometers to verify elemental content. Purification is essential for producing high-quality recycled metal that performs reliably in new applications.
Solidification and Manufacturing Preparation
The final step transforms purified molten metal into forms suitable for manufacturing. The liquid metal is cast into ingots, billets, or sheets, depending on its intended use. Continuous casting equipment allows for efficient production of standardized shapes ready for distribution to manufacturers.
Quality control inspections verify the physical and chemical properties of the solidified metal, including testing for tensile strength, hardness, and chemical composition. The recycled metal is then packaged and transported to manufacturing facilities where it becomes raw material for new products.
Through this six-step process, manufacturing scrap transforms from waste material into valuable manufacturing inputs. The system reduces demand for virgin materials while providing economic and environmental benefits. Modern recycling facilities continue to improve these processes with automation and advanced sorting technologies to increase recovery rates and final product quality.
What Are the Benefits of Recycling Manufacturing Scrap?
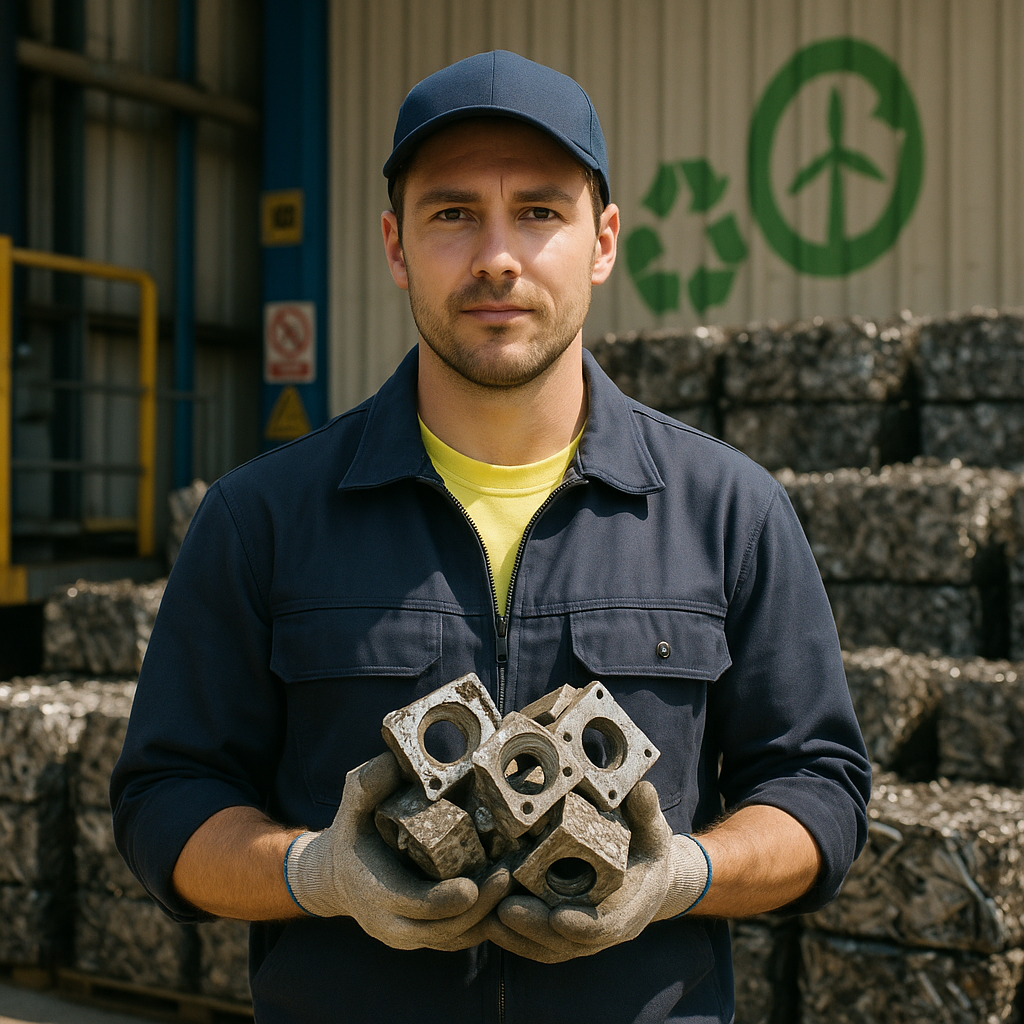
Recycling manufacturing scrap offers significant environmental and economic advantages beyond simple waste reduction. Manufacturing facilities generate notable metal waste during production processes, which, when properly recycled, becomes a valuable resource that supports sustainability efforts across industries.
Resource conservation is a major benefit of recycling manufacturing scrap. The process significantly decreases the need for extracting virgin materials through mining. For every ton of steel recycled, approximately 2,500 pounds of iron ore, 1,400 pounds of coal, and 120 pounds of limestone are conserved. This preservation of natural resources helps protect ecosystems from the disruption caused by extraction activities.
Another crucial advantage is energy savings. Recycling metals requires much less energy than processing virgin materials. Aluminum recycling saves up to 95% of the energy needed for new aluminum production from bauxite ore. Steel recycling conserves about 74% of the energy required to produce new steel from raw materials. These energy efficiencies lead to cost savings for manufacturers and reduced fossil fuel consumption.
- Aluminum recycling: 95% energy savings compared to virgin production
- Steel recycling: 74% energy savings compared to new production
- Copper recycling: 85% energy savings versus mining new copper
- Overall metal recycling: Saves enough energy to power 18 million homes annually
Emission reduction is another significant environmental benefit. The reduced energy requirements for recycled materials directly correlate with lower greenhouse gas emissions. According to the EPA, recycling one ton of steel reduces greenhouse gas emissions by 2.1 metric tons of carbon dioxide equivalent. Manufacturing with recycled materials produces fewer air pollutants, improving air quality in communities near production facilities.
The economic benefits of scrap recycling ripple through communities. The industry generates over $105 billion in economic activity annually in the United States, supporting more than 500,000 jobs in various roles, including collection specialists, processing facility workers, and administrative positions. These jobs typically offer competitive wages and benefits, providing stable employment across various skill levels.
Cost-effectiveness gives manufacturers a competitive edge. Utilizing recycled materials is usually cheaper than processing virgin resources, enhancing company profitability while reducing environmental impact. The decreased production costs allow manufacturers to offer more competitive pricing on finished goods, strengthening their market position.
Waste diversion from landfills is another significant benefit. Manufacturing scrap that would otherwise occupy valuable landfill space finds new purpose through recycling, preserving land for more productive community uses and minimizing the potential for soil and water contamination from metal waste.
Supply chain resilience improves with robust recycling programs. Domestic recycling provides manufacturers with reliable raw material sources, reducing reliance on international suppliers that may face disruptions. This local sourcing creates a more stable manufacturing environment capable of withstanding global supply chain challenges.
The circular economy benefits when manufacturing scrap enters the recycling stream. Materials maintain their value through multiple life cycles instead of following a linear take-make-dispose model. This circularity promotes sustainable economic growth while significantly reducing environmental impact across industrial sectors.
How Can Manufacturers Optimize Their Scrap Recycling Programs?
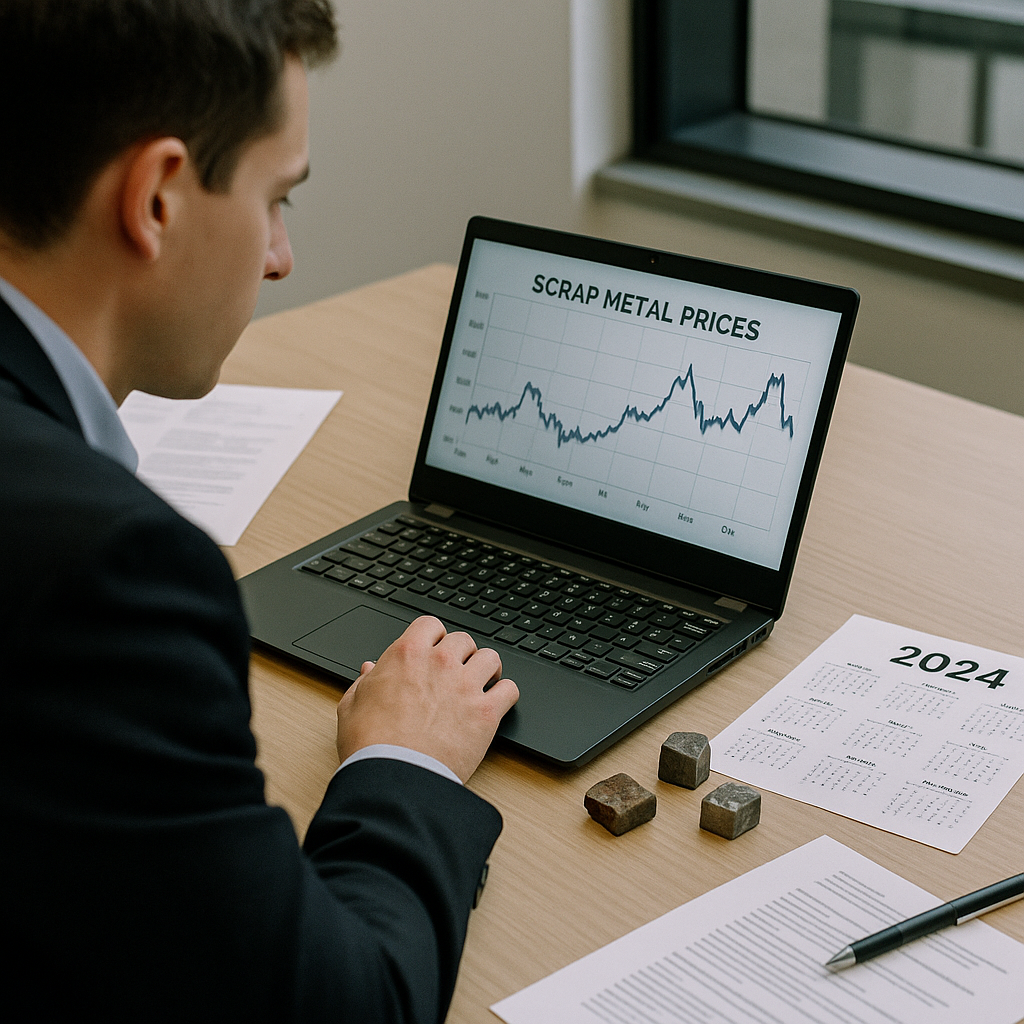
Implementing an efficient scrap recycling program offers manufacturers substantial benefits beyond environmental responsibility. Strategic optimization of scrap management processes can significantly reduce operational costs while creating new revenue streams from materials that would otherwise be discarded.
Implement Efficient Sorting Systems
Proper sorting forms the foundation of effective scrap recycling. Manufacturers should establish dedicated sorting stations throughout their facilities to separate different metal types, including ferrous metals, aluminum, copper, and specialized alloys.
Clear labeling of collection bins using color-coding and visual guides helps prevent cross-contamination, which can significantly decrease the value of recycled materials. Some facilities have found success with magnetic separators for automatically distinguishing ferrous from non-ferrous metals in mixed waste streams.
Advanced facilities are increasingly adopting optical sorting technologies that use sensors to detect material composition, enabling more precise separation of complex scrap materials that would be difficult to sort manually.
Train Employees on Proper Handling Procedures
Even the most sophisticated sorting systems fail without proper employee participation. Comprehensive training programs should educate workers about the different types of recyclable materials generated in their specific work areas.
Training should emphasize the proper handling of hazardous materials, contamination prevention, and the economic impact of effective recycling. Regular refresher courses help maintain knowledge and reinforce the importance of proper scrap management.
Consider designating recycling champions within different departments to monitor compliance and provide guidance to colleagues. These individuals can serve as valuable resources for answering questions and addressing challenges as they arise.
Partner with Certified Recycling Facilities
Selecting the right recycling partner is crucial for program success. Manufacturers should seek certified recycling facilities with proven track records in responsible processing and transparent operations.
Evaluate potential partners based on their compliance with environmental regulations, processing capabilities, and pricing structures. Reputable recyclers will provide documentation of proper material handling and can often offer market insights that help manufacturers maximize the value of their scrap.
Long-term partnerships often yield better economic terms and more consistent service than transactional relationships. Many recyclers will work with manufacturers to develop customized solutions for unique waste streams or challenging materials.
Consider On-Site Processing Equipment
For manufacturers generating substantial volumes of scrap, investing in on-site processing equipment can dramatically increase material value. Balers, shredders, and compactors reduce transportation costs by decreasing the volume of materials that need shipping.
On-site processing also enables manufacturers to transform scrap into more valuable forms. For example, clean, separated aluminum scrap commands significantly higher prices than mixed materials.
When evaluating equipment options, manufacturers should consider space requirements, maintenance needs, and return on investment. Many equipment providers offer lease options that minimize upfront capital requirements while still delivering operational benefits.
Establish Regular Pickup Schedules
Consistent collection prevents scrap buildup that can create safety hazards and consume valuable space. Work with recycling partners to establish regular pickup schedules aligned with your production patterns.
For operations with variable scrap generation, consider implementing a system that allows for on-demand pickups when collection areas reach capacity. Digital platforms now make it easier to schedule pickups and track material movements.
Proper storage between collections is equally important. Covered storage areas protect valuable metals from weather elements that could degrade their quality and value.
Track Recycling Metrics
Comprehensive monitoring of recycling performance provides insights that drive continuous improvement. Key metrics to track include total volume recycled, recycling rate as a percentage of total waste, contamination levels, and revenue generated from scrap sales.
These metrics should be regularly reviewed to identify trends and opportunities for program enhancement. Many manufacturers incorporate recycling metrics into broader sustainability reporting, highlighting their environmental stewardship to stakeholders.
Digital tracking systems can streamline data collection and analysis, making it easier to generate reports and identify areas for improvement. Some systems can even provide real-time updates on recycling performance across multiple facilities.
By implementing these strategies, manufacturers can transform scrap recycling from a simple waste management function into a valuable operational asset that supports both environmental goals and financial performance. The most successful programs treat recycling not as an afterthought but as an integral part of the manufacturing process.
Conclusion: The Future of Manufacturing Scrap Recycling
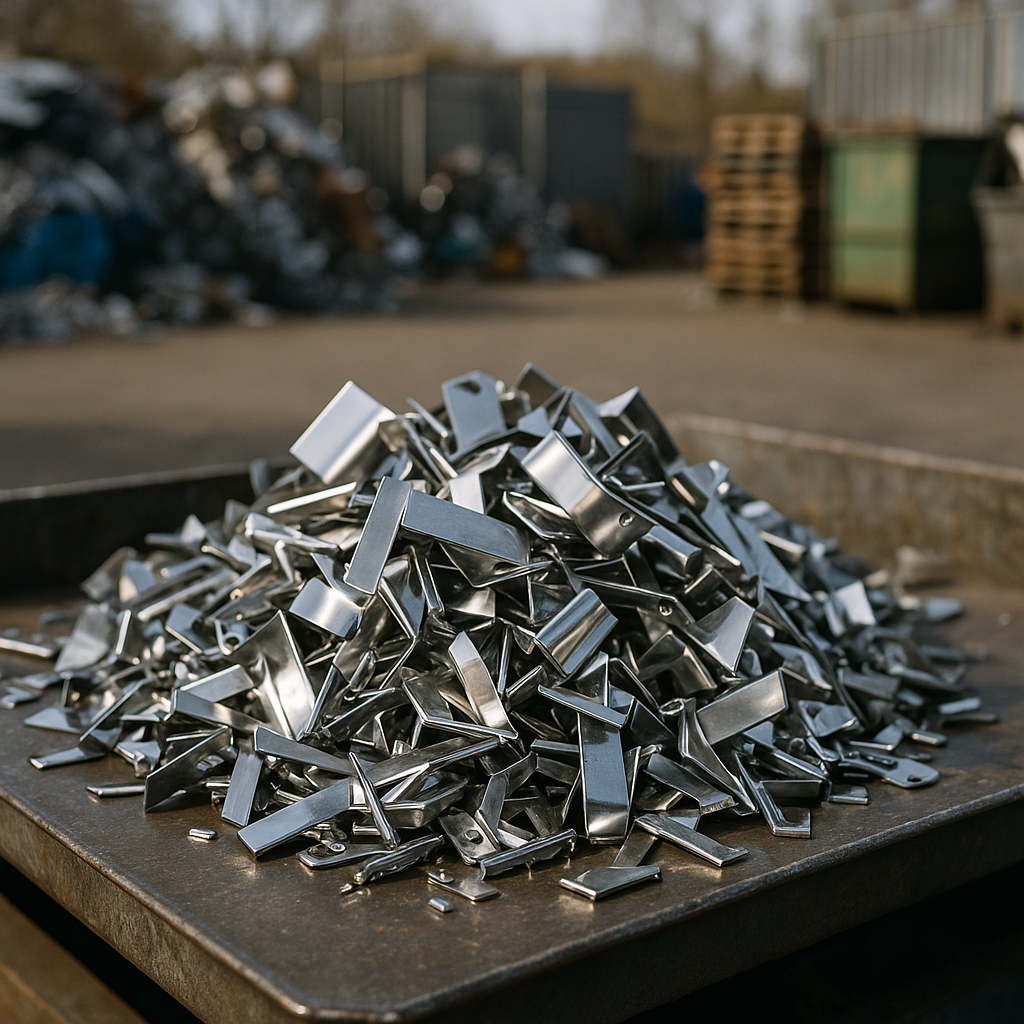
Manufacturing scrap recycling is essential to sustainable industrial practices in our resource-conscious world. As global demand for metals continues to rise, efficiently recycling manufacturing scrap becomes increasingly vital for environmental conservation and economic sustainability. Rapid advancements in technology are making recycling processes more efficient, accurate, and environmentally friendly.
Advanced sorting systems, improved metal analysis techniques, and automation are transforming how manufacturing scrap is processed and recycled. These innovations reduce waste, conserve natural resources, minimize energy consumption, and create new job opportunities within the circular economy. The future of manufacturing scrap recycling looks promising as businesses and governments recognize its crucial role in sustainable development.
For manufacturers aiming to enhance their recycling practices and contribute to a more sustainable future, contact Okon Recycling at 214-717-4083 for expert guidance and comprehensive recycling solutions tailored to your specific needs.